Ausfallzeiten reduzieren bedeutet, Störungen im Fertigungsprozess zu vermeiden und Instandhaltungsmaßnahmen sorgfältig zu planen und vorzubereiten. Bei Prozessen, die auf einem kontinuierlichen Durchlauf der Werkstücke durch eine Anlage beruhen, wirken sich Ausfallzeiten besonders kostensteigernd aus, weil dann die gesamte Produktion stillsteht. Die industrielle Oberflächenbeschichtung gehört zu diesen Prozessen. Für die einzelnen Arbeitsschritte in der Oberflächentechnik müssen eng tolerierte Zeiten und Prozessparameter eingehalten werden. Bei einem ungeplanten Stillstand sind deshalb häufig umfangreiche Nacharbeiten an den angearbeiteten Werkstücken erforderlich, die die Kosten zusätzlich erhöhen.
Risiken erkennen und minimieren = Ausfallzeiten reduzieren
Die Oberflächenbeschichtung ist ein Prozess, der sich in der Regel aus Reinigung, Aktivierung, Passivierung, Beschichtung und Nachbehandlung (z.B. Trocknung) zusammensetzt. Zwischen einigen Arbeitsschritten sind Spülvorgänge erforderlich. Der störungsfreie Betrieb der einzelnen Stationen setzt die stabile Energieversorgung, die exakte Zufuhr der benötigten Hilfsstoffe und das zuverlässige Ausschleusen der Abfälle voraus. Zur Energieversorgung zählen neben der Bereitstellung von Elektrizität auch die Aufrechterhaltung von Kühlwasser- und Wärmeträgerkreisläufen. Die Auswahl der optimalen Hilfsstoffe (Prozesschemikalien, Reinigungsmittel) trägt entscheidend zum verlässlichen Ablauf der Verfahren bei.
In vielen industriellen Anlagen der Oberflächentechnik durchlaufen die Werkstücke die Prozesskette kontinuierlich. Wird diese an irgendeiner Stelle unterbrochen, steht die gesamte Anlage still. Die Teilprozesse vor der Unterbrechung werden blockiert, weil die Werkstücke nicht weitergereicht werden, den Teilprozessen nach der Unterbrechung fehlt der Nachschub an Werkstücken.
Das Produkt aus der Wahrscheinlichkeit, mit der dieser Fall eintritt, und dem Schaden, der daraus resultiert, ergibt den rechnerischen Wert des Risikos.
Risiko bewerten
Der Schaden hängt von der Länge der Ausfallzeit und vom Umfang ggf. erforderlicher Nacharbeiten ab. Letzterer ist wiederum abhängig von der Dauer des Stillstandes. Viele Prozesse verkraften problemlos kurzzeitige Stillstände. Längere Ausfallzeiten können zum übermäßigen Fortschreiten chemischer und physikalischer Abläufe in einzelnen Teilprozessen führen. Das wirkt sich auf die Beschaffenheit der Werkstücke und den Zustand der Prozesschemikalien aus. Beides muss in den zulässigen Bereich gebracht werden, um die Abläufe nach einem Ausfall der Technik planmäßig zu starten.
Die Wahrscheinlichkeit eines Ausfalls ergibt sich aus den Wahrscheinlichkeiten von Störungen in den einzelnen Teilprozessen. Der wirtschaftlich vertretbare Aufwand für Maßnahmen, die die Häufigkeit derartiger Störungen reduzieren, muss im Verhältnis zum erwarteten Schaden stehen.
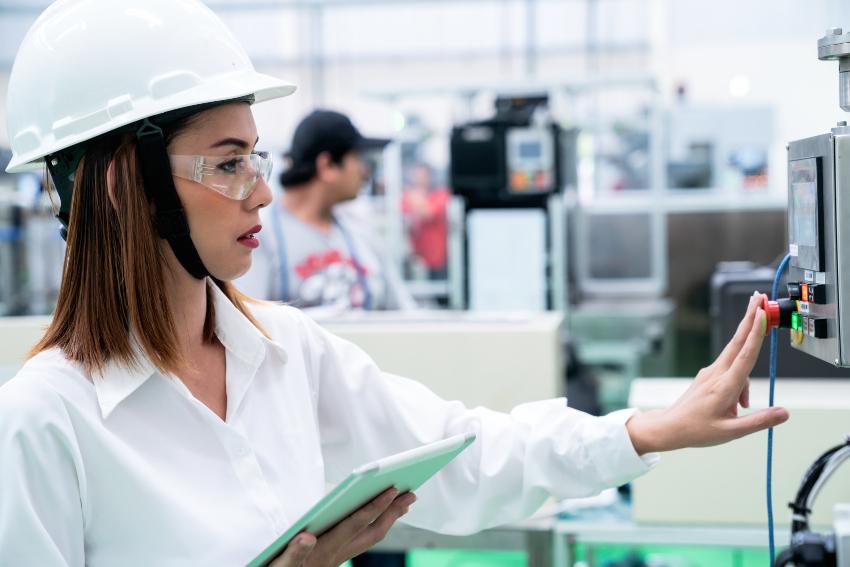
Vermeidung von Betriebsstörungen
Die Maßnahmen, mit denen sich die Wahrscheinlichkeit von Störungen und damit verbundene Ausfallzeiten reduzieren lassen, sind im Wesentlichen:
- der Einsatz von Ausrüstungen, die dem neuesten Stand der Technik entsprechen
- die Qualifizierung und das Training der Mitarbeiter
- die Nutzung von Regelungstechnik zur Prozessführung
- die Festlegung und Einhaltung von Wartungszyklen
- die Einrichtung von Redundanz für störanfällige Aggregate
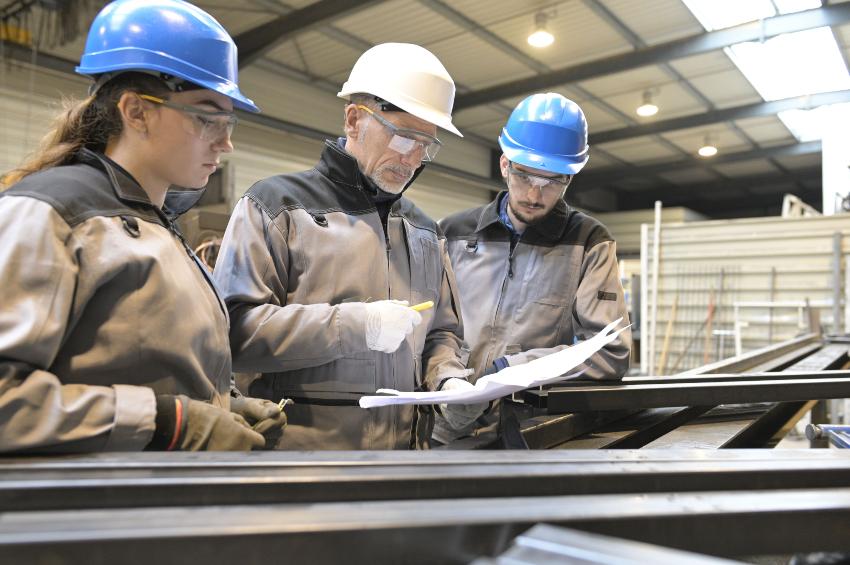
Ausrüstungen, die dem neuesten Stand der Technik entsprechen, sind in der Regel weniger störanfällig und wartungsintensiv. Das Wissen über die Vorgänge, die bei den Produktions- und Hilfsprozessen ablaufen, erhalten die Mitarbeiter durch eine zielgerichtete Qualifizierung. Darüber hinaus hilft ein regelmäßiges Training, unerwartete Situationen zu bewältigen, bevor sie zu einer Störung des Betriebs führen können.
Moderne Regelungstechnik entlastet die Mitarbeiter von Routinearbeiten und zeigt frühzeitig an, wenn sich die Prozessparameter festgelegten Grenzen nähern (Füllstand niedrig, Temperatur oder Druck grenzwertig). Geeignete Maßnahmen bringen die Werte wieder in den optimalen Bereich.
Eine regelmäßige Wartung beugt Ausfällen durch das technische Versagen einzelner Anlagenkomponenten vor. Die Betriebsanleitungen für diese Komponenten geben Auskunft über die erforderlichen Instandhaltungsarbeiten und die einzuhaltenden Wartungsfristen.
Aus den vorgesehenen Wartungs- und Prüffristen ergibt sich die Häufigkeit von geplanten Außerbetriebnahmen der Anlage. Die Zwischenzeiten lassen sich verlängern, wenn für Aggregate mit vergleichsweise kurzen Wartungsintervallen parallel geschaltete Reserveaggregate (Redundanz) vorgesehen werden.
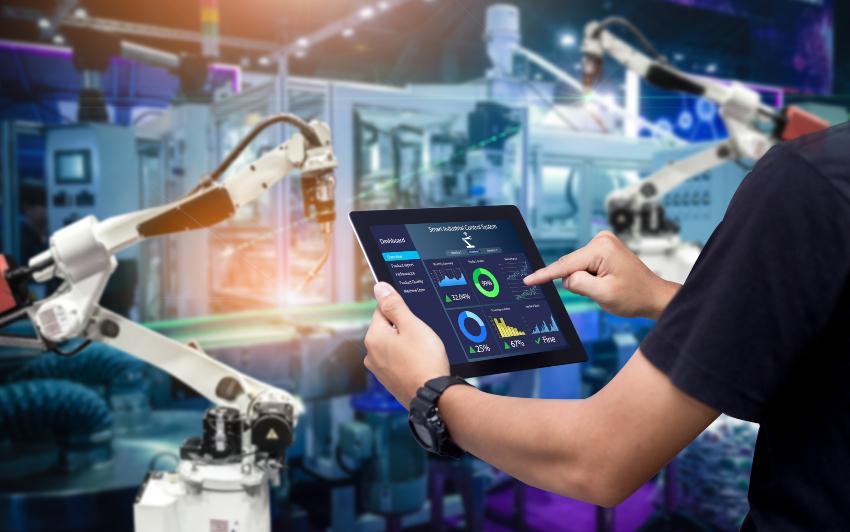
Verringerung von Schäden durch Betriebsunterbrechungen
Die Schadensbegrenzung und Reduzierung der Ausfallzeit für den Fall, dass dennoch eine Störung eintritt, wird erreicht durch:
- Notabschaltungen
- Abfahrroutinen
- Bereitschaftssystem für Instandsetzungsarbeiten
- Organisation eines planmäßigen Wiederanlaufs
Notabschaltungen können durch die Regelungstechnik oder durch das Personal ausgelöst werden, wenn sich eine Situation ergibt, die zu schweren Beschädigungen der Anlage oder zur Gefährdung der Mitarbeiter führen würde.
Im Anschluss an Notabschaltungen oder plötzlich auftretende Betriebsstörungen sorgen definierte Abfahrroutinen dafür, dass die Anlage in einen kontrollierten Zustand gebracht wird. Notentleerungen, die Aufrechterhaltung bestimmter Drücke und Temperaturen oder die Sicherung angearbeiteter Teile verhindern Folgeschäden und bilden die Voraussetzung für eine planmäßige Wiederinbetriebnahme.
In einem Bereitschaftssystem für Instandsetzungsarbeiten nimmt fachkundiges Personal mit geeigneter Ausrüstung die zeitnahe Beseitigung der Störung in Angriff. Aus dieser Maßnahme ergibt sich ein sehr hohes Potential, Ausfallzeiten zu reduzieren.
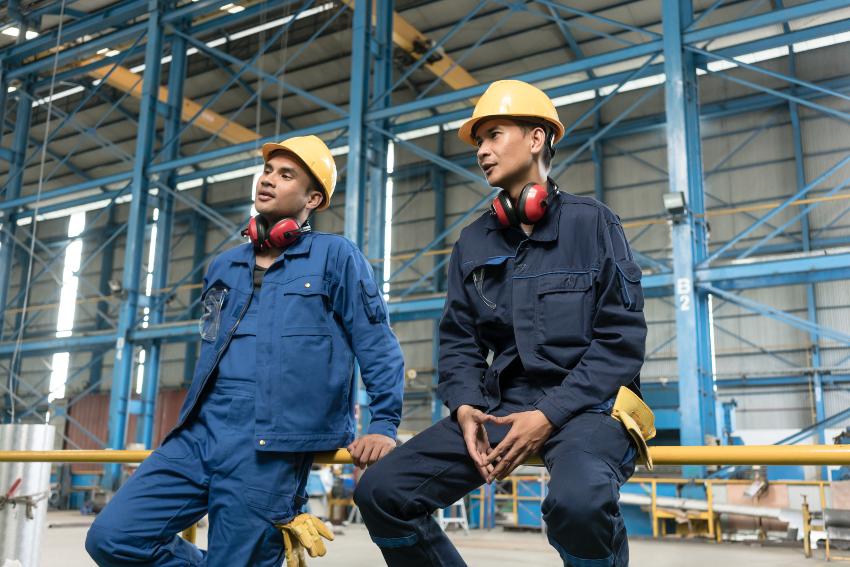
Ausfallzeiten durch Abnutzung: Instandhaltung optimieren
Die Anlagen zur Oberflächenbeschichtung unterliegen wie alle Maschinen und Ausrüstungen einer normalen Abnutzung. Bevor daraus Betriebsstörungen resultieren, sind planmäßige Wartungszyklen (planmäßig vorbeugende Instandhaltung) einzutakten. Während der Wartungsarbeiten werden unter anderem die Ausrüstungen auf den ordnungsgemäßen Zustand geprüft (Druck- und Dichtheitsprüfungen, Sichtprüfung auf Korrosionsschäden, Rissprüfungen), die Verschleißteile ausgetauscht und Ablagerungen in Rohrleitungen und Behältern entfernt.
Die Wartung ist ein Prozess, bei dem der Betrieb der Anlage zwangsläufig stillsteht. Diese Zeitspanne lässt sich durch sorgfältig geplante organisatorische und technische Vorkehrungen deutlich reduzieren. Zu den Möglichkeiten, die für die Wartung notwendigen Prozesse zu optimieren, zählen
- die Beauftragung zuverlässiger Lieferanten
- die rechtzeitige Beschaffung von Ersatzteilen
- die fristgerechte Auftragsvergabe für Dienstleistungen
- die Bereitstellung geeigneter Werkzeuge, Geräte und Hilfsmittel
- die Erstellung eines genauen Zeitplans für die Abfolge der erforderlichen Arbeiten
- die optimale Koordinierung der beteiligten Gewerke.
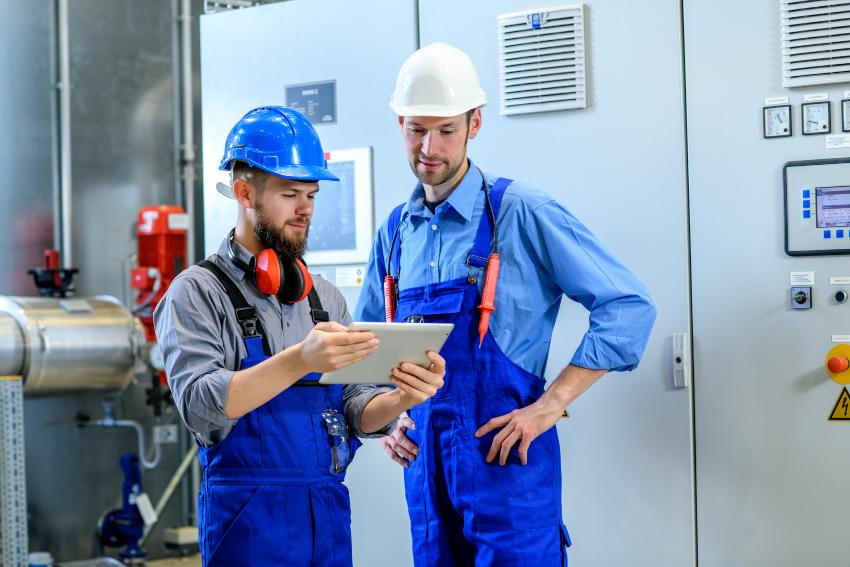
Die Zuverlässigkeit von Lieferanten lässt sich am besten durch eine partnerschaftliche Zusammenarbeit sicherstellen. Die Suche nach dem „unschlagbar“ niedrigsten Preis ist kontraproduktiv und führt häufig zu Verzögerungen und hohen Folgekosten. Bei der Beschaffung von Ersatz- und Verschleißteilen, müssen Lieferfristen berücksichtigt werden. Sollen Dienstleistungen durch Fremdfirmen erbracht werden, brauchen diese die Zeit, die Arbeiten ordnungsgemäß einzuplanen. Dabei helfen detailliert verfasste Aufträge.
Bei der Bereitstellung geeigneter Werkzeuge, Geräte und Hilfsmittel hilft eine Checkliste, die parallel zur Planung der Wartungsarbeiten erstellt werden kann. Die Koordinierung der beteiligten Gewerke und die Festlegung der zeitlichen Reihenfolge ihrer Leistungen haben einen deutlichen Einfluss auf die Reduzierung der geplanten Ausfallzeit. Besondere Aufmerksamkeit benötigen dabei die Schnittstellen zwischen den einzelnen Aufgabenbereichen. Überschneidungen oder Lücken sind ein Schwerpunkt für Fehlerquellen. Diese auszuschließen, birgt ein großes Maß an Reserven, Prozesse zu optimieren und geplante Ausfallzeiten zu reduzieren.