Chromates, which are chemical salts derived from chromic acid, play a role in two distinct surface treatment processes: Chromating, where chromic acid or its salts create a chromate layer on a material’s surface. Chromium plating, where dissolved chromates (electrolytes containing chromium) deposit chromium onto a material’s surface using electric current. Both processes have proven effective in wear and corrosion protection. However, chromic acid and its water-soluble salts are toxic and carcinogenic, leading to strict restrictions on their use. Today, most applications have shifted to chromate-free conversion processes where possible.
Overview: Chromium, Chromium (III), Chromium (VI), Chromic Acid, Chromates, and Chromium Salts
Many sources fail to clarify these terms, therefore, this section provides a concise explanation.
Chromium
Chromium is a corrosion-resistant, hard, silver-gray metal classified as a transition metal. Its chemical behavior depends on the reaction conditions, forming various oxides like CrO, Cr₂O₃, and CrO₃ when reacting with oxygen.
Valence of Chemical Elements
In chemistry, each element in a compound is assigned a valence, which indicates its positive or negative charge and determines the ratio in which elements combine. Oxygen always has a valence of -2, while chromium’s valence varies in its oxides: +2, +3, or +6. The sum of all valences in a compound is zero.
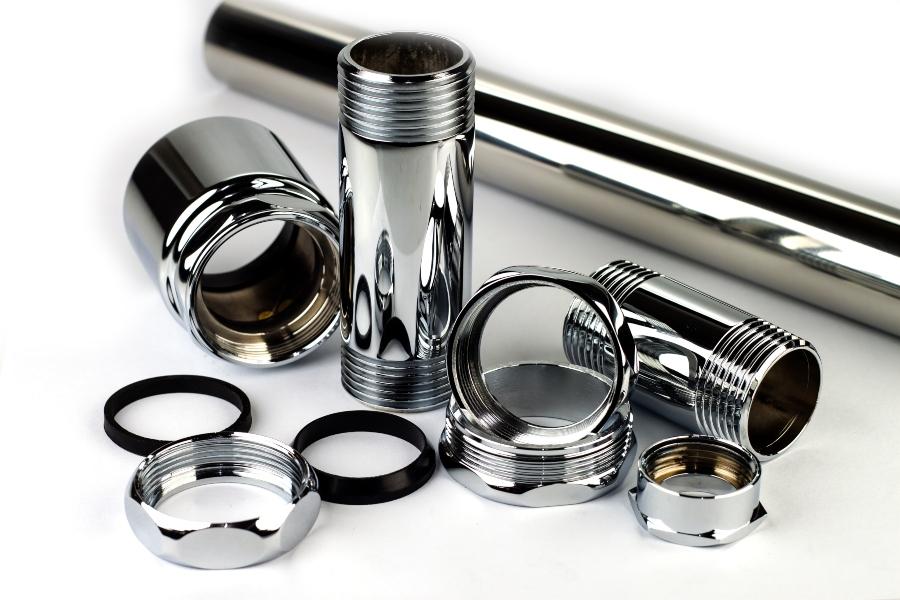
Chromium (III) and Chromium (VI)
Chromium (III) refers to trivalent chromium (+3 valence), which forms stable and relatively safe compounds. Chromium (VI) refers to hexavalent chromium (+6 valence), which is highly toxic and carcinogenic in its dissolved state. Chromium (II) compounds are unstable and quickly convert to other substances.
Chromic Acid, Chromates, and Other Chromium Salts
Chromic acid (H₂CrO₄) is essentially a water solution of chromium trioxide (CrO₃). When this solution comes into contact with metals, chromates are formed.
Chromating
Chromating involves using mixtures of chromic acid and additives to create chromate systems. These react with metals to form stable, complex chromate compounds. This process produces a thin, corrosion-resistant layer that adheres to the material’s surface. The term “conversion process” refers to this chemical transformation, giving rise to “conversion layers.”
Applications for chromating
Chromating involves using mixtures of chromic acid and additives to create chromate systems. These react with metals to form stable, complex chromate compounds. This process produces a thin, corrosion-resistant layer that adheres to the material’s surface. The term “conversion process” refers to this chemical transformation, giving rise to “conversion layers.”
Chromating is widely used to protect aluminum, zinc, and galvanized steel components from corrosion. It can also treat magnesium, copper, silver, and cadmium. In addition to corrosion resistance, chromate layers provide excellent adhesion for subsequent painting. These layers typically appear yellow, leading to the term “yellow chromating.”
Bans on Chromium (VI) Usage
Chromic acid and chromates are classified as Substances of Very High Concern (SVHCs) under the EU’s REACH Regulation (Registration, Evaluation, Authorization, and Restriction of Chemicals, Regulation EC No 1907/2006). Their use is now heavily restricted, with limited exceptions.
Exceptions to the Chromium (VI) Ban
Surface treatments involving chromium (VI) are still permitted in cases where high corrosion protection is required, such as in aerospace applications or for fasteners exposed to harsh chemical environments.
Chromate-Free Systems
In many cases, chromium (III) salts based on phosphoric acid serve as substitutes for chromates. These processes, often called “green chromating,” create olive-green layers and operate similarly to traditional chromating. Kluthe has developed DECORRDAL ZN 320 and DECORRDAL AL 325, which use alternative chromium (III) salts to provide comparable corrosion protection and paint adhesion on zinc and aluminum surfaces.
Chromium-Free Systems
For surfaces used as a base for wet or powder coatings, chromium compounds can often be entirely avoided. For example, Kluthe’s DECORRDAL AL 230 A and DECORRDAL AL 240 A use zirconium, titanium, and polymer-based systems, providing excellent adhesion and corrosion resistance. These systems have passed rigorous testing and are approved for use in GSB- and Qualicoat-certified surface treatment processes for powder coatings.
Applications of Chromium Plating
The ban on chromium (VI) presents challenges for electroplaters, as its coatings are highly valued for their superior wear and corrosion resistance. Hard chrome coatings withstand mechanical stress in components like hydraulic cylinders, piston rods, and shock absorbers. By preventing oxygen from reaching the base material, these coatings mitigate oxidation and corrosion. For optimal results, surfaces are often nickel- or copper-plated before chrome plating.
Additional applications include decorative bright chrome plating and black chrome plating, which produces deep black, conductive layers.
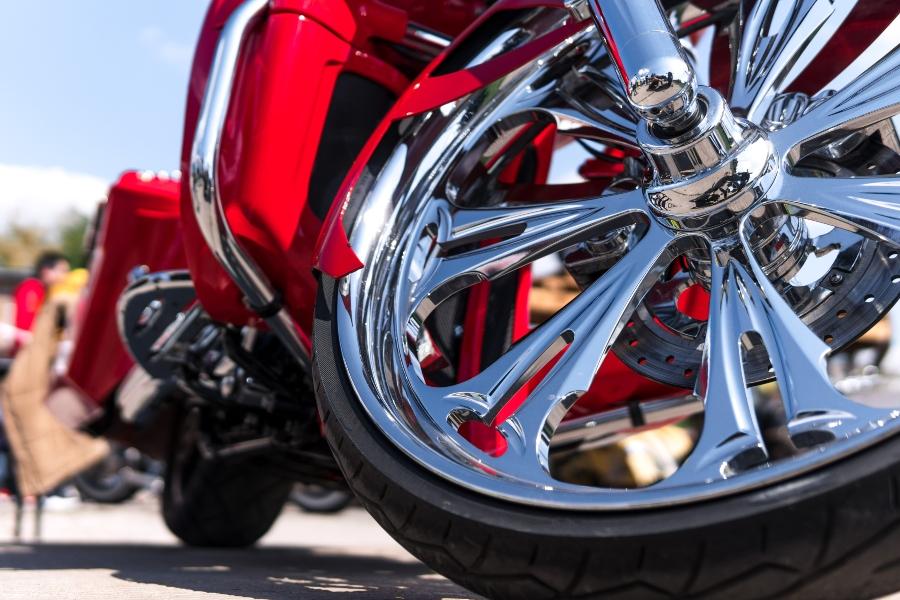
Chromium (III)-sulfate-based electrolytes are an alternative to chromium (VI), but achieving comparable properties often requires specialized additives to optimize performance. Research into optimizing chromium-free systems for electroplating continues to offer significant opportunities for innovation.