Wie funktioniert die Manganphosphatierung?
Die Manganphosphatierung ist ein Konversionsverfahren, das hauptsächlich auf den Oberflächen von Werkstücken aus niedrig legierten Eisenwerkstoffen angewendet wird. Manganphosphatschichten bewirken einen guten Korrosionsschutz und zeichnen sich besonders durch ihre Verschleißfestigkeit bei gleitender Bewegung aus. Hier erfahren Sie, wie Konversionsschichten aus Manganphosphat erzeugt werden und sich diese Phosphatierung auf die Eigenschaften der Werkstücke auswirkt.
Ablauf der Manganphosphatierung: wie Mangansphosphatschichten entstehen
Die Arbeitsschritte bei der Manganphosphatierung sind:
- Reinigung und Entfettung der Oberflächen
- Beizen zur Entfernung von Rost und Zunder
- Aktivierung der Oberflächen
- Erzeugung der Manganphosphatschicht
- Weiterbehandlung durch Beölung oder Beschichtung
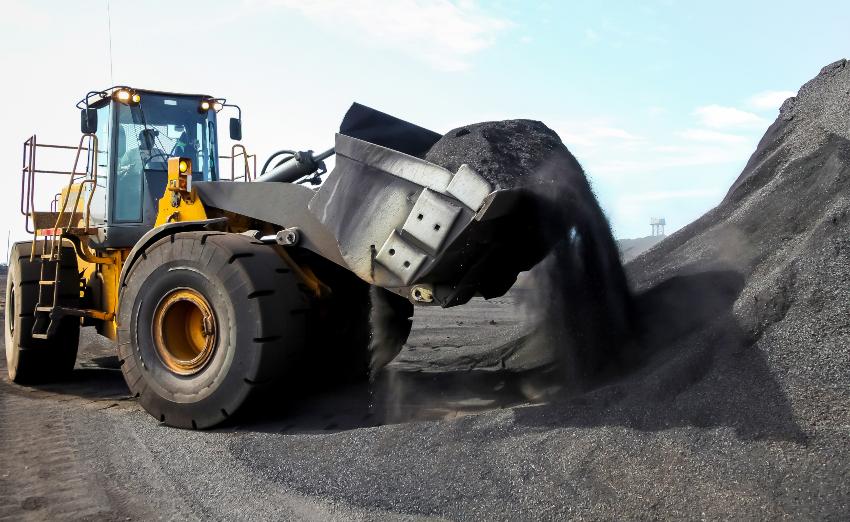
Reinigung und Entfettung der Oberflächen
Die Reinigung und Entfettung der Oberflächen steht am Beginn jeder Oberflächenvorbehandlung. Auf den Werkstücken sind häufig Rückstände von Kühlschmiermitteln aus der vorausgehenden Bearbeitung oder Korrosionsschutzmittel vorhanden, die die Wirkung der eingesetzten Prozesschemikalien beim Aufbau der Manganphosphatschicht beeinträchtigen würden. Die Entfernung der Verunreinigungen richtet sich nach der Art der Verschmutzung. Für hartnäckige fettige Ablagerungen sind alkalische Reinigungsmittel gut geeignet. Leichte Verschmutzungen lassen sich durch mildere Neutralreiniger entfernen. Das anschließende gründliche Spülen in einer Kaskade beseitigt die Reste der Reinigungslösung. Dabei durchlaufen die Werkstücke hintereinander geschaltete Becken. In der Gegenrichtung fließt vollentsalztes Wasser, das sich nach dem Spülvorgang für den Neuansatz der Reinigungslösung verwenden lässt.
Beizen zur Entfernung von Rost und Zunder
Nach einer Wärmebehandlung und nach Schweißprozessen bleiben auf den Oberflächen oft Rost oder Zunder zurück. Eine längere Lagerung der Werkstücke kann zur Bildung von rostigen Stellen führen. Da bei Konversionsverfahren chemische Reaktionen stattfinden, wären derartige Fremdstoffe äußerst störend. Das Beizen ist nur erforderlich, wenn die Werkstücke entsprechende Beeinträchtigungen aufweisen. Es erfolgt meist mit einer anorganischen Säure, die derartige Stoffe auflöst. An den Beizvorgang schließt sich eine mehrstufige Kaskadenspülung an.
Aktivierung der Oberflächen
Vor der Manganphosphatierung müssen die Oberflächen aktiviert werden. Als Salze der Phosphorsäure haben die Phosphate eine kristalline Struktur. Das Aktivierungsmittel erzeugt auf den Oberflächen Kristallisationskeime. An diesen Stellen beginnt die Bildung der Manganphosphatschicht. Die Kristalle wachsen solange, bis sie aneinanderstoßen und kein Platz mehr vorhanden ist. Deshalb bestimmt die Menge und Verteilung der Kristallisationskeime, wie groß die Phosphatkristalle im nachfolgenden Arbeitsschritt werden. Die Wahl des geeigneten Aktivierungsmittels ermöglicht es, den Aufbau der Manganphosphatschicht optimal zu gestalten und dem späteren Verwendungszweck anzupassen.
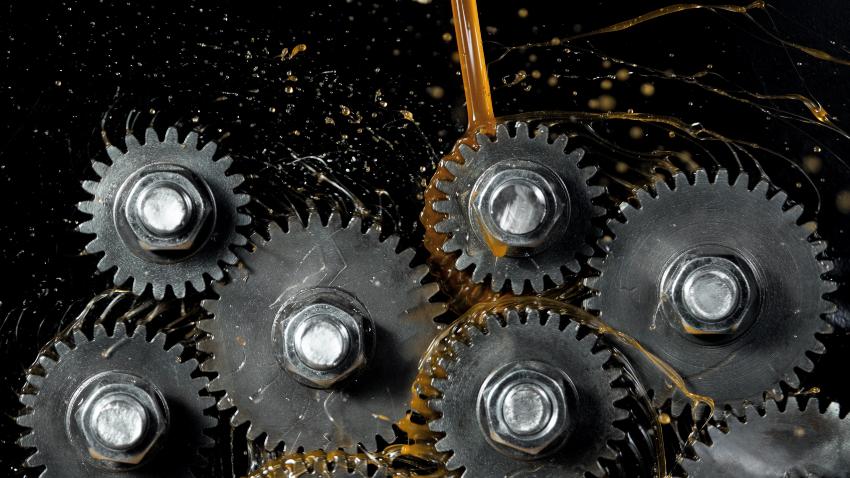
Erzeugung der Manganphosphatschicht
Die Manganphosphatierung erfolgt in Bädern durch die Einwirkung von verdünnter Phosphorsäure, Manganionen und weiteren Stoffen. Die Badtemperatur beträgt bei diesem Konversionsverfahren in der Regel 85 °C, die Einwirkungsdauer liegt meist zwischen 5 und 20 Minuten. Eine mehrstufige Kaskadenspülung und eine anschließende Trocknung beenden die Phosphatierung. Um bei der Erzeugung von Manganphosphatschichten die Konzentration der Prozesschemikalien in den erforderlichen Grenzen zu halten, müssen die Bäder überwacht werden. Der Nachschub der verbrauchten Stoffe lässt sich über Dosierpumpen bewerkstelligen. Verdunstetes Wasser wird zweckmäßig durch Spülwasser ausgeglichen, das bei der abschließenden Kaskadenspülung anfällt. Bei der Manganphosphatierung entsteht Schlamm, der am besten kontinuierlich über einen Schrägboden aus dem Bad entfernt wird. Andernfalls müsste das Bad regelmäßig entleert, entschlammt und neu befüllt werden.
Im Periodensystem der Elemente stehen Mangan (Ordnungszahl 25) und Eisen (Ordnungszahl 26) unmittelbar nebeneinander. Die beiden Stoffe ähneln sich stark in ihren chemischen Eigenschaften, und ihre Ionen sind nahezu gleichgroß. Auf den Werkstoffoberflächen bilden sich leicht Mischkristalle, die neben den Phosphationen sowohl Mangan- als auch Eisenionen aus dem Grundwerkstoff enthalten. Die beiden Metallionen können praktisch in jedem Verhältnis beteiligt sein. Die Kristallgröße hängt von der vorausgegangenen Oberflächenaktivierung ab. Für die Schichtdicke sind außerdem die Verweilzeit und die Betriebsbedingungen im Phosphatierungsbad entscheidend. Die Schichtdicken lassen sich sehr genau herstellen. Sie liegen üblicherweise zwischen 2 und 5 µm. Dicken bis zu 30 µm sind möglich.
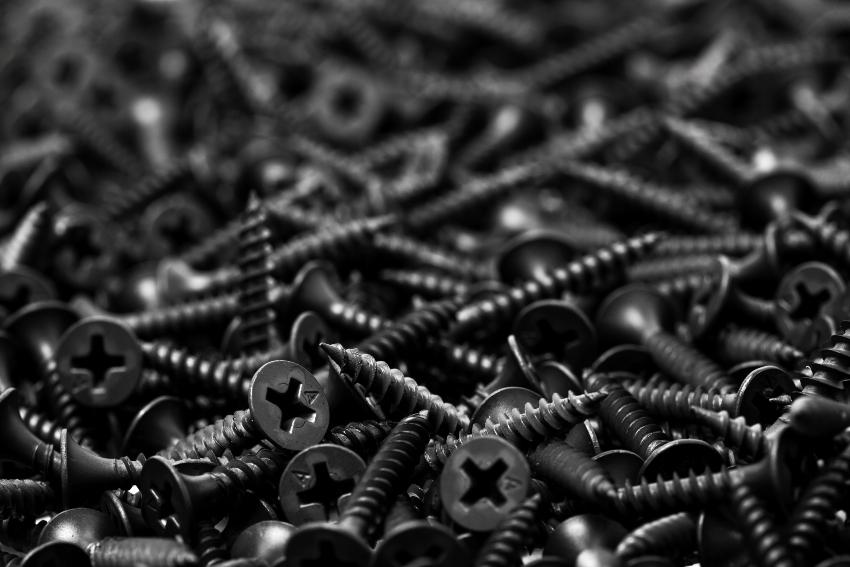
Weiterbehandlung durch Beölung oder Beschichtung
Manganphosphatschichten eigenen sich wegen ihrer sehr feinen porösen Struktur hervorragend als Haftgrund für eine anschließende Lackierung. Deshalb erfolgt die Manganphosphatierung häufig bei Oberflächenvorbehandlung vor einer organischen Beschichtung von hochwertigen Bauteilen. Die Struktur bewirkt auch eine gute Aufnahmefähigkeit für Öle und Fette. Zum Korrosionsschutz werden die Werkstücke in entsprechende Bäder getaucht. Die Korrosionsschutzmittel dringen in die Poren ein und werden dort festgehalten.
Einsatzbereiche für die Manganphosphatierung
Manganphosphatschichten zeichnen sich besonders durch ihre Verschleißfestigkeit und die Verringerung der Reibung bei gleitender Bewegung aus. Deshalb werden sie oft auf Bauteilen von Getrieben und Gleitlagern eingesetzt. Diese Vorteile wirken sich auch bei Umformprozessen aus. Erhalten Werkstücke, die beispielsweise durch Tief-, Draht- oder Rohrziehen weiter bearbeitet werden sollen, eine Manganphosphatschicht, sinken der Kraftaufwand für die Umformung, der Werkzeugverschleiß und das Risiko der Kaltverschweißung.
Weitere Eigenschaften von Phosphatschichten sind:
- elektrisch isolierend
- bis 300 °C temperaturbeständig
- attraktives, schwarz-graues, matt schimmerndes Erscheinungsbild
- hohe Maßhaltigkeit
- biegefest
- wasserunlöslich
- beständig gegen Lösemittel, Kraftstoffe und Schmiermittel
- fest auf der Oberfläche haftend
- umweltfreundlich
Die Einsatzgebiete für die Manganphosphatierung erstrecken sich über die Herstellung von Verbindungselementen und Zahnrädern über Bauteile für Wälz- und Gleitlager bis zu Teilen für Armaturen. Unter den Branchen, in denen Manganphosphatschichten benötigt werden, sind unter anderem der Fahrzeugbau, der Maschinenbau, die Luft- und Raumfahrttechnik sowie der Anlagenbau vertreten.
Im Maschinenbau und in der Waffentechnik ist immer noch das Brünieren verbreitet. Dieses Konversionsverfahren bewirkt einen temporären Korrosionsschutz und eine attraktive Schwarzfärbung. Brünierschichten werden durch bis zu 150 °C heiße, hochkonzentrierte Salzlösungen erzeugt, sind bis zu 1 µm dick und sehr glatt. Die stark alkalischen Brüniersalze sind als Gefahrstoffe eingestuft. In den meisten Fällen kann das energieaufwändige, umweltbelastende Brünieren durch die Manganphosphatierung ersetzt werden.