Konversionsverfahren nutzen die Reaktionsfreudigkeit von Metallen für den Korrosionsschutz aus. Sich selbst überlassen, zerstören Feuchtigkeit und Sauerstoff aus der Luft langsam die meisten metallischen Werkstoffe. Unter exakt definierten Bedingungen bilden sich durch die gleichen Reaktionsmechanismen dichte Schutzschichten. Auf diese Weise wehrt man sich gegen die Korrosion durch gezieltes Korrodieren.
Typen von Konversionsverfahren
Konversionsverfahren unterscheiden sich von Verfahren zum Lackieren oder zur Erzeugung galvanischer Überzüge dadurch, dass das Grundmaterial an der Schichtbildung beteiligt ist. Einzelne Atome, genauer gesagt Ionen, werden aus der Oberfläche herausgelöst und verbinden sich chemisch mit den Reaktionspartnern. Für den Korrosionsschutz sind nur Schichten geeignet, die eine gleichmäßige und dichte Struktur haben. Wird eine solche Schicht lokal zerstört, tritt an dieser Stelle verstärkt Korrosion auf.
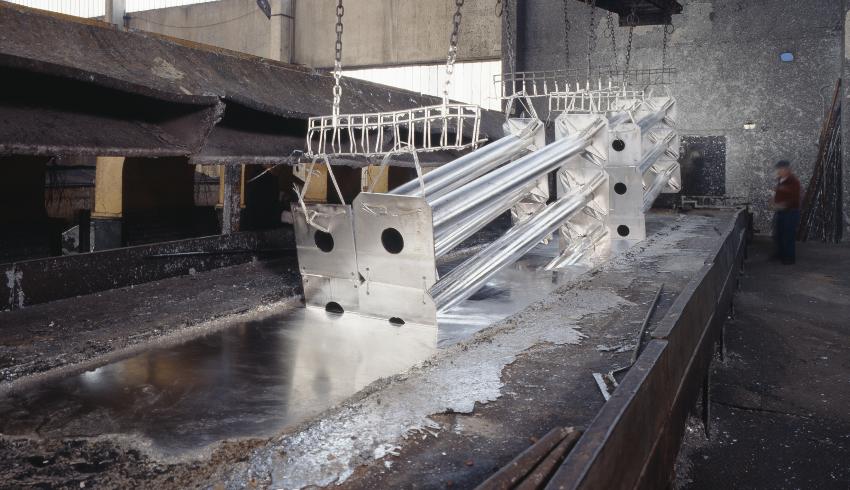
Erzeugung von Oxidschichten
Die meisten unedlen Metalle bilden von selbst eine natürliche Oxidschicht an der Oberfläche, die das darunterliegende Material vor weiteren Angriffen schützt. Dazu gehören Zink, Aluminium und Kupfer. Konversionsverfahren für diese Stoffe zielen darauf ab, die Schicht dichter und gleichmäßiger zu gestalten. Die eingesetzten Reagenzien bewirken eine chemische Reaktion zwischen Metallionen und Sauerstoff. Beispiele für diese Verfahren sind Brünieren und Eloxieren.
Erzeugung von schwerlöslichen komplexen Salzen
Die Rostschicht, die sich auf natürlichem Weg bei eisenhaltigen Werkstoffen wie Gusseisen und Stahl bildet, ist in der Regel locker und porös. Deshalb frisst sich die Korrosion immer weiter in das Grundmaterial hinein. Um sie zu stoppen, werden Konversionsschichten erzeugt, die aus Ionen des Grundmaterials und der Behandlungslösung zusammengesetzt sind. Beispiele für diese Verfahren sind die Phosphatierung und die Chromatierung.
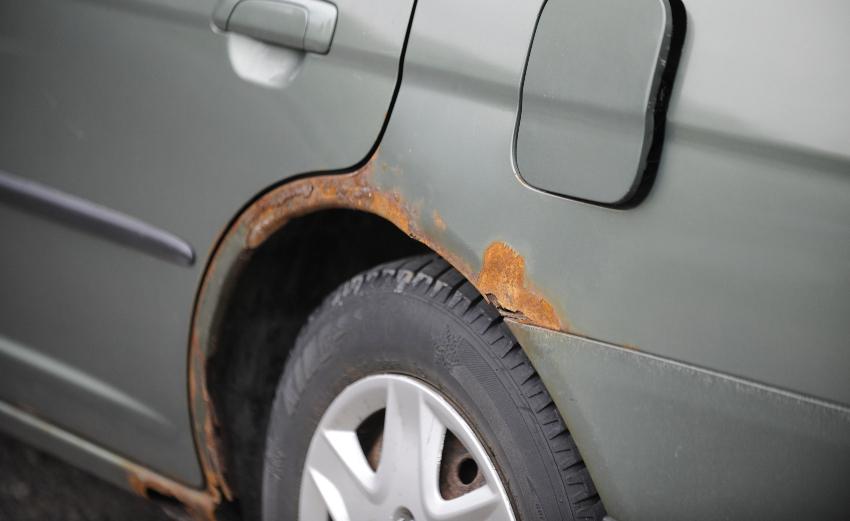
Allgemeine Vorgehensweise
Reinigung und Entfettung
Die Oberflächenbehandlung beginnt stets mit der Reinigung der Werkstoffe. Verschmutzungen, Zunder, Fette und Öle würden sich an den chemischen Reaktionen beteiligen oder diese lokal verhindern. Feste Verunreinigungen werden durch Strahlen oder Schleifen beseitigt. Für die Auflösung von Fetten und Ölen kommen meist alkalische Reinigungsmittel zum Einsatz. Die Wäsche erfolgt durch Tauchverfahren in Bädern oder durch Abspritzen der Oberflächen.
Spülen
Um die nachfolgenden Prozessschritte störungsfrei durchzuführen, müssen die Reinigungslösungen vollständig von den Oberflächen entfernt werden. Das geschieht in mehreren Stufen. Den Abschluss bildet das Spülen mit vollentsalztem Wasser.
Beizen
Beim Beizen werden die natürlichen Oxidschichten durch Säuren oder Laugen aufgelöst. Die Oberflächen sind danach metallisch rein, sodass eine gezielte Schichtbildung möglich ist. Diese Vorbereitung der Oberflächen wird auch als Aktivierung bezeichnet. Die Metallionen werden in einen reaktionsfreudigen Zustand versetzt. Im Anschluss müssen die Beizmittel gründlich entfernt werden. Bei Laugen ist dazu meist die Neutralisation mit einer Säure erforderlich. Mehrstufige Spülprozesse beseitigen die Reste der Behandlungslösung.
Erzeugung der Konversionsschicht
In Bädern oder in Spritzkabinen laufen die chemischen Reaktionen ab, die zur Bildung der vorgesehenen Konversionsschicht führen. Das Ergebnis hängt stark von den Bedingungen ab, unter denen die Stoffe miteinander reagieren. Entscheidend sind die Prozessparameter Temperatur, Konzentration und Verweilzeit. Die Konzentration der Einsatzstoffe bestimmt die Zusammensetzung der Konversionsschicht, die Temperatur wirkt sich auf die Reaktionsgeschwindigkeit aus und die Verweilzeit ist für die Schichtdicke verantwortlich. Bei der elektrolytischen Oxidation, die vorwiegend für die Erzeugung von Konversionsschichten auf Aluminium genutzt wird, ist zusätzlich die optimale elektrische Stromstärke einzuhalten.
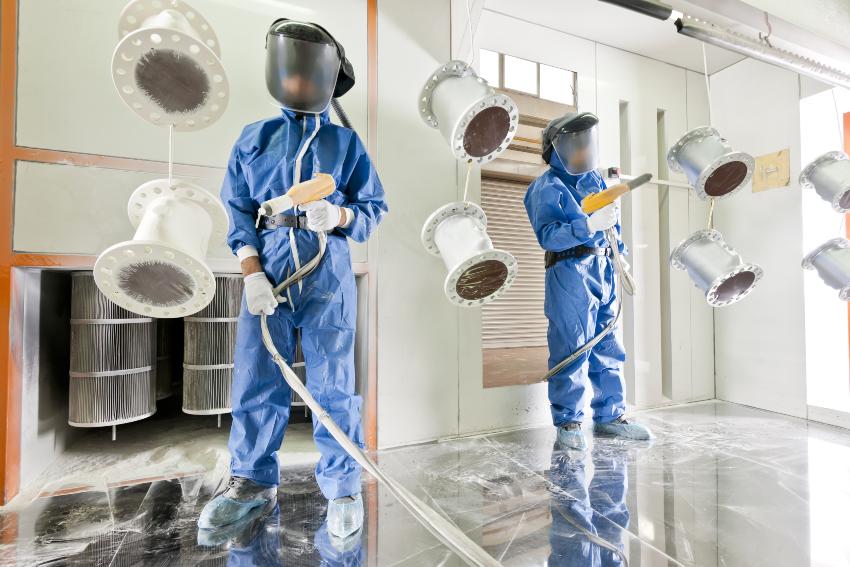
Die entstandenen Konversionsschichten bestehen aus stabilen Stoffen, die unter normalen Umgebungsbedingungen kein Bestreben zu irgendwelchen chemischen Reaktionen haben. Das drückt sich im Begriff Passivierung aus, unter dem die Konversionsverfahren zusammengefasst werden.
Durch unvermeidliche Nebenreaktionen entstehen Abfallstoffe, die aus dem Prozess ausgeschleust werden müssen. Häufig sammelt sich am Boden der Kabinen oder Tauchbecken Schlamm an, der abgepumpt und entsorgt oder aufbereitet werden muss. Unternehmen wie Kluthe arbeiten intensiv an der Entwicklung von Konversionsverfahren, die wenig Abfallstoffe produzieren und außerdem bei möglichst niedrigen Temperaturen ablaufen. Dadurch werden die Prozesse nachhaltiger.
Nachbehandlung
Ist die Schichtbildung abgeschlossen, werden die Teile gespült und getrocknet. Bei einigen Verfahren wird der Schutz gegen Korrosion durch das Aufbringen von Öl, Fett oder Wachs weiter verbessert. In vielen Fällen dient die Konversionsschicht auch als Untergrund für eine nachfolgende Lackierung oder als Gleitschicht für Umformverfahren.
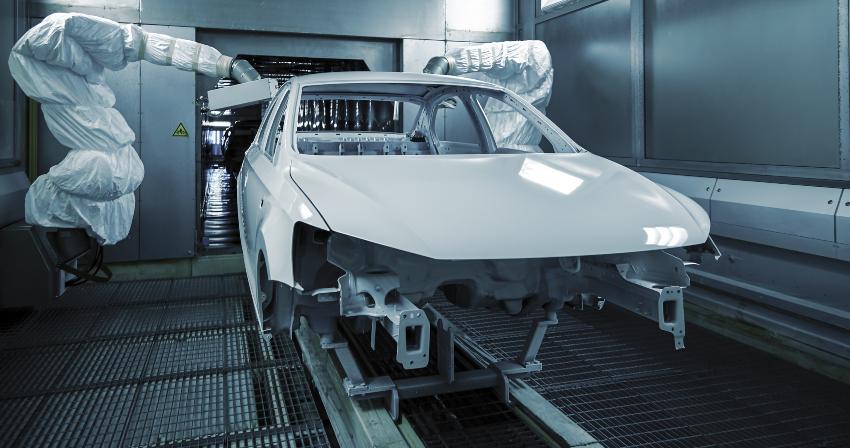
Brünieren
Beim Brünieren werden unter Einwirkung von starken Salzschmelzen, Säuren oder Laugen dünne Oxidschichten erzeugt. Die Schichtdicke beträgt dabei nur etwa 1µm. Dadurch verändern sich die Abmessungen der Teile nur geringfügig, was bei Präzisionsteilen von Bedeutung ist. Da die Schichten verhältnismäßig porös sind, erreicht man mit ihnen nur einen geringen Korrosionsschutz. Öle und Fette dringen allerdings leicht in die Poren ein und wirken korrosionsmindernd.
Die DIN 50 938 “Brünieren von Bauteilen aus Eisenwerkstoffen” beschreibt das Konversionsverfahren und die Qualitätsprüfung der erzeugten Schichten.
Eloxieren
Beim Eloxieren wird die Oxidschicht durch die Dissoziation von Wasser unter dem Einfluss einer elektrischen Spannung genutzt. Wasser zersetzt sich im elektrischen Feld. Der Sauerstoff verbindet sich mit den Aluminium Ionen zu Aluminiumoxid. Die Konversionsschicht ist porös. Dadurch kann sie in das Grundmaterial hineinwachsen und eine Dicke von bis zu 30 µm erreichen.
Unbehandelt sind Eloxalschichten sehr saugfähig. Sie eigenen sich deshalb sehr gut zum Färben und Bedrucken. Vor dem Einsatz als Baustoff erfolgt im Rahmen der Nachbehandlung eine Verdichtung der Poren.
Phosphatierung
Phosphate sind Salze der Phosphorsäure. Für die Oberflächenbehandlung von Eisenwerkstoffen wird in großem Umfang Zinkphosphat eingesetzt. Darüber hinaus sind die Phosphatierung mit Mangan und die Bildung von Eisenphosphat gebräuchlich. Die Schichten erreichen Dicken von über zwei µm.
Beim Einsatz von Titan oder Zirkonium lassen sich besonders dünne Schichten von wenigen Nanometern erzeugen, die den gleichen Schutz gegen Korrosion bieten. Diese Prozesse werden als Dünnschichtverfahren bezeichnet und gehören der Nanotechnologie an. Die Dünnschichtverfahren zeichnen sich durch niedrigen Chemikalienverbrauch, geringes Abfallaufkommen und gute Beständigkeit gegen Korrosion aus.
Die Phosphatierung bildet die Grundlage für Lacke. Sie erleichtert außerdem Umformprozesse. Soll sie als alleiniger Schutz vor Korrosion dienen, werden die Teile nach der Oberflächenbehandlung in der Regel eingeölt.
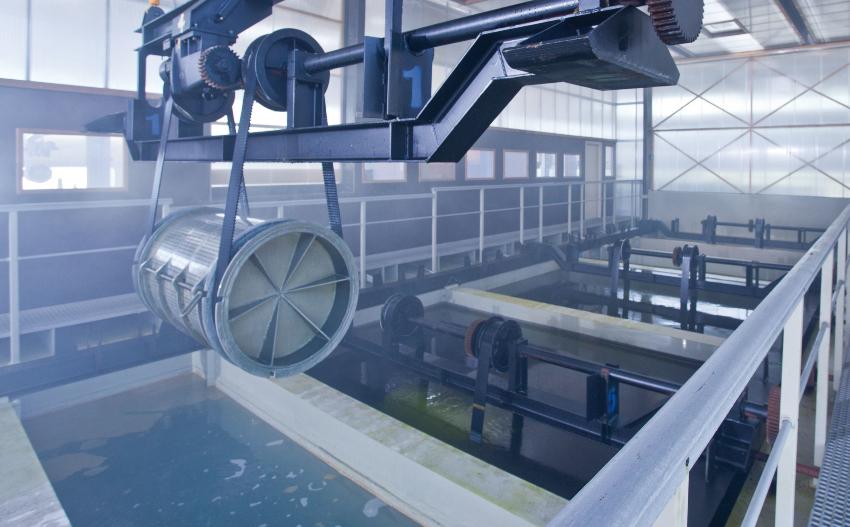
Chromatierung
Die Chromate sind Salze der Chromsäure. Chromionen kommen als dreiwertige und sechswertige Variante vor. Die chemische Wertigkeit von Atomen und Ionen bestimmt, in welchem Verhältnis sich diese zu chemischen Verbindungen zusammenfinden. Daraus leiten sich die Bezeichnungen Chrom III und Chrom VI ab. Die Chrom VI Schichten leisten zwar einen besonders guten Schutz gegen Korrosion, werden aber wegen der starken Vergiftungsgefahr bei der Handhabung der sechswertigen Chromsäure nur in Ausnahmefällen eingesetzt. Dafür werden Chrom VI freie Verfahren weiterentwickelt und verbessert.
Die Chromatierung eignet sich vor allem für Aluminium- und Zinkwerkstoffe. Häufig wird Sie nach dem Verzinken von Eisenwerkstoffen angewendet. Die Dicke von Chromatschichten liegt zwischen 0,01 und 1,25 µm.