In Zeiten von Industrie 4.0 stehen Unternehmen vor der großen Herausforderung, ihre Prozesse effizienter, kostengünstiger und nachhaltiger zu gestalten. Durch eine kontinuierliche Verfahrensoptimierung lassen sich technische Abläufe – insbesondere in der Produktion – gezielt verbessern, um Produktivität und Ressourceneffizienz zu steigern sowie die Wettbewerbsfähigkeit zu erhöhen. Parallel dazu zielt die Prozessoptimierung auf die Optimierung organisatorischer Abläufe im gesamten Unternehmen, etwa im Workflow-Management oder der Logistik. Beide Konzepte greifen oft ineinander. Die industrielle Optimierung trägt nicht nur zur Kostenreduktion und zur Verbesserung der Durchlaufzeiten bei. Sie hilft auch, die Prozesssicherheit dauerhaft zu gewährleisten, Innovationen voranzutreiben und gesetzliche Vorgaben einzuhalten. Damit ist die Verfahrens- bzw. Prozessoptimierung ein essenzieller Schritt für den langfristigen Erfolg und die Zukunftsfähigkeit eines Unternehmens.
Verfahrensoptimierung vs. Prozessoptimierung: Das ist der Unterschied
Die Verfahrensoptimierung ist ein kontinuierlicher Verbesserungsprozess, der versucht, die Effizienz, die Qualität, die Nachhaltigkeit und den Return on Investment (ROI) industrieller Verfahren zu steigern. In der Praxis überschneidet sie sich oft mit der Prozessoptimierung. Daher werden beide Begriffe häufig synonym verwendet. Die Prozessoptimierung befasst sich allerdings eher mit der Workflow-Optimierung im gesamten Unternehmen, während die Verfahrensoptimierung sich vorrangig auf technische Vorgänge, insbesondere in der Produktion, konzentriert.
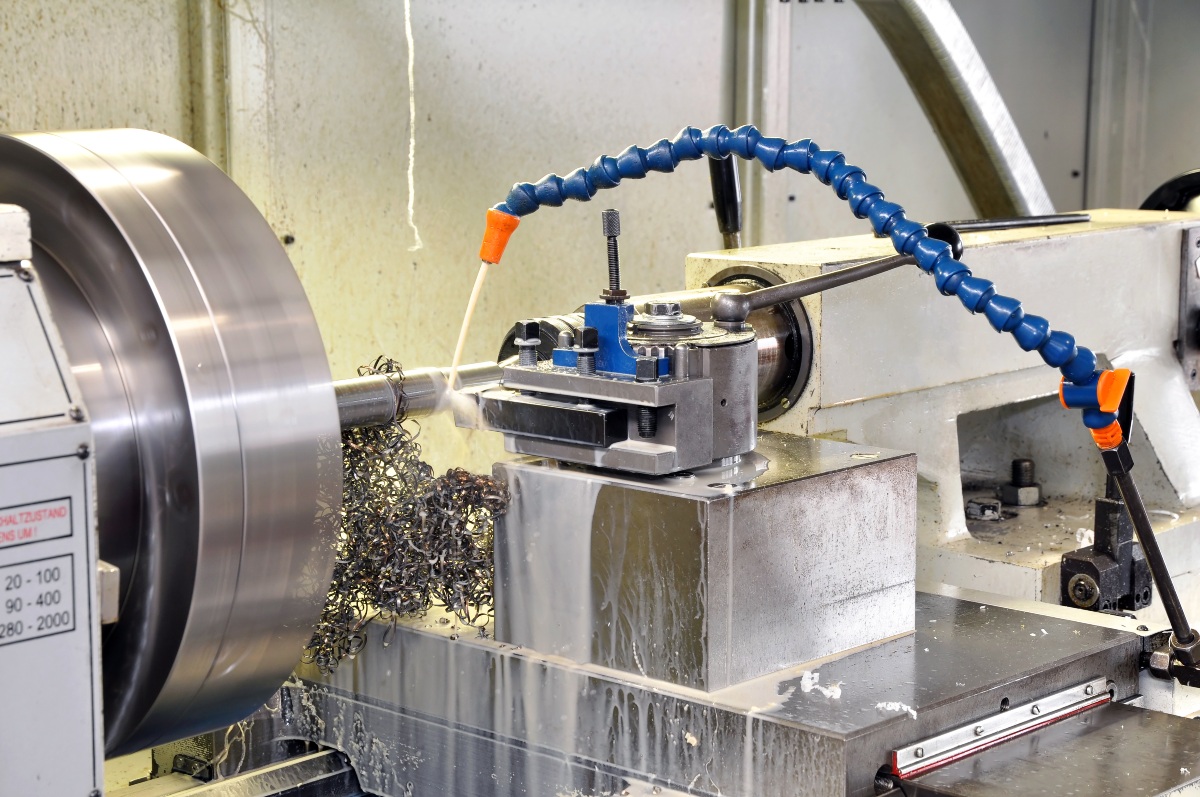
Ziele der Verfahrensoptimierung im Überblick
Die industrielle Optimierung verfolgt vielfältige Ziele, die stark von den Anforderungen des Unternehmens und seinen spezifischen Prozessen abhängen. Hier einige der häufigsten Zielsetzungen:
- Produktivitätssteigerung: Durch die gezielte Verfahrensoptimierung der Produktionsabläufe, den Einsatz effizienterer Technologien und das Reduzieren von Verschwendung können Unternehmen ihre Produktivität und damit auch den ROI erhöhen, ohne zusätzliche Ressourcen zu beanspruchen.
- Verkürzung der Produktionszeiten: Durch eine konsequente industrielle Optimierung kann die Durchlaufzeit gesenkt werden. Das bedeutet eine schnellere Markteinführung von Produkten und oft auch eine Kostenreduktion durch höhere Energieeffizienz.
- Ressourceneffizienz: Optimierte Prozesse helfen, Ressourcen wie Rohstoffe, Wasser und Energie effizienter einzusetzen. Oft wird die industrielle Optimierung mit einer dynamischen Wartungsoptimierung kombiniert, um die Langlebigkeit und damit auch die Nachhaltigkeit des Equipments sicherzustellen.
- Erfüllung gesetzlicher Vorgaben: Viele Produktionsverfahren müssen angepasst werden, um Sicherheits- und Umweltschutzrichtlinien einzuhalten.
- Verbesserung der Produktqualität: Optimierte Verfahren ermöglichen präzisere und gleichmäßigere Ergebnisse. Gleichzeitig sinkt das Risiko für Produktionsfehler und Ausschuss. Damit steigt die Qualität der Erzeugnisse.
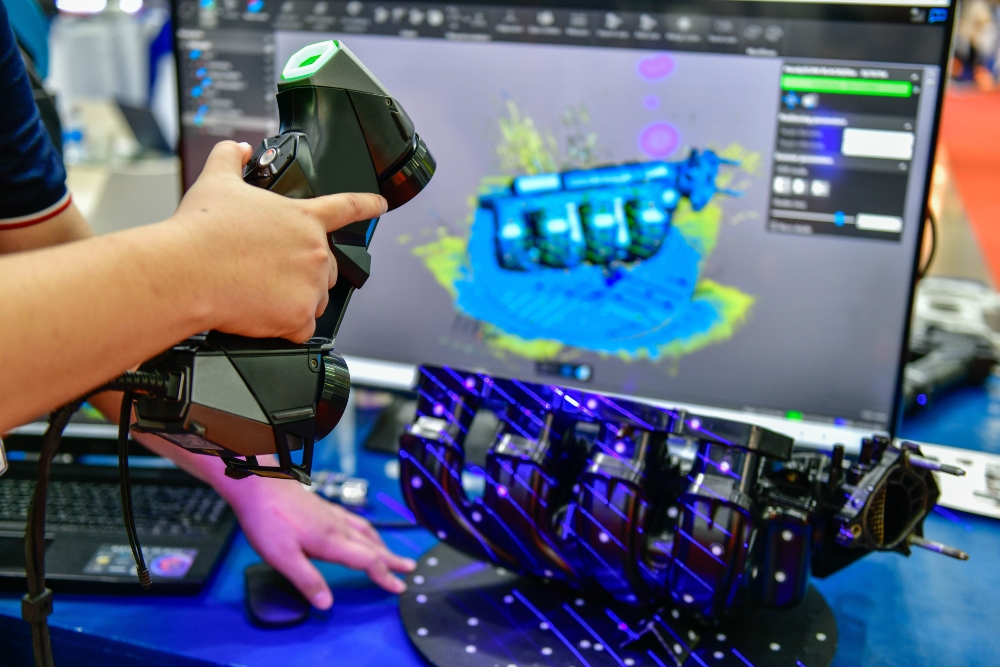
Die wichtigsten Methoden der Verfahrensoptimierung in der Industrie
Die industrielle Optimierung greift auf eine Fülle bewährter Ansätze zurück. Eine zentrale Rolle spielen folgende Methoden und Techniken:
Lean Management
Lean Management, auch als schlankes Management bekannt, zielt darauf ab, Verschwendung durch systematische Workflow-Optimierung zu minimieren und den Wert für den Kunden zu maximieren. In einer Lean-Umgebung findet ein kontinuierlicher Verbesserungsprozess statt. Beim Lean Management werden Abläufe ständig analysiert, um Optimierungsmöglichkeiten in der Wertschöpfungskette zu finden und mit minimalem Aufwand bestmögliche Resultate zu erzielen.
Zentrale Methoden im Lean Management sind:
- Wertstromanalyse: Visuelles Darstellen von Prozessen, um Verschwendung und Engpässe sichtbar zu machen
- Just-in-Time (JIT): Bedarfsgerechte Produktion und Lieferung
- Kanban: Steuerung von Produktionsabläufen auf Basis von Bedarf und Priorität
- Kaizen: Kontinuierlicher Verbesserungsprozess durch Einbindung der Betriebsangehörigen
- 5S-Methode: Ordnung und Organisation am Arbeitsplatz durch Sortieren, Systematisierung, Standardisierung, Sauberkeit und Selbstdisziplin
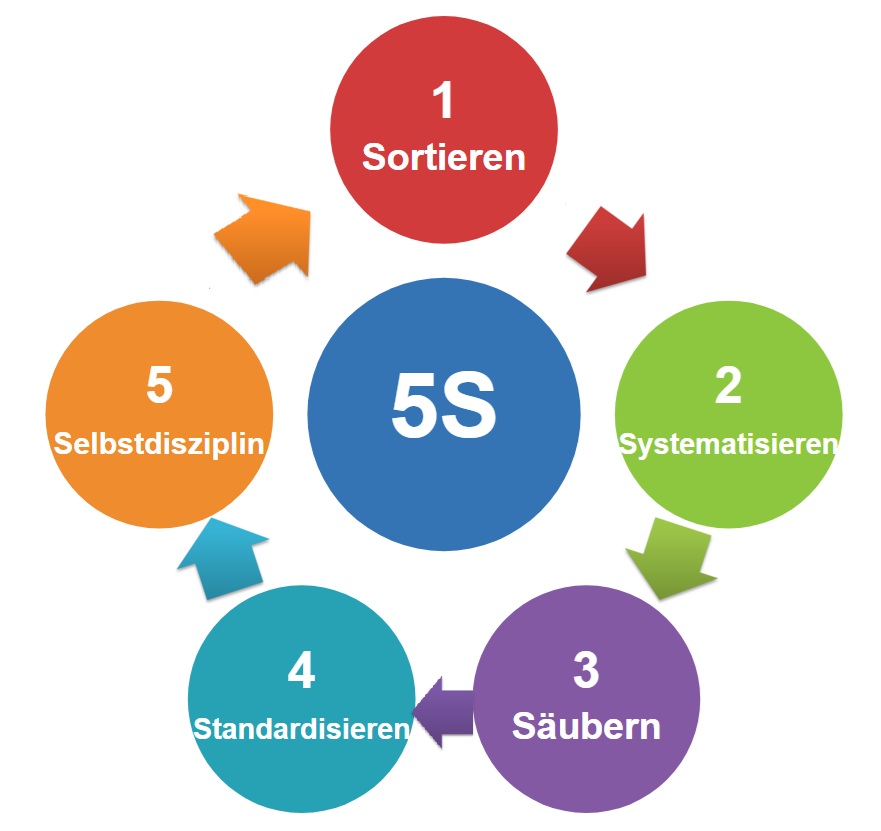
Six Sigma
Six Sigma ist ein datengetriebenes Verfahren zur Prozessoptimierung, das auf Fehlerminimierung und die Reduzierung von Schwankungen und Ineffizienzen abzielt. Der in den 1980er Jahren entwickelte Ansatz hat sich als Standard für das Qualitätsmanagement in zahlreichen Branchen etabliert. Zu den Grundprinzipien von Six Sigma Kundenzentrierung zählen faktenbasierte Entscheidungen, Fehlerminierung und die kontinuierliche Verbesserung der Prozessqualität. In vielen Anwendungen spielt auch die Ausrichtung auf Kundenanforderungen eine wichtige Rolle.
Das Herzstück von Six Sigma ist der DMAIC-Zyklus. Die Abkürzung steht für:
- Define (Definieren): Formulieren der Problemstellung und der Ziele der Prozessoptimierung mit Fokus auf Kundenbedürfnisse und Wertschöpfung
- Measure (Messen): Erhebung relevanter Daten zur Bewertung der aktuellen Leistungsfähigkeit
- Analyze (Analysieren): Analyse von Leistungskennzahlen, sogenannter Key Performance Indicators (KPIs), zur Identifikation von Problemen und Schwankungen
- Improve (Verbessern): Entwickeln und Einbinden von Lösungen, um Probleme zu beheben
- Control (Steuern): Sicherstellen einer nachhaltigen Verfahrensoptimierung, z. B. durch regelmäßige Überwachung und eine fortlaufende Mitarbeiterqualifikation
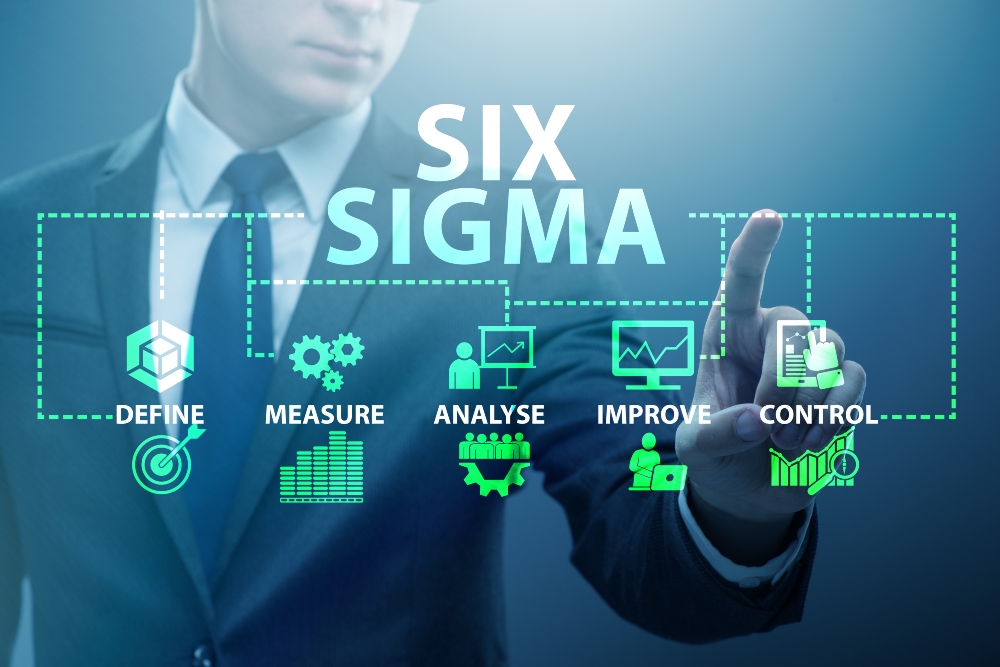
Weitere Ansätze für die industrielle Verfahrensoptimierung
Neben Lean Management und Six Sigma gibt es zahlreiche weitere Methoden, die bei der Prozessoptimierung zur Anwendung kommen können:
- Total Quality Management (TQM): umfassender Ansatz zur Gewährleistung der Qualität in allen Unternehmensbereichen
- Benchmarking: Vergleich eigener Prozesse und Kennzahlen mit denen anderer Unternehmen, um Verbesserungspotenzial zu erkennen
- Agiles Prozessmanagement: Flexible und interaktive Optimierung von Prozessen auf Grundlage kurzfristigen Feedbacks.
- Business Process Reengineering (BPR): radikale Neugestaltung von Prozessen mit dem Ziel, signifikante Verbesserungen zu erreichen
- Lean Six Sigma: Kombination aus Lean Management und Six Sigma
Schon kleine Veränderungen im Detail – wie der Einsatz effizienterer Kühlschmierstoffe, optimierte Teilereinigung oder passender Korrosionsschutzmittel – entfalten in der industriellen Praxis oft große Wirkung: Sie steigern die Prozesssicherheit, senken Ausschuss und fördern nachhaltige Abläufe.
Ablauf der Verfahrensoptimierung in der Industrie
Die industrielle Optimierung folgt einem systematischen Ablauf, der in mehrere Schritte unterteilt ist.
Prozessanalyse
In der Prozessanalyse geht es darum, den Ist-Zustand bestehender Prozesse zu erfassen und Engpässe, Schwachstellen und Verbesserungspotenziale zu identifizieren. Hierzu werden Kennzahlen wie Bearbeitungszeit, Ressourceneinsatz und Fehlerquote erhoben und genau untersucht.
Planungsphase
Dieser Schritt der Prozessoptimierung umfasst das Definieren der Ziele (z. B. schnellere Durchlaufzeit, höhere Energieeffizienz) und das Erarbeiten von Optimierungsansätzen und Alternativen. Die Lösungsansätze können in Umstrukturierungen, der Standardisierung von Prozessen, dem Einführen neuer Technologien oder einer verstärkten Digitalisierung und Automatisierung bestehen. Viele Unternehmen kombinieren die industrielle Optimierung oft mit einer Wartungsoptimierung, um neben der Effizienz der Abläufe auch die Zuverlässigkeit der Maschinen und Anlagen sicherzustellen.
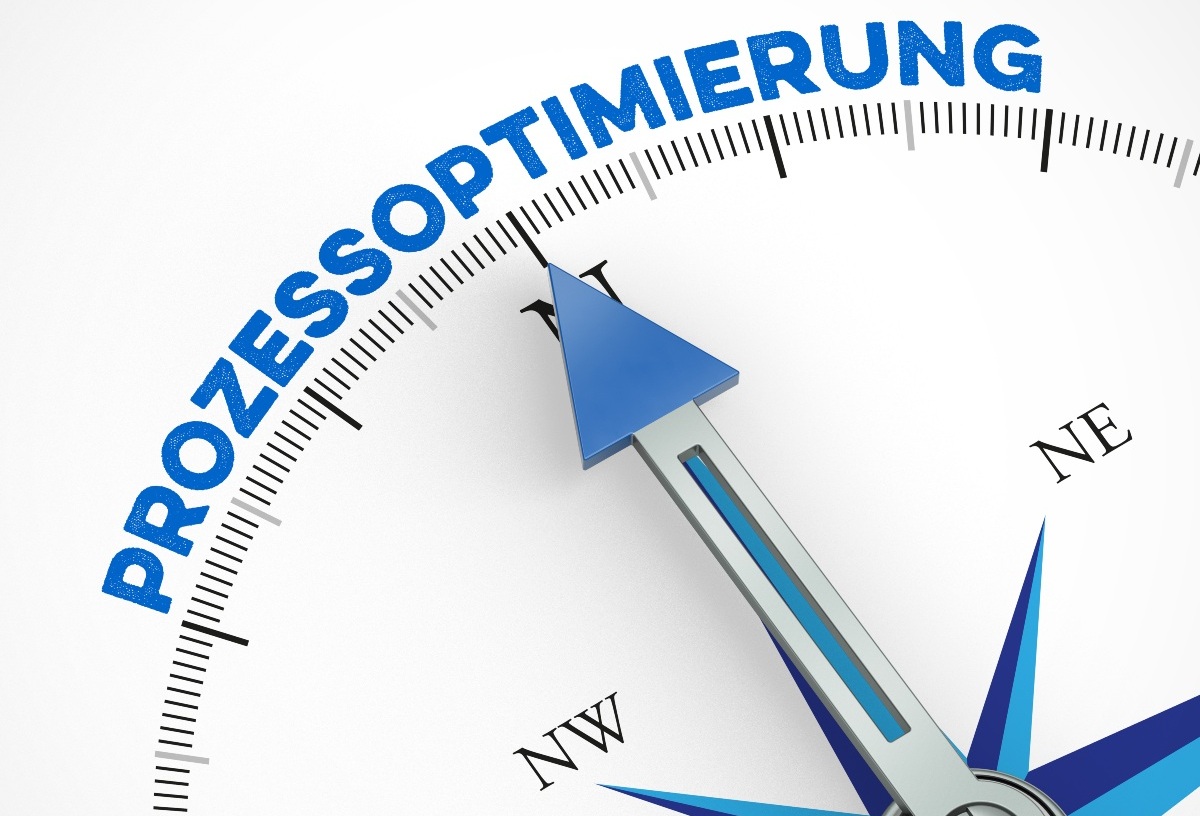
Implementierungsphase
Das Unternehmen integriert die geplanten Lösungen in die bestehenden Prozesse. Für einen reibungslosen Ablauf ist es wichtig, die Änderungen und deren Ziele vorab klar zu kommunizieren. Ebenfalls essenziell für eine erfolgreiche Verfahrensoptimierung ist eine rechtzeitige und umfassende Mitarbeiterqualifikation.
Test- und Überwachungsphase
Vor der vollständigen Einbindung wird der optimierte Prozess in kleinerem Maßstab getestet, um etwaige Probleme frühzeitig zu erkennen und die Prozesssicherheit zu gewährleisten. Nach der Implementierung werden die KPIs des Prozesses beständig überwacht, um das Erreichen der angestrebten Ziele sicherzustellen.
Kontinuierlicher Verbesserungsprozess
Aufgrund des raschen technologischen Wandels im Zeitalter von Industrie 4.0, Digitalisierung und Automatisierung ist ein kontinuierlicher Verbesserungsprozess unverzichtbar. Die kontinuierliche Verbesserung wird vom Qualitätsmanagement koordiniert, wobei Rückmeldungen aus Produktion, Instandhaltung und anderen Bereichen einbezogen werden.