In zahlreichen technischen Anwendungen werden Oberflächen beschichtet, beispielsweise in der Automobilindustrie oder der Luft- und Raumfahrttechnik. Nicht auf allen Ausgangsmaterialien haften die Beschichtungen ohne Weiteres. In vielen Fällen ist vorab eine Oberflächenaktivierung, eine Oberflächenvorbehandlung oder auch eine chemische Vorbehandlung erforderlich, um die Haftung von Lacken und anderen Beschichtungsprodukten sicherzustellen.
Adhäsion als Grundlage für eine stabile Haftung von Beschichtungsmedien
Entscheidend für eine hohe Beschichtungsleistung ist eine möglichst starke Adhäsion. Um eine feste mechanische Verbindung zu schaffen, müssen die Adhäsionskräfte zwischen den Molekülen des Substrats und denen der Beschichtung höher sein als die innerhalb des Beschichtungsmediums wirkenden Kohäsionskräfte.
Der Begriff Adhäsion steht für die Anziehungskraft zwischen Atomen und Molekülen unterschiedlicher Substanzen aufgrund relativ schwacher physikalischer, chemischer oder elektrochemischer Bindungskräfte. Je größer die Kontaktfläche zwischen dem Grundmaterial und Beschichtungsmittel ist, desto stärker ist die Bindung. Vergrößern lässt sich die Kontaktfläche durch das Erhöhen der Oberflächenrauheit, da die mikroskopisch kleinen Erhebungen und Vertiefungen für zusätzliche Verzahnung und damit für eine bessere mechanische Verbindung sorgen. Auf makroskopischer Ebene ähnelt diese Form der Adhäsion einem Klettverschluss, dessen Haftfestigkeit ebenfalls durch eine derartige Verklammerung erzielt wird.
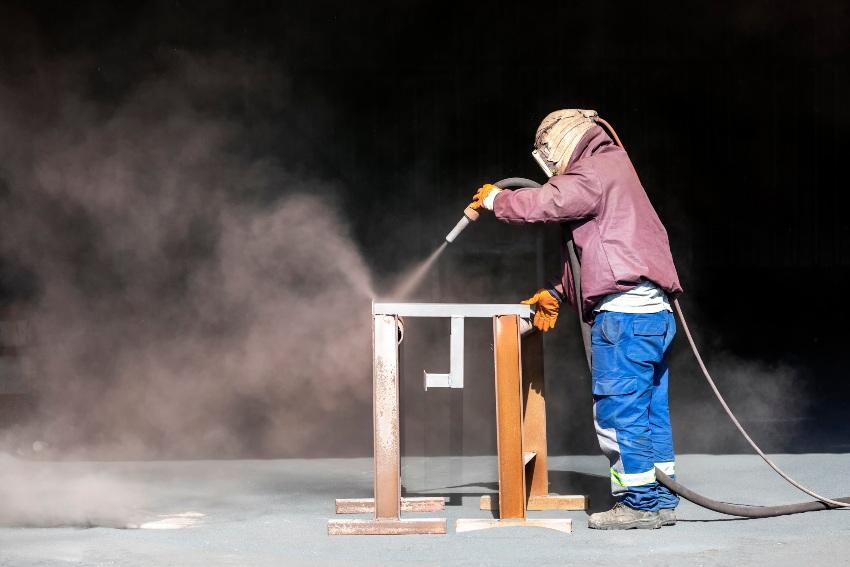
Neben der Adhäsion spielt die Benetzung eine wichtige Rolle für die Beschichtungsleistung. Sie ist abhängig von den Stoffeigenschaften des Beschichtungsmediums und des Grundmaterials. Darüber hinaus hängt es von der vorherrschenden Temperatur ab, ob eine Flüssigkeit in einem dünnen Film auseinanderfließen und in mikroskopische Strukturen eindringen kann, oder ob sie sich in Tropfen zusammenzieht. Daher ist neben einer gezielten Oberflächenaktivierung auch das Einhalten der vorgeschriebenen Verarbeitungstemperaturen entscheidend für die Qualität einer Beschichtung.
Oberflächenaktivierung bei Metallen
Bei Metallen bietet die meist hohe freie Oberflächenenergie eine günstige Voraussetzung für eine stabile Haftung. Dennoch bedarf es für eine gute Beschichtungsleistung einer vorbereitenden Reinigung und zum Teil auch einer Oberflächenvorbehandlung, um eine optimale Bindung zwischen dem Substrat und der Beschichtung zu gewährleisten.
Oberflächenvorbereitung durch Reinigung
Eine Reinigung und Entfettung stellen sicher, dass Staub, Öle, Fette und lockere Schichten aus korrodiertem Material die Benetzung der Oberfläche nicht blockieren. Bewährt haben sich hierfür sowohl wasserbasierende Reinigungsmittel als auch lösemittelbasierende Reinigungsprodukte.
Eine weitere Möglichkeit der Oberflächenreinigung ist das Strahlen. Hierbei wird die zu beschichtende Fläche mithilfe von Druckluft und Strahlmitteln wie Quarzsand, Korund oder Glasperlen von Zunder, Rost und anderen Verunreinigungen befreit. Bei Bedarf kann dabei zugleich die Oberflächenrauheit erhöht werden.
Beizen
Bei dieser Art der Oberflächenaktivierung werden die natürlichen Oxidschichten auf Metallen mithilfe von Laugen oder Säuren aufgelöst. Danach sind die Oberflächen nicht nur metallisch rein, Beizen versetzt die Metallionen darin auch in einen reaktionsfreudigen Zustand. Damit schafft es optimale Voraussetzungen für eine hohe Beschichtungsleistung.
Konversionsverfahren
Auf Metallen werden im Rahmen der Oberflächenaktivierung Konversionsschichten erzeugt, die neben der Beschichtungsleistung auch den Korrosionsschutz und den Verschleißschutz verbessern können. Alkalische und saure Prozessflüssigkeiten gehen mit dem Grundmaterial eine chemische Verbindung ein, die zu einer guten Haftung beiträgt.
Drei der bekanntesten Konversionsverfahren sind die Zinkphosphatierung, die Eisenphosphatierung und die Manganphosphatierung. Erstere wird vor allem im Automobilbereich häufig mit der kathodischen Tauchlackierung kombiniert. Sie ermöglicht optimale Haftfestigkeitsergebnisse bei organischen Beschichtungen.
Die Eisenphosphatierung kommt oftmals vor einer Pulverbeschichtung zur Anwendung. Zu den wichtigsten Einsatzgebieten zählen der Maschinenbau, die Elektroindustrie und der Landmaschinenbau.
Durch eine Manganphosphatierung lässt sich eine dichte, feinkristalline und fest haftende Trägerschicht für eine Gleitlackbeschichtung schaffen, die sich durch hohen Korrosionsschutz und Verschleißschutz auszeichnet. Damit können unter anderem die Einlaufeigenschaften von sich gegeneinander bewegenden Maschinenbauteilen wie Verzahnungselementen verbessert und der Verschleiß minimiert werden.
Vervollständigt werden die Konversionsverfahren durch die Dünnschicht-Technologie (auch Nano-Technologie), Chrom(III)-haltige Formulierungen sowie chromatfreie Verfahren, die in erster Linie auf Aluminium zur Anwendung kommen.
Oberflächenaktivierung bei Kunststoffen
Viele Kunststoffe, insbesondere Polyolefine, haben eine geringe Oberflächenenergie, wodurch Beschichtungen ohne geeignete Substratvorbehandlung unzureichend haften. Eine Vorbereitung der Grenzflächen ist daher in aller Regel unerlässlich. Zur Anwendung kommen in erster Linie folgende Verfahren:
Beflammen
Die chemische Behandlung durch Beflammen erzeugt an der Bauteiloberfläche verschiedene, mehrheitlich sauerstoffhaltige funktionelle Gruppen, die eine Erhöhung der Oberflächenspannung bewirken und damit die chemische Verbindung mit dem Beschichtungsmedium verbessern.
Plasma-/Coronabehandlung
Diese Verfahren der Substratvorbehandlung bieten den Vorteil, dass sich die Oberflächenenergie erhöhen lässt, ohne gleichzeitig die Eigenschaften des Materials zu drastisch zu verändern.
Bei der Plasmabehandlung reagieren Plasmapartikel mit der Kunststoffoberfläche, wodurch die Oberflächenmoleküle aufgeladen werden. Dadurch erhöht sich ihre Mobilität und aus der nicht-polaren Oberfläche wird eine semipolare mit besserer Benetzbarkeit. Bei der Coronabehandlung wird dieser Effekt erzielt, indem eine elektrische Hochspannungsentladung auf die Kunststoffoberfläche einwirkt.
Mittlerweile kommt die Plasmatechnologie immer häufiger auch bei Metallen zur Anwendung, beispielsweise in der Automobilindustrie, der Luft- und Raumfahrttechnik, der Elektroindustrie und in der Medizintechnik.
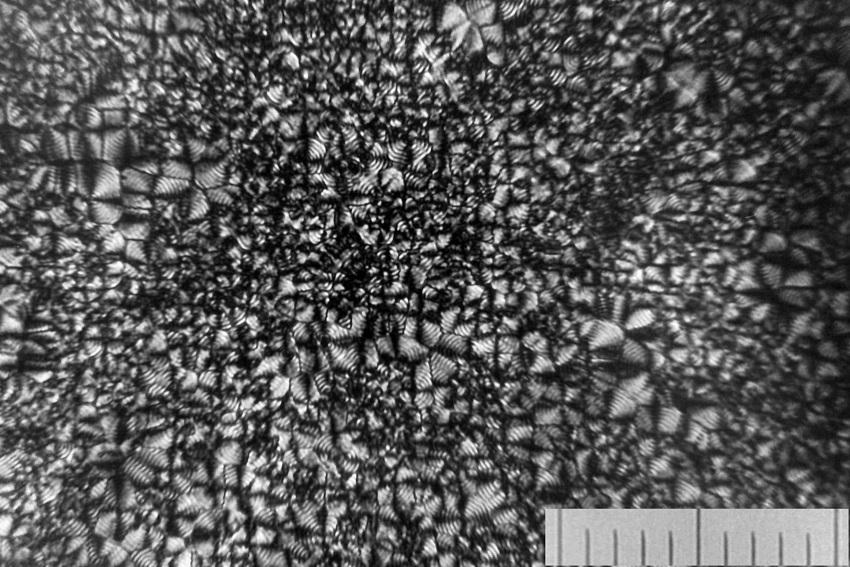
Fluorierung
Bei dieser Methode wird der Kunststoff einem Fluorgemisch ausgesetzt. Das Fluor reagiert mit den Wasserstoffatomen aus der Polymerkette und erhöht auf diese Weise die Polarität der Oberfläche und damit zugleich die Oberflächenspannung.
Enge Abstimmung von Oberflächenaktivierung und Beschichtung gewährleistet optimale Haftung
Grundsätzlich ist es wichtig, die Oberflächenvorbereitung und die anschließende Beschichtung aufeinander abzustimmen. Neben einer gezielten Oberflächenaktivierung tragen auch im Beschichtungsmaterial enthaltene Bindemittel (z. B. Öle, Harze, Kunstharze, Polyurethane) und die Trocknungsbedingungen zur optimalen Haftung bei. Letztlich muss das Gesamtpaket stimmen, um die bestmögliche Verbindung zwischen Beschichtung und Substrat zu gewährleisten.