« Effective Methods at a Glance »
Have you ever accidentally snagged yourself on an overhanging piece of metal? Sharp edges, splinters, or burrs on parts made from wood, plastic, or metal not only compromise aesthetics but can also lead to injuries or hinder further processing. In technical terms, these unwanted formations are referred to as burrs , and in many processes, the formation of burrs is unavoidable. How can metal be deburred to prevent further negative effects?
Burred or Burr-Free?
In metalworking, various methods are used, some of which inevitably create burrs. A burr is technically defined as an unwanted projection of the material, that forms on the surface of a workpiece when the material is displaced, or edges are created. These protrusions extend beyond the workpiece and are therefore undesirable. Burrs commonly occur in primary shaping processes such as metal casting, sintering, or electroforming. They are also unavoidable in pressure-forming methods such as rolling or die forging. Cutting and separation processes like shearing, grinding, or planing, as well as joining processes like welding or casting, also produce burrs.
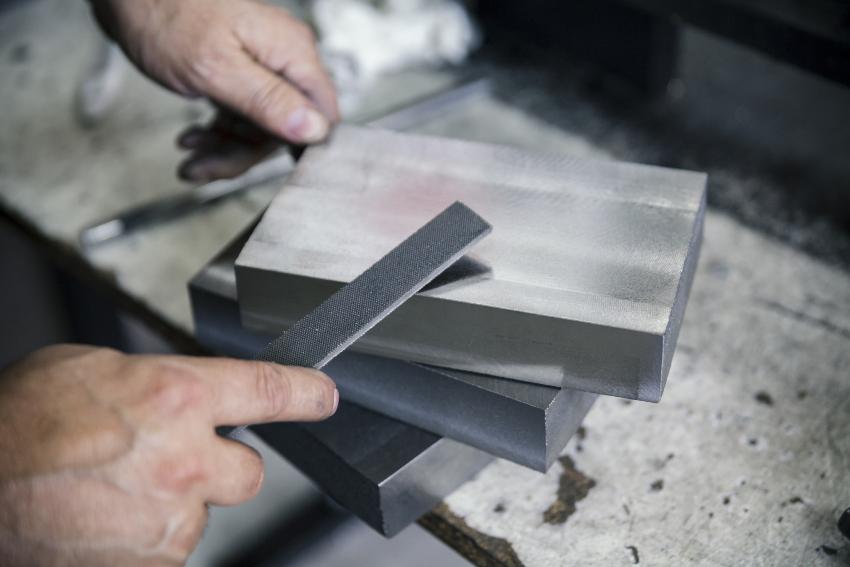
Various Deburring Methods
Deburring methods ensure the safety, functionality, and aesthetic quality of the workpiece. Numerous approaches exist for deburring metal parts. These include mechanical, chemical, and thermal deburring methods.
Mechanical methods include brushing, where technical brushes, often round brushes, rotate along the edges to remove burrs. There are various types of brushes, including disc brushes, cup brushes, conical brushes, and internal brushes, each suited to specific applications. A process similar to brushing is grinding which can also be used for deburring, employing methods such as vibratory grinding or flow grinding. These processes can be manual or fully automated. For smaller parts, vibratory grinding is particularly effective, using abrasive media made of ceramic, plastic, metal (such as steel or bronze), or natural materials like walnut shell granules to remove unwanted burrs.
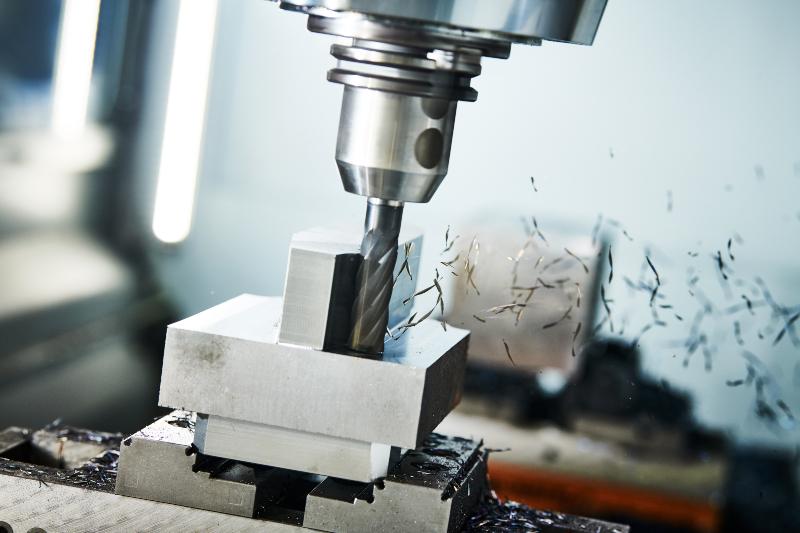
Within vibratory grinding, techniques such as barrel finishing, vibratory finishing, or drag grinding are differentiated . In barrel finishing, workpieces, abrasive media, and additives are placed in a barrel that rotates or oscillates, a process which removes burrs through relative motion. A simple manual method for deburring is filing, which uses different file types for various applications. Other mechanical options include milling, countersinking, or other machining processes.
Burrs can also be removed chemically or electrochemically. Chemical deburring immerses workpieces in corrosive or etching solutions to remove edges. Electrochemical deburring uses electrolysis and is particularly suitable for extremely hard metals. In this process, the workpiece acts as an anode, and the tool as a cathode, with material removed through an electrolyte solution, typically an aqueous solution of sodium chloride or sodium nitrate.
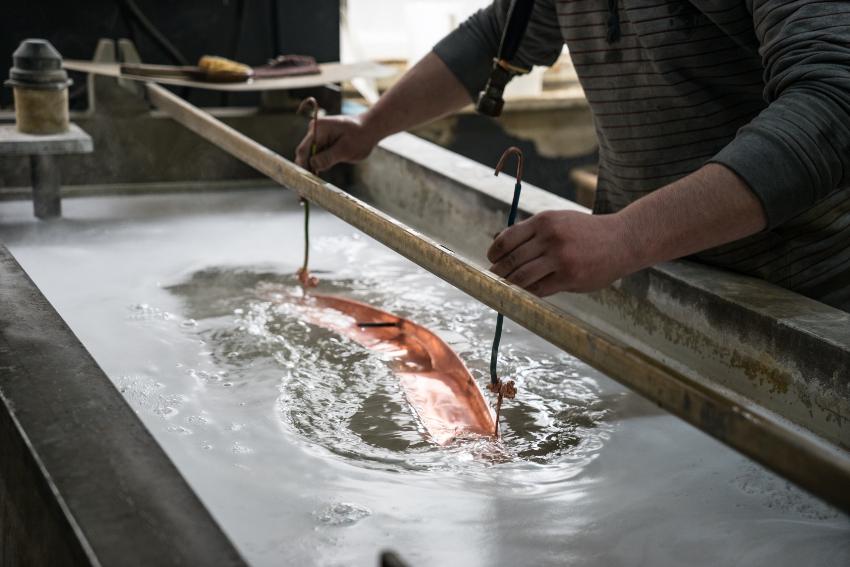
Thermal deburring is another option available, which uses a gas mixture of oxygen, hydrogen, natural gas, or methane ignited in a deburring chamber. This produces remarkably high temperatures, whereby excess oxygen burns off the protruding edges. This method is ideal for thin burrs and can access hard-to-reach areas.
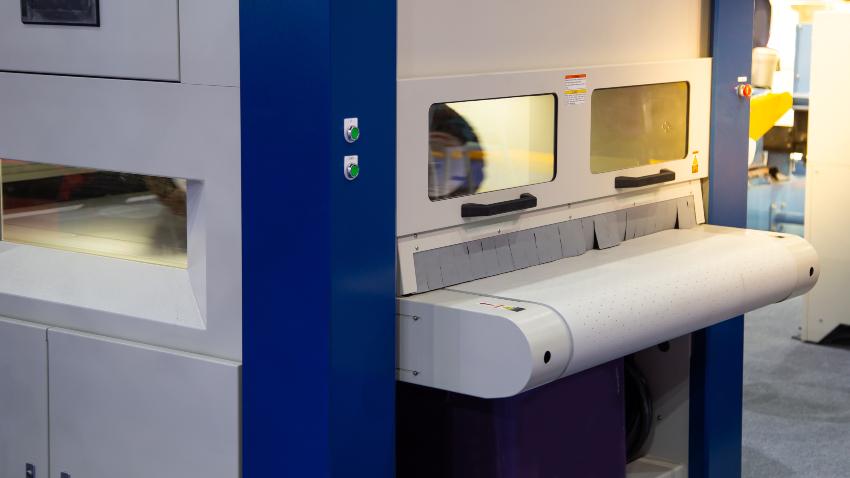
Multiple Deburring Methods Available
Just as there are diverse metalworking methods, there are equally varied deburring techniques. Often, multiple processes are combined to achieve the desired result. Automation has also significantly advanced in this field, making procedures more economical and efficient. Deburring is crucial for subsequent processes, not only to prevent tool wear and ensure worker safety but also to create a solid foundation for other treatments. For example, a rounded edge allows for uniform coating, which results in long-term corrosion prevention.
What’s Next for the Future?
As in many industrial fields, automation continues to revolutionize the deburring processes, with robotic systems increasingly used as standalone or in subsequent process steps. This makes the entire metalworking process chain even more efficient.
Additionally, existing technologies are being refined, and new methods are continually introduced. One such evolving method is laser-based deburring, which is applicable to both glass and metal. This technique melts the metal’s surface layer using absorbed laser radiation. Laser deburring smooths roughness, precisely rounds edges, and even heals micro-defects.
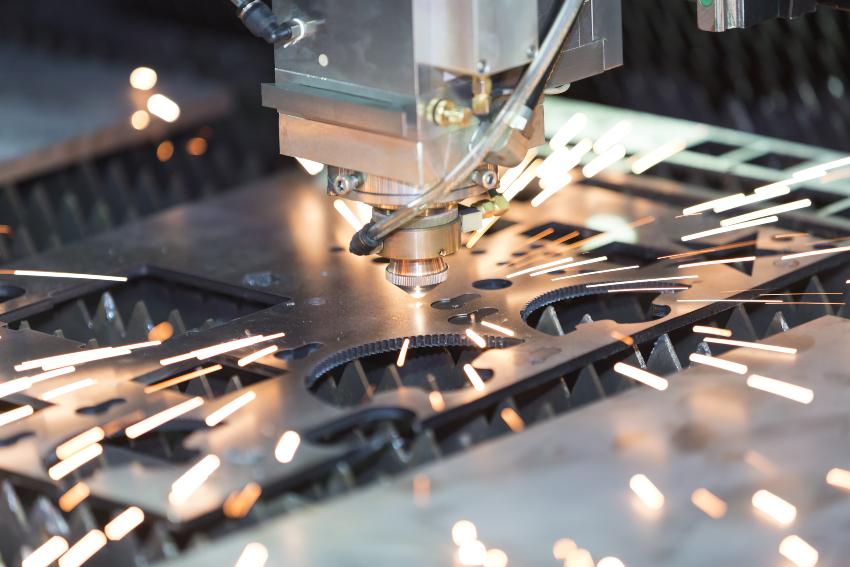
Finally, high-pressure water jet deburring is worth mentioning. Under high pressure, water is directed at the workpiece through rotating multi-nozzle heads or single jets. The output of intense kinetic energy deforms and subsequently breaks off the burr, as it cannot withstand the impact force.