« Maschinen auf Hochglanz bringen »
Für den einwandfreien Betrieb und hocheffizientes Arbeiten gilt ein gut gewarteter Maschinenpark als unabdingbar. Gerade in Zeiten sehr guter Konjunkturdaten steigt die Nachfrage nach der professionellen Maschinenreinigung im Industrie-Sektor daher unaufhörlich an. Nicht zuletzt aufgrund der Belastungen für die Umwelt, sollte erst auf lösemittel-basierte Maschinenreiniger zurückgegriffen werden, wenn ihr Einsatz alternativlos ist. Der nun folgende Bericht wird daher unter anderem verdeutlichen, welche anderen Maßnahmen sich in deutschen Industrie-Betrieben etabliert haben, um Metall zu reinigen.
Zuweilen „Drecksarbeit“: Vollautomatische Maschinen im Produktionsbetrieb
Zunächst gilt es jedoch zu klären, mit welchen Schmutzablagerungen heutige Maschinenreiniger überwiegend konfrontiert werden. Schließlich unterscheiden sich die Anforderungen an die Maschinenreinigung je nach Branche und Unternehmen mitunter erheblich. So sammeln sich an umlaufenden Maschinen in der Metall-, Kunststoff- und Holzbearbeitung produktionsbedingt zahlreiche Späne, die sich überwiegend manuell entfernen lassen. Vor allem bei größeren Anlagen dringen die Überreste des Materials aber zum Teil tief in die Maschine ein und können sich dort unangenehm festsetzen. Immerhin treffen sie dort in der Regel auf bindende Kühl- und Schmiermittel. Wenn jene beiden Elemente in Inneren der Maschine aufeinandertreffen, bilden sich nicht selten hartnäckige Schmutzablagerungen, die ohne gründliche Reinigung dessen Wirkungsgrad herabsetzen und schließlich zu Produktionsausfällen führen würden. Ähnliche Auswirkungen sind zu verzeichnen, wenn in Industrie-Anlagen Wasser zur Kühlung oder zum Zwecke der Staubbindung eingesetzt wird. So bilden sich in diesem Falle häufig großflächige Kalkablagerungen, die verminderte Wärmeübertragung, geringere Durchflussmengen und Korrosion begünstigen. Und da die Anlagen in Industrie-Betrieben inzwischen immer komplexer gebaut werden, lässt sich die manuelle Maschinenreinigung oft nur mit sehr hohem personellen und finanziellen Aufwand umsetzen. Dies trifft umso mehr zu, wenn die Anlage weitgehend demontiert werden muss, um dessen Einzelteile gründlich zu reinigen. Zum Zwecke der professionellen Maschinenreinigung setzen Industrie-Unternehmen daher bereits seit Jahrzehnten auf chemische Mittel auf Lösemittel- oder Wasserbasis.

Besser als ihr Ruf: Lösemittel-basierte Maschinenreiniger
Aufgrund unangenehmer Gegebenheiten aus der näheren Vergangenheit beschwören Lösemittel-basierte Maschinenreiniger bei unkundigen Zeitgenossen noch immer Horror-Bilder herauf. Schließlich wurden zur Maschinenreinigung in Industrie-Betrieben bis in die 80er Jahre fast ausschließlich die Ozonschicht schädigende Chemikalien mit hohem VOC-Anteil (volatile organic compound; z. B. FCKW) eingesetzt. Moderne Industriereiniger, wie lösemittel-basierte Produkte der HAKUPUR-Serie, nutzen hingegen stabile Tenside (Lösemittel), wie Salzsäure und milde alkalische Lösungen auf Ethanol-Basis. Dank fortwährender Weiterentwicklung jener Chemikalien lässt sich die Maschinenreinigung in der Industrie inzwischen so umweltschonend wie kostenbewusst und zeitsparend umsetzen. Schließlich ist die Produktpalette von HAKUPUR inzwischen soweit angewachsen, dass sich damit nicht nur Stahl von produktionsbedingten Schmutzablagerungen befreien lässt, sondern auch:
- Eisen
- Grauguss
- Leichtmetalle
- zahlreiche Metall-Legierungen
Dass damit immer noch eine gewisse Belastung der Umwelt verbunden ist, lässt sich natürlich nicht ignorieren. Da sie heutzutage das effektivste Mittel für die professionelle Maschinenreinigung in Industrie-Betrieben darstellen, kann ihr Einsatz jedoch nicht immer umgangen werden. Andererseits klafft zwischen der manuellen und der lösemittelbasierten Maschinenreinigung eine recht große Lücke, die von wasserhaltigen Reinigern gefüllt wird. Diese enthielten in früheren Zeiten zwar immer noch einen gewissen Anteil an Tensiden, erzielen ihre Reinigungswirkung aber inzwischen durch umweltschonende Glykol-Verbindungen. Im Vergleich zu chemischen Reinigern besitzen sie damit folgende Vorteile:
- weniger geruchsintensiv
- ohne toxisches Potential und
- nicht entflammbar
Darüber hinaus sind wasserbasierende Maschinenreiniger, wie Sie ebenso in der HAKUPUR-Serie vorkommen, mittlerweile auch mit hochwertigen Korrosionshemmern versetzt, sodass sie für jede der heute üblichen Methoden der industriellen Reinigung eingesetzt werden können.
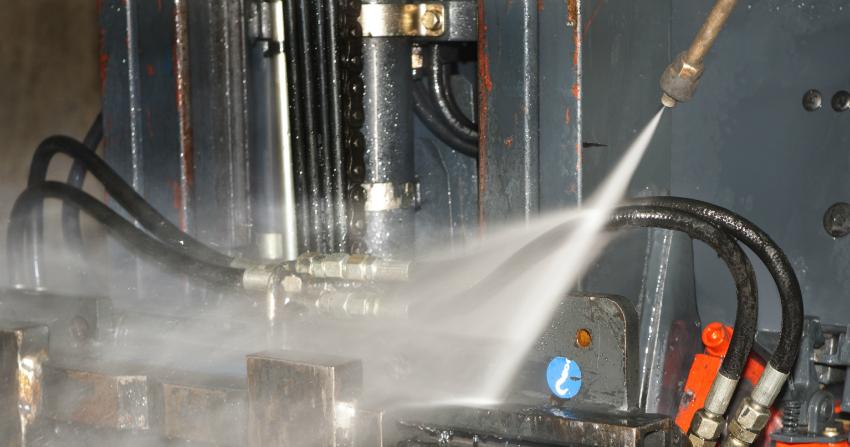
Vom Tauchbad bis zur Ultraschall-Methode: Die Optionen für die moderne Maschinenreinigung
Ultraschall
Eine recht materialschonende Variante klingt dabei noch immer ziemlich futuristisch: Die Reinigung per Ultraschall. Die verschmutzten Metallteile werden dazu in einem Korb oder einer Wanne platziert, die wiederum von einer mit Reinigungsmitteln versetzten Lösung umgeben ist. Ultraschallfrequenzen mit einer Bandbreite von 20 bis 400 kHz versetzen die Konstruktion schließlich in Schwingung, woraufhin sich winzige Kavitationsbläschen bilden. Diese reinigen die Metall-Objekte letztlich umso schonender, je höher die Frequenz eingestellt wurde. Somit lassen sich mithilfe der Ultraschall-Methode zwar Energiekosten einsparen, andererseits stößt sie aber an Grenzen, wenn Metall zu reinigen ist, das recht stark verunreinigt wurde.
Tauchbäder
Ähnliche Ergebnisse lassen sich mit sogenannten Tauchbädern erzielen. Die verunreinigten Maschinenteile bekommen in diesem Fall entweder einen konkreten Bestimmungsort in der Reinigungslösung zugeordnet und werden dort mit einem gewissen hydraulischen Druck umspült oder stattdessen maschinell durch das Tauchbad gezogen. Sehr stark verschmutzte Maschinenteile werden dabei nach dem Drei-Phasen-Prinzip gereinigt: Dem Bad in der Reinigungslösung bei Temperaturen bis zu 45°C folgt der Spülgang mit herkömmlichem Leitungswasser. In der abschließenden Phase wird das Tauchbad schließlich mit deionisiertem Wasser geflutet, das die Bauteile von den letzten noch verbliebenen Schmutzpartikeln säubert. Sollten diese aus eisenhaltigen Metallen bestehen, wird die Lösung in dieser Phase zudem häufig mit wirksamen Rosthemmern versetzt, um der Bildung von Flugrost vorzubeugen.
Industrielle Waschmaschinen
Mit einem gewissen Druck ist wiederum auch die Reinigung in einer industriellen Waschmaschine verbunden. Jene Geräte gleichen vom Aufbau und ihrer Wirkungsweise herkömmlichen Geschirrspülern, werden aber mit deionisiertem Wasser betrieben, das im Verhältnis 5:1 mit hochwertigen Industriereinigern versetzt wurde. Der Reinigungszyklus erfolgt in diesem Falle in vier Schritten, wobei die auf die Bauteile einwirkenden Temperaturen von der Grundreinigung bei etwa 50°C bis zum Abtrocknungsprozess bei 115°C beständig ansteigt. Die exakte Dauer und erforderlichen Temperaturen hängen dabei jedoch weniger vom verwendeten Industriereiniger, sondern vielmehr vom Verschmutzungsgrad der Bauteile, dem Rückflussprofil der Maschine und dessen allgemeiner Effizienz ab. Zur Optimierung der Maschinenreinigung empfiehlt sich daher der Einsatz digitaler Luftmess-Geräte, mit deren Hilfe sich die Temperatur und der Gesamtenergiebedarf auch kurzfristig anpassen lassen. Jene Methode gilt heutzutage als Standard in der industriellen Maschinenreinigung und repräsentiert im Grunde die moderne Variante vollgekapselter Reinigungsanlagen.
Diese Option hatte sich in den frühen 70ern etabliert und wurde damals fast ausschließlich mit FCKW-haltigen Reinigungsmitteln betrieben. Der vollautomatische Prozess erfolgte dabei selbstreinigend mit wieder aufbereiteten Lösemitteln. Gekapselte Reinigungsanlagen gelten inzwischen zwar als technisch überholt, wirken aufgrund ihrer seinerzeit immensen Anschaffungskosten und nicht zuletzt wegen der hohen Lebensdauer aber noch immer in zahlreichen Industriebetrieben. Ihr Wirkungsprinzip erscheint dabei wie die Blaupause für heutige Waschmaschinen: Die verschmutzten Maschinenbauteile werden in der Spülkammer an Haken befestigt bzw. in spezielle Drahtkörbe gelegt und dort einer gründlichen Reinigung mit anschließender Spülung unterzogen. Direkt darauf nutzen Heißgebläse das Prinzip der Dampfkondensation, um die Bauteile schnellstmöglich abzutrocknen. Unter anderem wegen des hohen Energieverbrauchs kann man hier aber nicht mehr von einer zukunftsfähigen Technologie sprechen.
Abschließendes Fazit: Maschinen müssen nicht zwingend umweltschädlich auf Hochglanz gebracht werden
Schließlich scheint die Spül-Methode mit den heutigen industriellen Waschmaschinen bereits ausentwickelt. So dürfte die Zukunft wohl den Anlagen gehören, die fortgeschrittene Technik verwenden. Die Ultraschall-Methode wirkt in diesem Zusammenhang recht ausbaufähig, wenngleich die neuesten Forschungen eher in die Richtung effizienter Präzisionslaser gehen bzw. die Möglichkeiten der Nano-Technologie auszuloten scheinen. So faszinierend diese Aussichten auch seien mögen, bleibt letztlich jedoch festzuhalten, dass der deutschen Wirtschaft mit den heute verfügbaren Reinigungsmitteln und -prozessen bereits genügend Alternativen zur Verfügung stehen, um ihre Maschinen umweltschonend auf Hochglanz zu bringen. Der nächste große Innovationssprung in der industriellen Maschinenreinigung dürfte daher das Absenken der dabei anfallenden Energiekosten zum Ziel haben.