Der Eiffelturm ist das Symbol von Paris. Vor rund 130 Jahren wurde dieses Bauwerk aus Stahl pünktlich zur Weltausstellung fertiggestellt und hat bis heute nichts von seiner Faszination eingebüßt. Mehr als 7 Millionen Besucher besichtigen den unter der Ägide von Gustave Eiffel erbauten Stahlturm jedes Jahr. Der Eiffelturm besteht aus über 18.000 Einzelteilen aus Metall und die Stahlkonstruktion wiegt um die 7300 Tonnen. Um diese vor den ärgsten Feinden – Witterung, Sauerstoff und Feuchtigkeit – zu schützen, werden allein alle sieben Jahre bis zu 60 Tonnen Farbe benötigt, die dem Turm nicht nur einen neuen Anstrich verleihen, sondern vor allem als Korrosionsschutz dienen.
Damit diese äußerste Schicht ihre Aufgabe erfüllen und den darunter liegenden Stahl wirkungsvoll schützen kann, ist eine gute Verbindung zwischen Metalloberfläche, Zwischen- und Deckbeschichtung notwendig.
Eine wirkungsvolle Oberflächenbehandlung spielt dabei eine, hier im wahrsten Sinne des Wortes, tragende Rolle. Die Phosphatierung und, im Fall von Eisen und Stahl, die Eisenphosphatierung sind hier häufig die Mittel der Wahl.
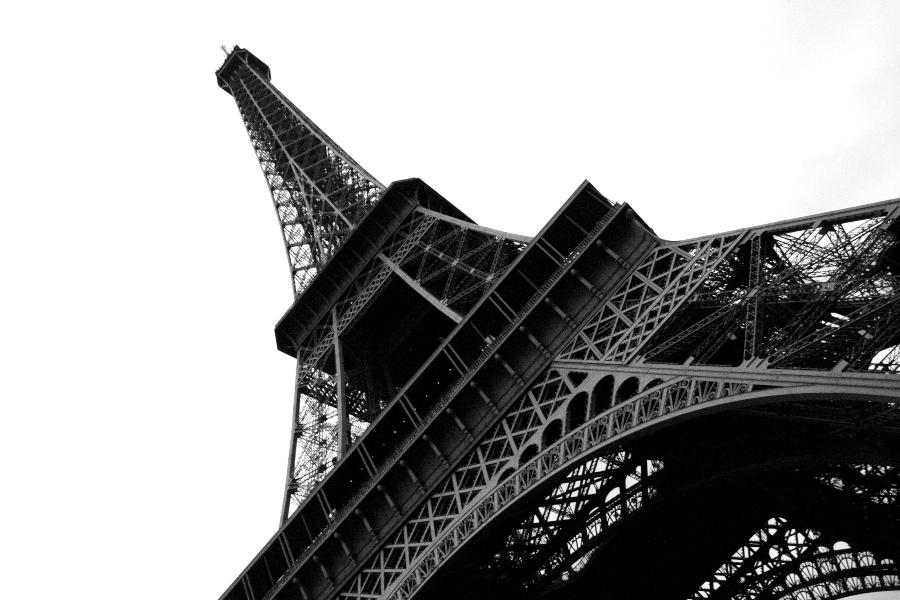
Die häufigsten Metalle für die Konstruktion in der verarbeitenden Industrie
Schiff- oder Hochbau, die Automobil- oder Flugzeugindustrie – alle diese Industriezweige benötigen Stahl und Eisen in mehr oder weniger hohen Anteilen. Die beiden Varianten, die sich durch die Qualität unterscheiden, gehören zu den weltweit am meisten eingesetzten Metallen und Fachleute schätzen ihren Anteil auf 95% an allen verarbeiteten Metallen. Neben den Vorteilen, wie der hohen Stabilität, der guten Bearbeit- und Formbarkeit sowie der Recyclingfähigkeit, hat Eisen – und damit auch Stahl – einen entscheidenden Nachteil: es reagiert mit dem Sauerstoff aus der Luft zu Eisenoxid. Dieser Vorgang, umgangssprachlich als rosten bezeichnet, wird durch Witterungseinflüsse, wie Feuchtigkeit oder Salze, noch unterstützt.
Die “National Association of Corrosion Engineers” schätzt, dass sich die Kosten für Schäden, die durch Korrosion entstehen, in einem hochtechnisierten Land auf 3-6% des Bruttosozialproduktes belaufen können. Daher wird schon von jeher viel in den Korrosionsschutz gesteckt, um Bauwerke und Konstruktionen über die Jahre zu schützen.
Die International Standardization Organisation (ISO) hat mit der ISO 12944 ein eigenes Regelwerk geschaffen, in dem Normen und technische Regeln für den Korrosionsschutz von Stahlkonstruktionen durch verschiedene Beschichtungssysteme niedergeschrieben sind. Eines der wichtigsten Verfahren in der Oberflächentechnik ist dabei die Eisenphosphatierung.
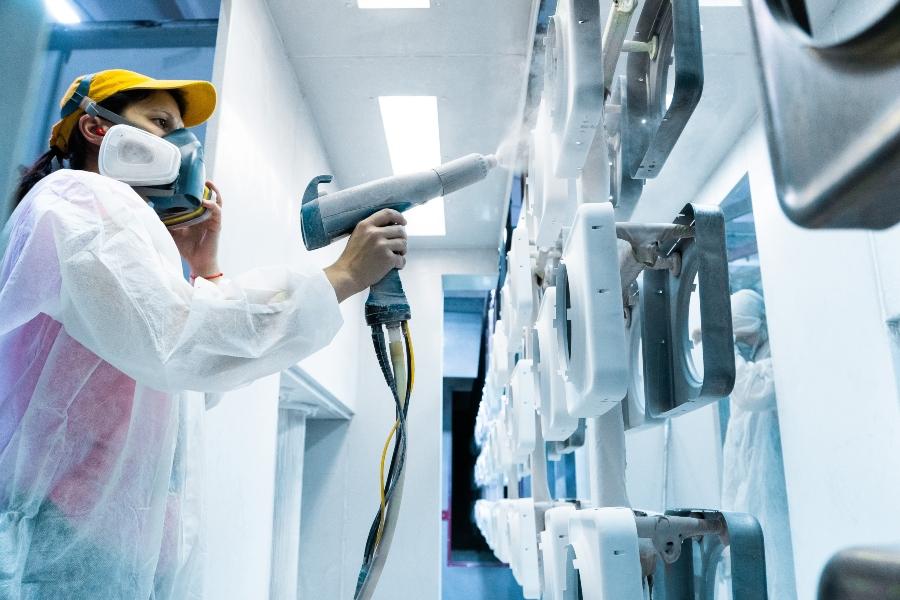
Eine umfassende Oberflächenbehandlung ist das A und O im Korrosionsschutz
Um ein Stahl- oder Eisenteil wirkungsvoll vor Korrosion zu schützen, braucht es eine Barriere, die Sauerstoff, Feuchtigkeit und Salze (bzw. Elektrolyte) möglichst umfassend abhält. In den meisten Fällen wählt man dafür eine Lackierung. Dabei ist es essenziell, dass diese gut auf dem Metall haftet und eine langanhaltende Verbindung zwischen Lack und Metall hergestellt wird. Damit Lack gut haften kann, müssen zwei Voraussetzungen erfüllt sein:
(1) die Metalloberfläche muss absolut und einwandfrei sauber sein
(2) die Metalloberfläche muss entsprechend vorbehandelt sein. Ein in der Oberflächentechnik häufig genutztes Vorbehandlungsverfahren ist die Phosphatierung.
Die Phosphatierung ist ein chemisches Verfahren zur Oberflächenbehandlung
Bei der Phosphatierung reagiert die Metalloberfläche mit einer wässrigen Lösung aus Alkaliphosphaten sowie freier Phosphorsäure. Dabei wird in der Oberflächentechnik zwischen zwei Verfahren unterschieden: dem nicht-schichtbildenden und dem schichtbildenden Verfahren. Bei beiden Methoden, die auch als Konversionsverfahren bezeichnet werden, bilden sich Schichten aus. Sie unterscheiden sich nur in der chemischen Zusammensetzung.
Das nicht-schichtbildende Verfahren: die Eisenphosphatierung
Bei der Eisenphosphatierung laufen verschiedene Reaktionen an der Oberfläche gleichzeitig ab.
Das Werkstück wird in eine Phosphatierlösung gegeben, die aus freier Phosphorsäure und sauren Alkaliphosphaten, beispielsweise Natriumhydrogenphosphat, besteht.
Der pH-Wert der Lösung liegt im sauren Bereich zwischen 3,5 und 6. Im ersten Schritt, der Beizreaktion, wird die Metalloberfläche angegriffen und Eisenionen gehen unter gleichzeitiger Wasserstoffentwicklung in Lösung. Im zweiten Schritt reagieren die zweiwertigen Eisenionen mit den in der Lösung vorhandenen Hydrogenphosphaten zu schwerlöslichen Eisen(III)phosphaten sowie, in kleineren Anteilen, auch zu Eisen(II)phosphaten sowie zu Eisenoxiden. Diese Schritte laufen nicht nur nacheinander, sondern auch parallel nebeneinander ab.
Auf der Oberfläche der Eisenmetalle bildet sich ein amorphes Gemisch aus Eisenphosphaten, Eisenoxiden und Eisenhydroxiden. Es können Schichtdicken zwischen 0,15 Mikrometern und bis zu 8 Mikrometern erreicht werden. Vor allem sind die Schichten aber ein guter Untergrund für nachfolgende Beschichtungen, da eine amorphe, mikroporöse beziehungsweise auch mikrokapillare Struktur gebildet wird. Diese vereinfacht die Verankerung nachfolgender Schichten, beispielsweise durch eine Lackierung.
In der Phosphatierlösung befinden sich zusätzlich Oxidationsmittel, wie Bromate, Chlorate, Nitrate oder Molybdate. Diese reagieren mit dem bei der Beizreaktion freiwerdenden Wasserstoff und oxidieren diesen zu Wasser, um dadurch eine Blockade der Metalloberfläche durch Wasserstoffbläschen zu verhindern. Alternativ können auch organische Verbindungen, wie m-Nitrobenzolsulfonat oder Nitroguanidin als Oxidationsmittel eingesetzt werden.
Das schichtbildende Verfahren – die Phosphatierung
Der Unterschied der schichtbildenden Verfahren zur Eisenphosphatierung besteht darin, dass sich auf der Oberfläche kein Eisenphosphat, sondern Zinkphosphate oder gemischte Zink-Eisen- und Zink-Manganphosphate bilden. Die Phosphatierlösungen enthalten die entsprechenden Kationen, die sich als Phosphatverbindungen auf der Eisenoberfläche ablagern. Auch diese Oberflächentechnik baut auf zwei Schritte – der Beizreaktion und der anschließenden Schichtbildung – auf. Wie bei der Eisenphosphatierung werden Oxidationsmittel zugesetzt, die mit dem bei der Beizreaktion freigesetzten Wasserstoff reagieren. Beim schichtbildenden Verfahren werden etwas dickere Schichten als bei der reinen Eisenphosphatierung gebildet und die Schutzwirkung wird daher als etwas höher eingestuft.
Eisenphosphatierung in der Praxis
Die Phosphatierung erfolgt normalerweise in mehreren Schritten und damit auch abgetrennt in verschiedenen Bädern. Die Spritztechnik ist dabei dem Tauchverfahren vorzuziehen, da eine viel bessere Reinigungswirkung erreicht wird. Die Beizreaktion, die als Reinigungsschritt zur Entfernung von unerwünschten Oxiden üblicherweise separat erfolgt, kann bei der Eisenphosphatierung im gleichen Bad wie die Phosphatierung erfolgen. Dieser kombinierte Schritt dauert im Schnitt ein bis zwei Minuten im Spritzverfahren, im Tauchverfahren circa drei bis fünf Minuten.
Diese Zeiten reichen im Schnitt aus, um eine ausreichend dicke Konversionsschicht zu erreichen. Die Badtemperaturen liegen bei 40°C – 60°C. Anschließend werden die Teile gespült, zunächst in einem Becken mit unbeheiztem Brauchwasser und anschließend in einem Bad mit vollentsalztem Wasser. Dadurch werden die noch auf der Oberfläche vorhandenen Reste und löslichen Salze sehr gut entfernt.
Vorteile einer Eisenphosphatierung gegenüber anderen Verfahren der Oberflächentechnik
Gegenüber anderen Oberflächenbehandlungen hat die Eisenphosphatierung einige Vorteile. Die Eisenphosphatierung erhöht beispielsweise die Elastizität des Materials und die Gleiteigenschaften der Metalloberfläche. Das kann für nachfolgende Prozesse, wie der Kaltumformung von Stahl oder bei der Montage, vorteilhaft sein. Außerdem bietet allein die Bildung der Konversionsschicht, zumindest kurzfristig, einen meistens ausreichenden Korrosionsschutz. Werden die Werkstücke später nur in Innenräumen genutzt und keinen extremen Bedingungen ausgesetzt, kann dieser Schutz sogar schon genügen.
In allen anderen Fällen reicht er zumindest bis zum nächsten Prozessschritt aus und durch Wachsen oder Einölen kann der Schutz weiter verbessert werden. Schließlich haben alle Werkstücke mit einer Metall-Phosphatschicht einen hohen elektrischen Widerstand. Dadurch können zum Beispiel Elektrobleche gegeneinander isoliert werden.
Dies gilt allerdings für jede Phosphatierung und ist nicht allein auf das Verfahren der Eisenphosphatierung begrenzt. Letzteres hat allerdings den Vorteil, dass es sich um ein relativ kostengünstiges Verfahren in der Oberflächentechnik handelt und damit weit verbreitet ist.