« Welche Beschichtungen halten besonders viel Wärme aus »
Mit steigender Temperatur ändern sich die physikalischen Eigenschaften der Werkstoffe. Außerdem nimmt die Geschwindigkeit chemischer Reaktionen, die zur Korrosion führen, zu. Die Wärmewirkungen können also zu Schäden im Material führen. Deshalb muss die thermische Belastung bei der Konstruktion von den Bauelementen berücksichtigt werden, die einer hohen Betriebstemperatur ausgesetzt sind. Die Oberflächentechnik hält optimale Lösungen für die Beschichtung thermisch belasteter Bauteile in unterschiedlichen Temperaturbereichen bereit.
Wirkung hoher thermischer Belastung auf beschichtete Werkstoffe
Ausdehnung bei Wärmezufuhr
Bei der Zufuhr von Wärme dehnen sich Werkstoffe aus. Dieses Verhalten wird durch den Wärmeausdehnungskoeffizienten beschrieben. Unterscheiden sich die Wärmeausdehnungskoeffizienten von Grundwerkstoff und Beschichtungsmaterial sehr stark, entstehen zwischen den beiden Materialien mechanische Spannungen.
Das kann sich besonders bei hohen Schichtdicken auf die Haftung der Schicht auswirken. Die Beschichtungswerkstoffe sollten deshalb ein ähnliches Wärmeausdehnungsverhalten wie der Grundwerkstoff aufweisen oder so beschaffen sein, dass sie die mechanische Spannung ertragen.
Verringerung der Belastbarkeit durch Festigkeitsverlust
Die mechanische Festigkeit der meisten Werkstoffe verringert sich bei einem Temperaturanstieg. Dann geben sie äußeren Kräften nach und verändern langsam ihre Form. Das als Kriechen bezeichnete Verhalten tritt verstärkt bei Temperaturen auf, die das 0,4–fache der absoluten Siedetemperatur übersteigen.
Die absolute Temperatur wird in Kelvin [K] gemessen. 0 °C sind 273,15 K.
Die erforderliche Temperaturbeständigkeit erreicht man durch Legierungen aus unterschiedlichen Metallen bzw. durch mineralische oder metallische Zusätze zu Anstrichstoffen. Besonders hohe Temperaturen erfordern keramische Werkstoffe.
Verstärkte Korrosion durch Wärmebelastung
Die Temperatur ist ein Maß für die Bewegungsenergie der Atome, aus denen sich die Werkstoffe zusammensetzen. Eine hohe thermische Belastung führt dazu, dass die Teilchen beweglicher werden und schneller mit den chemischen Stoffen aus der Umgebung reagieren. Schutz vor Korrosion bieten Beschichtungen aus unedlen Metallen, die sich auflösen, bevor der Grundwerkstoff angegriffen wird (z.B. Zink-Nickel-Beschichtung), oder die stabile schützende Oxidschichten auf ihrer Oberfläche bilden (z.B. Aluminium-Beschichtung).
Werkstoffermüdung bei Temperaturschwankungen
Schwankt die thermische Belastung der Bauteile durch wiederholtes Aufheizen und Abkühlen, kann es zur sogenannten Ermüdung des Werkstoffs kommen. Die Schicht dehnt sich bei der Temperaturerhöhung aus und zieht sich bei der Verringerung der Temperatur wieder zusammen. Dadurch ist sie ständig wechselnden mechanischen Spannungen ausgesetzt. In der Folge können sich Risse in der Schutzschicht bilden, die bis in den Grundwerkstoff hineinwachsen.
In diesen Fällen werden duktile Metalle oder Legierungen eingesetzt, die sich gut verformen können. Der Zusammenhalt im Werkstoff bleibt dann bestehen.
Beschichtungsstoffe für unterschiedliche Temperaturbereiche
Wärmebeständige Beschichtungen für eine Belastung unter 500 °C
Für erhöhte Temperaturen bis ca. 120 °C bei normalen Umgebungsbedingungen eignen sich Beschichtungssysteme auf der Basis von Acryl, Epoxidharz und Polyurethan. In diesem Bereich liegen die Oberflächentemperaturen von Heizkörpern und Rohrleitungen für die Warmwasserversorgung und für Dampfheizungen. Die thermische Belastung ist hier relativ gering. Ofenrohre und Abgasleitungen können sich bis auf ca. 250 °C erhitzen. Dieser Wärmebelastung halten Epoxid-Phenolharzlacke stand. Bei höheren Temperaturen versagen organische Bindemittel. Sie zersetzen sich thermisch. Zink-Nickel-Beschichtung, die häufig zum Korrosionsschutz von Motorenteilen und Abgasleitungen von Fahrzeugen eingesetzt wird, ist bis zu Temperaturen von ca. 300 °C beständig. Dann übernehmen Silikonharze. Sie ertragen Temperaturen bis ca. 350 °C.
Die konkrete Temperaturbeständigkeit ist von der genauen chemischen Zusammensetzung abhängig. Eine Belastbarkeit bis auf 450 °C wird durch den Zusatz von Zinkstaub erreicht. Metallische oder anorganische Zusätze wie Aluminium oder Glimmer in Form von Plättchen können die Temperaturbeständigkeit auf bis zu 600 °C steigern. Der Schutz von Bauteilen, die einer Belastung gleichzeitig durch hohe Temperaturen und aggressive Medien ausgesetzt sind, kann durch eine Emaillierung erfolgen. Diese korrosive und thermische Belastung ist häufig innerhalb von verfahrenstechnischen Anlagen anzutreffen. Die glasähnlichen Emailleschichten sind in einem Bereich von –60 bis +450°C korrosionsbeständig.
Hochtemperaturbeschichtungen für Temperaturen über 500 °C
Die Metallurgie, die Triebwerkstechnik und die Glasherstellung sind Beispiele für Bereiche, in denen Betriebstemperaturen bis über 1500 °C vorkommen. Hitzebeständige Stähle, besondere Legierungen und keramische Werkstoffe können diese Belastung ertragen. Den Korrosionsschutz für hitzebeständige Stähle erfüllen Beschichtungen aus Aluminium oder Chrom. Diese Metalle bilden mit dem Luftsauerstoff stabile, dichte Oxidschichten, die den Grundwerkstoff schützen.
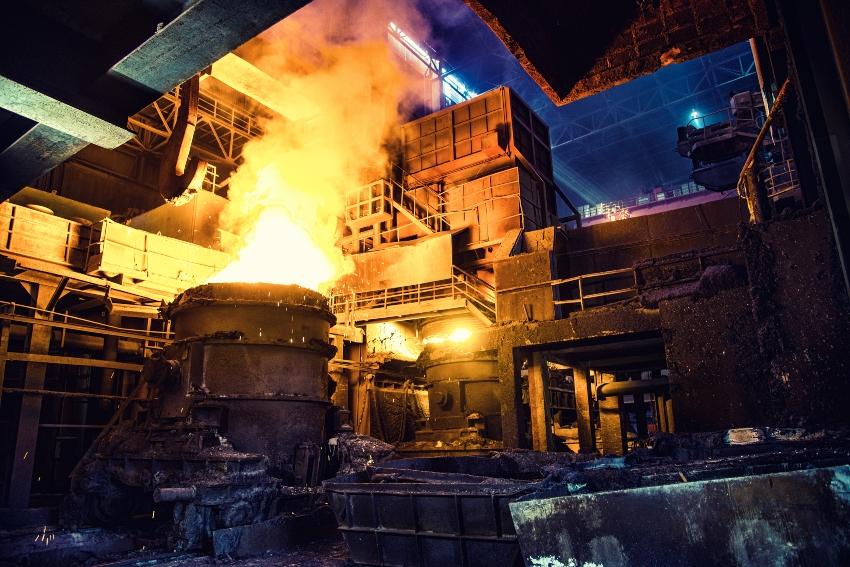
Beschichtungsverfahren
Temperaturbeständige Lacke werden in großtechnischen Anwendungen durch Pulverbeschichtung oder kathodische Tauchlackierung aufgebracht. Für Reparaturzwecke sind auch Lacksprays verfügbar. Legierungen aus Zink und Nickel werden galvanisch auf den Oberflächen abgeschieden. Hochtemperaturbeschichtungen erzeugt man durch eine thermische Beschichtung. Zu den verwendeten Verfahren gehören:
- chemische Gasphasenabscheidung
- physikalische Gasphasenabscheidung
- thermische Spritzverfahren
- Plattieren
Chemische Gasphasenabscheidung
Die chemische Gasphasenabscheidung (CVD, chemical vapour deposition) führt zu Schichten, die sich aus dem Grundwerkstoff und dem Beschichtungsstoff zusammensetzen.
Bei Temperaturen von ca. 1000 °C werden gasförmige chemische Verbindungen, die das schichtbildende Metall enthalten, mit der Teileoberfläche in Kontakt gebracht.
Dort löst sich das Metall aus der Verbindung und dringt in den Grundwerkstoff ein.
Physikalische Gasphasenabscheidung
Bei der physikalische Gasphasenabscheidung (PVD, physical vapour deposition) wird der Beschichtungsstoff verdampft. Der Dampf kondensiert auf der Bauteiloberfläche und bildet beim weiteren Abkühlen die Schutzschicht.
Thermische Spritzverfahren
Beim thermischen Spritzen wird das Beschichtungsmaterial geschmolzen und auf die Werkstückoberfläche gespritzt. Wärmequellen für das Aufschmelzen können eine Flamme, ein Lichtbogen, eine Plasmaflamme oder eine Detonation sein. Als Treibgas für den Spritzvorgang eignen sich Edelgase sehr gut. Aus der Wärmequelle leitet sich die jeweilige Bezeichnung für die thermische Beschichtung ab.
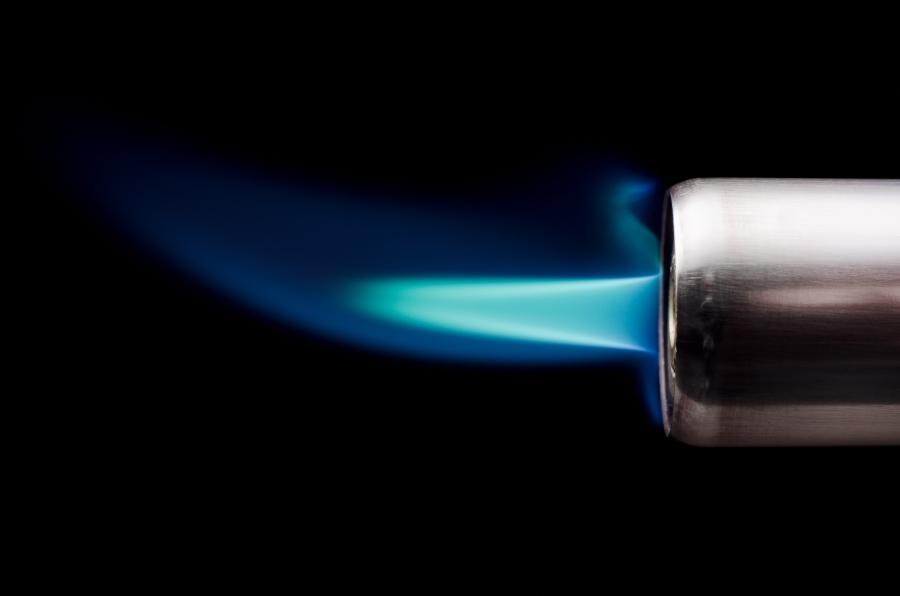
Plattieren
Bauteile mit einfachen Konturen, wie Bleche, Stangen und Rohre lassen sich durch das Plattieren gegen die thermische Belastung und die damit verbundene Korrosion schützen. Der Beschichtungswerkstoff hat die Form eines dünnen Bleches oder einer Folie. Er wird auf den Grundwerkstoff aufgewalzt.