« Was versteht man darunter eigentlich? »
Von der Oberfläche eines Gegenstandes hängt ab, wie er auf verschiedene Umgebungseinflüsse reagiert. Durch die gezielte Veränderung der Oberflächeneigenschaften lassen sich die Wechselwirkungen in eine bestimmte Richtung lenken. Im Ergebnis entstehen funktionale Oberflächen, die spezielle Aufgaben erfüllen. Preiswerte Konstruktionswerkstoffe oder Werkstoffe mit geringem Gewicht können auf diese Weise für anspruchsvolle Einsatzwecke fit gemacht werden.
Aufgaben für funktionale Oberflächen
Die möglichen Wechselwirkungen zwischen Oberflächen und der angrenzenden Umgebung sind äußerst vielfältig. Fast alles, was Physik, Chemie und Biologie zu bieten haben, ist hier zu finden. Wichtige Aufgaben:
- Oberflächenschutz
- Korrosionsschutz
- Verschleißschutz
- Schutz vor ungewollten Ablagerungen (Antihaftbeschichtungen gegen Verschmutzung, Vereisung, Niederschlagen von Feuchtigkeit)
- Schutz vor mikrobiologischer Besiedlung durch Bakterien, Algen oder Pilze
Verbesserung der Haftfähigkeit
Funktionale Oberflächen entstehen meistens durch eine Schicht aus Werkstoffen, die die geforderten Eigenschaften mitbringen. In vielen Fällen werden mehrere Schichten benötigt, die unterschiedliche Aufgaben erfüllen. Es muss sichergestellt werden, dass alle Beschichtungen fest haften und die gesamte Oberfläche oder vorgesehene Oberflächenbereiche vollständig bedecken.
Beispiele dafür sind:
- Herstellen einer geeigneten Oberflächenstruktur (Aufrauen, Schleifen)
- Erzeugung von Konversionsschichten (Phosphatieren, Chromatieren)
- Verringerung der Oberflächenspannung für gute Benetzbarkeit
- Metallisierung von Kunststoffen, Glas oder Keramik zum Beispiel zur Vorbereitung auf eine galvanische Beschichtung oder Lackierverfahren wie die kathodische Tauchlackierung
- Förderung der mikrobiellen Besiedlung für biotechnologische Verfahren
Erzeugung spezieller Gebrauchseigenschaften
Funktionale Schichten werden immer häufiger eingesetzt, um spezielle Gebrauchseigenschaften hervorzubringen. Dabei nutzt man die Reaktion von Stoffen auf physikalische oder chemische Einflüsse. Beispiele für die Funktionen, die von Oberflächenschichten übernommen werden, sind:
- Verstärken oder Herstellen der elektrischen Leitfähigkeit (Widerstand elektrischer Kontakte verringern, elektrostatische Aufladung vermeiden, Touchdisplays herstellen)
- elektrische Isolierung
- Verringerung von reibungsbedingten Energieverlusten
- Verstärkung der Reibung, um Aus- oder Abrutschen zu vermeiden
- Verhindern, dass Gase oder Dämpfe eindringen bzw. entweichen (Barriereschichten)
- Ausrüstung von Membranen zur Stofftrennung (Ultrafiltration, Umkehrosmose)
- Verhindern von Lichtreflexion (Entspiegelung)
- Verspiegeln für verbesserte Licht- und Wärmereflektion
- Sensoroberflächen zur Bestimmung von chemischen Substanzen in Stoffgemischen für die Prozessteuerung und Qualitätssicherung
- Anzeige von Temperaturänderungen durch Farbwechsel
Beschichtungstechniken
Die Oberflächentechnik unterscheidet bei der Beschichtung zwischen nasschemischen Verfahren und Gasphasenverfahren. Bei nasschemischen Verfahren liegen die Beschichtungsstoffe in flüssiger Form vor. Schmelzen, Lösungen, Emulsionen (Tröpfchen in Flüssigkeit) oder Suspensionen (Feststoffpartikel in Flüssigkeit) werden auf die Werkstoffoberflächen aufgetragen oder aufgespritzt. Alternativ werden die zu beschichtenden Teile in die Flüssigkeit getaucht. Gasphasenverfahren nutzen das Bestreben von gasförmigen Stoffen aus, sich im Raum gleichmäßig zu verteilen. Dadurch lassen sich sehr dünne Schichten im Nanometerbereich erzeugen.
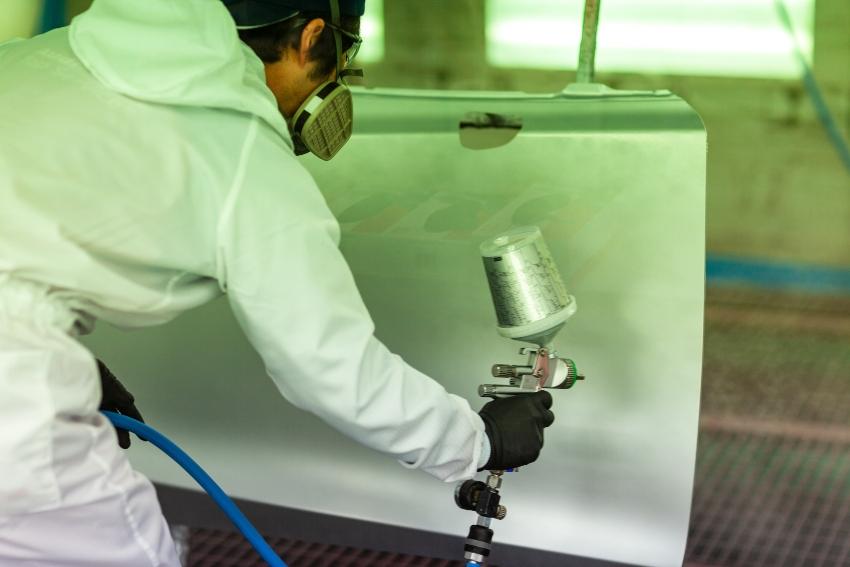
Nasschemische Verfahren
Zu den nasschemischen Verfahren, mit denen funktionelle Schichten erzeugt werden, zählen das Lackieren, die Erzeugung von Konversionsschichten und die Galvanisierung. Beim Lackieren sind die schichtbildenden Stoffe in einer Flüssigkeit fein verteilt. Nach dem Auftragen verdunstet die Flüssigkeit und hinterlässt eine feste Schicht. Neben dem Korrosionsschutz und der Dekoration lassen sich auf diese Weise funktionale Schichten erzeugen, die die Gleiteigenschaften von Oberflächenpaarungen verbessern, einen Temperaturwechsel anzeigen oder vor Verschleiß schützen.
Konversionsschichten entstehen, wenn sich Substanzen mit dem Grundmaterial zu neuen chemischen Verbindungen umsetzen. Die Schichten verbessern die Beständigkeit gegen Korrosion und dienen als Haftvermittler für nachfolgende Lackierprozesse. Während der Galvanisierung scheiden sich Metallionen aus einer Salzlösung auf dem Grundmaterial ab. Das Verfahren dient der Veredelung von Metallen und dem Korrosionsschutz. Häufig angewendet werden das Vergolden, das Versilbern, das Verkupfern, das Verchromen und das Verzinken.
Gasphasenverfahren
Bei den Gasphasenverfahren unterscheidet man zwischen der chemischen Gasphasenabscheidung (englisch: chemical vapour deposition, abgekürzt CVD) der physikalischen Gasphasenabscheidung (englisch: physical vapour deposition, abgekürzt PVD) und den plasmaunterstützten Verfahren.
Chemische Gasphasenabscheidung
Die chemische Gasphasenabscheidung erfolgt in einem geschlossenen Reaktionsbehälter, der das zu beschichtende Bauteil, den Beschichtungsstoff und ein Trägergas enthält. Der Beschichtungsstoff und das Trägergas regieren miteinander zu einem gasförmigen Zwischenprodukt. Das Gas verteilt sich gleichmäßig im Behälter.
Trifft es auf die Bauteiloberfläche, zerfällt die Verbindung. Die Teilchen des Beschichtungsstoffs werden freigesetzt. Es baut sich eine Schicht auf, die in Bauteilnähe aus einem Gemisch aus Grund- und Beschichtungsstoff besteht. Nach außen nimmt der Anteil des Grundmaterials in der Beschichtung ab.
Physikalische Gasphasenabscheidung
Bei der physikalischen Gasphasenabscheidung wird der Beschichtungsstoff im Hochvakuum verdampft. Das Hochvakuum ist erforderlich, um chemische Reaktionen des Dampfes mit der Luft zu verhindern. Die Wärmezufuhr erfolgt in der Regel über eine elektrische Widerstandsheizung oder durch einen Elektronenstrahl. Auf diese Weise lassen sich funktionale Oberflächen erzeugen, die aus unterschiedlichen Stoffen zusammengesetzt sind.
Plasmaunterstützte Beschichtungsverfahren
Plasma ist ein gasartiger Stoff, der nicht aus Molekülen oder Atomen sondern aus Ionen, Elektronen und Bruchstücken von Molekülen besteht. Es kann kalt sein, wie zum Beispiel in Leuchtstoffröhren oder heiß, wie beispielsweise in einer Flamme. Erzeugt wird es durch den Eintrag von Energie in ein Gas. Energiequellen sind Lichtbögen, hohe elektrische Feldstärken oder starke Magnetfelder. Die plasmaunterstützte Beschichtungstechniken bieten ein breites Anwendungsfeld für die Erzeugung funktionaler Oberflächen, weil sie sich einerseits durch die Gaszusammensetzung und andererseits durch die elektrischen Größen der Energiequelle in einem weiten Bereich einstellen lassen.
Über das Plasma lassen sich Werkstoffe chemisch oder physikalisch beschichten, die den hohen Temperaturen bei anderen Verfahren nicht standhalten. Die Anwendungsgebiete der plasmaunterstützen Oberflächentechnik reichen von der Vorbehandlung zur Verbesserung der Haftung nachfolgender Beschichtungen über die Erzeugung definierter Oberflächenstrukturen, die Reinigung und Desinfektion bis zur Abscheidung unterschiedlichster Schichten. Mit Hilfe von Plasma erzeugte funktionale Oberflächen können zum Beispiel Schutz vor Witterungseinflüssen, Korrosion und Verschmutzung bieten und das Benetzungsverhalten oder tribologische Eigenschaften einstellen.
Es ist möglich, wasserabweisende oder gut benetzbare Oberflächenschichten zu generieren oder die Reibung in mechanischen Systemen so zu vermindern, dass auf den Einsatz von Schmiermitteln verzichtet werden kann. Weitere Einsatzgebiete sind die Veredlung von Textilien und die Beschichtung von Folien.