« Effizienzvergleich in der Metallverarbeitung »
In vielen Bereichen der Metallverarbeitung, insbesondere in der Zerspanung, ist Schmierung unverzichtbar. Die Trockenzerspanung punktet zwar mit geringen Betriebskosten und Umweltfreundlichkeit, hat aber auch Nachteile wie erhöhten Werkzeugverschleiß und eine thermische Belastung des Werkstücks. Alternativen sind die Nassbearbeitung und die Minimalmengen-Schmierung (MMS). Wie funktionieren die beiden Methoden und worin liegen die Vorteile der Minimalmengen-Schmierung?
Nassbearbeitung: Weniger Verschleiß durch optimierte Kühlung
Bei dieser Methode werden große Mengen an Kühlschmierstoffen, meist Emulsionen, eingesetzt, um Reibung zu reduzieren, Wärme abzuleiten und die Lebensdauer der Werkzeuge zu verlängern. Dabei wird das Werkzeug regelrecht mit dem Kühlmittel umspült.
Das ständige Einbringen von Flüssigkeit verhindert hohe Temperaturen, die sich nachteilig auf die Maßhaltigkeit und die Oberflächenqualität des Werkstücks auswirken könnten. Zugleich helfen die Kühlschmierstoffe, abgetragene Späne zu entfernen. Das verbessert die Prozessstabilität. Da sich die mechanische Belastung der Werkzeuge verringert, erhöht sich deren Standzeit. Das sorgt für weniger Maschinenstillstand, ermöglicht ein insgesamt effektiveres Arbeiten und senkt die Kosten für die Neubeschaffung oder das Nachschärfen von Werkzeugen.
Mit der Nassbearbeitung gehen jedoch auch einige Nachteile einher. Die Beschaffung, Aufbereitung und Entsorgung der Kühlschmierstoffe erfordern zusätzlichen Aufwand und verursachen erhebliche Kosten. Zudem können bestimmte Emulsionen Atemwegsbeschwerden oder Hautreizungen hervorrufen, was den Einsatz entsprechender Schutzmaßnahmen nötig macht. Bei unsachgemäßer Handhabung können darüber hinaus negative Auswirkungen auf die Umwelt nicht ausgeschlossen werden.
Minimalmengen-Schmierung: Effizienz durch Präzision
Bei der MMS wird ein Gemisch aus Öl und Gas (meist Druckluft) als Aerosol direkt am gewünschten Wirkungsort aufgebracht. Damit lässt sich eine optimale Kühlleistung bei der Zerspanung mit deutlich weniger Schmiermittel sicherstellen. Der Maximalvolumenstrom bei der Minimalmengen-Schmierung liegt bei unter 50 Milliliter pro Stunde, während es bei der konventionellen Nassbearbeitung bis zu 12.000 Liter sein können.
Arten der Minimalmengen-Schmierung
Die Zufuhr des Schmiermittels kann bei der MMS sowohl extern als auch intern erfolgen. Welche Methode sich am besten eignet, hängt vom Einsatzszenario ab.
Bei der externen Zufuhr wird der Kühlschmierstoff über Sprühdüsen aufgebracht, die sich am Spindelkopf befinden. Diese Vorgehensweise eignet sich gut für die Nachrüstung von Werkzeugmaschinen, da sich das benötigte Equipment relativ einfach am Spindelkopf anbringen lässt. Typische Anwendungsfelder sind Standardprozesse wie Bohren, Sägen, Drehen oder Fräsen. Nachteilig sind die begrenzten Anpassungsmöglichkeiten der Düsen auf unterschiedliche Längen und Durchmesser der Werkzeuge. Dadurch kann der Sprühstrahl Abschattungseffekten und Streuverlusten unterliegen, wodurch die Aerosole die Schneide nicht immer optimal erreichen.
MMS-Systeme mit innerer Zufuhr ermöglichen die präzise Zuführung des Kühlschmierstoffs durch das Werkzeug hindurch direkt an die Bearbeitungsstelle. Somit sind die Aerosole im gesamten Bearbeitungsprozess kontinuierlich an den kritischen Stellen verfügbar. Das ermöglicht sehr große Bohrtiefen und Schnittgeschwindigkeiten. Eine Umrüstung auf dieses System kann jedoch mit hohen Kosten verbunden sein, da die erforderlichen Kanäle durch die Maschinenspindel hindurchgeführt werden müssen.
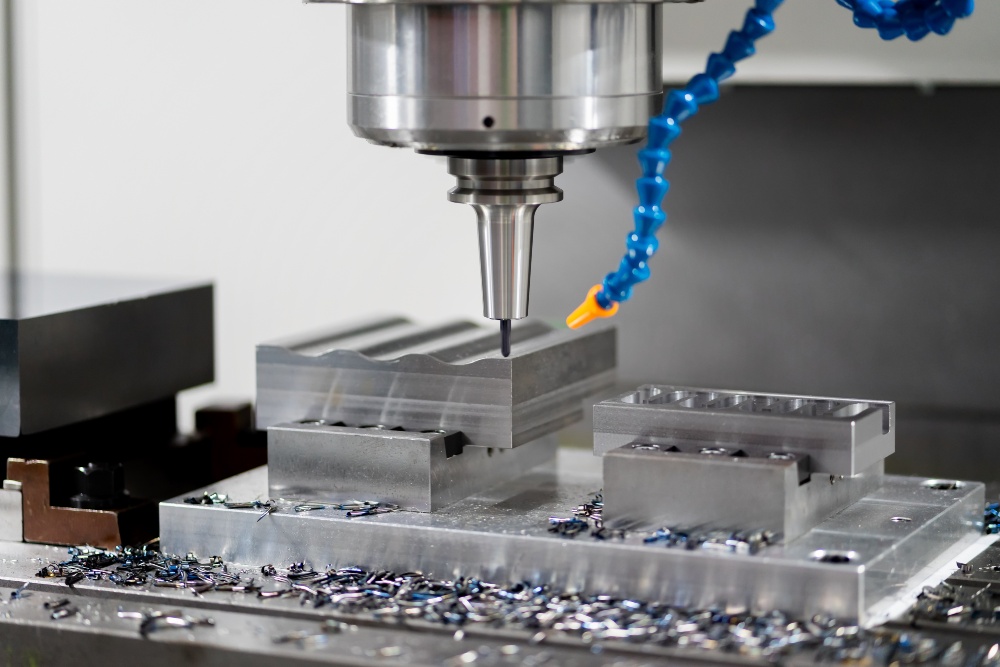
Vorteile der Minimalmengen-Schmierung gegenüber der Nassbearbeitung
Ist die Trockenzerspanung keine Option, stellt sich die Frage, welche Methode der Kühlschmierung sich für den jeweiligen Anwendungsfall am besten eignet. Eine Minimalmengen-Schmierung ist in aller Regel die bessere Wahl, wenn Wirtschaftlichkeit und Umweltschutz im Vordergrund stehen und weder eine intensive Kühlung noch eine hohe Spülleistung erforderlich sind.
Die MMS ermöglicht eine gezielte Schmierung. Das senkt den Kühlmittelverbrauch erheblich, während die Prozesseffizienz steigt. Die Kühlleistung ist geringer als bei der Nassbearbeitung, jedoch lässt sich mit einer präzisen Abstimmung auf Werkzeug, Werkstück und Maschinenparameter trotzdem eine optimale Wärmeableitung erreichen. Dadurch sind auch hier die Oberflächenqualität und die Maßgenauigkeit gewährleistet.
Unternehmen können vom Einsatz der MMS gleich mehrfach profitieren, nicht zuletzt im finanziellen Bereich. Auch hinsichtlich des Arbeitsschutzes, der Mitarbeitergesundheit und des ökologischen Fußabdrucks sind große Nutzeffekte zu verzeichnen.
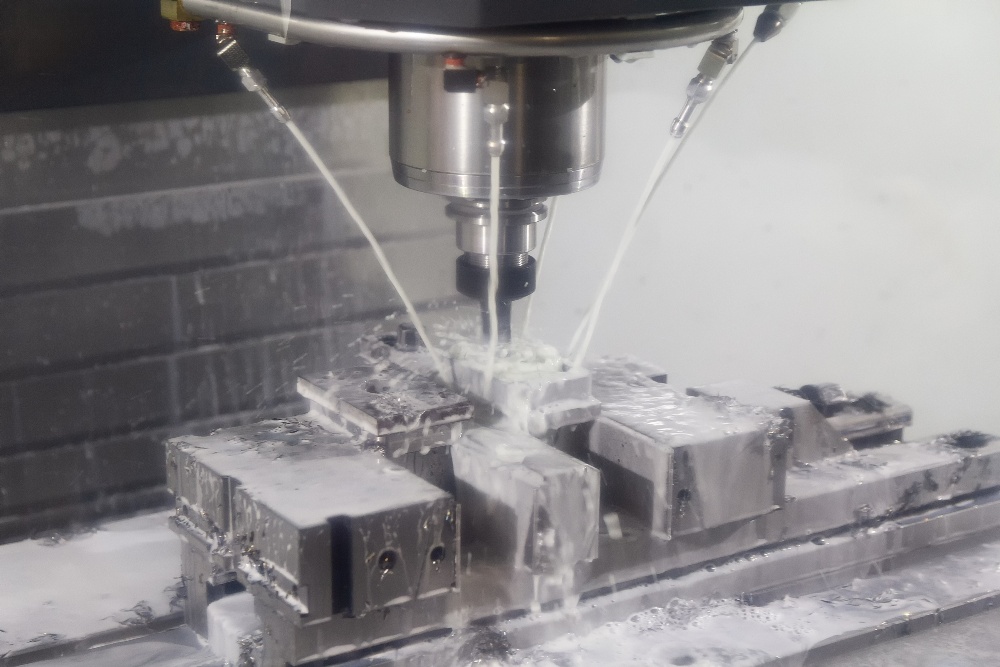
Vielfältige Einsparpotenziale
Zu den größten Vorteilen der MMS zählt der geringe Verbrauch an Schmiermitteln, der sowohl die Anschaffungs- als auch die Entsorgungskosten verringert. Bei der herkömmlichen Nassbearbeitung ist die Reinigung der Werkstücke nach der Fertigstellung unabdingbar. Bei der Minimalmengen-Schmierung kann das Waschen nach dem Bearbeitungsprozess entfallen oder zumindest auf einen Bruchteil reduziert werden. Auch das hilft, Kosten zu sparen. Während durch Öl-Schmierstoffe verunreinigte Späne als Sondermüll gelten, stellen die trockenen Späne moderner MMS-Lösungen ein wertvolles Recyclinggut dar, das anderweitig verarbeitet oder verkauft werden kann – ein wichtiger Beitrag für die Kosten- und Ressourceneffizienz.
Der Wegfall energieintensiver Hochdruckpumpen reduziert den Energieverbrauch und verringert den Wartungsaufwand. Da die Prüfpflichten nach TRGS 611 entfallen, sinken zudem der regulatorische Aufwand und die damit verbundenen Kosten. Die Minimalmengen-Schmierung erfordert spezielle Werkzeuge, die in der Anschaffung zunächst zusätzliche Kosten verursachen. Das wird jedoch durch den geringeren Werkzeugverschleiß und die längere Standzeit ausgeglichen, sodass die Wirtschaftlichkeit auf lange Sicht gewährleistet ist.
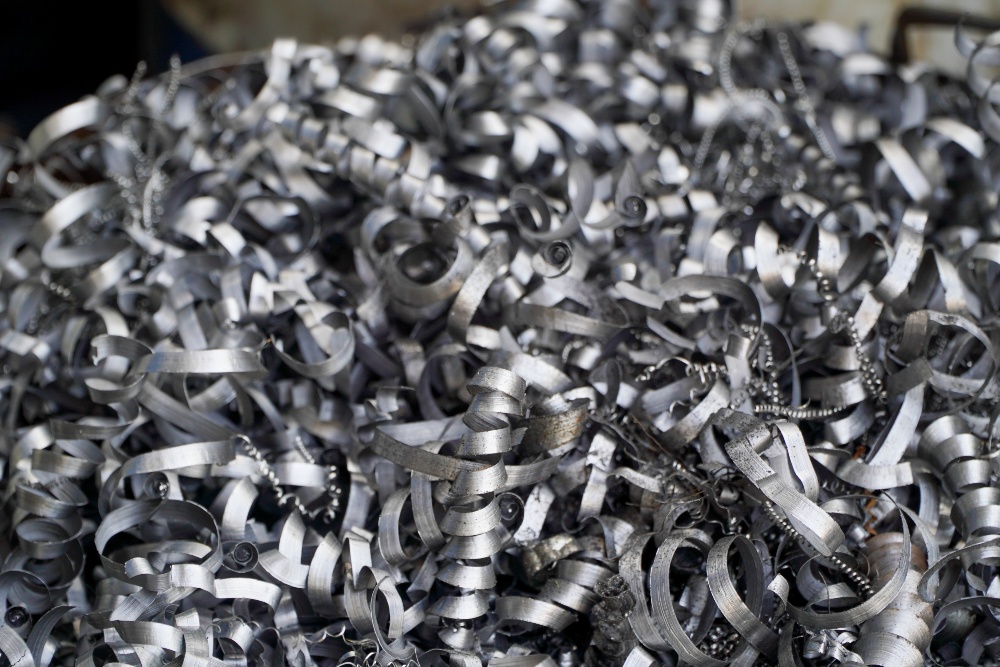
Verbesserung der gesundheitlichen Bedingungen
Bei der MMS wird das Schmiermittel fast vollständig verbraucht und es treten wesentlich weniger Dämpfe aus. Das hilft, Haut- und Augenreizungen zu vermeiden.
Gewährleistung sicherer Arbeitsbedingungen
Da weniger Schmiermittel austreten, sinkt das Rutschrisiko und damit auch die Gefahr von Arbeitsunfällen. Das wirkt sich positiv auf die Arbeitssicherheit aus.
Vorteile für den Umweltschutz
Zum einen sind keine Biozide erforderlich. Zum anderen werden weniger umweltschädliche Emissionen ausgestoßen. Zusätzlich verringert sich die Gefahr von Havarien. Auch der sinkende Energieverbrauch trägt zum Schutz der Umwelt bei.
Minimalmengen-Schmierstoffe im Überblick
Kühlschmierstoffe für die Minimalmengen-Schmierung sollten ein gutes Schmiervermögen, hohe thermische Belastbarkeit sowie ein niedriges toxikologisches und dermatologisches Gefährdungspotenzial mitbringen. In der Praxis bewährt haben sich vor allem synthetische Esteröle und Fettalkohole, die zusätzlich ein günstiges Verdampfungsverhalten aufweisen. Wassermischbare Kühlschmiermittel und Schmierstoffe mit zink- oder chlorhaltigen Additiven eignen sich ebenso wenig wie native Ester mit Neigung zum Verharzen (z. B. Rapsöl) und Erzeugnisse auf Basis mineralischer Grundöle mit mehr als 3 ppm Benzo[a]pyren im Schmierstoff.
Kluthe-Lösungen für nachhaltige Zerspanungsprozesse
Das Kühlschmiermittel-Portfolio der Kluthe GmbH erstreckt sich von wasserlöslichen über wassermischbare bis hin zu nicht-wassermischbaren Produkten. Optimal auf die Anforderungen in der Metallverarbeitung abgestimmt, ermöglichen alle KSS eine sichere Kühlung und eine verlässliche Schmierung. Dabei ist die Prozesseffizienz ebenso gewährleistet wie die Umweltfreundlichkeit.
HAKUFORM A und HAKUFORM SE
Diese Kühlschmierstoffe bieten sich überall dort an, wo eine Zerspanung mit hohen Schnittgeschwindigkeiten und starker Wärmeentwicklung einhergeht. Die Grundlage für diese Schmierstoffe bilden Basisöle, die durch Beigabe von Emulgatoren wassermischbar werden. Im praktischen Einsatz überzeugen HAKUFORM A und HAKUFORM SE durch ausgeprägten Korrosionsschutzeigenschaften und ihre besondere Bio- und pH-Stabilität. Die nachhaltigere HAKUFORM-Variante SE punktet außerdem mit guter Haut- und Umweltverträglichkeit, die sie ihren aromatenfreien Basisölen verdankt.
HAKUFORM L und HAKUFORM S
Erfordern hohe Schneidbelastungen eine deutliche Reduzierung der Reibung, sind die nicht-wassermischbaren Kühlschmiermittel HAKUFORM S und HAKUFORM L ideal. Die S-Serie vereint höchste Zerspanungsleistungen mit Nachhaltigkeit und Ressourceneffizienz. In einem innovativen Verfahren aus Gebrauchtöl hergestellt, ermöglichen sie 75 Prozent CO2-Äquivalent-Einsparungen gegenüber KSS aus konventionellen Mineralölen.
Die Basisöle der L-Reihe werden aus Erdgas gewonnen. Sie sind außergewöhnlich vernebelungs- und verdampfungsarm, was der Arbeitssicherheit zugutekommt. Gleichzeitig sinkt der Verbrauch um bis zu 30 Prozent.