«Wie Nachhaltigkeit in die chemische Oberflächentechnik Einzug hält»
Niedriger Energie- und Rohstoffverbrauch, geringes Abfallaufkommen und eine stabile Prozessführung sind Kriterien für nachhaltige Chemie. Die Zinkphosphatierung zählt zu den am häufigsten angewendeten Verfahren der Oberflächentechnik zur Verbesserung von Korrosionsschutz und Lackhaftung. Deshalb wirkt sich eine Weiterentwicklung zu effizienteren Methoden hier besonders vorteilhaft auf die Umwelt aus. Die Niedrigtemperatur-Zinkphosphatierung ist das Ergebnis entsprechender Anstrengungen. Wird sie durch eine automatisierte Prozesskontrolle unterstützt, stellen sich stabile Abläufe und eine gleichbleibend hohe Qualität der Erzeugnisse ein.
Anwendungsgebiete der Zinkphosphat-Konversionsbeschichtung
Überall, wo hohe Anforderungen an den Korrosionsschutz und die Lackhaftung bestehen, finden sich Beispiele für den Einsatz der Zinkphosphatierung. Besonders beim Bau von Fahrzeugen, Landmaschinen und Baumaschinen, die hohen Beanspruchungen durch Witterungserscheinungen und mechanische Belastungen ausgesetzt sind, hat sich diese Konversionsschicht als Untergrund für eine abschließende KTL-Beschichtung bewährt.
Als Grundmaterial eigenen sich Eisen, Stahl, Zink, Aluminium, Magnesium und Cadmium.
Konventionelle Zinkphosphatierung
Konventionelle Erzeugung von Zinkphosphat-Schutzschichten erfolgt bei einer Temperatur von 45 bis 50 °C mit einer Lösung aus Phosphorsäure, Zink, Mangan, Beschleunigungsmitteln (z.B. Nitrat) und speziellen Zusätzen, die den Aufbau feinkristalliner Schichten bewirken. Phosphat-, Zink- und Mangan-Ionen bilden zusammen mit Ionen aus der Oberfläche des Grundwerkstoffs eine dichte, korrosionsbeständige Schutzschicht.
Bei starker Vergrößerung wird sichtbar, dass sich auf der behandelten Metalloberfläche dicht beieinander liegende, kleine Körner gebildet haben. Daran kann sich eine Lackschicht gut anhaften.
Veränderungen der Reaktionsbedingungen während des Aufbaus der Schutzschicht
Bei chemischen Stoffumwandlungen laufen in der Regel parallel zur angestrebten Hauptreaktion weitere Nebenreaktionen ab. Je mehr Stoffe anwesend sind, umso vielfältiger sind die entstehenden Reaktionsprodukte. Reichern sie sich in der Prozesslösung an, funktioniert die Hauptreaktion nicht mehr richtig. Deshalb und weil sich die Ausgangsstoffe bei den Reaktionen aufbrauchen, muss die Prozesslösung ständig in Ordnung gebracht werden. Im Laufe der Zinkphosphatierung bilden sich nicht nur auf den Werkstoffoberflächen, sondern auch in der Flüssigkeit wasserunlösliche Phosphate.
Während der ständigen Umwälzung der Prozesslösung vom Becken über Filter zurück ins Becken werden diese Phosphate aus dem System ausgeschleust. Das gelingt allerdings nicht ganz vollständig. Am Beckenboden und in Rohrleitungsabschnitten mit geringen Strömungsgeschwindigkeiten setzt sich Phosphatierschlamm ab und bildet harte Krusten. Die Ablagerungen müssen regelmäßig mit viel Aufwand mechanisch entfernt werden.
Niedrigtemperatur-Zinkphosphatierung
An der Niedrigtemperatur-Zinkphosphatierung nehmen zusätzlich Nickel-Ionen teil. In die Zinkphosphat-Konversionsbeschichtung lagert sich damit auch Nickelphosphat ein. Das passiert bei einer Temperatur von 35 °C. Bei diesem Verfahren entsteht etwa 25 % weniger Phosphatierschlamm. Er ist weicher und lässt sich mit deutlich geringerem Aufwand beseitigen. Das reduzierte Abfallaufkommen bedeutet, dass auch 8 bis 12 % weniger Phosphatier-Ergänzungslösung erforderlich sind. Der Wärmeverlust ist vom Temperaturunterschied zwischen der Prozesslösung und der Umgebung abhängig. Er verringert sich mit jedem Grad, mit dem sich die Anwendungstemperatur an die Umgebungstemperatur annähert.
Eine weitere Reduzierung der Wärmeverluste geht mit der niedrigeren Verdunstung bei tieferen Temperaturen einher. Unter Berücksichtigung des geringeren Wärmebedarfs für das Aufheizen der Prozessflüssigkeit ergibt sich eine Energieeinsparung von insgesamt 25 bis 30 % gegenüber dem konventionellen Verfahren. Der geringere Rohstoffverbrauch und die Energieeinsparung sind mit einer Reduzierung des CO2-Footprints verbunden. Damit ist die Niedrigtemperatur-Zinkphosphatierung ein guter Schritt in Richtung nachhaltige Chemie.
Ablauf des Verfahrens
Der eigentlichen Konversionsbeschichtung gehen die sorgfältige Reinigung und die Aktivierung der Metalloberflächen voraus. Bei der Aktivierung erzeugt ein zinkphosphat-basiertes Aktivierungsmittel Kristallisationskeime, an denen die Phosphate später heranwachsen. Je höher die Anzahl dieser Keime ist, umso mehr Körnchen bilden sich, umso feiner wird die Struktur der Beschichtung auf der Metalloberfläche. Die Phosphatschicht entsteht auf der Metalloberfläche entweder durch Besprühen der Teile mit Prozesslösung (Spritzverfahren) oder durch das vollständige Eintauchen in mit Prozesslösung gefüllte Becken (Tauchverfahren). An die Niedrigtemperatur-Zinkphosphatierung kann sich bei Bedarf eine Nachpassivierung anschließen.
Das ist erforderlich, wenn keine abschließende Lackierung vorgesehen ist und ein langfristiger Korrosionsschutz erreicht werden soll. Durch die Nachpassivierung verringert sich die Porosität der Beschichtung. Feuchtigkeit und andere aggressive Substanzen finden weniger Angriffspunkte.
Prozesskontrolle zur Steuerung der Abläufe
Bei der Niedrigtemperatur-Zinkphosphatierung nehmen drei unterschiedliche Metallionen am Schichtaufbau teil. Sie sind elektrisch positiv geladen und gehören deshalb zu den Kationen. Aus diesem Zusammenhang leitet sich die Bezeichnung Trikation-Zinkphosphatierung ab. Das für die Konversionsbeschichtung benötigte negativ geladene Anion ist das Phosphat-Ion aus der Phosphorsäuere. Außerdem werden Nitrat-Ionen und Zusatzstoffe für den Prozess benötigt.
Damit das Zusammentreffen der vielen Chemikalien zu dem gewünschten Ergebnis führt, sind die optimale Anwendungstemperatur und die erforderlichen Konzentrationen der einzelnen Komponenten genau einzuhalten. Grundlage dafür ist eine sorgfältige Prozesskontrolle.
Automatische Prozesssteuerung
Jede Abweichung von den optimalen Prozessparametern erfordert eine schnelle Gegenmaßnahme. Bei anspruchsvollen Verfahren ist das nur durch eine automatisierte Prozesskontrolle durchführbar: Messfühler, sogenannte Sensoren, erfassen laufend die verschiedenen Parameter und vergleichen sie mit den Sollwerten. Abweichungen werden mit Hilfe von Dosierpumpen oder Regelventilen ausgeglichen. Ist der Gehalt einer Komponente im System zu niedrig, fördert die angesteuerte Dosierpumpe diesen Stoff solange in das Becken, bis der Sollwert wieder erreicht ist. Stimmt die Temperatur nicht mehr, öffnet oder schließt das Regelventil für die Heizung ein bisschen und bringt die Temperatur wieder in den “grünen Bereich”. Wichtige Hinweise für den ordnungsgemäßen Verfahrensablauf lassen sich auch aus dem pH-Wert und der elektrischen Leitfähigkeit der Prozessflüssigkeit schlussfolgern.
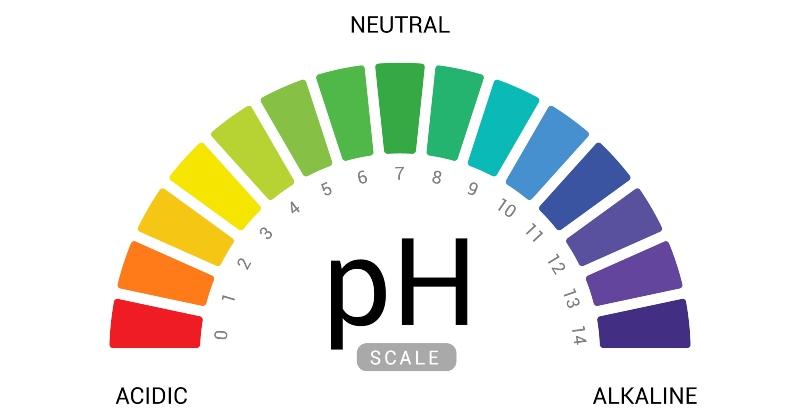
Der pH-Wert ist ein Maß für den Gehalt an freien Wasserstoff-Ionen in der Flüssigkeit und muss in einem engen Toleranzbereich stabil gehalten werden. Das gelingt durch die automatische Zufuhr von pH-Regulatoren. Die elektrische Leitfähigkeit gibt Auskunft über die Gesamtmenge frei beweglicher Ionen. Über diesen Wert lässt sich die Zufuhr der Phosphatier-Ergänzungslösung steuern. Außerdem können die Füllstände der Behälter, aus denen die Dosierpumpen die Chemikalien entnehmen, überwacht werden. Sind entsprechende Rohrleitungssysteme mit geeigneten Absperrarmaturen vorgesehen, kann die automatische Umschaltung auf einen Reservebehälter die kontinuierliche Versorgung sicherstellen.
Auswertung der erfassten Daten für betriebswirtschaftliche Aufgaben
Die Prozesskontrolle lässt sich mit weiteren Funktionen verknüpfen. Beispielweise kann die Steuerung den tatsächlichen Verbrauch an Prozesschemikalien berechnen. Wenn die Vorräte zur Neige gehen, erfolgt eine Meldung. Daraufhin wird automatisch oder durch eine verantwortliche Person die erforderliche Bestellung ausgelöst. Auf diese Weise lässt sich eine wirtschaftliche Lagerhaltung einrichten.