« Warum ist die Hitzebeständigkeit eine wichtige Eigenschaft in der Oberflächentechnik »
In vielen Industrieanlagen sind die Oberflächen von Reaktoren, Öfen oder chemischen Anlagen kontinuierlich einer hohen Temperatur ausgesetzt, oft auch mehr oder weniger großen Temperaturschwankungen. Ähnliches gilt für Schmierstoffe, die bei der Bearbeitung von Werkteilen überall dort zum Einsatz kommen, wo es gilt, mechanische Reibung zu vermindern und die Materialien gleichzeitig vor zu hoher Hitzeeinwirkung zu schützen. Für beide Fälle braucht es High-Tech-Produkte, die eine hohe Temperaturbeständigkeit aufweisen.
Lacke schützen viele Oberflächen vor extremen Temperatureinflüssen…
In Motoren, in chemischen Anlagen, in Reaktoren oder (Hoch-)Öfen werden Konstruktions- und Werkteile eingesetzt, die oft extremen Bedingungen ausgesetzt sind. Hohe Temperaturen und extreme Temperaturschwankungen gehören dazu. Unbehandeltes Material, wie Stähle oder Metalllegierungen können diese nicht immer aushalten. Als Folge dieser extremen Umwelteinflüsse kann es zu Materialermüdung kommen, in der Oberfläche bilden sich Risse oder es tritt Korrosion auf. Und wer möchte schon, dass dieser Fall in einer chemischen Anlage auftritt. Ein hitzebeständiger Lack, der auch extremen Temperaturen von über 1000°C aushalten kann, bietet zuverlässigen Hitzeschutz und hilft dabei auch, weitere Materialermüdungen zu verhindern.
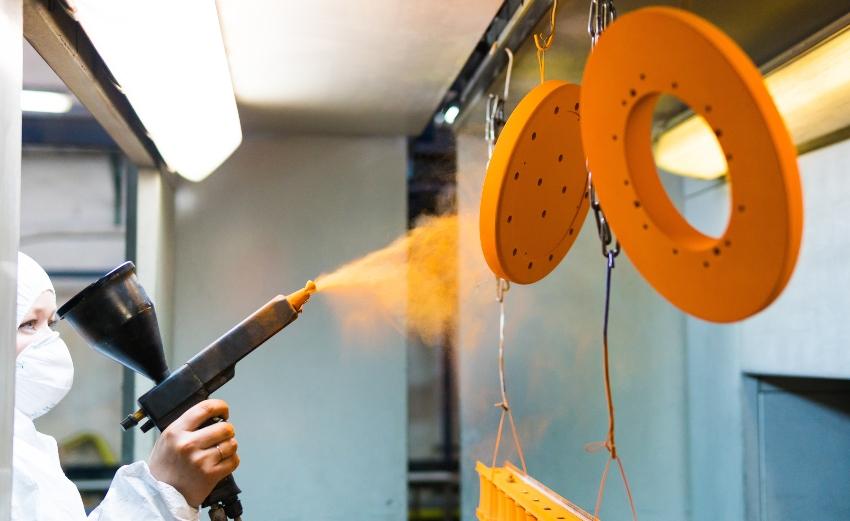
Eine hitzebeständige Beschichtung bietet mehr als Temperaturbeständigkeit
Ein hitzebeständiger Thermolack muss hohe Temperaturen aushalten. Dieser Temperaturbereich beinhaltet eine große Bandbreite und kann von „moderaten“ +200°C bis hin zu Extremfällen von über +1000°C reichen. Hier ist eine ausgeklügelte Oberflächentechnik und passgenaue Auswahl des geeigneten Produkts gefragt, um diese hohe Temperaturbeständigkeit über einen langen Zeitraum zu gewährleisten. In einem industriellen Prozess ist das Material aber nicht nur einer oft extrem hohen Temperatur, sondern in vielen Fällen gleichzeitig einer mechanischen Belastung ausgesetzt. Für Reaktoren oder Rohre muss dies nicht unbedingt gelten, aber Motoren oder Pumpen sind beidem ausgesetzt. Es gibt ausgefeilte Lacksysteme, die neben der Hitzbeständigkeit auch die Oberfläche vor mechanischen Einflüssen und Belastungen schützen. Dies hat direkten Einfluss auf die Materialermüdung und die Lebensdauer der Bauteile und der gesamten Anlage. Erstere wird verringert, während die Lebensdauer der Bauteile und Anlagen insgesamt verbessert wird.
Materialanfälligkeit gegenüber Korrosion verhindern
Viele Lacke bieten nicht nur eine hohe Temperaturbeständigkeit, sondern gleichzeitig einen integrierten Korrosionsschutz. Der Thermolack wird auf die bereits vorhandene Oberfläche aufgetragen und schützt damit als weitere Schicht vor einer möglichen Korrosion des Werkteils. Zu guter Letzt heißt eine hohe Temperaturbeständigkeit auch, dass ein Werkteil nicht so sehr gekühlt werden muss. Ökonomisch gesehen wird der Wirkungsgrad verbessert, ökologisch gesehen wird Energie für die Kühlung eingespart. Macht man sich daher von Beginn an Gedanken über einen, vielleicht vermeintlich nicht so wichtigen Punkt wie die Oberflächenbeschichtung der eingesetzten Werkteile, kann man langfristig an vielen Stellen einsparen und sowohl Effizienz wie Effektivität eines Industrieprozesses erhöhen. Für die Oberflächenbearbeitung kann man aus einer breiten Auswahl an unterschiedlichen Lack-Systemen wählen.
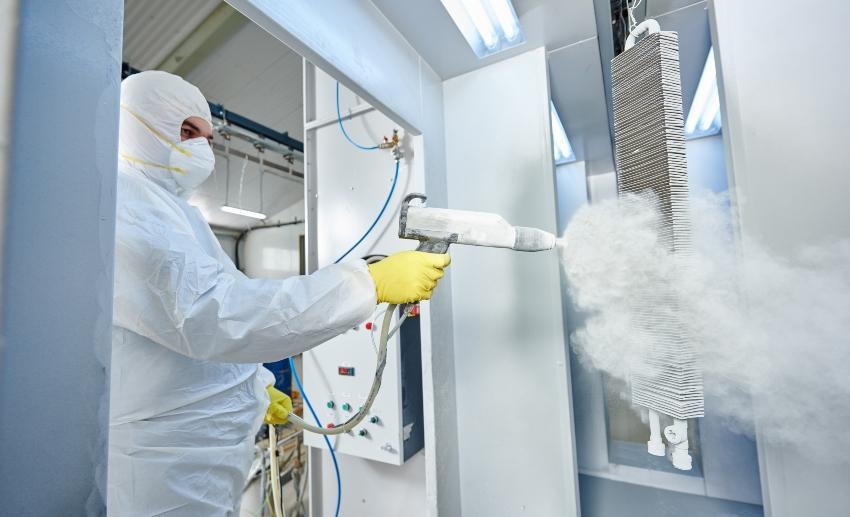
Hitzebeständige Lacke unterscheiden sich in ihrer Temperaturbeständigkeit und chemischen Zusammensetzung
In der Oberflächentechnik können ganz verschiedene Lacke und Techniken für die Oberflächenbearbeitung eingesetzt werden. Dabei spielt nicht nur die Hitzebeständigkeit eine Rolle, sondern auch, ob es sich um eine Dauerbelastung bei einer bestimmten Temperatur handelt oder ob das Material schwankenden Temperaturen ausgesetzt ist. Außerdem muss klar sein, ob weitere Ansprüche, wie ein Korrosionsschutz erfüllt werden müssen. Der schlimmste Fall, das Beschädigen der Lackoberfläche und damit des darunterliegenden Materials, muss verhindert werden. Daher tut es Not, sich vor der Oberflächenbearbeitung Gedanken über den Prozess und das Material zu machen. Ist dies entschieden, kann man zwischen verschiedenen Lacksystemen auswählen.
Silikonharze – ein weitverbreiteter Schutz mit hoher Temperaturbeständigkeit
Die meisten Silikonharze bieten bis zu einer Temperatur von +350°C ausreichenden Schutz. Für extremere Anwendungen bieten sich sogenannte Phenylsilikonharzlacke an, die kurzfristig Temperaturspitzen von bis zu +700°C aushalten. Grundbaustein der Silikonharzlacke sind hochmolekulare Polysiloxane, die eine dichte, hoch vernetzte Schicht und damit sehr guten, festen Film auf der Oberfläche bilden, der beim Aushärten nur eine geringe Volumenänderung aufweist. Neben der hohen Temperaturbeständigkeit zeichnen sich Silikonharzlacke durch eine gute Wetterbeständigkeit sowie einen geringen Vergilbungsgrad aus. Silikonharze können durch Pigmente, wie Titandioxid oder Ruß eingefärbt werden.
Metall-Coating – eine Oberflächentechnik für besondere Einsatzbereiche
Fein verteiltes Metallpulver kommt beim sogenannten Flammspritzen zum Einsatz. Dabei wird das für den Überzug gewünschte Metall in einer Brenngas-Sauerstoffflamme geschmolzen. Mit einer Sprühpistole wird das aufgeschmolzene Metall durch Druckluft oder durch Stickstoff zerstäubt und die feinen Metalltröpfchen auf die Oberfläche geschleudert. Die Oberfläche des behandelten Werkstücks selber wird nicht aufgeschmolzen. Diese Oberflächentechnik bietet gleichzeitig Schutz vor Korrosion und vor Hitze bis zu einer Temperatur von +400°C. Sie wird vor allem für Anlagen im Onshore- oder Off-Shore-Bereich eingesetzt.
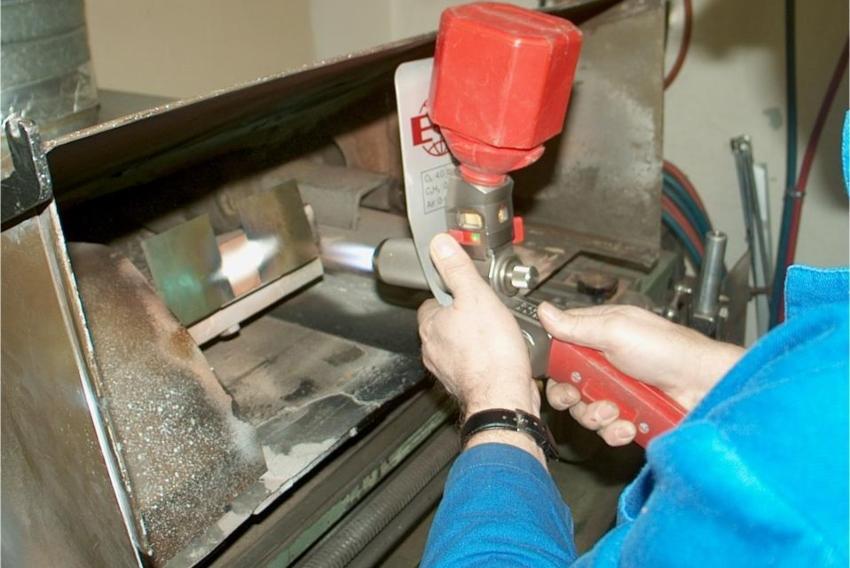
Pulverbeschichtung – Korrossionsschutz in verschiedensten Farben
Die Pulverbeschichtung mit Pulverlacken ist eine Oberflächentechnik, die Ähnlichkeiten zum Metall-Coating aufweist. Es werden keine Metalltröpfchen, sondern ein Pulverlack aufgetragen. Die Grundlage sind Poylester- oder Epoxidharze und zusätzlich Bindemittel, Additive, Füllstoffe sowie farbgebende Pigmente. Dieser Lack wird auf ein elektrisch leitfähiges Metall aufgesprüht. Die Pulverlackteilchen werden elektrostatisch aufgeladen, auf die Oberfläche transportiert und haften dort. Pulverlacke haben eine mittlere bis hohe Hitzebeständigkeit, die zwischen 200°C und 500°C liegt. Ähnlich wie beim Metall-Coating kommt auch hier zur Temperaturbeständigkeit der Korrosionsschutz dazu.
Keramische Werkstoffe für den Motoren- und Turbinenbau
Wird eine hohe Temperaturbeständigkeit verlangt, beispielsweise für Krümmer und Auspuffe im Automobilbau oder für Werkteile im Motoren- und Turbinenbau, greift man auf keramische Werkstoffe zurück. Dazu zählen beispielsweise Keramikbeschichtungen aus Aluminiumoxid, titanverstärktem Chromoxid oder aus mit Yttrium stabilisiertem Zirkonoxid. Diese Spezialkeramiken zeichnen sich zudem durch eine hohe Härte, sehr gute Chemikalien- und Korrosionsbeständigkeit aus. Auch schützen sie Werkteile sehr gut gegen Verschleiß. Sie können auf Metall- aber auch Glasfaser- oder Carbonoberflächen durch thermisches Spritzen aufgebracht werden. Dabei wird beim Plasmaspritzen, einem High-Tech-Verfahren der Oberflächentechnik, bei einer Flammtemperatur von 20.000°C gearbeitet. Bei dieser Temperatur wird die aufgeschmolzene Keramik auf das Metallteil geschossen und bildet eine geschlossene Schicht.
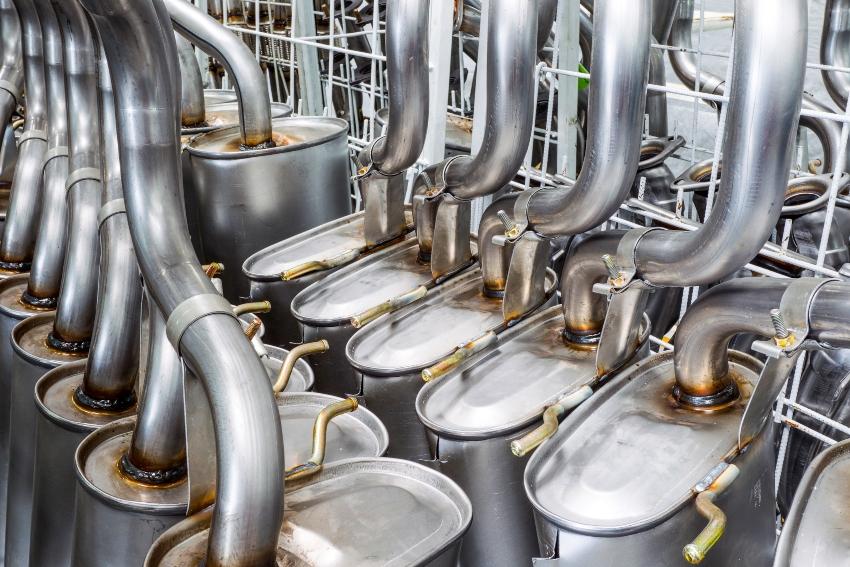
Schmierstoffe in der verarbeitenden Industrie – High-Tech-Produkte halten die Produktion am Laufen
Nicht nur die Oberflächen müssen eine gewisse Hitzebeständigkeit aufweisen, auch im Prozess muss Wärme abgeführt werden. Denn in eigentlich jedem Prozess tritt Reibung auf und diese erzeugt Wärme. Dieses Phänomen machen wir uns im Winter zunutze, wenn wir unsere eisigen Hände durch gegenseitiges Reiben erwärmen. Viel mehr Hitze wird in Industrieprozessen erzeugt, wenn Werkzeuge bearbeitet werden, wenn Walzen oder Kugellager betrieben werden. Durch die gegenseitige Reibung von Metall auf Metall oder Kunststoff können große Mengen an Hitze erzeugt werden. Um eine zu hohe Reibung zu vermeiden, werden seit jeher Schmierstoffe eingesetzt. Je nach Prozess handelt es sich um flüssige Öle oder um Schmierfette.
Basis für Schmieröle sind entweder Mineralöle, die aus einem Gemisch unterschiedlicher Kohlenwasserstoffe bestehen, oder synthetische Öle. Dies sind beispielsweise Polyolester. Typische Schmierfette bestehen aus einem Grundöl, typischerweise längerkettigen Kohlenwasserstoffen, wie Paraffinen. Dazu kommen sogenannte Verdicker, die dem Schmierfett eine bestimmte Struktur geben, und Additive. Typische Verdicker sind Metallseifen. Als Additive werden Stoffe zugesetzt, die beispielsweise vor Korrosion oder Oxidation schützen.
Bei allen Schmierölen und Schmierfetten steht nicht nur die Schmierwirkung im Vordergrund, sondern gleichzeitig auch das Kühlen. Je nach Prozess überwiegt der ein oder andere Aspekt. Steht das effektive Ableiten der im Prozess entstandenen Hitze im Vordergrund, werden in der Oberflächenbearbeitung spezielle Schmiermittel, sogenannte Kühlschmierstoffe (KSS) eingesetzt. Diese entfernen die entstandene Wärme möglichst schnell von der Bearbeitungsstelle. Kühlschmierstoffe auf Wasserbasis sind dabei besonders effektiv.