« So lassen sich Lackstörungen effektiv vermeiden »
Beschichtungsfehler bei der Lackierung sind in vielen Fällen erst sichtbar, wenn der Lack getrocknet ist. Manchmal wirken sie sich aus, nachdem die beschichteten Gegenstände bereits verbaut sind. Der immense Mehraufwand, den die Beseitigung derartiger Lackstörungen verursacht, lässt sich durch die sorgfältige Planung und Durchführung der Oberflächenbeschichtung vermeiden.
Sinn der Lackierung
Lacke sollen Oberflächen schützen, besondere Oberflächeneigenschaften hervorrufen und ein dekoratives Aussehen bewirken. Beschichtungsfehler sind die Ursache dafür, dass der Lackfilm an mindestens einer dieser Aufgaben scheitert. Abhängig vom Schwerpunkt der Tätigkeit, von den vorhandenen Werkstoffen und vom Verfahren, mit dem der Lack aufgetragen werden soll, wurden unterschiedlichste Lacksysteme entwickelt. Allen – bis auf Pulverlacke – gemeinsam ist, dass sie aus einer flüssigen Mischung aus Lösemitteln und Zusatzstoffen bestehen. Das Lösemittel verdunstet und die verbleibende Lackschicht wird fest. Danach soll diese als farblich und strukturell gleichmäßiger Film dauerhaft auf dem Untergrund haften.
Planung der Lackierarbeiten
Lackiersystem auswählen
Voraussetzung für die erfolgreiche Lackierung und zur Vermeidung von Beschichtungsfehlern ist die Auswahl des geeigneten Lackiersystems. Dabei sind die Beschaffenheit des Untergrundes und die zu erwartenden Beanspruchungen zu berücksichtigen. Für einige Abwendungsfälle muss die Fläche mit Spachtelmasse behandelt und grundiert werden. Bei anderen Arbeiten reicht die gründliche Reinigung der Oberfläche für die gewünschten Ergebnisse aus. Außerdem ist die Verträglichkeit des Werkstoffes mit den Lösemitteln, die Haftfähigkeit auf dem vorhandenen Material und die Saugfähigkeit des Untergrundes zu prüfen.
Benötigte Menge des Lacks bestimmen
Die Menge der zu beschaffenden Materialien muss für die zu beschichtende Fläche ausreichen. Wird zu wenig Farbe beschafft, ist es schwierig, den genauen Farbton wiederzufinden. Die Farbtöne weichen dann an den Übergängen voneinander ab. Die Farben haben eine zeitlich begrenzte Haltbarkeit. Bleibt zu viel Farbe übrig, muss sie in der Regel entsorgt werden. Auf den üblichen Verpackungen stehen Angaben, welche Mengen des Inhalts pro Quadratmeter erforderlich sind.
Geeignete Auftragstechnik auswählen
Eine zusammenhängende Fläche soll in einem Durchgang lackiert werden. Wird die Arbeit für längere Zeit unterbrochen, sind Beschichtungsfehler wie Farbunterschiede an den Übergängen zu erwarten. Von der Größe der Fläche hängt ab, wie zeitintensiv das gewählte Verfahren sein darf. Für kleine Flächen sind Spachtel und Pinsel ausreichend, größere Flächen können mit Farbrollen beschichtet werden, für sehr große Flächen sind Spritzpistolen geeignet.
Zeitmanagement beim Lackieren
Der Aufbau der Beschichtung besteht häufig aus mehreren Anstrichen. Jede Schicht benötigt zum Trocknen und aushärten eine genau bestimmte Zeit. Wird diese unterschritten, ergeben sich Lackstörungen aus dem Vermischen der Farbschichten. Wird sie überschritten, können Haftungsprobleme bei der folgenden Schicht und die Bildung von Bläschen auftreten.
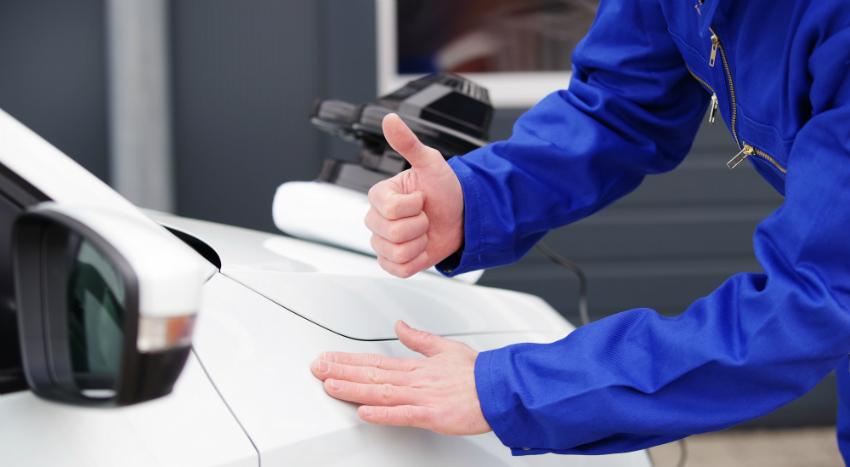
Vorbereitung des Untergrundes
Reinigung
Die Oberflächen müssen vor der Oberflächenbeschichtung frei von Verunreinigungen und trocken sein. Aus ungenügender Reinigung und Trocknung ergeben sich folgende Beschichtungsfehler:
- Abblättern der Farbe durch mangelnde Haftungsfähigkeit
- Benetzungsstörungen durch farbabweisende Verunreinigungen wie Handschweiß oder Reste von Hautcreme
- kleine pickelartige Erhebungen durch Einschlüsse von Staub und anderen Verunreinigungen
- Bläschenbildung durch verdunstendes Wasser aus dem Material
- Rissbildung in der Farbschicht
Schleifen und Spachteln
Das Glattschleifen der Oberflächen und das Anschleifen zwischen zwei Beschichtungen müssen mit einer ausreichend feinen Körnung erfolgen. Ist die Körnung zu grob, ergeben sich später deutlich sichtbare Schleifriefen, an deren Rändern sich der Lack ansammelt und aufquillt. Bleiben nach dem Schleifen Poren im Untergrund zurück, machen sich die kleinen Vertiefungen nach dem Trocknen als “Nadelstiche” bemerkbar. Sorgfältiges Auftragen von Spachtelmasse verhindert diesen Beschichtungsfehler. Beim Zwischenschleifen darf die letzte Schicht an keiner Stelle vollständig entfernt werden. An diesen Stellen würde sich die Folgeschicht aufkräuseln und hochziehen.
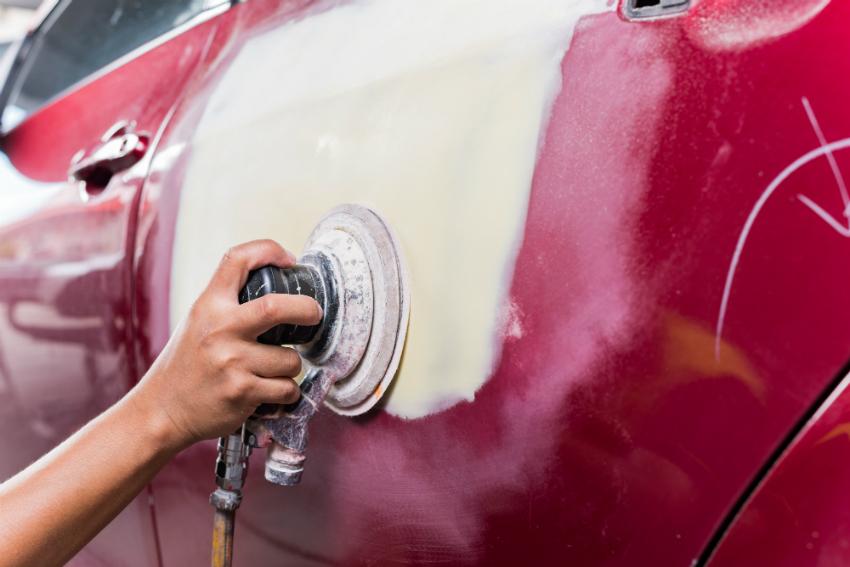
Was ist beim Beschichten selbst zu beachten, um Beschichtungsfehler zu vermeiden?
Umgang mit den Materialien
Die Grundierung und die Lackierung müssen sauber gehalten werden. Verunreinigungen rufen ähnliche Beschichtungsfehler hervor wie mangelhafte Oberflächenreinigung. Bei der Lagerung der Gebinde setzen sich Pigmente am Boden ab, Lösungsmittel sammeln sich an der Oberfläche. Deshalb ist es erforderlich, die einzelnen Farben gründlich zu durchmischen. Wird dies versäumt, kommt es zu fehlender Deckkraft und Abweichungen der Farbverteilung.
Mischungsverhältnisse korrekt einhalten
Bei Produkten aus mehreren Komponenten sind die Mischungsverhältnisse korrekt einzuhalten und nur aufeinander abgestimmte Bestandteile zu verwenden. Werden Farben mit unverträglichen Verdünnern gemischt, trübt sich die Mischung ein. Das kann zur Bildung von Klümpchen, zum Verstopfen von Spritzdüsen führen und unterschiedliche Beschichtungsfehler verursachen.
Geforderte Umgebungsbedingungen berücksichtigen
Zu hohe Luftfeuchtigkeit bewirkt, dass sich bei Temperaturschwankungen Kondenswasser aus der Luft ausscheidet, das graue Schleier oder die Konturen von Wassertropfen zurücklässt. Zu hohe oder zu niedrige Temperaturen rufen Lackstörungen hervor, die auf zu schnellem Verdunsten des Lösungsmittels und auf der falschen Fließfähigkeit beruhen. Trocknet die Schicht zu schnell, können sich Risse bilden. Ist es zu kalt, wird die Farbe zähflüssiger. Verlaufsstörungen wie Apfelsinenhaut oder Lackläufer sind die Folge. Feuchtigkeit kann auch zum Glanzverlust der Oberfläche führen.
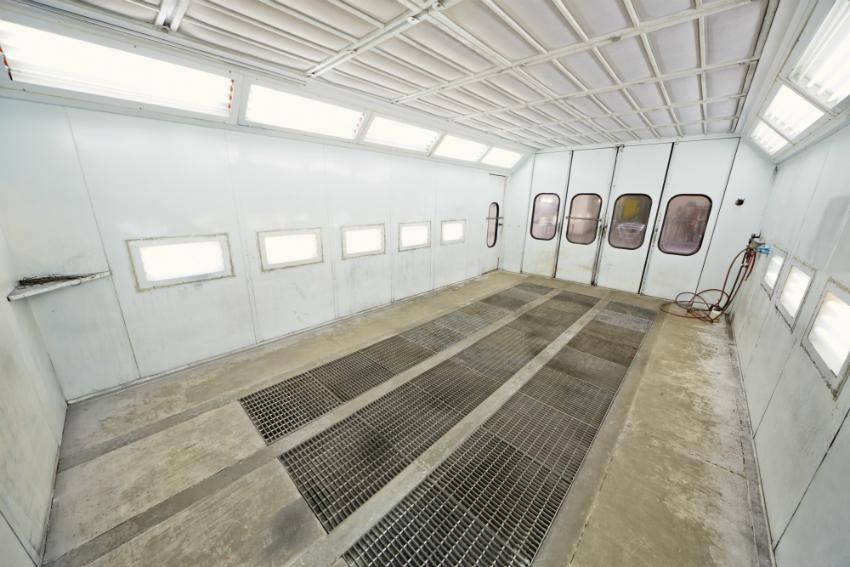
Vorgegebene Schichtstärke einhalten
Die von den Herstellern der Lacke vorgegebene Schichtstärke ist auf die ordnungsgemäße Trocknung abgestimmt. Viele Beschichtungsfehler gehen auf Abweichungen von diesen Vorgaben zurück. Bei zu dicken Schichten wird die Oberfläche fest und zieht sich zusammen, während der Untergrund noch weich ist. Die weichen Bereiche üben einen Druck aus, der Steifen, Randmarkierungen, Kräuselungen und Risse verursacht. Randmarkierungen sind Unebenheiten in der Lackoberfläche mit erhöhten Rändern. Zu dünnen Schichten fehlt die Deckkraft. Für die korrekte Schichtdicke beim Spritzlackieren sind die Vorgaben der Hersteller zur Düsengröße und zum Druck einzuhalten.
Ablüften und Trocknen
Für das Ablüften und das Trocknen der Oberflächenbeschichtung sind von den Herstellern der Lacksysteme genaue Zeiten und Bedingungen vorgesehen. Werden diese nicht eingehalten treten Beschichtungsfehler wie Haftungsstörungen und Rissbildung ein. In vielen Fällen kommt es auch zur Bildung von Runzeln oder Bläschen. Erfolgt die Trocknung in einer staubbelasteten Umgebung, setzen sich die Schmutzteilchen auf der Oberfläche ab und bleiben dort kleben.
Anwendungs- und Verarbeitungsvorschriften beachten
Die einzelnen Lacke wurden mit den folgenden Schwerpunkten entwickelt:
- Haltbarkeit der Farbschichten
- Verträglichkeit mit Werkstoffen
- Beschichtungsverfahren und
- Umweltverträglichkeit
Die unterschiedlichen Einflussfaktoren haben zu einem umfangreichen Angebot verschiedener Mittel für die Oberflächenbeschichtung geführt. Den optimalen Lack für einen ganz bestimmten Einsatz herauszufinden, ist deshalb oft sehr aufwendig. Laien sollten sich bei der Auswahl beraten lassen. Die Hersteller von Lacksystemen stellen in der Regel Merkblätter zur Verfügung, in denen sie die Eigenschaften, die Einsatzbereiche und Vorschriften für die Verarbeitung zusammenstellen. Die genaue Einhaltung dieser Vorgaben beugt Beschichtungsfehlern und Lackstörungen vor.