« Why Heat Resistance Is a Critical Property in Surface Technology »
In many industrial facilities, the surfaces of reactors, furnaces, and chemical plants must endure high temperatures and frequent thermal cycling. Lubricants used during machining face similar demands, where they reduce friction and protect materials from heat damage. In both cases, high-performance products with proven heat resistance are essential for reliable operation.
Coatings Protect A Variety Surfaces from Extreme Heat…
Engines, chemical plants, reactors, and (high-temperature) furnaces all use structural and component parts that must withstand tough conditions. High temperature swings can be part of everyday operations. Untreated materials like steel or metal alloys cannot always handle these extremes. When exposed to harsh conditions, materials can suffer from fatigue, develop cracks on the surface, or corrode. Such surface damage can lead to critical failures in chemical plants. A heat-resistant coating that can withstand temperatures above 1800 °F (1000 °C) provides reliable thermal protection and helps prevent further material fatigue.
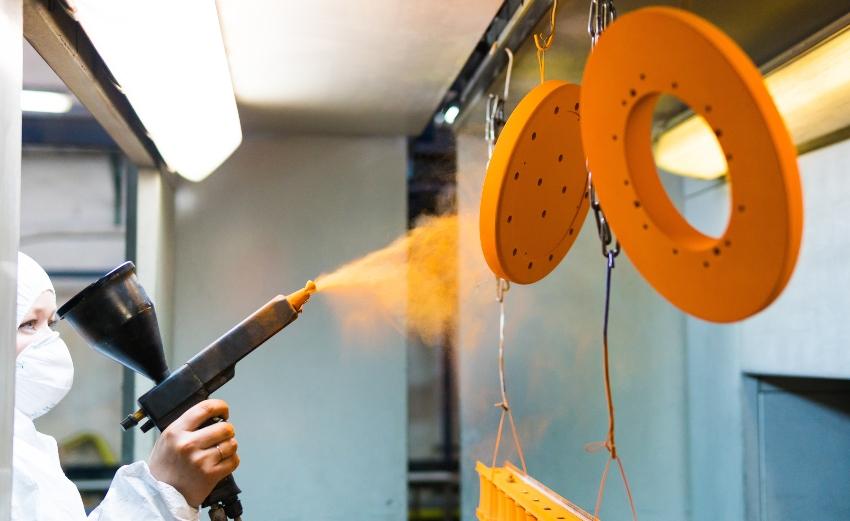
Heat-Resistant Coatings Offer More than Just Thermal Protection
A thermal coating must withstand elevated temperatures. This temperature range can span from a moderate 400 °F (200 °C) up to extreme conditions exceeding 1800 °F (1000 °C). Achieving long-term stability under these conditions requires advanced surface technology and the precise selection of the right product. In many industrial processes, a component faces not only high heat but also mechanical stress. While reactors or pipes may not see much mechanical load, engines and pumps certainly do. Sophisticated coating systems can provide both heat resistance and protection against mechanical stress. This directly affects material fatigue and the lifespan of components and entire systems: fatigue is reduced while the durability of parts and equipment increases.
Preventing Corrosion Susceptibility
Multiple coatings provide not only excellent temperature resistance but also built-in corrosion protection. A thermal coating adds a protective layer that prevents corrosion of the base material. In the end, high heat resistance also means a component may not require as much active cooling. Economically, this improves efficiency; ecologically, it saves energy otherwise needed for cooling. Considering the surface coating of critical parts right from the start can lead to long-term savings and boost both efficiency and effectiveness of industrial processes. A wide variety of coating systems are available for surface treatment.
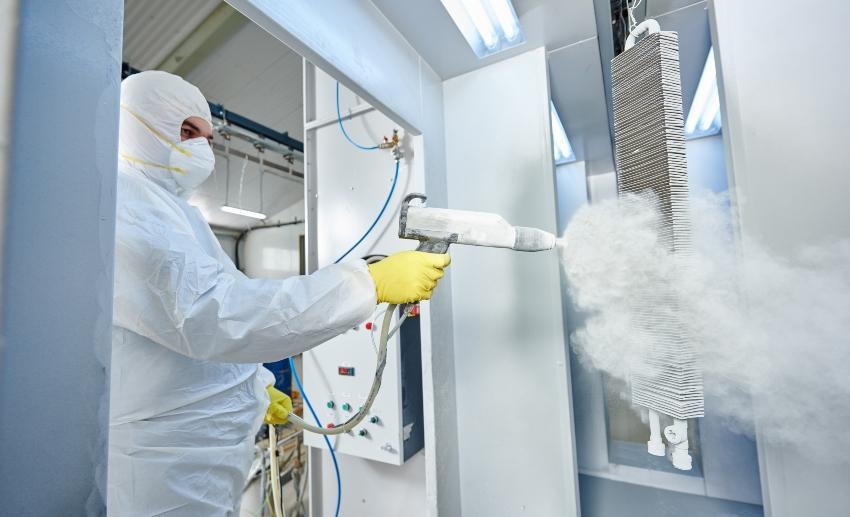
Heat-Resistant Coatings Vary in Temperature Limits and Chemical Composition
In surface technology, different coatings and techniques can be used for surface treatment. It is not just about the heat resistance range — it is important to consider whether a material will be exposed to constant temperatures or frequent fluctuations. Other requirements, like corrosion protection, must be considered as well. . The worst-case scenario would be damaging the coating and the material underneath, which must be avoided. That is why it is important to plan the process and materials in advance. Selecting the right system at this stage ensures reliable performance under the plant’s specific thermal and environmental conditions.
Silicone Resins — A Widely Used, High-Temperature Solution
Most silicone resins provide adequate protection up to about 660 °F (350 °C). For more extreme conditions, phenyl silicone resin coatings can handle peak temperatures of up to about 1300 °F (700 °C) for short periods. The base of silicone resin coatings is high-molecular polysiloxanes, which create a dense, highly crosslinked film with minimal volume change during curing. Besides high heat resistance, silicone resins offer good weatherability and minimal yellowing. They can be tinted with pigments like titanium dioxide or carbon black.
Metal Coatings — A Surface Technique for Special Applications
Finely dispersed metal powder is used in thermal spraying. Here, the chosen metal is melted in a fuel gas-oxygen flame. A spray gun atomizes the molten metal using compressed air or nitrogen, propelling tiny metal droplets onto the surface. The workpiece surface itself has not melted. This surface technique provides both corrosion protection and heat resistance up to about 750 °F (400 °C). It is widely used for equipment in onshore and offshore environments.
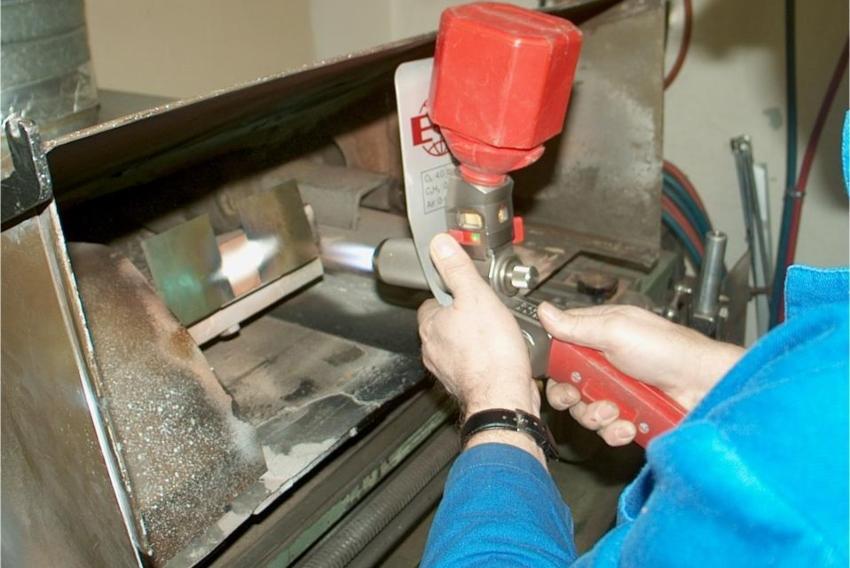
Powder Coating — Corrosion Protection in A Myriad of Colors
Powder coating is a surface treatment similar to metal coating but uses powder paints instead of metal droplets. Based on polyester or epoxy resins combined with binders, additives, fillers, and pigments, the powder is sprayed onto an electrically conductive metal. The particles are electrostatically charged, adhere to the surface, and form a coating. Powder coatings offer medium to high heat resistance, usually between about 400 °F and 930 °F (200–500 °C). Like metal coating, powder coating combines heat resistance with corrosion protection. Powder coatings are common for oven panels, industrial piping, and outdoor equipment that must endure both high temperature and weather exposure.
Ceramic Materials for Engines and Turbines
When extreme heat resistance is required — for example, for manifolds and exhaust systems in automotive applications or for components in engines and turbines — ceramic materials are used. These include ceramic coatings made from aluminum oxide, chromium oxide reinforced with titanium, or zirconium oxide stabilized with yttrium. These advanced ceramics also offer exceptional hardness, outstanding chemical and corrosion resistance, and excellent wear protection. They can be applied to metal, fiberglass, or carbon surfaces using thermal spraying. In plasma spraying — a high-tech surface treatment method — flame temperatures reach up to about 36,000 °F (20,000 °C). At this temperature, the molten ceramic is propelled onto the metal part, forming a sealed layer.
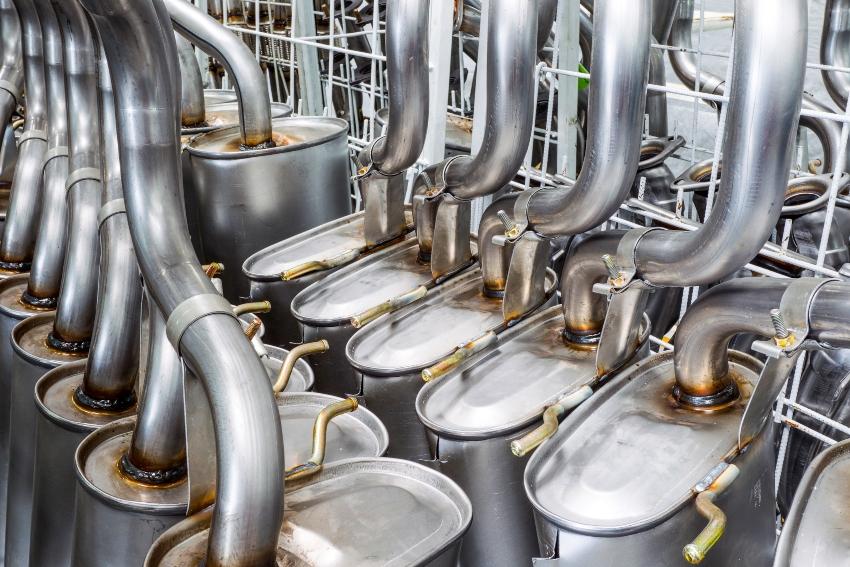
Lubricants in Manufacturing — High-Tech Products Keep Production Running
It is not only surfaces that need to handle high temperatures; excess thermal energy must also be removed during processing. Virtually every process generates friction — and friction means rising temperatures. For example, rubbing your hands together generates warmth through friction — the same principle applies at a larger scale in industrial processes. Much more thermal output is produced in industrial processes — during tooling, when operating rollers or bearings, or anywhere metal contacts metal or plastic. To reduce friction and heat buildup, lubricants have always been used. Depending on the process, these are liquid oils or greases.
Base oils can be mineral-based, composed of various hydrocarbons, or synthetic, such as polyol esters. Typical greases are formulated from a base oil (usually longer-chain hydrocarbons like paraffins), combined with a thickener to give the grease its structure, and additives. Common thickeners include metal soaps, while additives help prevent corrosion or oxidation.
With all lubricants and greases, the goal is not only to lubricate but also to cool. Depending on the process, one function may be more important than the other. When heat removal is the main focus, special cutting fluids known as cooling lubricants are used in surface processing. These fluids remove heat from the machining zone as quickly as possible. Water-based cutting fluids are especially effective in this role.