« Wir erklären den Unterschied »
Passiver und aktiver Korrosionsschutz umfasst alle technischen Maßnahmen, die dazu dienen, Werkstoffe vor der Zerstörung durch Umgebungseinflüsse zu schützen. Der Sauerstoff und die Feuchtigkeit in der Atmosphäre setzen vor allem Eisenwerkstoffen zu, die in allen Bereichen der Industrie und der Infrastruktur zu finden sind. Um die Bauteile und Konstruktionselemente langfristig zu erhalten, sind große Anstrengungen und ein hoher finanzieller Aufwand erforderlich.
Ursachen für Korrosion
In der Natur kommen nur Edelmetalle in reiner Form als chemisches Element vor. Die meisten Metalle, die als Werkstoff für Bauteile zu gebrauchen sind, werden mühsam aus Erzen gewonnen. Dort verstecken sie sich in chemischen Verbindungen. Metallwerkstoffe streben ihren natürlichen Zustand wieder an. Sie gehen mit den Stoffen in ihrer Umgebung chemische Verbindungen ein, sobald sich die Gelegenheit bietet. Das macht sich als Korrosion bemerkbar. Für Vorgänge, die in der Natur freiwillig ablaufen, ist immer ein Unterschied zwischen physikalischen Größen verantwortlich, der durch diese Vorgänge ausgeglichen wird. Das betrifft Druck, Temperatur, Konzentration und elektrische oder mechanische Spannung. Immer ist irgendeine Energie mit im Spiel, die ihr Erscheinungsbild ändert. Und immer fließt etwas. Das ist auch bei der Korrosion der Fall. Will man sie unterbinden, muss man die Bewegung verhindern oder ins Leere laufen lassen. Das lässt sich passiv bewerkstelligen, indem eine Barriere aufgebaut wird, und aktiv, indem man eine Gegenbewegung oder Richtungsänderung veranlasst. Passiver Korrosionsschutz wird durch eine Oberflächenbeschichtung erreicht, die das Metall von seinen Reaktionspartnern trennt. Aktiver Korrosionsschutz mischt sich in die Chemie der Reaktionen ein.
Die Werkstoffwissenschaft unterscheidet zwischen chemischen und elektrochemischen Korrosionsvorgängen. Die chemische Korrosion wird durch heiße, trockene Gase oder Metallschmelzen in Anlagen der Chemieindustrie oder der Metallurgie hervorgerufen. Verhindert wird sie durch den Einsatz von Werkstoffen, die diesem Angriff widerstehen. Weitaus häufiger sind Korrosionserscheinungen, die aus elektrochemischen Reaktionen resultieren.
Elektrochemische Korrosionsvorgänge
Elektrochemische Reaktionen laufen ab, wenn ein Metall von einer elektrisch leitfähigen Flüssigkeit (Elektrolyt) benetzt ist und voneinander verschiedene Metallarten miteinander in Kontakt sind, Konzentrations- oder Temperaturunterschiede in der angreifenden Flüssigkeit bestehen oder in Bereichen eines Metalls unterschiedliche mechanische Spannungen herrschen.
Unter diesen Umständet bildet sich Korrosionselemente aus. Der Begriff lehnt sich an die in Batterien und Akkumulatoren genutzten galvanischen Elemente an. Bestimmte Werkstoffbereiche oder ganze Bauteile werden zur positiv geladenen Anode, an der sich Metall auflöst. Andere Stellen werden zur negativ geladenen Kathode. Dort nimmt die vorhandene Flüssigkeit Elektronen auf. Sind die Abmessungen der Korrosionselemente mikroskopisch klein, werden sie als Lokalelemente bezeichnet. Die Zersetzung des Materials läuft dann im Werkstoffgefüge zwischen den Kristallen der verschiedenen Legierungselemente ab. Aktiver Schutz gegen elektrochemische Korrosionserscheinungen setzt die genaue Kenntnis der Reaktionsmechanismen voraus.
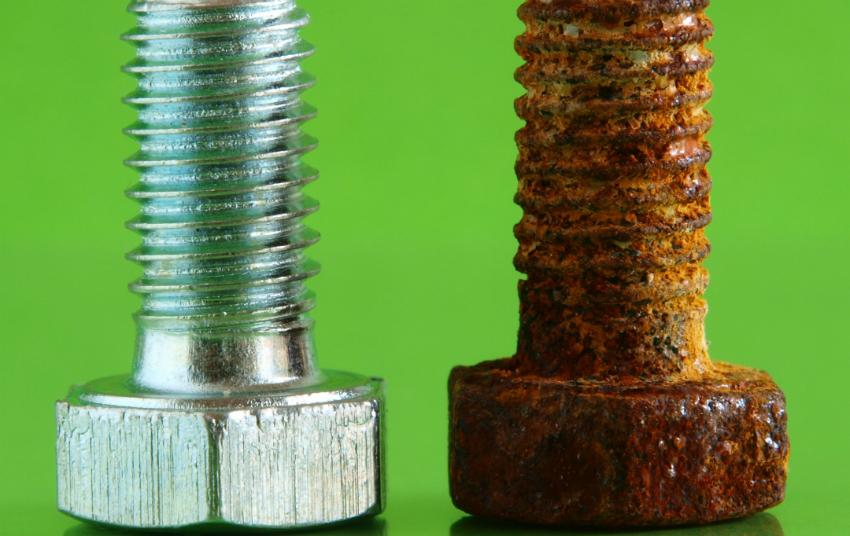
Neben der Feuchtigkeit ist die Anwesenheit von Sauerstoff von Bedeutung. Die meisten Korrosionsprodukte sind Metalloxide. Der Sauerstoff ist in der Atmosphäre stets vorhanden. In Wasser, das in Kontakt mit der Luft steht, löst er sich bis zu einer gewissen Grenze. Außerdem bildet sich bei der Zersetzung von Wasser während der elektrochemischen Reaktion.
Einige Metalle bilden Korrosionsprodukte, die auf der Oberfläche dichte zusammenhängende Schichten bilden. Diese Schichten schützen den Werkstoff vor der weiteren Zersetzung. Am bekanntesten ist die grüne Patina, die auf Kupferdächern weithin sichtbar ist. Ähnliche Schutzschichten entstehen auf Aluminium und Magnesium. Auf Chrom und nichtrostenden Stählen entstehen sehr dünne, mit dem Auge nicht erkennbare Oberflächenschichten, die angreifende Medien fast vollständig blockieren. Rost auf eisenhaltigen Werkstoffen ist in den meisten Fällen locker und porös. Die Rostschichten verstärken Korrosionsvorgänge eher.
Welche Korrosionsarten gibt es?
- Nach dem Erscheinungsbild der Korrosionsprodukte unterscheidet man
- Flächenkorrosion
- interkristalline Korrosion (Kornzerfall)
- transkristalline Korrosion
- Lochfraß
- Spannungsrisskorrosion
Den passiven und aktiven Korrosionsschutz und ihre jeweiligen Verfahren sowie Anwendungen betrachten wir im Folgenden etwas näher.
Passiver Korrosionsschutz
Passiver Korrosionsschutz wird durch Korrosionsschutzmittel erreicht, mit denen die Metalloberflächen beschichtet werden. Langfristig haltbar sind fachgerechte Lackierungen auf einer Konversionsschicht. Konversionsschichten werden durch Phosphatieren, Chromatieren oder Brünieren erzeugt. Dabei reagiert das Material im oberflächennahen Bereich mit dem Behandlungsmittel. Eine abschließende Lackschicht vervollkommnet den Schutz gegen korrosive Medien. Dieses Verfahren wird vor allem in der Metallbearbeitung für Verkleidungen von Maschinen und für Fahrzeugteile eingesetzt.
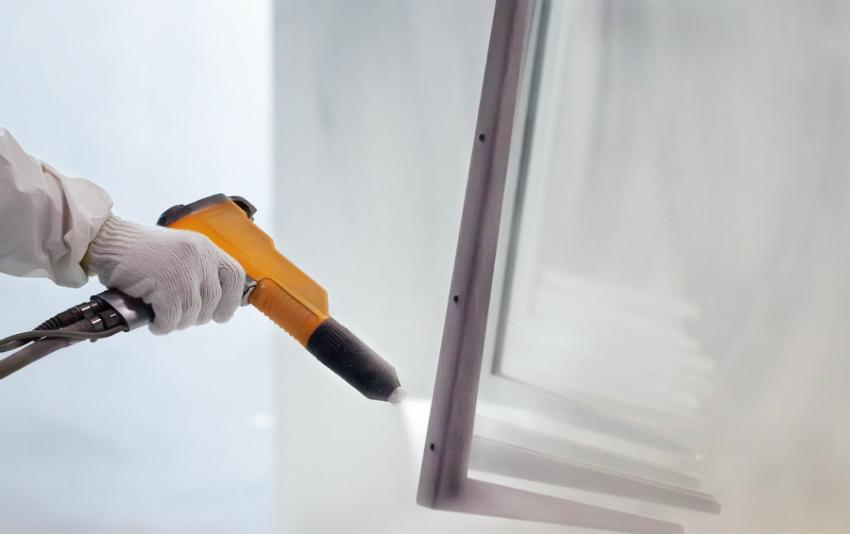
An Stahlbauten wie Brücken oder Masten für Stromleitungen wird die Farbschicht durch Witterungseinflüsse nach und nach abgetragen. Um die Stabilität dieser Bauwerke zu erhalten, sind regelmäßige Kontrollen erforderlich. Ist die Schicht rissig oder blättert die Farbe ab, wird sie vollständig entfernt. Anschließend werden die Oberflächen grundiert und erneut lackiert. Mit speziellen Rostschutzfarben lassen sich die Intervalle zwischen den Korrosionsschutzmaßnahmen verlängern.
Als Alternative zu Farben und Lacken werden vor allem bei Eisenwerkstoffen metallische Überzüge aus Zink oder Chrom für den Korrosionsschutz eingesetzt. In der Metallbearbeitung werden Halbzeuge und angearbeitete Teile mit einem temporär wirkenden Korrosionsschutzmittel behandelt. Dünne Schichten aus Öl, Lack oder Zink, die sich leicht wieder entfernen lassen, verhindern, dass sich vor der Bearbeitung oder in Bearbeitungspausen Rost bildet. Das ist besonders im Winter sinnvoll, wenn Metallteile in der Kälte gelagert oder transportiert und dann in einer beheizten Werkhalle abgestellt werden. Die Luftfeuchtigkeit schlägt sich auf den Oberflächen nieder und bewirkt innerhalb weniger Minuten, dass ungeschützte Teile anrosten.
Aktiver Korrosionsschutz
Aktiver Schutz vor Korrosion wird hauptsächlich für Werkstoffe eingesetzt, die während ihrer Nutzung schwer zugänglich sind und sich dadurch der regelmäßigen Oberflächenbeschichtung entziehen. Das betrifft zum Beispiel erdverlegte Kabel und Rohrleitungen, Wasserbauwerke, Kessel in Kraftwerken, Lagerbehälter in der Chemie und die Außenhaut von Schiffen. Aktiver Schutz gegen korrosive Vorgänge erfolgt auf der Grundlage des kathodischen oder des anodischen Korrosionsschutzes und durch die Beeinflussung des Werkstoffs oder des korrodierend wirkenden Mediums.
Kathodisches Verfahren
Beim kathodischen Verfahren wird der elektrische Strom durch einen gleichgroßen Strom kompensiert, der in entgegengesetzter Richtung fließt. Das geschieht durch eine äußere Gleichspannungsquelle oder mittels Opferanoden aus unedlem Metall. Die Opferanode oder auch Schutzanode wird mit dem Werkstoff kurzgeschlossen und löst sich statt diesem auf.
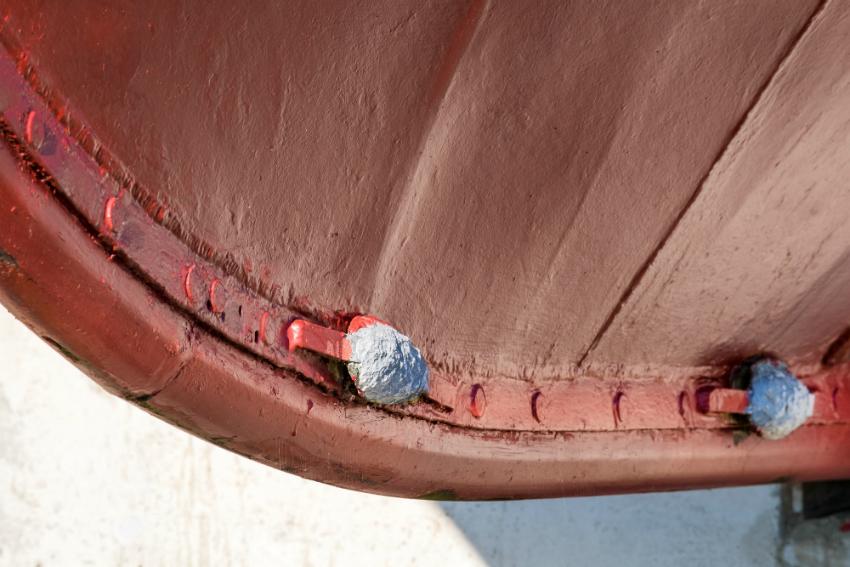
Anodisches Verfahren
Anodische Korrosionsschutzverfahren nutzen die Bildung einer dünnen Schutzschicht aus Korrosionsprodukten auf der Oberfläche des Materials aus, die den weiteren Angriff verhindert. Der metallische Gegenstand wird dabei durch Polarisation passiviert. Das Verfahren setzt voraus, dass die Metalle entsprechende Oxidationsprodukte hervorbringen.
Aktiver Schutz gegen Korrosion besteht auch darin, durch eine Wärmebehandlung Spannungsunterschiede im Material abzubauen, die aus der Metallbearbeitung resultieren. Zu diesen Maßnahmen gehören das Spannungsarmglühen und das Normalglühen. Neben dem Ausgleich von Spannungen wirken sich diese Arbeiten positiv auf das Werkstoffgefüge aus.
Einsatz von Inhibitoren
In Kühlwasserkreisläufen und in Kesselspeisewasseranlagen werden Inhibitoren eingesetzt, die die chemischen Reaktionen zwischen Wasser und Behälter- oder Rohrwänden stören. Dabei kommt zum Beispiel eine verdünnte Hydrazin-Lösung zum Einsatz. Dieses Mittel ist eine Verbindung aus Wasserstoff und Stickstoff, die den Sauerstoff aus dem Wasser entfernt und den pH-Wert anhebt. Alkalische Lösungen greifen eisenhaltige Werkstoffe weniger stark an. Das Hydrazin reagiert mit dem Sauerstoff zu Wasser und Stickstoff.