« Welche Option der Lackierung ist zu empfehlen? »
Sowohl Pulverlack als auch Nasslack sind Mittel, die in der Oberflächenbeschichtung breite Anwendung finden. Die Entscheidung für eine der beiden Varianten hängt hauptsächlich vom Material, der Kontur und der Größe der zu lackierenden Teile sowie von den Anforderungen an die erzeugten Schichten ab. Entscheidenden Einfluss haben darüber hinaus die Rentabilität der Technik für die Lackierung und die Erwirtschaftung der laufenden Kosten.
Aufbringen des Lacks auf die Oberflächen
Pulverlack besteht aus fein gemahlenen festen Körnern. Nasslack ist eine flüssige Mischung aus dem Lack und einem Lösemittel oder zwei Komponenten, die sich chemisch miteinander verbinden. Daraus ergibt sich die Technologie für die Lackierung. Während eine Flüssigkeit Oberflächen benetzt, rieselt ein Pulver im Normalfall herab.
Bei der Pulverlackierung wird das Herabrieseln verhindert, indem die Körner elektrostatisch aufgeladen und dadurch von den Oberflächen angezogen werden. Das Prinzip funktioniert nur bei metallischen Werkstoffen, die geerdet sind. Materialien wie Kunststoffe, mineralische Baustoffe oder Holz können nur mit Flüssiglack beschichtet werden.
Trocknungsbedingungen
Die endgültige feste Lackschicht bildet sich bei Pulverlack durch das Aufheizen der vorbereiteten Teile in einem Trockenofen. Dort schmilzt das Pulver, verteilt sich gleichmäßig auf der Oberfläche und härtet beim Abkühlen aus. Flüssiglack wird fest, wenn das Lösemittel verdunstet bzw. die Bestandteile des Lacks miteinander (Zweikomponentenlack) oder mit dem Luftsauerstoff (Kunstharzlack) chemisch reagieren.
Diese Vorgänge dauern in den meisten Fällen länger als das Aufheizen im Trockenofen. Lacke, die auf der Basis verdunstender Lösemittel oder durch Reaktion mit dem Luftsauerstoff trocknen, werden von außen nach innen fest. Um zu gewährleisten, dass die der Luft abgewandten, werkstoffnahen Bereiche ordnungsgemäß durchtrocknen, muss flüssiger Lack häufig in mehreren dünnen Schichten aufgetragen werden bis die benötigte Gesamtdicke erreicht ist. Erst wenn eine Zwischenschicht getrocknet ist, kann die nächste aufgetragen werden. Bei der Pulverlackierung ist für die erforderliche Schichtdicke nur ein Durchlauf notwendig. Dieses Verfahren benötigt weniger Zeit und ist außerdem etwas preiswerter.
Eigenschaften der Lackschichten
Die Beschaffenheit von Lackschichten wird zu einem erheblichen Teil von der Oberflächenvorbehandlung bestimmt. Dazu zählen die Reinigung und Entfettung, die Erzeugung von Konversionsschichten und die Trocknung der Oberflächen. Diese vorbereitenden Prozesse sind unabhängig vom verwendeten Lacksystem erforderlich.
Sie bewirken eine gute Lackhaftung und eine gleichmäßige Beschichtung. Stahlteile, die im späteren Gebrauch starken mechanischen Beanspruchungen und der Witterung ausgesetzt sind, werden im Rahmen der Oberflächenvorbehandlung, vor allem vor der Pulverbeschichtung, häufig zusätzlich verzinkt.
Die modernen Lacksysteme sind so optimiert, dass sich mit Pulverlack und mit Nasslack ähnliche Schichteigenschaften erreichen lassen. Liegt der Schwerpunkt auf dem Korrosionsschutz, geht die Tendenz eher zur Pulverlackierung. Diese Lackierung ist kratz- und abriebfest, witterungsbeständig und elastisch. Dadurch verringert sich die Gefahr von Rissen in der Lackschicht biegebeanspruchter Teile.
Im Maschinen- und Gerätebau sowie beim Bau von Landmaschinen und Nutzfahrzeugen ist die Pulverbeschichtung das am meisten eingesetzte Verfahren. Die Nasslackierung wird bevorzugt, wenn zusätzlich zum Korrosionsschutz bestimmte optische Effekte erzielt und wenn nichtmetallische Werkstoffe beschichtet werden sollen.
Eine mehrfarbige oder hochglänzende Oberflächenbeschichtung lässt sich durch dieses Verfahren wesentlich leichter bewerkstelligen. Große Anwendungsfelder für Nasslack sind die kathodische Tauchlackierung von Fahrzeugkarosserien für Personenkraftwagen und die Lackierung von Gehäusen aus Kunststoffen.
Aufbau der Beschichtungstechnik
Im industriellen Maßstab erfolgt die Lackierung in Anlagen, die aus mehreren Stationen bestehen. An die Oberflächenvorbehandlung, die aus aufeinanderfolgenden Prozessen aufgebaut ist, schließen sich die Farbgebung und die Trocknung an. Bestandteil größerer Anlagen ist Technik zur Rückgewinnung von Rohstoffen und Betriebswasser, zur Abluftreinigung und zur Aufbereitung des Abwassers.
Verarbeitung von Pulverlack
Zum Auftragen von Pulverlack werden Pulversprühkabinen benötigt. Diese sind geschlossen oder mit Öffnungen versehen. Geschlossene Kabinen werden chargenweise betrieben. Für einen kontinuierlichen Betrieb oder den Einsatz von Handsprühgeräten werden Kabinen mit einsprechenden Öffnungen verwendet. Die zu beschichtenden Teile befinden sich an Gehängen, über die auch die Erdung erfolgt. Der Lack wird von einem Luftstrom durch eine Sprühpistole getrieben. Die elektrostatische Aufladung wird durch ein elektrisches Feld am Ausgang der Pistole (Korona) oder durch Reibung innerhalb der Pistole erzeugt. Die aufgeladene Pulverwolke wird von den Oberflächen angezogen. Dadurch entsteht wesentlich weniger Overspray (Lack, der die Oberfläche verfehlt) als beim Nasslackieren.
Dem Verlauf des elektrischen Feldes folgend, gelangen die Lackteilchen auch an hinterschnittene und rückseitige Flächen. Die Aushärtung von Pulverlack erfolgt im Trockenofen mit einer genauen Temperaturführung. Der Temperaturverlauf besteht aus den Phasen Aufheizen, Halten und Abkühlen. Durch die Kabinengröße und die Größe des Trockenofens sind die Abmessungen der Teile begrenzt. Der Overspray wird in regelmäßigen Zeitabständen aus der Kabine gefördert. Kleine Mengen werden in der Regel entsorgt. Bei großen Mengen rentiert sich die Aufbereitung und Rückführung.
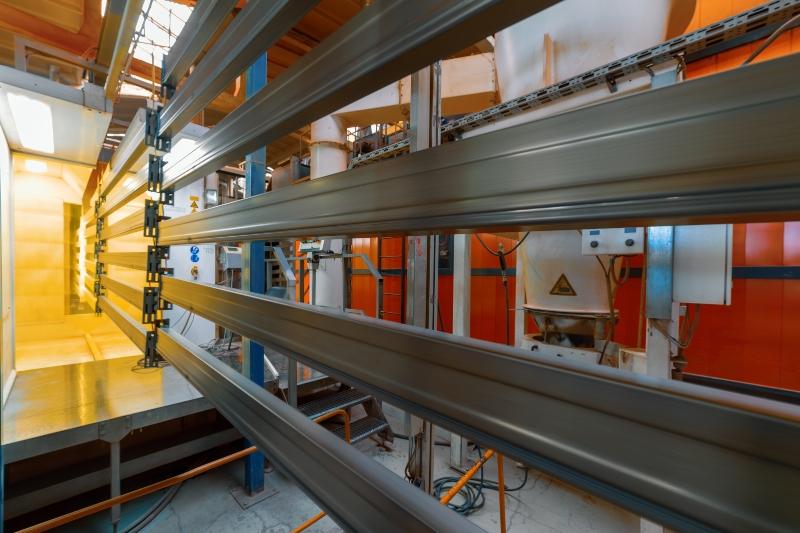
Verarbeitung von Nasslack
Die Nasslackierung kann durch Streichen, Sprühen oder Tauchen erfolgen. Je nach Werkstückaufkommen werden die Arbeiten an Handarbeitsplätzen, in Tauchbecken oder in Spritzkabinen durchgeführt. Beim Sprühen ergeben sich größere Lackverluste durch den Overspray, der an der Oberfläche vorbeiströmt und in größeren Anlagen durch eine Wasserwand aufgefangen wird. Der Lack gelangt nur an die Flächen, die der Austrittsöffnung zugewandt sind. In Tauchbecken entfallen die Verluste durch Overspray. Der Flüssiglack gelangt an alle Bereiche der Oberfläche. Für eine gleichmäßige Oberflächenbeschichtung von Teilen mit komplizierten Konturen wird das Tauchen durch ein elektrisches Feld unterstützt. Das Feld wird durch eine Gleichspannung erzeugt, die zwischen dem Teil und zusätzlichen Elektroden anliegt. (kathodische Tauchlackierung)
Das Trocknen der lackierten Teile kann ohne Einsatz von Wärmeenergie an der Luft erfolgen. Durch eine moderate Wärmezufuhr lässt sich dieser Vorgang beschleunigen.
Sicherheits- und umwelttechnische Aspekte
Ein Vorteil bei der Verarbeitung von Pulverlack ist die Abwesenheit von flüchtigen organischen Lösemitteln und der geringere Wasserverbrauch. Gesteigerter Aufmerksamkeit bedarf die elektrisch aufgeladene Pulverwolke. Das Lackpulver besteht aus überwiegend organischen Stoffen, die brennbar sind. Deshalb müssen Vorkehrungen gegen eine Staubexplosion getroffen werden. Das trifft vor allem auf die Abluftanlage zu. Wird der Pulverlack in der Kabine von Hand gespritzt, ist das Personal vor elektrischen Schlägen zu schützen. Die betreffenden Mitarbeiter dürfen sich selbst nicht elektrisch aufladen. Das wird durch leitfähige Arbeitskleidung, leitfähiges Schuhwerk und leitfähige, geerdete Fußböden erreicht.
Nachteilig ist bei der Pulverlackierung der im Vergleich zur Nasslackierung höhere Energieverbrauch durch den Trockenofen für die Aushärtung. Bei der Nasslackierung wird häufig mit flüchtigen organischen Lösemitteln gearbeitet, die brennbare Dampf-Luft-Gemische bilden können und als Luftschadstoffe gelten. Dieser Nachteil wird durch den zunehmenden Einsatz von wasserbasierendem Lack zurückgedrängt.