« Das Verfahren in der Kurzbeschreibung »
Durch das Eloxal-Verfahren erhalten Halbzeuge oder Werkstücke aus Aluminium eine korrosions- und verschleißbeständige Oberfläche. Die entstehende Schutzschicht baut sich mit Unterstützung durch elektrischen Strom auf und enthält Bestandteile des Grundwerkstoffs. Das Metall wandelt sich im oberflächennahen Bereich zu Aluminiumoxid um. Aus diesem Zusammenhang ergibt sich die Kurzbezeichnung Eloxal, die sich aus den Anfangsbuchstaben der Worte elektrisch, Oxidation und Aluminium zusammensetzt.
Warum Aluminium eloxieren?
Aluminium und seine Legierungen gehören zu den wichtigsten Konstruktionswerkstoffen. Die gute Festigkeit und vor allem das geringe Gewicht sind ausschlaggebend für den Einsatz dieses Metalls beim Bau von Fahrzeugen, Flugzeugen, Haushaltsgegenständen oder im Bauwesen. Auf der Oberfläche von Aluminiumteilen bildet sich an der Luft schnell eine sehr dünne Oxidschicht, die den Werkstoff vor Korrosion schützt.
Diese Schicht ist allerdings anfällig gegen mechanischen Verschleiß und verschiedene chemische Stoffe. Durch das Eloxal-Verfahren, manchmal auch als Eloxal-Methode bezeichnet, entsteht eine künstliche Oxidschicht, die einen besseren Verschleiß- und Korrosionsschutz bietet.
Wie läuft das Eloxal-Verfahren ab?
Wie in der Oberflächentechnik üblich, besteht auch das Eloxal-Verfahren aus mehreren Schritten. Die Durchführung hängt von den angestrebten optischen, chemischen und physikalischen Schichteigenschaften ab. Sollen die Werkstoffoberflächen besonders glatt werden, gehen dem Eloxieren entsprechende Arbeitsschritte wir Schleifen oder Polieren voraus.
Vorbehandlung der Oberflächen
Voraussetzung für eine ordnungsgemäße Schichtbildung ist, dass die Oberflächen sauber und frei von Fetten und Ölen sind. Auch die natürliche Oxidschicht muss vor dem eigentlichen Verfahren entfern werden. Die Oberflächenvorbehandlung umfasst die Verfahrensschritte Entfetten, Beizen und Dekapieren. Das Entfetten erfolgt mit heißem Wasserdampf, Heißwasser und ggf. alkalischen Reinigungsmitteln. Beim Beizen zersetzen Laugen die natürliche Oxidschicht.
Da die alkalischen Rückstände der Beize die Schichtbildung stören würden, müssen sie neutralisiert und abgespült werden. Dieser Vorgang wird als Dekapieren bezeichnet. Das gründliche Spülen mit vollentsalzten Wasser nach jedem Arbeitsschritt sorgt für einen qualitätsgerechten Ablauf des Verfahrens.
Eloxieren durch anodische Oxidation
Um Aluminium zu eloxieren, wird es fest an den Pluspol einer Gleichspannungsquelle angeschlossen und in einen Säurebad getaucht. Die Behälterwand oder ein im Bad befindliches, säurebeständiges Bauteil werden mit dem Minuspol der Spannungsquelle verbunden. Beim Freischalten der Spannung wird das Aluminiumteil bzw. -halbzeug zur Anode. An der Oberfläche der Anode verbindet sich der Werkstoff mit Sauerstoff zu Aluminiumoxid.
Auf diese Weise baut sich die Schutzschicht auf. Die Behälterwand bzw. das mit dem Minuspol der Spannungsquelle verbundene Bauteil werden zur Kathode. Dort entsteht gasförmiger Wasserstoff.
Prozessparameter bei der Eloxal-Methode
Das Eloxal-Verfahren läuft bei Temperaturen von 15 bis 20 °C ab. Die angelegte Spannung liegt zwischen 14 und 20 V. Im Bad stellt sich eine Stromdichte von 1,5 A/dm² ein, bei der die Schichtdicke um bis zu 3 µm/min anwächst. In Abhängigkeit von der Einwirkzeit werden 10 bis 25 µm starke Schutzschichten erzeugt. Ein Sonderfall ist das Harteloxieren. Bei diesem Verfahren entsteht ein äußerst verschleißfester Korrosionsschutz mit 25 bis 250 µm starken Schichten. Diese Schichtdicken lassen sich bei Temperaturen unter 10 °C mit einer elektrischen Spannung über 40 V und Stromdichten von 2 bis 3 A/dm² erreichen.
Nachbehandlung durch Färben und Verdichten der Schicht
Die Schutzschicht hat eine poröse Struktur. Durch die Poren könnten Feuchtigkeit und aggressive Stoffe an den Grundwerkstoff gelangen und Korrosionsschäden verursachen. Deshalb muss die Schutzschicht in einem abschließenden Arbeitsschritt verdichtet werden. Die Poren können allerdings auch Farbe aufnehmen. Soll die Oberfläche zu dekorativen Zwecken eingefärbt werden, bietet sich die poröse Schicht zur Einfärbung an. Das geschieht unmittelbar im Anschluss an das Eloxieren in der Regel durch Tauchen in ein Farbbad oder elektrolytisch.
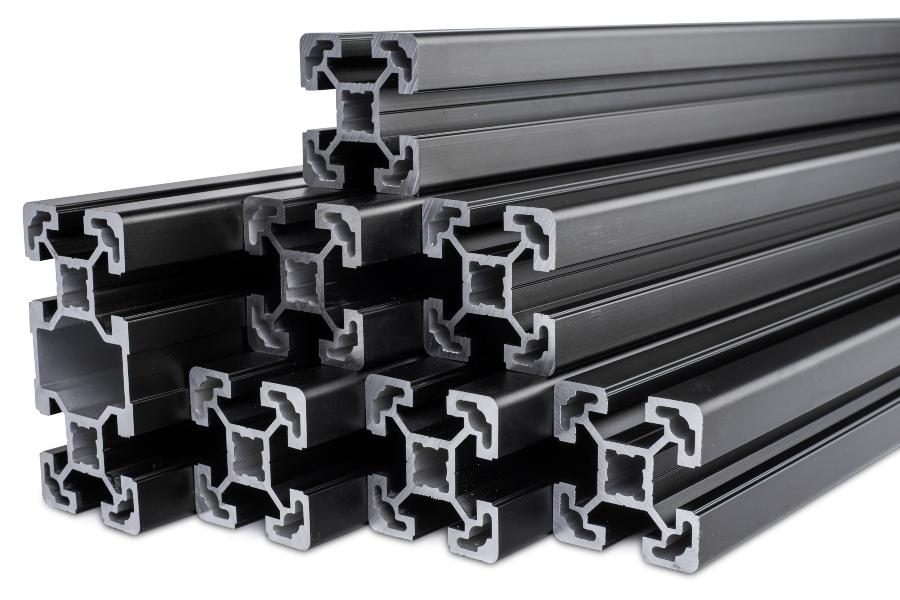
Die Eloxal-Methode schließt mit dem Verdichtungsprozess ab. Dabei wird das eloxierte Metall in vollentsalztem Wasser gekocht oder mit Heißdampf behandelt. Bei Temperaturen von 90 bis 100 °C wandelt sich das Aluminiumoxid in den Poren mit Wasser in Aluminium-oxid-hydroxid um. Dieser Stoff verengt und verschließt die Poren. Er kommt in der Natur als Mineral vor. Dort ist er unter der Bezeichnung Böhmit bekannt.
Was passiert bei der anodischen Oxidation an der Werkstoffoberfläche?
Die Oxidation ist ein chemischer Prozess, bei dem Elektronen aus der Atomhülle freigesetzt werden. Der entgegengesetzte Vorgang ist die Reduktion. Hierbei werden Elektronen in die Atomhülle aufgenommen. Das Eloxal-Verfahren beruht darauf, dass Wasser unter Einwirkung elektrischer Gleichspannung in negativ geladene Hydroxidionen (Sauerstoff und Wasserstoff, OH-) und positiv geladene Hydroniumionen (Wasser und Wasserstoff, H3O+) zerfällt.
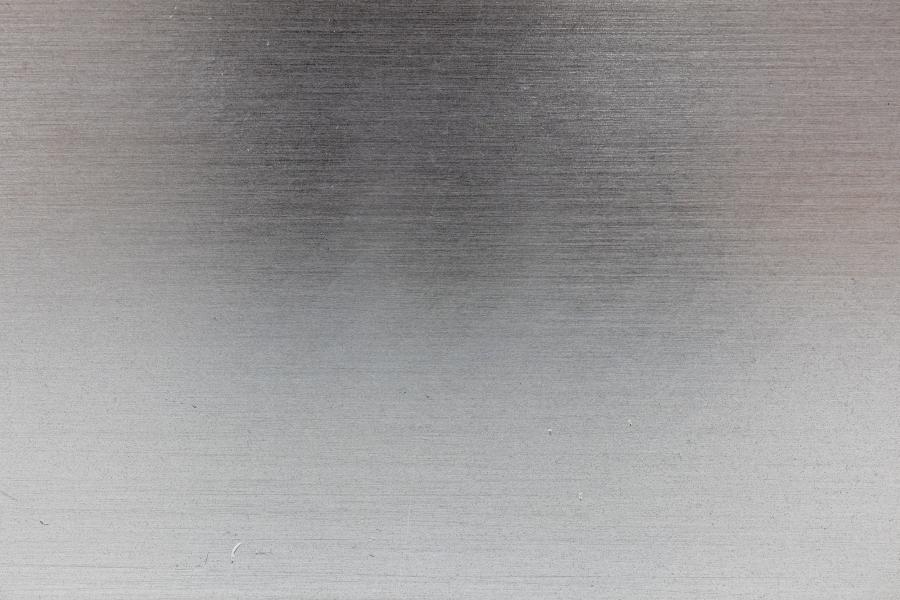
Während die Ionen an der Kathode Elektronen aufnehmen und gasförmigen Wasserstoff bilden, reagiert das Metall der Anode mit dem Sauerstoff der Hydroniumionen zu Metalloxid und Wasser. Die dabei freiwerdenden Elektronen fließen zum Pluspol der Spannungsquelle. Die Säure im Elektrolytbad ist an der Reaktion nicht beteiligt. Sie dient lediglich dazu, die Leitfähigkeit zu erhöhen und eine ausreichende Stromdichte im Bad zu ermöglichen.
Schichtbildung beim Eloxal-Verfahren
Die anodische Oxidation von Aluminium, das Eloxieren, erzeugt zunächst eine sehr dünne Schicht aus Aluminiumoxid auf der Werkstückoberfläche. Diese Schicht wirkt isolierend. Der Stromfluss wäre unterbrochen, würden nicht an einigen Stellen Spannungsdurchschläge erfolgen. An diesen Stellen bleibt der Stromfluss erhalten, die Schicht kann weiter anwachsen.
Aber dort, wo der Strom fließt, bleiben kleine “Kanäle” in der Schicht zurück. Das sind die Poren, die zum Schluss verschlossen werden müssen.
Eigenschaften der Eloxal-Schicht
Schichten, die durch das Eloxal-Verfahren erzeugt werden, weisen eine gute Haftung, einen hohen elektrischen Widerstand, eine hohe Härte und eine gute Korrosionsbeständigkeit in neutralen Flüssigkeiten (pH-Wert 5 bis 8) auf. Die Schichten sind außerdem ungiftig. Deshalb können eloxierte Aluminiumgeräte in der Lebensmittelindustrie verwendet werden. Auf der hohen Härte beruht die gute Verschleißfestigkeit.
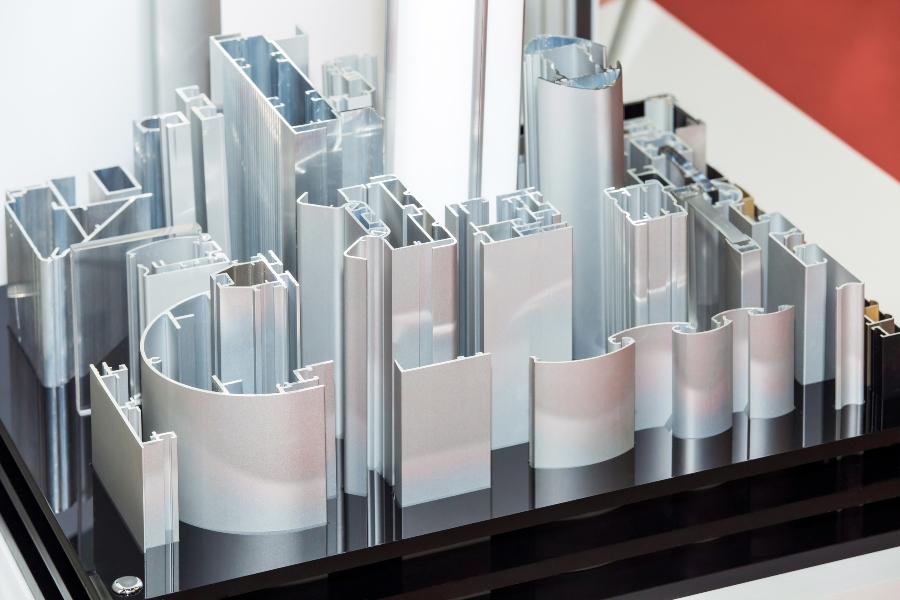