Electroplating is a process in which electric current causes metals to deposit uniformly on the surface of workpieces. The metallic layer primarily serves to protect against corrosion, resist mechanical wear, or improve electrical conductivity. Additionally, electroplating may aim to achieve decorative purposes or facilitate the further processing of the base material. This article will provide more detail on how the process works.
Direct Current Sources and Different Metals
The term “electroplating” and related concepts trace back to Luigi Galvani, an 18th-century Italian scientist. He is known for pioneering experiments in bioelectricity, such as observing the effects of electric current on a frog’s leg. In his experiment, Galvani unknowingly created a circuit by connecting two different metallic elements with the frog’s tissue, leading to muscle contractions.
Initially, differences in voltage between conductive materials were used to generate direct current in batteries. Early batteries contained materials such as copper, zinc, and sulfuric acid. These devices produced current as the zinc gradually dissolved. Once the zinc was depleted, the battery was no longer functional.
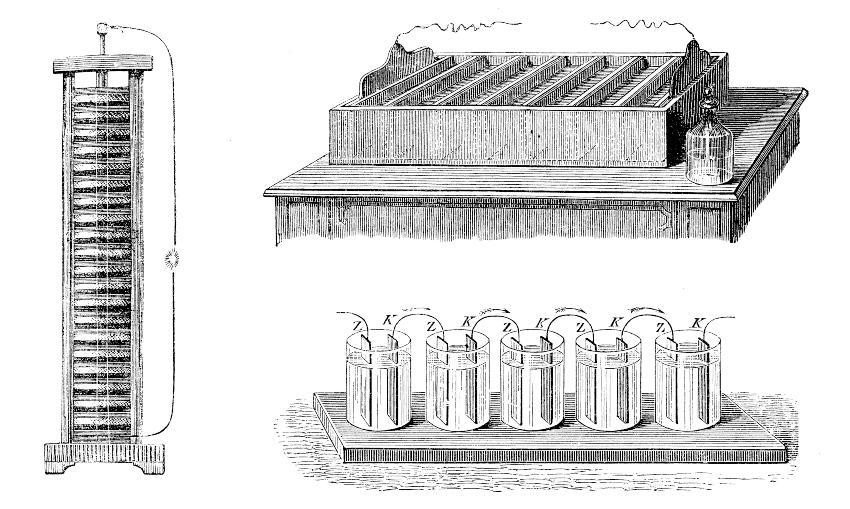
Electroplated Metal Deposition
Electroplating uses the reverse of this process. A direct current source is included in a closed circuit that runs through a conductive liquid. Outside the liquid, electrons move from the negative pole (cathode) to the positive pole (anode) of the power source. When the electrons reach the liquid, they initiate electroplating electrochemical reactions.
At the cathode (where electrons enter the liquid), positively charged ions are attracted. These ions capture electrons and become solid metallic elements, depositing on the cathode’s surface. This disrupts the balance between positively charged ions and negatively charged ions in the liquid, causing the negative ions to move toward the anode. There, they release electrons that flow back to the power source, completing the circuit.
The conductive liquid facilitating these reactions is called the electrolyte. The specific composition of the cathode, anode, and electrolyte determines the type of reactions and the resulting metal deposition.
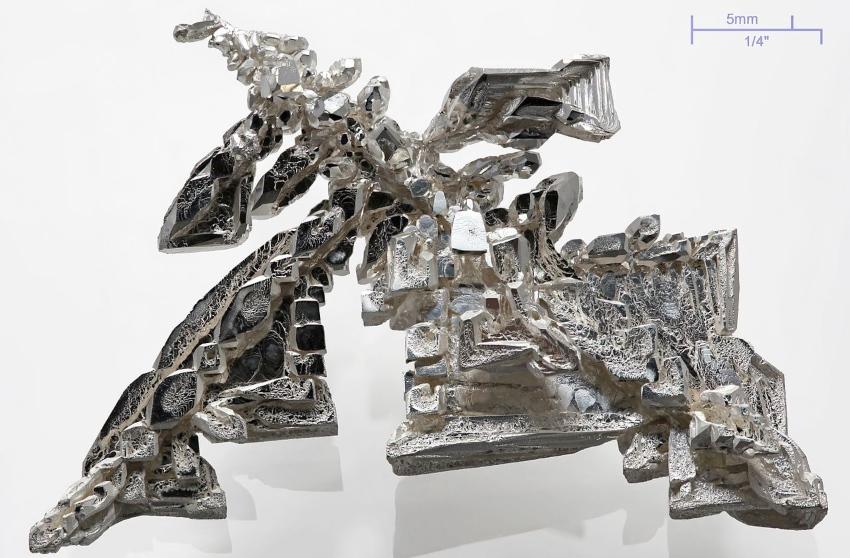
Anodic Oxidation
Electroplating also encompasses chemical processes, such as anodic oxidation, which is widely used to create protective layers on aluminum (commonly known as anodizing). Sulfuric acid typically serves as the electrolyte, with aluminum acting as the anode. The externally applied current releases oxygen at the anode, which reacts with the base material to form a protective oxide layer. This layer uniformly coats the underlying material, preventing oxygen and moisture from reaching the surface, thus providing corrosion resistance.
Metal Refinement Without an External Power Source
Certain metallic elements can be plated without external electricity. By immersing a less noble metal into an electrolyte containing dissolved salts of a more noble metal, eletroplating electrochemical reactions cause the less noble material to dissolve and the noble metal to deposit on the workpiece. The reaction stops once the surface is completely coated.
This process is also utilized for active corrosion protection. For example, zinc is applied to steel for galvanization, or sacrificial anodes are used on ship hulls to absorb corrosive factors, sparing the underlying material.
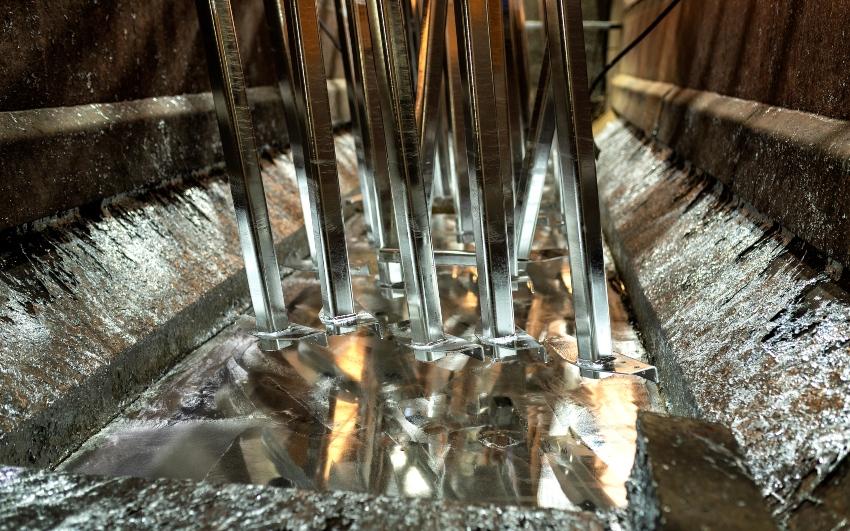
Practical Application of Electroplating
Pre and Post-Treatment
Electroplating requires meticulous preparation of surfaces for optimal results. Surfaces must be free of impurities to ensure durable coatings. Less noble coatings (e.g., zinc) often require post-treatment to create protective conversion layers (e.g., phosphating or chromating). These pre- and post-treatment steps are also common in other surface technologies.
When electroplating non-conductive materials such as plastics or glass, their surfaces must first be made conductive. This can be achieved through metal-containing lacquers, thin chemically deposited metal layers, or seeding with metal particles.
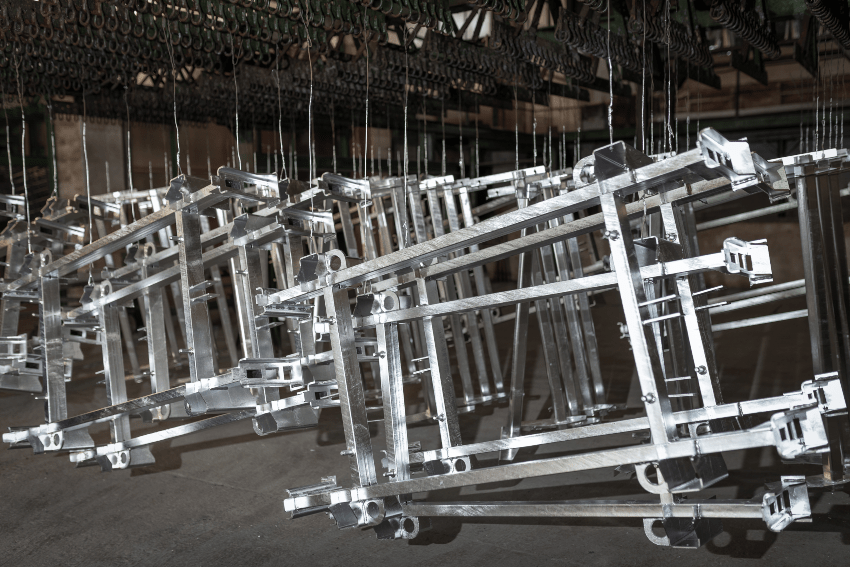
Electroplating with Consumable Anodes
The size of the workpieces determines the design of the plating system. Large components are immersed in baths, where an electrically conductive connection to the power source’s negative pole makes them the cathode. The anode, usually composed of the metal to be deposited, dissolves as the process continues. The electrolyte contains salts of the anode material, enabling a continuous supply of ions. Proper bath maintenance allows the process to continue until the anode is depleted. This method is commonly used for plating with silver, gold, copper, and zinc.
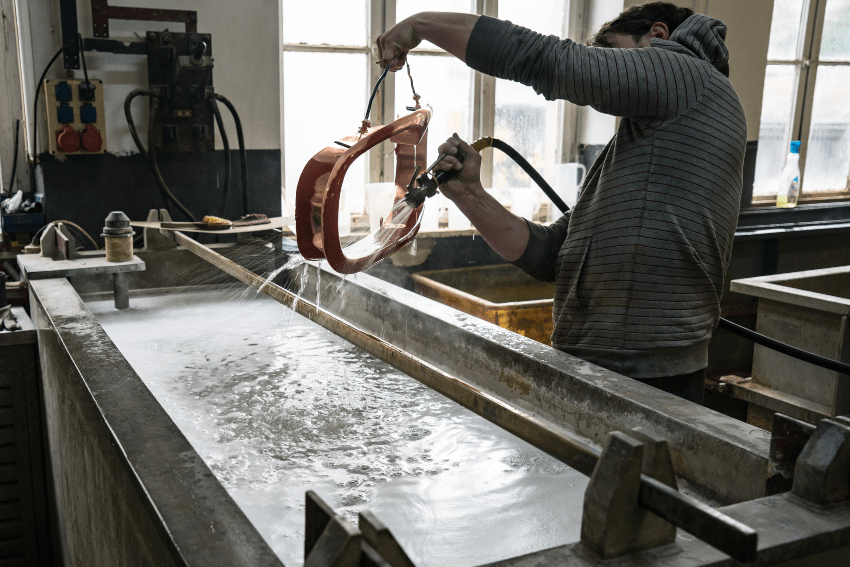
Electroplating with Stable Anodes
In chrome plating, only the electrolyte contains the required metal ions, while oxygen is released at the anode. This method requires strict monitoring and regular replenishment of chromium salts to maintain bath consistency.
Electroplating in Drums or Bell
Small parts are electroplated in rotating or perforated drums or bell-shaped containers. These containers, connected to the power source’s negative pole, move within the electrolyte bath, or allow the electrolyte to circulate through them.
Factors Influencing Surface Coating
The strength of the current determines how many electrons are available at the cathode and removed at the anode. Current strength depends on the applied voltage and the electrolyte’s conductivity. Higher current and prolonged exposure increase the thickness of the metal layer.
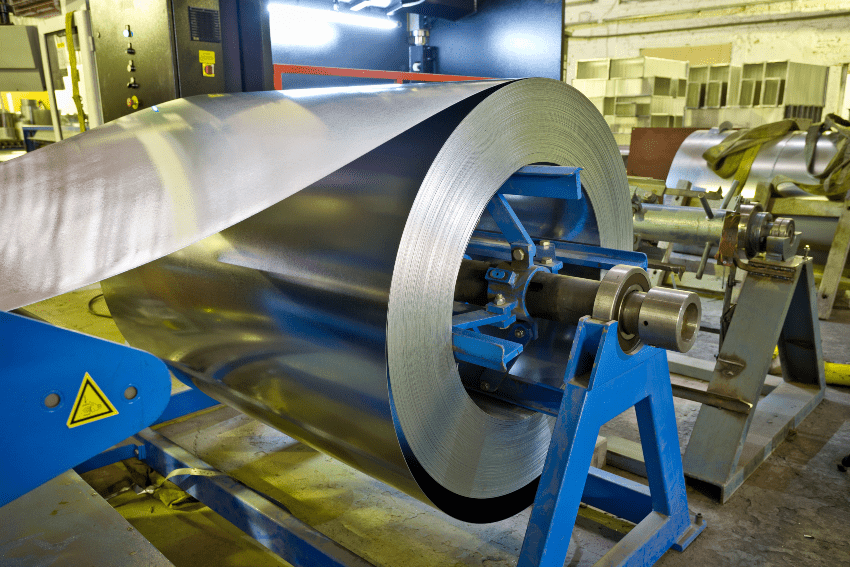
Coating quality depends on the electrolyte’s composition and temperature. Additives such as brighteners, wetting agents, pH stabilizers, and other substances fine-tune the layer’s properties. Contaminants, including impurities or ions released from the workpieces, can disrupt the process. Using deionized water for the electrolyte solution and regular bath monitoring are crucial for proper coating formation.