Durch eine professionelle Oberflächenbehandlung lässt sich die Lebensdauer von Werkstücken deutlich erhöhen. Welche Methode dabei zur Anwendung kommt, richtet sich zum einen nach dem Basismaterial, zum anderen aber auch nach dem zu erzielenden Effekt. Zu den wichtigsten Verfahren in diesem Bereich zählen das Galvanisieren und das Eloxieren. Beide funktionieren mit Strom und können gleichermaßen zu Schutz- und zu Dekorationszwecken eingesetzt werden, doch damit enden die Gemeinsamkeiten auch schon.
Oberflächenbeschichtung durch Galvanisieren
Beim Galvanisieren bringt elektrischer Strom Metalle dazu, sich gleichmäßig an Werkstückoberflächen abzulagern. In den meisten Fällen dient die Metallschicht dem Schutz vor mechanischem Verschleiß, dem Korrosionsschutz und/oder der Verbesserung der elektrischen Leitfähigkeit. Darüber hinaus kann das Ziel der Galvanisierung in einer leichteren Weiterverarbeitung und im Erzielen optischer Veränderungen bestehen.
Verwendung findet die Galvanik vor allem bei Werkstücken aus Stahl oder Edelstahl. Als Schutzschicht dienen Metalle mit einem für die jeweilige Anwendung geeigneten Eigenschaftsprofil, beispielsweise:
- Kupfer,
- Zink,
- Zinn,
- Messing,
- Nickel,
- Silber und
- Gold.
Die Galvanotechnik eignet sich nicht nur für das Überziehen metallischer Gegenstände, sondern auch für Kunststoffe, Keramiken und Glas. Diese werden vorab durch das Beschichten mit metallhaltigem Lack, mithilfe chemisch erzeugter Metallüberzüge oder durch das aufwendige Ausstatten mit Metallkeimen leitfähig gemacht. Als Beschichtungsmaterial kommen hierbei in erster Linie Chrom, Kupfer, Zink und Nickel zur Anwendung.
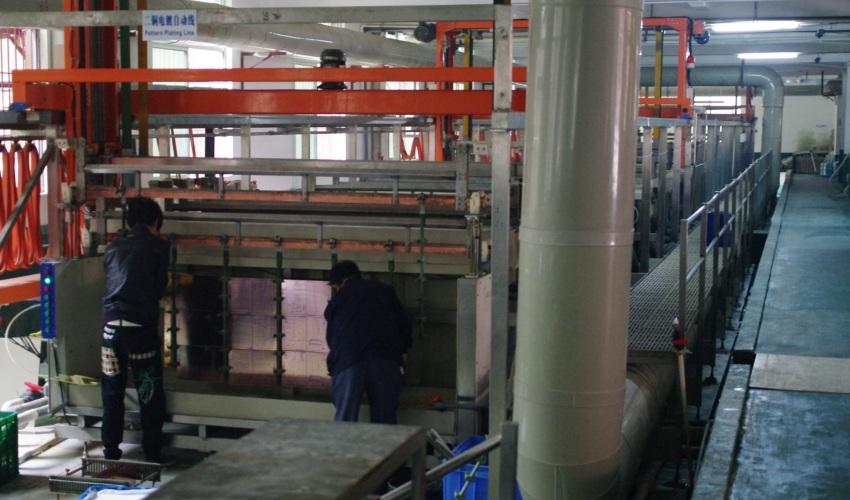
Oberflächenmodifikation durch Eloxieren
Eloxal ist die Abkürzung für “elektrolytische Oxidation von Aluminium”. Schon die Bezeichnung deutet darauf hin, dass sich ausschließlich Aluminium eloxieren lässt.
Das Leichtmetall hat die Eigenschaft, unter Einwirkung von Sauerstoff eine dünne, aber dichte Oxidschicht auszubilden, die seine Oberfläche vor weiterer Oxidation und in einem gewissen Maß auch vor Korrosion schützt. Kommen Substanzen wie Salz (Natriumchlorid) und Schwefeldioxid ins Spiel, stößt die natürliche Schutzschicht an ihre Grenzen. Zudem ist sie nicht in der Lage, das Aluminium vor Verschleiß zu bewahren.
Durch Eloxieren lässt sich die oberste Aluminiumschicht gezielt verstärken. Dabei bildet sich eine fast porenfreie dielektrische Sperrschicht aus, über der sich eine wabenförmige feinporige Deckschicht befindet. Während die natürliche Schicht nur wenige Nanometer stark ist, lassen sich mit dem Eloxal-Verfahren Schichtdicken von bis zu 25 Mikrometern erzielen. Dadurch wird es möglich, Bauteile aus Aluminium auch unter rauen Industriebedingungen und in Meeresnähe einzusetzen. Die Beschaffenheit der Deckschicht ermöglicht es außerdem, das Aluminium beim Eloxieren beliebig einzufärben. Dafür eignen sich am besten Reinaluminiumwerkstoffe mit einem Magnesiumgehalt von maximal 4 %.
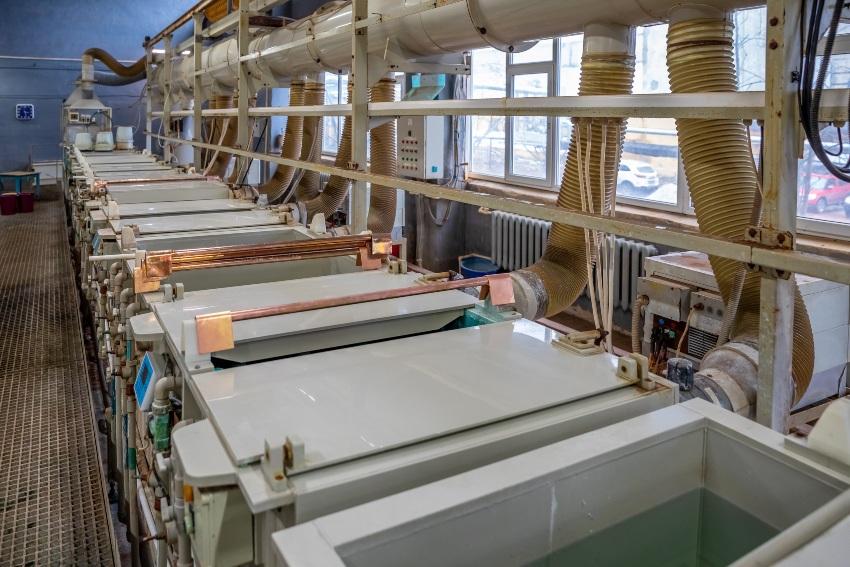
Verfahrensablauf beim Galvanisieren
Abhängig von der Werkstückgröße und den jeweiligen Anforderungen können verschiedene Techniken des Galvanisierens zur Anwendung kommen. Sind die Bauteile beispielsweise so groß, dass eine Behandlung in der Elektronenwanne nicht möglich ist, können das Tauchbadgalvanisieren oder das Tampongalvanisieren Verwendung finden. Bei Letzterem wird der Elektrolyt unter Spannung mithilfe eines Schwammes aufgetragen.
Darüber hinaus existieren folgende Verfahren:
- Trommelgalvanisieren,
- chemisches Galvanisieren,
- Bandgalvanisieren,
Das Prinzip der Galvanisierung ist einfach. Grob lässt es sich in drei Schritte einteilen.
1. Vorbehandlung
Durch verschiedene mechanische und chemische Verfahren werden Fette und Öle, Rost und Zunder sowie Späne und Schleifstaub aus vorherigen Bearbeitungsschritten von der Werkstückoberfläche entfernt. Abgeschlossen wird die Vorbehandlung durch mehrere Spülvorgänge, die eine absolut saubere Oberfläche gewährleisten.
2. Beschichten
Das Werkstück wird in eine Elektrolytlösung auf Basis des aufzutragenden Metalls eingebracht. Es ist an eine Gleichspannungsquelle angeschlossen und dient als Kathode. Den Gegenpol bildet die aus dem Beschichtungsmaterial bestehende Anode. Wird Strom angelegt, lösen sich positive Metallionen von der Anode und lagern sich auf dem Werkstück ab. Je länger sich der Gegenstand im elektrolytischen Bad befindet und je höher die Stromstärke ist, desto ausgeprägter wird die Beschichtung.
3. Nachbehandlung
Nach dem Galvanisieren wird das Werkstück zumindest gespült und getrocknet. Manchmal umfasst die Nachbehandlung auch das Passivieren oder Chromatieren (z. B. bei galvanisch verzinktem Stahl).
Verfahrensablauf beim Eloxieren
Anders als beim Galvanisieren wird beim Eloxieren keine Schutzschicht aufgetragen. Stattdessen findet eine Umwandlung der obersten Aluminiumschicht statt. Das dafür erforderliche Eloxal-Verfahren lässt sich in vier Schritte einteilen, wobei das Einfärben als optional anzusehen ist. Ist keine Farbveränderung erwünscht, kann dieser Vorgang entfallen.
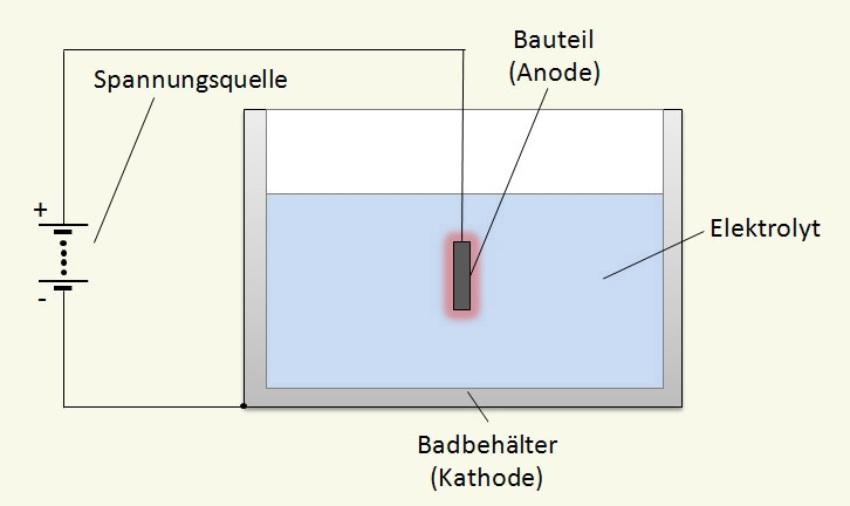
1. Vorbehandlung
Wie beim Galvanisieren dient dieser Schritt der Schaffung einer fett- und staubfreien Oberfläche. Werden an das Werkstück hohe optische Ansprüche gestellt, kann eine chemische Vorbehandlung erforderlich sein. Bei dieser werden durch vorangegangene Arbeitsschritte hervorgerufene Unebenheiten in der Oberfläche durch Beizen geglättet.
2. Anodische Oxidation
Die Aluminiumteile werden in ein Elektrolyt (Schwefel- oder Oxalsäure) eingetaucht. In diesem Fall ist das Werkstück als Anode mit dem Pluspol der Gleichstromquelle verbunden. Als Kathode finden häufig Blei- oder Titanplatten Verwendung, die der Elektrolyt nicht angreift. Fließt Strom, wird an der Kathode Wasser elektrolytisch zersetzt.
Der Wasserstoff entweicht an der Kathode. Der Sauerstoff reagiert mit dem Aluminium, wodurch sich die Oxidschicht ausbildet. Je länger der Vorgang andauert, desto weiter wächst die Schutzschicht in das Aluminium hinein. Dabei bilden sich kapillarähnliche Poren.
3. Einfärben (optional)
Die bei der anodischen Oxidation erzeugten Poren können Farbstoffe aufnehmen. Da die Farbwirkung nicht auf der Oberfläche entsteht, sondern am Porengrund, sind die Farben äußerst abriebfest und langlebig.
4. Versiegeln
Nach dem Aluminium Eloxieren werden die noch offenen Poren versiegelt beziehungsweise verdichtet. Das geschieht durch einfaches Kochen in vollentsalztem Wasser. Hierbei reagiert das Aluminiumoxid mit dem Wasser zu Aluminium-Oxid-Hydroxid. Außerdem führt die Wasseraufnahme zum Aufquellen der Poren vom Rand zur Mitte hin. Dadurch verengt sich der Porenhals und wird letztlich geschlossen.
Vor- und Nachteile beim Galvanisieren
Beim Galvanisieren handelt es sich um ein kostengünstiges Verfahren, das umfangreiche Beschichtungsmöglichkeiten bietet. Das Werkstück erhält durch die Galvanotechnik einen guten Korrosionsschutz und wird zugleich optisch aufgewertet.
Nachteilig bei der Galvanik sind vor allem die dabei entstehenden Fällungsschlämme. Diese bestehen aus konzentrierten Chemikalien, die nach dem Galvanisieren im Elektrolyten zurückbleiben. Wird das Verfahren nicht ordnungsgemäß durchgeführt, kann schädlicher Abfall in die Umwelt gelangen. Deshalb ist eine korrekte Abfallentsorgung unverzichtbar.
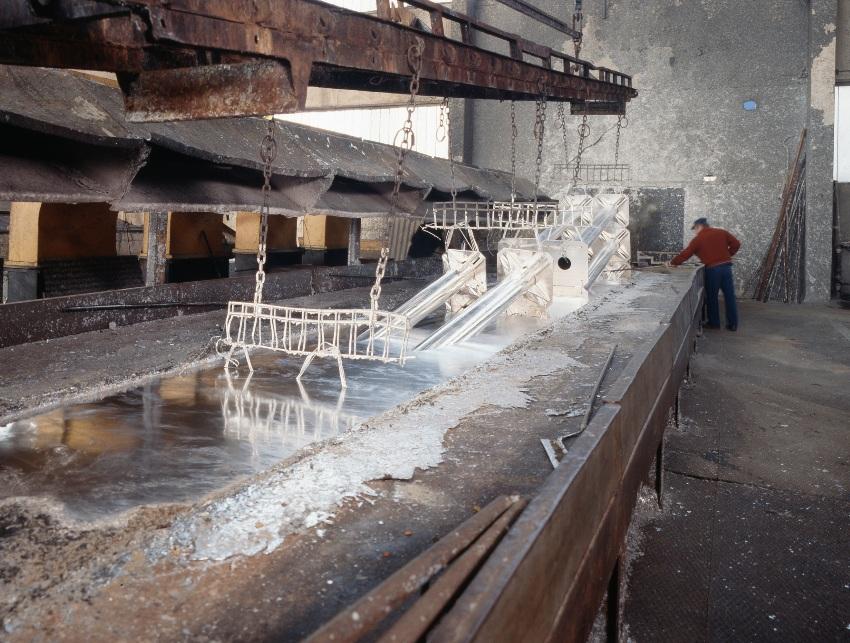
Vor- und Nachteile beim Eloxal-Verfahren
Wie beim Galvanisieren wird auch beim Eloxieren eine haltbarere, korrosionsfestere Oberflächenstruktur erzeugt. Eloxiertes Aluminium kann Härten von 200 bis 400 HV aufweisen. Mittels Harteloxieren lassen sich sogar Härten von bis zu 600 HV erzeugen. Dabei bietet das Eloxal-Verfahren gleichzeitig den Vorteil, dass das Werkstück zugleich eingefärbt werden kann. Der größte Nachteil besteht darin, dass das Eloxieren ausschließlich für Bauteile aus Aluminium einsetzbar ist.
Da die beim Eloxieren entstehende Schutzschicht nicht leitend ist, kann eloxiertes Aluminium nicht ohne Weiteres erneut anodisch oxidiert werden. Hierzu muss zunächst die Eloxal-Schicht durch Beizen wieder entfernt werden, um das eigentliche Aluminium freizulegen. Dieser Schritt kann dazu führen, dass bei Bauteilen mit wichtigen Passungen die Maße nach dem Eloxieren nicht mehr den Vorgaben entsprechen.