Kunststoffadditive sind Zusätze, mit denen die Eigenschaften der Polymer-Werkstoffe gezielt beeinflusst werden. Die preiswerte Verfügbarkeit, das niedrige Gewicht und die leichte Verformbarkeit der Kunststoffe haben dazu geführt, dass Metalle, Glas oder Holz in vielen Industriezweigen durch solche Materialien ersetzt wurden. Diese Entwicklung ist vor allem im Fahrzeugbau, in der Luft- und Raumfahrt und in der Verpackungsindustrie zu beobachten. Um einen Kunststoff an die jeweiligen Erfordernisse anzupassen, sind Kunststoffadditive erforderlich. An der Oberfläche können diese Stoffe die Lackhaftung stören.
Lackhaftung und Oberflächenspannung
Eine Voraussetzung für die Haftung von Lack oder Druckfarben auf der Oberfläche eines Gegenstandes ist, dass die aufgetragenen Stoffe einen gleichmäßigen dünnen Film bilden. Flüssigkeiten haben das Bestreben, sich zu Tropfen zu formen, die der Filmbildung bei der Oberflächenbeschichtung entgegenwirken. Dieses Verhalten wird in der Physik mit Hilfe der Oberflächenspannung beschrieben. Die Wirkung der Oberflächenspannung lässt sich mit dem Zusammenwirken des Drucks innerhalb eines Luftballons mit seiner Hülle vergleichen. Der Ballon strebt immer die Gestalt einer Kugel an. Ein im luftleeren Raum frei fallender Tropfen erreicht eine exakte Kugelgestalt. Gelangt ein Tropfen auf eine feste Oberfläche, kommt es zu Wechselwirkungen zwischen der Oberflächenspannung und den Adhäsionskräften, die den Tropfen auf der Fläche festhalten.
Das Verhältnis der Oberflächenspannungen von Tropfen und Fläche entscheidet darüber, ob der Tropfen breitläuft oder ob die Kugelform mehr oder weniger erhalten bleibt. Ein Film bildet sich, wenn die Oberflächenspannung des Tropfens deutlich kleiner ist als die der Fläche. In diesem Fall kann die Flüssigkeit die Oberfläche benetzen.
Oberflächenspannung und Kunststoffadditive
Das charakteristische Merkmal von Kunststoffen ist ihre Molekülstruktur. Sie wird durch Makromoleküle bestimmt, die sich bei der Polymerisation aus kleinen reaktionsfähigen Molekülen bilden. Die Oberflächen der meisten Kunststoffe haben eine vergleichsweise geringe Oberflächenspannung. Das zeigt sich zum Beispiel beim Spülen von Geschirr. Auf den Teilen aus Kunststoff bleiben viele Wassertropfen hängen, von den anderen läuft das Wasser schnell ab.
Kunststoffadditive, die das Material widerstandsfähig gegen UV-Licht, Hitze und Witterungseinflüsse machen, die Festigkeit erhöhen, die Brennbarkeit herabsetzen oder die Verarbeitung verbessern, sind im Werkstoff gleichmäßig verteilt. Die Anteile, die sich direkt an der Oberfläche befinden, setzen die Oberflächenspannung herab und schränken die Farb- und Lackhaftung ein. Die Lackierung stellt unter diesen Bedingungen eine Herausforderung an die Oberflächentechnik dar. Weil die Kunststoffadditive in das Werkstoffgefüge eingebettet sind, lassen sie sich nicht durch normale Reinigungsverfahren entfernen.
Aktivierung von Kunststoffoberflächen
Die Vorbereitung von Kunststoffen für die Oberflächenbeschichtung wird als Aktivierung bezeichnet. Ziel der Aktivierung ist, die Kunststoffadditive von der Oberfläche zu entfernen und auf diese Weise die Bildung einer von Kunststoffadditiven verursachten Grenzschicht, dem sogenannten “weak boundary layer” zu verhindern. Dazu stehen verschiedene Verfahren zur Verfügung. Häufig angewendete Aktivierungsverfahren sind:
- Plasmaaktivierung
- Koronabehandlung,
- Beflammen
- Gasphasenfluorierung
Das gewählte Verfahren muss in den Prozess der Oberflächenbeschichtung eingegliedert werden und kurzfristig vor der Lackierung stattfinden. Die im Material vorhandenen Kunststoffadditive würden sonst langsam aus dem Werkstoffinneren an die Oberfläche wandern und die positiven Auswirkungen der Aktivierung auf die die Farb- oder Lackhaftung rückgängig machen.
Plasmaaktivierung
Plasma entsteht, wenn einem Gas große Mengen Energie zugeführt werden. Ab einem bestimmten Energiegehalt treten einzelne Elektronen aus den Gasteilchen aus. Das Gas wird zu einem Gemisch aus den negativ geladenen Elektronen, positiv geladenen Ionen und neutralen Gasmolekülen, die noch alle Elektronen behalten haben. Die geladenen Teilchen werden als freie Ladungsträger bezeichnet. Durch die freien Ladungsträger ist das Plasma elektrisch leitfähig.
Bei der Erzeugung von Plasma für die Vorbehandlung von Kunststoffen erfolgt die Energiezufuhr durch starke elektrische Felder, die von Wechselstrom hervorgerufen werden. In diesen Feldern bilden sich in der Luft freie Ladungsträger. Das aus der Luft entstandene kalte Plasma wird durch Düsen auf die Kunststoffoberflächen gesprüht. Die Ladungsträger gehen chemische Reaktionen mit den Kunststoffadditiven auf der Oberfläche ein. Die Oberflächenspannung des Materials wird dadurch erhöht; die störende Wirkung der Kunststoffadditive auf die Lackhaftung wird reduziert.
Der Vorteil der Plasmaaktivierung liegt im problemlosen Einfügen der Technik in vorhandene Anlagen für die Oberflächenbeschichtung.
Plasma eignet sich neben der Aktivierung von Kunststoffoberflächen auch direkt zum Auftragen von Druckfarben. Die Farbe gelangt in einem Arbeitsschritt im Plasmastrom auf die Fläche.
Koronabehandlung
Bei der Koronabehandlung werden die Kunststoffoberflächen direkt durch starke elektrische Felder beaufschlagt. Die Oberflächenspannung erhöht sich durch Veränderungen in der Werkstoffstruktur. Die Lackhaftung wird möglich. Die Lichterscheinung, die durch das elektrische Feld hervorgerufen wird, wird als Korona bezeichnet. Daraus resultiert der Name des Verfahrens. Es eignet sich gut für die Behandlung von Folien vor dem Bedrucken.
Die Folien werden zwischen einer elektrisch geerdeten Walze aus Metall und einer isolierten Elektrode bewegt. An der Elektrode liegt eine hohe Wechselspannung an, die das elektrische Feld verursacht.
Beflammen
Die Oberflächenspannung von Thermoplasten wie Polypropylen oder Polyethylen lässt sich durch die Einwirkung einer Propan- oder Acetylen-Flamme mit Sauerstoffüberschuss erhöhen. Die Wirksamkeit ist von der Relativgeschwindigkeit zwischen Oberfläche und Flamme, der Flammentemperatur und dem Abstand der Flamme vom Material abhängig. Bei Abweichungen von den optimalen Werten bleibt die beabsichtigte Wirkung aus oder der Kunststoff verbrennt.
Die Parameter werden empirisch (durch Versuche) ermittelt und durch Roboter gesteuert. Da dies mit einem hohen Aufwand verbunden ist, rechnet sich der Einsatz nur für große Serien. Die Oberfläche raut sich bei der Beflammung auf, die oberflächennahen Bereiche verändern ihre Struktur und die Kunststoffadditive werden oxidiert, sodass der Lack bei der nachfolgenden Beschichtung den erforderlichen dünnen Film bilden kann.
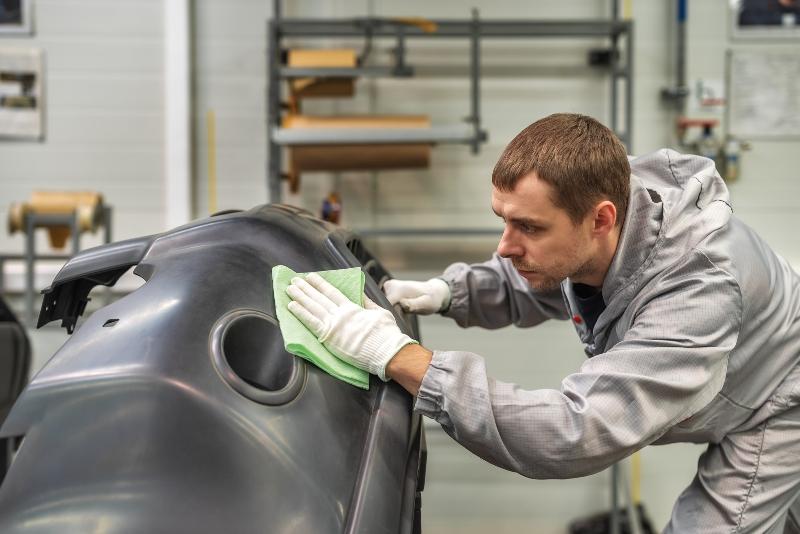
Gasphasenfluorierung
Für Bauteile mit komplizierten Geometrien wie Zahnräder, Kraftstofftanks, Gehäuse oder Teile von Verkleidungen eignet sich die Gasphasenfluorierung. Dabei werden die Teile in einer Vakuum-Kammer einem Gemisch aus Fluor und Stickstoff ausgesetzt. Das gasförmige Fluor reagiert an der Materialoberfläche mit dem Werkstoff. Es nimmt den Platz von Wasserstoffatomen ein und setzt Fluorwasserstoff frei.
Die chemischen Reaktionen führen zur Erhöhung der Oberflächenspannung und zur Verbesserung der Lackhaftung. Die Kunststoffadditive an der Oberfläche der Teile werden dauerhaft chemisch verändert. Da das Fluor leicht in Hohlräume und Spalten gelangt, kann der Lack im nächsten Bearbeitungsschritt sonst nur schwer erreichbare Stellen benetzen. Das Verfahren bringt zwar hervorragende Ergebnisse, ist aber auch sehr preisintensiv. Zu den hohen Kosten tragen neben dem technischen Aufwand auch die sicherheitstechnischen Maßnahmen bei, die für den Umgang mit Fluor und Fluorwasserstoff erforderlich sind. Diese Stoffe sind giftig und ätzend.