Die Verdampfung von Flüssigkeitsgemischen wird in der Chemie häufig zur Stofftrennung eingesetzt. Das an vielen unterschiedlich zusammengesetzten Mischungen erprobte Verfahren eignet sich auch für die Lösemittelaufbereitung. Organische Lösemittel, die beispielsweise in der Oberflächentechnik zur Reinigung von Werkstücken oder als Bestandteil von Beschichtungsstoffen genutzt werden, lassen sich auf diese Weise in den Stoffkreislauf zurückführen. Lesen Sie hier, welche Vorteile Dünnschichtverdampfer beim Recycling von Lösemitteln bieten.
Aufbau und Funktionsweise von Dünnschichtverdampfern
Dünnschichtverdampfer bestehen aus einem meist senkrecht angeordneten Rohr, das über einen Heizmantel von außen mit Wärme versorgt wird. Im Inneren dreht sich ein Gestell, an dem Abstreifer angeordnet sind. Die feststehenden oder beweglichen Abstreifer (z.B. Wischerblätter, Rollen) laufen dicht an der Rohrwandung entlang. Über ein Einlaufsystem gelangt die zu verdampfende Flüssigkeit von oben in das Rohr. Die Abstreifer verteilen und durchmischen die Flüssigkeit so, dass ein gleichmäßiger dünner Film an der Wand herabfließt. Die Filmstärke liegt in den meisten Fällen unter einem Millimeter. Die Wärme geht vom Medium im Heizmantel durch die Rohrwand direkt auf den Film über und bringt die Flüssigkeit zum Sieden. Dadurch entstehende Dämpfe steigen nach oben und verlassen den Dünnschichtverdampfer durch einen Stutzen, an den sich ein Kondensator oder andere Apparate zur Weiterverarbeitung anschließen. Die restliche Flüssigkeit, in besonderen Fällen auch zurückbleibender Feststoff, läuft am unteren Ende des Verdampfers in einen Auffangbehälter.
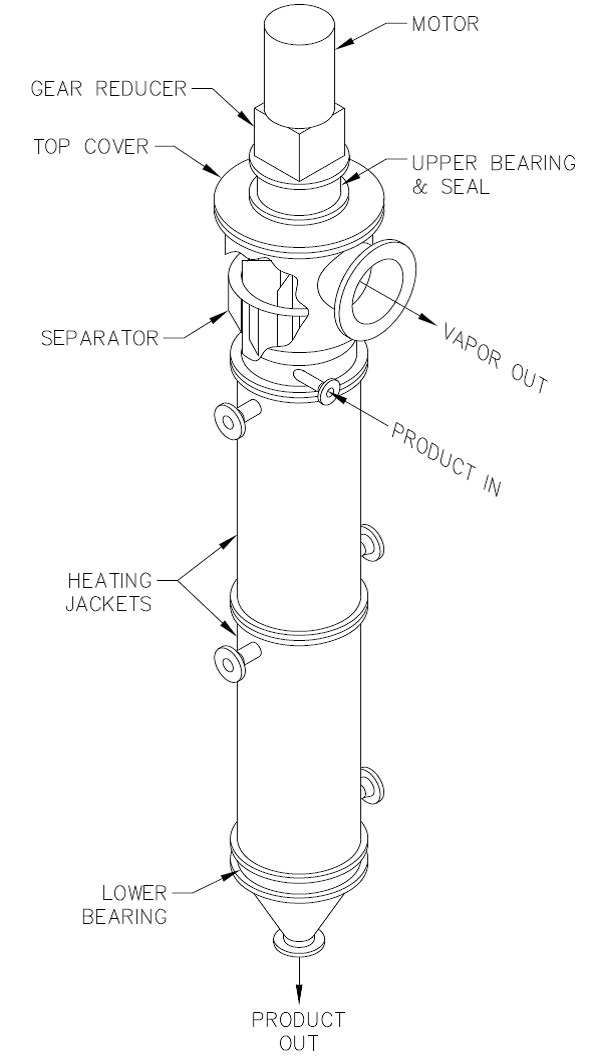
Wärmeversorgung
Die Teilchen (Atome, Ionen, Moleküle), aus denen sich alle Stoffe zusammensetzen, sind in ständiger Bewegung. Die Bewegungsenergie tritt als Wärme in Erscheinung. Solange der Aggregatzustand (bei festen Stoffen das Gefüge) gleich bleibt, gibt die Temperatur darüber Auskunft, wieviel Wärme ein Stoff enthält. Berühren sich Teilchen, gleichen sich Unterschiede der Temperatur dadurch aus, dass schnelle Teilchen langsamere anstoßen und beschleunigen, wobei die schnellen gebremst werden. So gelangt die Wärme vom Medium im Heizmantel durch die Rohrwand in den Flüssigkeitsfilm. Als Energielieferant für den Dünnschichtverdampfer eignet sich kondensierender Wasserdampf. Die Temperatur, bei der der Dampf den Aggregatzustand ändert, hängt nur vom vorherrschenden Druck ab. Dadurch lässt sich ein optimaler Temperaturunterschied zum Flüssigkeitsfilm einstellen. Alternativ können erwärmte Thermoöle oder Heißwasser eingesetzt werden.
Einstellung der Betriebsbedingungen
In Flüssigkeiten macht sich die Teilchenbewegung durch den Dampfdruck bemerkbar. Soll eine Flüssigkeit verdampfen, müssen ihr Dampfdruck und der Druck, der in ihrer Umgebung herrscht, gleichgroß sein. Das lässt sich durch Steigerung der Temperatur oder durch Verringerung des Drucks erreichen. Dünnschichtverdampfer arbeiten in den meisten Fällen bei Unterdruck. Dadurch erfolgt das Verdampfen bei Temperaturen, die deutlich unterhalb der Siedetemperaturen bei normalem Luftdruck liegen. Die genaue Steuerung des Betriebsdrucks, der Durchlaufmenge und der Drehzahl des Abstreifsystems lassen eine schonende Verdampfung bei einer geringen Verweilzeit zu. Für die Lösemittelaufbereitung bedeutet das, dass sich nicht nur die Lösemittel zurückgewinnen lassen. In vielen Fällen ist es möglich, auch die abgetrennten Inhaltsstoffe zu recyceln.
Verdampfung
Solange der Druck unverändert bleibt, verdampfen reine Flüssigkeiten bei konstanter Temperatur. Flüssige Stoffgemische verhalten sich in Abhängigkeit von ihrer Zusammensetzung recht unterschiedlich. Die Zusammensetzung des Dampfes über einem siedenden Stoffgemisch entspricht den Dampfdrücken der Komponenten. Entscheidenden Einfluss auf das Verdampfungsverhalten hat die Löslichkeit der beteiligten Stoffe untereinander.
Bei idealen vollständig löslichen Flüssigkeitsgemischen ergibt sich der Dampfdruck aus der Summe der Teildampfdrücke ihrer Bestandteile. Der Teildampfdruck (Partialdruck) ist gleich dem Dampfdruck der reinen Komponente bei der herrschenden Temperatur, multipliziert mit ihrem Anteil von Teilchen im Gemisch. Deshalb geht zu Beginn des Prozesses mehr Leichtersiedendes in den gasförmigen Zustand über als Schwerersiedendes. Die Zusammensetzung der Flüssigkeit ändert sich im Verlauf des Prozesses. Dadurch ändern sich auch die Teildampfdrücke, und die Siedetemperatur steigt an.
Um den Anteil von Teilchen im Gemisch zu bestimmen, nutzt die Chemie das Zählmaß “Mol” mit der Maßeinheit mol. Ein Mol enthält so viele Teilchen, wie in 12 g reinem Kohlenstoff enthalten sind. Im Periodensystem finden Sie für jedes Element die Gesamtmasse dieser Anzahl von Atomen (molare Masse, Äquivalentmasse, Maßeinheit g/mol). Bei chemischen Verbindungen werden die molaren Massen der beteiligten Atome addiert.
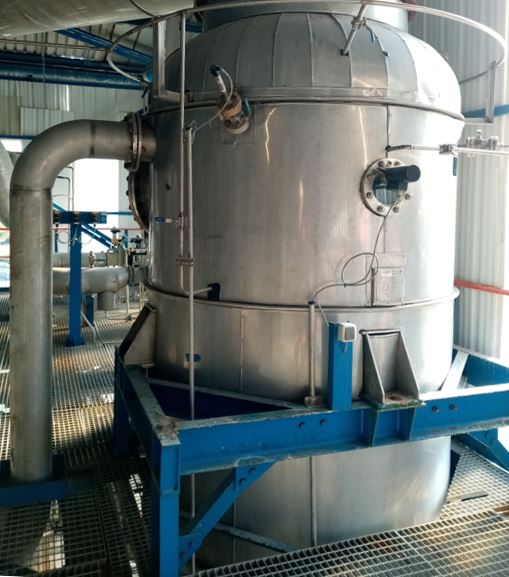
Sind die Bestandteile eines Flüssigkeitsgemisches gar nicht ineinander löslich, behält jede Komponente ihren temperaturabhängigen Dampfdruck unverändert bei. Bei Wärmezufuhr beginnt das “Ideal”-Gemisch zu sieden, wenn die Summe der Dampfdrücke gleich dem Umgebungsdruck ist. Das bedeutet, eine reine Emulsion verdampft bereits bei einer Temperatur unterhalb des niedrigsten Siedepunktes ihrer Komponenten. Die Siedetemperatur bleibt konstant, solange noch Anteile der Komponenten im Gemisch vorhanden sind.
Ideale Bedingungen sind in der Natur selten anzutreffen. Auch die Oberflächentechnik unterliegt den Naturgesetzen. Deshalb wird das Verdampfungsverhalten lösemittelhaltiger Rückstände aus der Oberflächenbehandlung und der Beschichtung experimentell bestimmt. Aus den Versuchsergebnissen lassen sich die optimalen Bedingungen für die Lösemittelaufbereitung im Dünnschichtverdampfer ableiten.
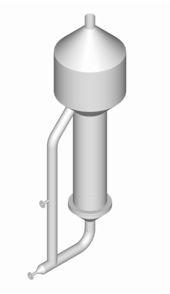
Vorteile der Dünnschichtverdampfung im Überblick
Maximale Verdampfungsraten bei minimalem Energieeinsatz
Der dünne, gut durchmischte Film im Dünnschichtverdampfer bewirkt, dass sich die Wärme im Flüssigkeitsgemisch schnell und gleichmäßig verteilt. Deshalb werden auch nur verhältnismäßig geringe Temperaturdifferenzen zum Heizmedium benötigt. So lassen sich mit einem minimalen Energieeinsatz maximale Verdampfungsraten und hohe Stoffdurchsätze erreichen. Aus der deutlichen Einsparung von Energie im Vergleich zur Herstellung der Lösemittel oder der Rückgewinnung der Stoffe durch andere Techniken ergibt sich eine deutliche Reduzierung des Kohlendioxidausstoßes und damit ein merklicher Beitrag zum Klimaschutz.
Beliebiges Fließverhalten
Eine optimierte Gestaltung der Abstreifer erlaubt, die Fließbewegung zähflüssiger Stoffgemische zu unterstützen. In Kombination mit der guten Steuerbarkeit der Betriebsparameter (Rotationsgeschwindigkeit, Druck, Wärmeversorgung) in weiten Grenzen gelingt im Dünnschichtverdampfer auch die Lösemittelaufbereitung von problematischen Rückständen, die beispielsweise bei der Entlackung von Teilen oder der Reinigung von Lackieranlagen anfallen und zuweilen auch Feststoffe enthalten.
Geringe thermische Belastung
Kurze Verweilzeiten und niedrige Verdampfungstemperaturen führen bei der Dünnschichtverdampfung zu einer sehr geringen thermischen Belastung der im Gemisch enthaltenen Komponenten. Höhere Temperaturen und längere Einwirkzeiten würden bei vielen Stoffen chemische Reaktionen in Gang setzen. Bei der Lösemittelaufbereitung, bei der außer dem Lösemittel auch die anderen Inhaltsstoffe wiederverwendet werden sollen, ist die Vermeidung chemischer Reaktionen sehr wichtig. Durch die Dünnschichtverdampfung ist ein großer Schritt in Richtung Kreislaufwirtschaft möglich.