Eine lange Werkzeugstandzeit ist ein zentraler Wirtschaftlichkeitsfaktor in der industriellen Fertigung – besonders in der Metallbearbeitung. Eine entscheidende Rolle spielt sie unter anderem bei der Zerspanung, beim Stanzen und beim Umformen. Lesen Sie hier, welche Vorteile eine hohe Werkzeugstandzeit hat und welche Produkte die Kluthe GmbH für eine diesbezügliche Prozessoptimierung anbietet.
Was ist die Werkzeugstandzeit und warum ist sie so wichtig?
Die Werkzeugstandzeit beschreibt die nutzbare Einsatzdauer eines Werkzeugs, bis es nachgeschliffen oder ersetzt werden muss – typischerweise ohne gravierenden Verschleiß. Je länger diese Phase, desto wirtschaftlicher und prozesssicherer ist die Fertigung.
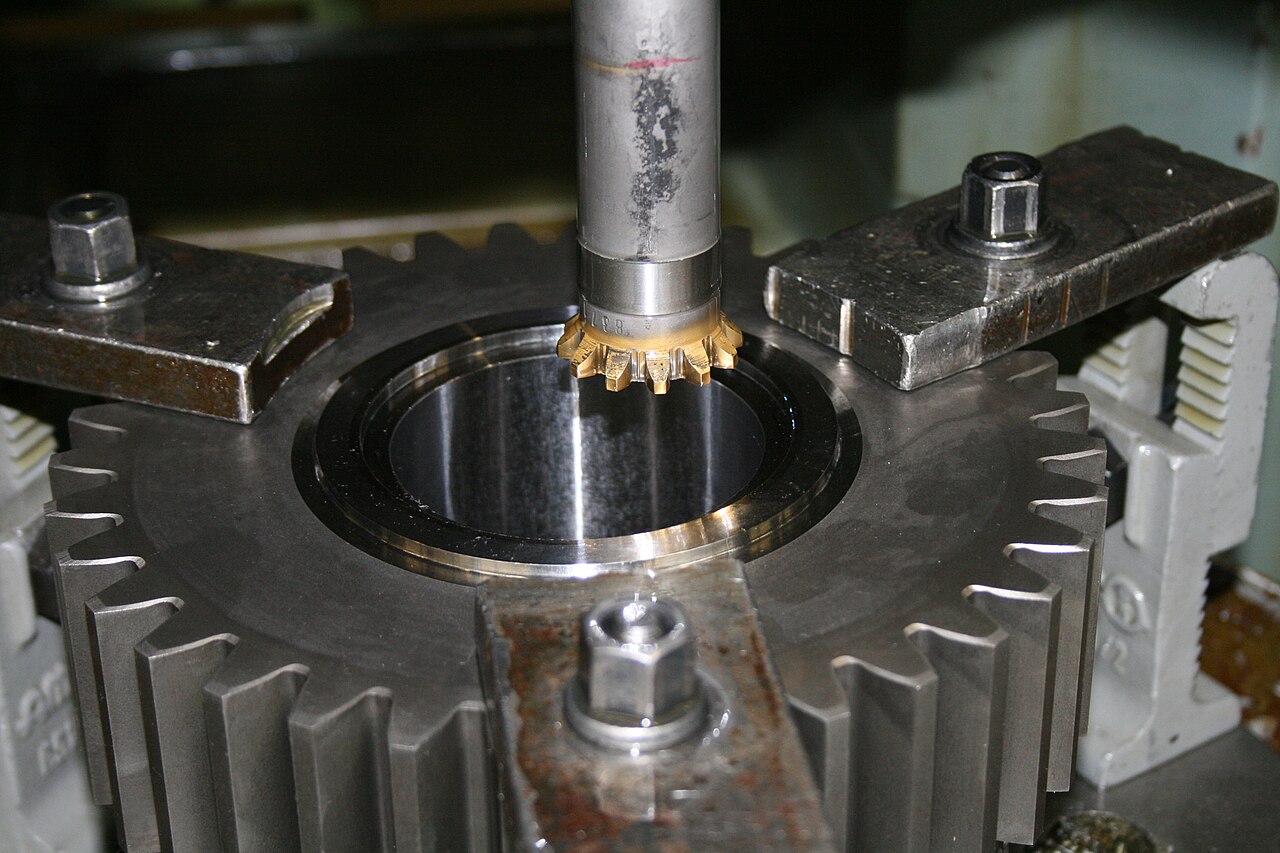
Dass die Standzeit begrenzt ist, hat physikalische Gründe. Während des Bearbeitungsprozesses wird das Werkzeug mechanisch beansprucht und erhitzt sich. Dadurch unterliegt es einer gewissen Abnutzung. Wie stark der Werkzeugverschleiß bei Zerspanungsprozessen ist, hängt von Faktoren wie den folgenden ab:
- Werkzeuggeometrie (spezifische Form des Werkzeugs)
- Material, aus dem das Werkzeug besteht
- konkrete Einsatzbedingungen (insbesondere Vorschub, Schnittgeschwindigkeit, Schnitttiefe)
- Material des zu bearbeitenden Werkstücks
- Temperatur bzw. Temperaturveränderung des Werkzeugs
Verlängern lässt sich die Werkzeugstandzeit durch geringere Vorschub- und Zerspanungsgeschwindigkeiten, eine exakt berechnete Schnitttiefe und eine auf den Prozess zugeschnittene Kühlung und/oder Schmierung.
Anzeichen für den Werkzeugverschleiß
Die Werkzeugstandzeit markiert die erste Verschleißgrenze, während die Werkzeuglebensdauer mit dem endgültigen Ausscheiden des Werkzeugs aus dem Prozess endet. Bei der Zerspanung stehen zwei Arten von Verschleiß im Vordergrund: der Freiflächenverschleiß (an der Werkzeugfreifläche) und der Kolkverschleiß (an der Spanfläche). Ob die Werkzeugstandzeit erreicht ist und ein Werkzeug nachgeschliffen oder ersetzt werden muss, wird meist anhand von Standzeitkriterien wie der Verschleißmarkenbreite oder der Kolktiefe beurteilt.
Neben dem Freiflächen- und dem Kolkverschleiß gibt es in der Metallverarbeitung weitere relevante Verschleißarten wie:
- Verzunderung (Oxidation der Werkzeugoberfläche durch Luftsauerstoff, insbesondere bei höheren Temperaturen)
- Ausbrüche aus dem Werkzeug
- Risse (vor allem durch wechselnde thermische und mechanische Belastungen)
Mit zunehmendem Werkzeugverschleiß sinkt die Zerspanungsleistung des Werkzeugs. In erster Linie leiden die Bearbeitungsgenauigkeit und die Qualität des bearbeiteten Werkstücks.
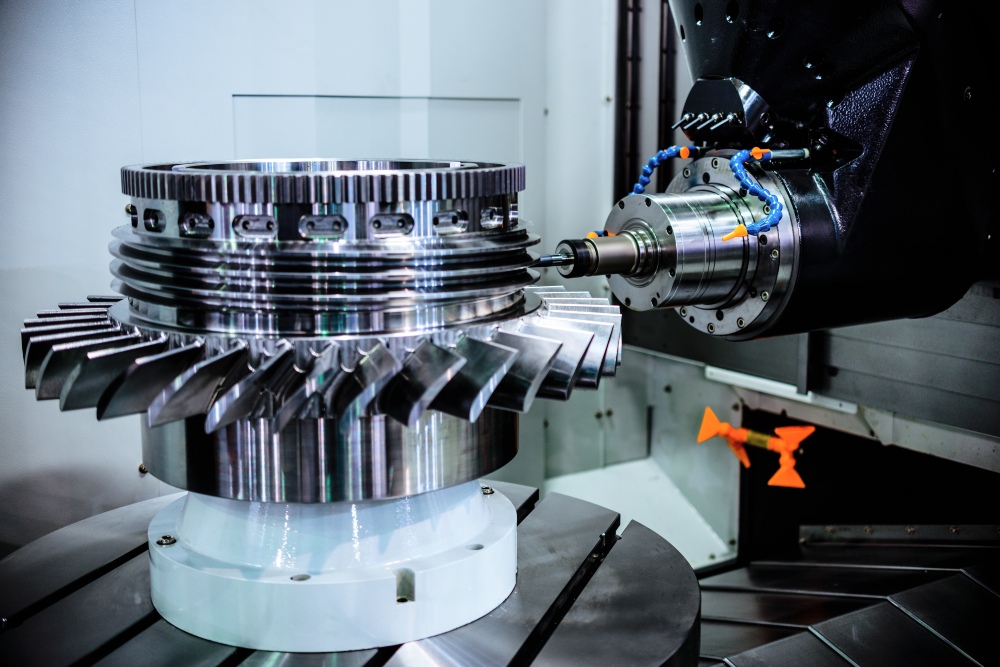
Welche Vorteile bietet eine hohe Werkzeugstandzeit?
Wie wichtig die Zusammenhänge zwischen Werkzeugwechselzeit und Werkzeugstandzeit betont die verlinkte Arbeit der Hochschule Merseburg. Aus einer erhöhten Standzeit von Werkzeugen ergeben sich unter anderem folgende Nutzeffekte:
Höhere Produktivität
Gelingt es, die Standzeit zu verlängern, ist seltener ein Maschinenstillstand für den Werkzeugwechsel erforderlich. Die Maschinen arbeiten länger unterbrechungsfrei, wodurch sich die gesamte Produktionsleistung verbessert.
Bearbeitungsqualität
Werkzeuge mit langer Werkzeugstandzeit gewährleisten über eine längere Zeit hinweg eine gleichmäßige Bearbeitung der Werkstücke. Damit steigt die Produktionsqualität.
Kosteneinsparung
Eine längere Werkzeugstandzeit bedeutet seltenere Werkzeugwechsel und somit auch geringere Kosten für neue Werkzeuge. Das senkt die Produktionskosten und erhöht den Gewinn.
Weniger Wartung
Die Werkzeugstandzeit zu erhöhen, reduziert den Aufwand für die Werkzeug- und Maschinenpflege.
Nachhaltigkeit
Weniger Verschleiß bedeutet weniger Abfall und einen geringeren Ressourcenverbrauch. Somit kommt die Prozessoptimierung auch der Umwelt zugute.
Wie lässt sich bei Werkzeugen die Standzeit verlängern?
Hierfür gibt es mehrere bewährte Strategien, die sich individuell oder in Kombination einsetzen lassen. Schon die Auswahl hochwertiger, für den Anwendungsfall geeigneter Werkzeugmaterialien kann dazu beitragen, die Standzeit zu erhöhen. Spezielle Hartstoffbeschichtungen verbessern den Verschleißschutz des Grundmaterials und verlängern so die Nutzungsdauer des Werkzeugs.
Sitzt das Tool nicht fest genug in der Werkzeugmaschine oder im CNC-Bearbeitungszentrum, kommt es zu Mikrobewegungen. Diese können den Verschleiß erhöhen und sich nachteilig auf die Lebensdauer des Werkzeugs auswirken. Daher ist es wichtig, auf eine stabile und präzise Werkzeugspannung zu achten. Die Bandbreite von Spannsystemen reicht von hydraulisch und pneumatisch über elektromechanisch und magnetisch bis hin zu Nullpunktspannsystemen.
Ein effektiver Kühlschmierstoff in optimaler Konzentration reduziert die Reibung und Hitzeentwicklung. Das schont das Werkzeug und kann dadurch seine Standzeit verlängern. Des Weiteren kann das Anpassen der Vorschub- und Schnittgeschwindigkeit den Verschleiß verringern und die Werkzeugstandzeit erhöhen. Regelmäßige Inspektionen und Wartungen helfen, Abnutzung frühzeitig zu erkennen und zu beheben.
Kühlschmierstoffe als Multitalente bei der Prozessoptimierung
Im Wesentlichen erfüllen Kühlschmiermittel drei wichtige Aufgaben: Zum einen verhindern sie thermische Schäden, indem sie Wärme aufnehmen und abführen. Zum anderen bilden sie einen dünnen Schmierfilm, der die Reibung reduziert. Überdies wirken sie als Transportmedium und befreien die Bearbeitungszone von Spänen und Verunreinigungen. All das trägt gemeinsam mit einem verbesserten Korrosionsschutz dazu bei, den Verschleiß von Werkzeugen zu reduzieren und so deren Werkzeugstandzeit zu verlängern.
Indem sie unerwünschte Oberflächendefekte wie Kratzer oder Rattermarken sowie Verformungen und innere Spannungen in Werkstücken minimieren, sind Kühl- und Schmiermittel gleichzeitig ein wichtiger Faktor für die Qualitätssicherung. Außerdem helfen sie, Bearbeitungsprozesse stabiler und vorhersehbarer zu machen, was die Wahrscheinlichkeit von Maschinenstillständen und Produktionsfehlern verringert und die Prozesssicherheit erhöht.
Standzeit verlängern mit HAKUFORM A 846 DELTA
Mit der HAKUFORM A-Reihe setzt Kluthe Maßstäbe im Bereich wassermischbare Kühlschmierstoffe mit Mineralölen. Die Produkte dieser Serie überzeugen durch Höchstleistungen bei Zerspanungsprozessen und ermöglichen lange Werkzeugstandzeiten. Zugleich verfügen sie über ausgeprägte Korrosionsschutz-Eigenschaften, die ebenfalls zur Prozessoptimierung beitragen. Die Emulsion der Schmierstoffe ist frei von nativen Ölen, die zum Verharzen neigen, und enthält weder leicht flüchtige, geruchsintensive Amine noch Formaldehyddepotstoffe.
Ein typischer Kühlschmierstoff aus dieser Reihe ist HAKUFORM A 846 DELTA. Dieses Produkt punktet neben den genannten Eigenschaften mit einer borfreien Formulierung und erfüllt damit sämtliche Forderungen der TRGS 611. Verschiedene Additive sorgen für eine optimale Zerspanungsleistung und erhöhen den Korrosionsschutz sowohl am Werkzeug als auch an der Maschine.
HAKUFORM A 846 DELTA im praktischen Einsatz
Seinen hohen Nutzen konnte dieser Kühlschmierstoff beispielsweise in einem weltweit führenden Forschungsinstitut beweisen, das präzise Bauteile aus Aluminium, Titan und Edelstahl für die Produktion von Satelliten und Teleskopen herstellt. Die hierfür nötige Präzision lässt sich nur mit einwandfreien Werkzeugen erzielen. Das wiederum erfordert optimale Lösungen für die Kühlung und Schmierung der Fertigungstools.
Durch die Kombination der exzellenten Schmierwirkung und der stabilen Emulsion von HAKUFORM A 846 DELTA gelang es nicht nur, die Werkzeugstandzeit zu verlängern. Die Prozesseffizienz bei der Herstellung der Präzisionsteile konnte ebenfalls deutlich verbessert werden. Zugleich sorgt der angenehme Geruch für ein ansprechenderes Arbeitsumfeld.