« Moderne Prozesse in der Oberflächentechnik »
Die Prozesseffizienz lässt sich verbessern, indem die Prozesse an den Stand der Technik angepasst werden. Die Wirtschaftlichkeit in der Oberflächentechnik hängt vom Verbrauch an Energie, Wasser und Prozesschemikalien, vom Materialverbrauch und von der Durchlaufzeit der Teile ab. Weitere Kostenfaktoren sind Aufwendungen für Wartungs- und Instandhaltungsarbeiten, Abfallentsorgung und Qualitätssicherung. Vor der Verbesserung der Prozesseffizienz steht die Bestandsaufnahme. An den Stellen, die hohe Kosten verursachen, lohnt es sich, den Hebel anzusetzen.
Kostenfaktoren in der Oberflächentechnik
Die Möglichkeiten, die Prozesseffizienz zu verbessern, sind eng mit den angewendeten Verfahren und der eingesetzten Technik verknüpft. Diese unterscheiden sich in den beiden Teilbereichen der Oberflächentechnik. Die Teilbereiche sind Oberflächenbearbeitung und Oberflächenbehandlung.
Oberflächenbearbeitung
Von Oberflächenbearbeitung spricht man, wenn die Teilefertigung durch mechanischen Materialabtrag in Werkzeugmaschinen erfolgt. Bekannte Verfahren sind Drehen, Fräsen und Schleifen. Die angewendeten Methoden stammen aus dem Bereich der Fertigungstechnik. Während die Kontur der Teile entsteht, wird das überschüssige Material zerspant. Die Späne werden – möglichst nach Werkstoffen getrennt – gesammelt und der Metallurgie zugeführt. Von dort gelangt das Material in den Wirtschaftskreislauf zurück.
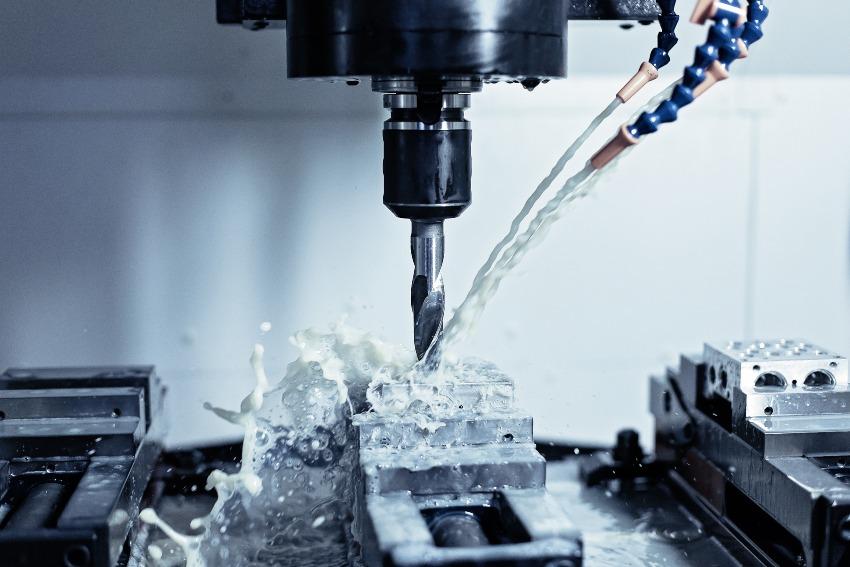
Oberflächenbehandlung
Die Oberflächenbehandlung erfolgt durch Reinigung, Erzeugung von Konversionsschichten und Beschichtung in Anlagen. Dabei wird das Material nicht bearbeitet, sondern verarbeitet. Die Methoden ordnen sich in den Bereich der Verfahrenstechnik ein. Die wichtigsten Ziele sind Korrosions- und Verschleißschutz. Zunehmend gewinnen Verfahren zur Herstellung von funktionalen Schichten an Bedeutung. Dadurch stellen sich zum Beispiel bestimmte optische, bioaktive oder Antihafteigenschaften ein.
Kostenfaktor Zeit
Will man die Prozesseffizienz in der Oberflächentechnik verbessern, ist der Kostenfaktor Zeit ein Schlüsselkriterium. Maßnahmen zur Verkürzung der Dauer vom Beginn der Arbeiten bis zur Fertigstellung eines Teils sind häufig mit der Optimierung weiterer Kostenfaktoren verknüpft. Werden zum Beispiel Be- oder Verarbeitungszeiten verringert, sinkt in der Regel auch der Energieverbrauch. Das gilt vor allem für unvermeidbare Wärmeverluste in der Oberflächenbehandlung. Überschreiten Bearbeitungszugaben von Halbzeugen, Rohteilen und teilbearbeiteten Werkstücken das Fertigmaß in nur absolut notwendigen Größenordnungen, sinkt mit der Bearbeitungszeit auch der Materialverbrauch bei der Oberflächenbearbeitung.
Auf die Teile umzulegender Zeitaufwand
Sowohl in der Oberflächenbearbeitung als auch in der Oberflächenbehandlung sind Zeiten für die Wartung und Instandhaltung zu berücksichtigen und auf die Durchlaufzeit der Teile umzulegen. Das gleiche gilt für die Zeit, in der die Maschinen eingerichtet bzw. die Anlagen umgestellt werden. Mit der Verringerung dieser Zeiten gelingt es häufig, die Effizienz der Prozesse entscheidend zu verbessern.
Reine Durchlaufzeit
In der Oberflächenbearbeitung ergibt sich die reine Durchlaufzeit aus der Zeit, in der die Werkzeuge im Eingriff sind und der Zeit, in der die Teile ein- und ausgespannt, geprüft, zwischengelagert und transportiert werden. In der Oberflächenbehandlung sind das die Verweilzeit, in der physikalische Prozesse und chemische Reaktionen ablaufen, und die Zeit, in der die Werkstücke von einem Verarbeitungsschritt zum nächsten gelangen und geprüft werden.
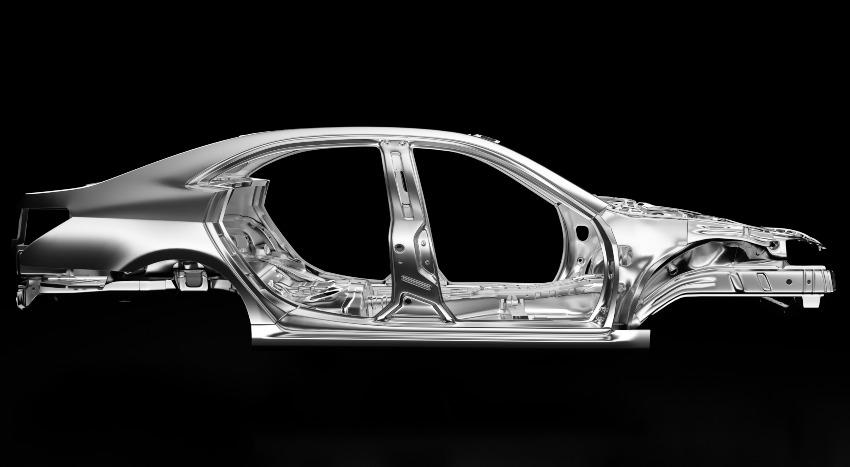
Andere Kostenfaktoren
Über die Optimierung der anderen Kostenfaktoren lässt sich für die vorhandene Technik die Prozesseffizienz verbessern durch:
- Optimierung der Betriebsorganisation zur Vermeidung von Leerlauf und Stillstand
- Pflege von Kühlschmierstoffen Bädern zur Standzeitverlängerung
- prozessbegleitende Qualitätsüberwachung, um Fehler frühzeitig aufzudecken, zu beheben und fehlerhafte Teile vor der weiteren Be- oder Verarbeitung aus der Produktion zu nehmen
- Sorgfältige Wartung der Maschinen und Anlagen, um Reparaturkosten und reparaturbedingte Stillstandszeiten zu vermeiden.
Modernisierung der Oberflächentechnik
Mehr Möglichkeiten, die Prozesseffizienz zu verbessern, ergeben sich durch Investitionen in moderne Maschinen- und Anlagentechnik. Der Trend geht zur Entwicklung von Verfahren der Oberflächenbearbeitung und -behandlung, die per se energie- und materialsparend sind und durch die Nutzung elektronischer Steuerungs- und Überwachungsmethoden optimale Betriebsbedingungen aufrechterhalten. Das zugehörige Stichwort lautet Industrie 4.0. Das ist ein Zustand, der durch die komplette Automatisierung der Produktion erreicht werden soll.
Kontinuierliche Prozesse realisieren
Voraussetzung für die komplette Automatisierung der Produktion ist die Gestaltung kontinuierlicher Prozesse. Die Verfahrenstechnik nutzt vielfach diese Technologien, bei denen Rohstoffe ständig aus Vorratslagern in die Produktionsanlagen gefördert werden, sich dort schrittweise umwandeln und in Form von Endprodukten wieder ans Tageslicht treten. Alternativ dazu läuft der Chargenbetrieb ab. Dabei wandelt sich eine vorgegebene Menge Rohstoffe in Endprodukte um. Die Endprodukte werden entnommen und die Produktionseinrichtung wird neu befüllt. Beide Formen kommen in der Oberflächenbehandlung zum Beispiel bei der Beschichtung von Werkstücken vor.
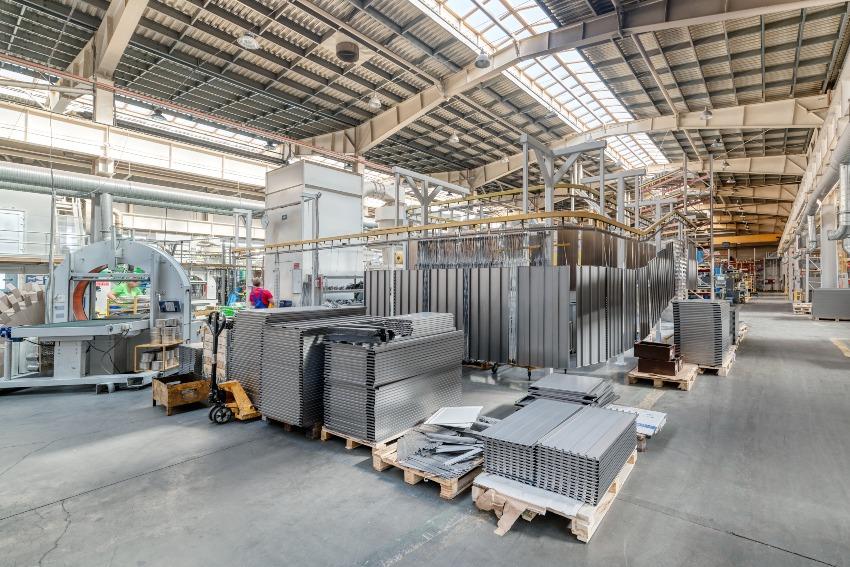
Vom Chargenbetrieb zur kontinuierlichen Arbeitsweise
Die Produktionsweise in der konventionellen Oberflächenbearbeitung entspricht einem Chargenbetrieb: Teil einspannen, Maschine starten, Teil ausspannen, Teil ablegen. Die Fertigung lässt sich in eine kontinuierliche Produktion überführen, wenn das ausgespannte Teil maschinell gegriffen und in die Spannvorrichtung der Folgemaschine gebracht wird. Bei der Serienproduktion, zum Beispiel im Automobilbau, haben sich derartige Systeme bereits bewährt. Das Greifen und Bringen erledigen Roboter. Roboter übernehmen nach der mechanischen Fertigung oft auch die Beschichtung der Teile durch Spritzlackierung.
Nutzung intelligenter Systeme zur Verbesserung der Prozesseffizienz
Bei der Nutzung einer kontinuierlichen Arbeitsweise entfällt die Zwischenlagerung. Das trägt dazu bei, die Prozesseffizienz wesentlich zu verbessern. Der kontinuierliche Betrieb ist nur möglich, wenn die Produktionsschritte zeitlich präzise aufeinander abgestimmt sind. Er ist nur beherrschbar, wenn die Qualitätsanforderungen bei allen Teilprozessen sicher eingehalten werden und wenn das komplette System störungsfrei arbeitet. Fehlt die erste Voraussetzung, werden unter Umständen große Mengen an Ausschuss produziert. Fehlt die zweite Voraussetzung, wird eventuell gar nichts produziert. Die Verbesserung der Prozesseffizienz durch kontinuierliche Arbeitsweise wird durch den Einsatz der Mikroelektronik für die Qualitätssicherung und die Prozesssteuerung wirksam. Mit Hilfe der IT lassen sich die Systeme beherrschen.
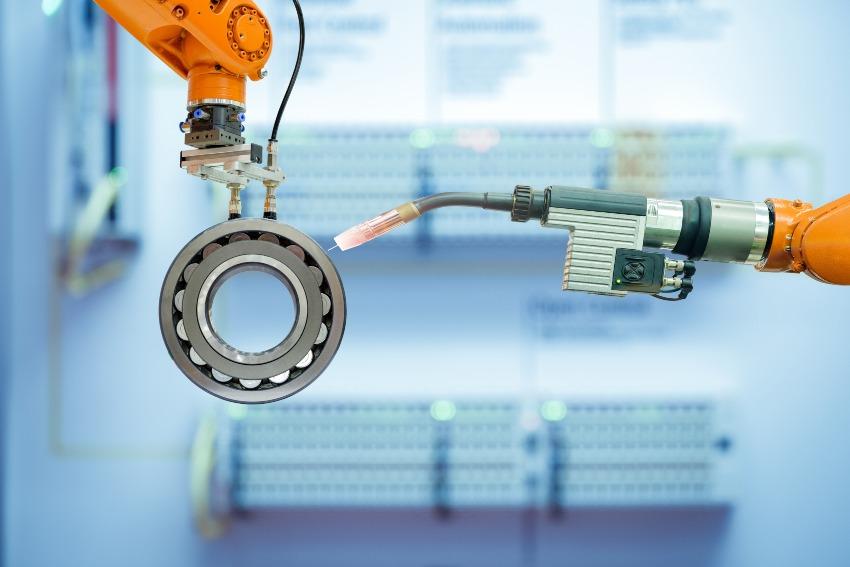
Vorhandene Produktionsanlagen nachrüsten
In vorhandenen Produktionsanlagen erfolgt die prozessbegleitende Qualitätsüberwachung häufig auf Basis der Mikroelektronik. Sensoren erfassen die Betriebsparameter und die Qualitätskenngrößen. Computer vergleichen die Werte mit Grenzwerten. Wandern die Messgrößen an die Toleranzgrenzen, steuern die Computer dagegen. Verlassen die Messgrößen den zulässigen Bereich, schlagen die Computer Alarm. Verletzen die Messgrößen sicherheitsrelevante oder qualitätsentscheidende Grenzwerte, stoppen die Computer die Produktion. Um die Prozesseffizienz zu verbessern, können auch vorhandene Produktionsanlagen mit solchen Systemen nachgerüstet werden.