« What problems arise from insufficient oil-water separation? »
Puddles shimmering with gasoline like a rainbow—what might seem intriguing can quickly become expensive. When oil and water are not properly separated, the mixture can enter the sewage system, and thereby cause harm to the environment in a number of ways. Discover how oil separators help reduce hydrocarbon levels to meet legal discharge thresholds and protect both the environment and your operations.
Generation of Oily Wastewater
The primary sources that produce oily wastewater are gas stations, car washes, and auto repair shops. Here, problems can arise if mineral oils are dispersed and washed into the sewage system along with precipitation. Floor drains in such facilities must therefore be equipped with light liquid separators—devices designed to separate lighter-than-water hydrocarbons like oil and fuel—allowing clean water to flow out.
Larger volumes of oily wastewater are produced during the cleaning stages in surface treatment processes. Before chemicals are used for surface coating, residues from previous steps—primarily cooling lubricants and temporary corrosion protection agents—must be removed from surfaces. In many manufacturing processes, compressed air is used for control tasks or to blow off chips and cooling lubricant residues from finished parts. Compressors that supply this compressed air continuously generate oily condensate. The water content comes from air humidity, while the oil originates from machine lubrication, creating a problematic combination.
Emulsions as a Special Case of Oily Wastewater
Mineral oils are insoluble in water. Therefore, mixtures of these substances usually separate into an oily and a watery phase. Oil droplets merge and rise to the liquid surface. In these cases, oil separation occurs in a separator or skimmer. However, emulsions behave differently, as the oil droplets remain dispersed in the liquid. This dispersion is often caused by very high pressures in high-pressure cleaners or compressors, which mechanically break up the oil droplets so finely that they cannot coalesce.
Often, emulsifiers are responsible for emulsion formation. These consist of molecules with water-attracting and oil-attracting groups, binding water, and oil molecules together. This principle underpins the effectiveness of water-miscible cooling lubricants—cooling fluids that can mix with water—and many cleaning agents. For proper separation, or in conjunction with it, emulsion breaking is necessary. Demulsifiers release the oil droplets, allowing them to rise to the surface. Other options for this process include using coalescence separators, centrifuges, or water-repellent materials that absorb oils.
Oil Separation in Surface Treatment Systems
Surface treatment systems are suitable for water recirculation in washing processes. In connected wastewater treatment systems, oils and impurities are removed. The efficiency and profitability of these systems improve with higher separation rates. If oil separation is insufficient, impurities Would be reintroduced into the washing process, or the residue for disposal will contain excessive water content.
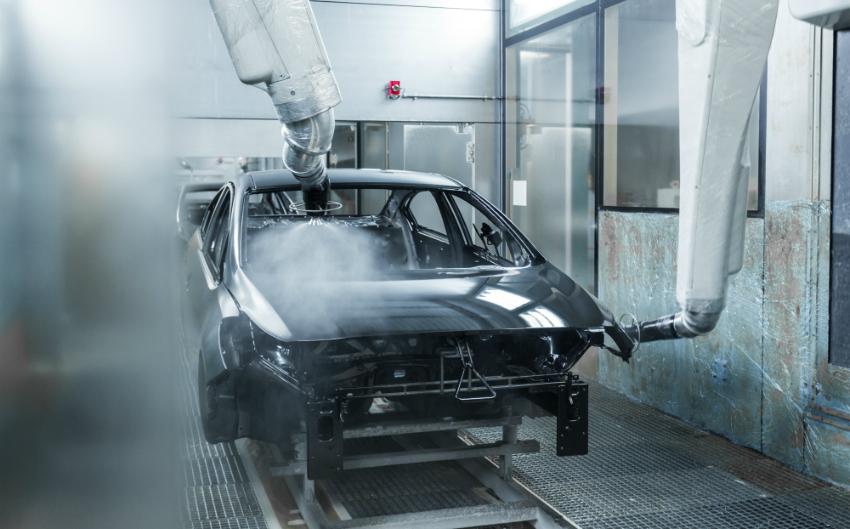
Removing foreign oils is a significant way to extend the lifespan of water-miscible cooling lubricants. Slideway oils or hydraulic fluids that enter the cooling lubricant during metalworking accumulate on the surface and block air exchange in the collection tank. When work pauses over the weekend, anaerobic microorganisms quickly multiply under these conditions. The cooling lubricant “spoils” and must be entirely replaced.
Light Liquid Separators
Light liquid separators are used to separate oil from water that contains environmentally hazardous substances before discharge into the sewer. These substances include mineral oils, lubricants, heating oil, diesel, and gasoline, which can be released during vehicle refueling, washing, or repair. The construction and operation of light liquid separators are subject to extensive legal requirements and technical standards, which vary by location. The suitability of these systems must be proven through a certification process. The systems consist of a sludge trap (a compartment to collect solid waste materials), an oil separator, and a sampling chamber. The size of the sludge trap and separator depends on the area to be drained. The separator must have a warning device to signal when its maximum volume is reached. Additionally, an automatic shut-off device is required to prevent overflow if the separator exceeds its capacity.
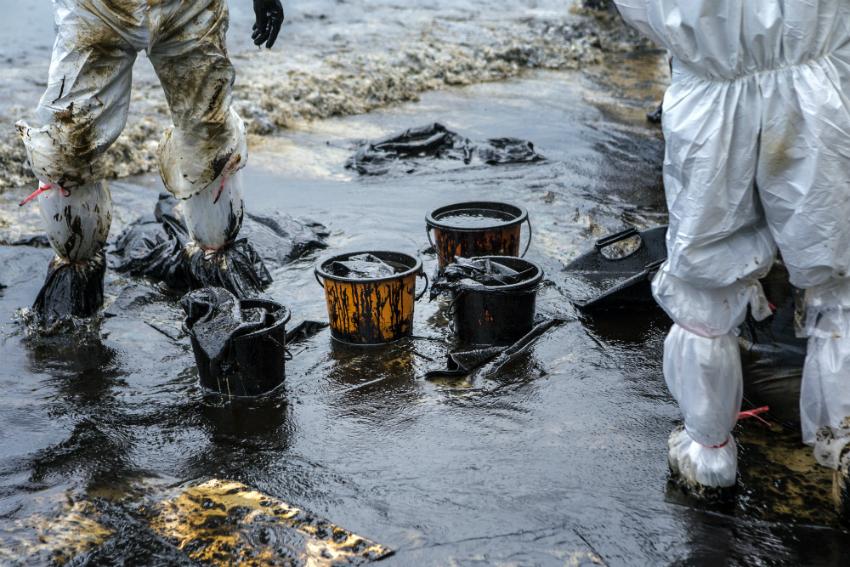
Weekly inspections by an expert are legally mandated, depending on local regulations. These inspections include checking the functionality of the warning and shut-off devices and measuring the accumulated sludge and oil levels. The results are recorded in maintenance records. Maintenance is required every six months, involving cleaning, and emptying the separator, with these activities also documented in the records. A general inspection, including a leak test of the entire oil separation system, is mandatory every five years.
Disposal of Compressor Condensates
In lubricated compressors, condensate from air humidity forms during compressed air generation. This condensate, due to its oil content, cannot be discharged into the sewer. Most compressor manufacturers provide oil separation units tailored to their compressors’ capacity. In these compact devices, oil binds to activated carbon or other materials, while filters remove dust and other impurities from the air.
Conclusion on Oil Separation
Proper oil separation enables water recirculation in surface treatment processes, conserving resources and reducing costs. Water consumption and waste volumes decrease significantly, and bath lifespans are extended as contaminants are continuously removed.
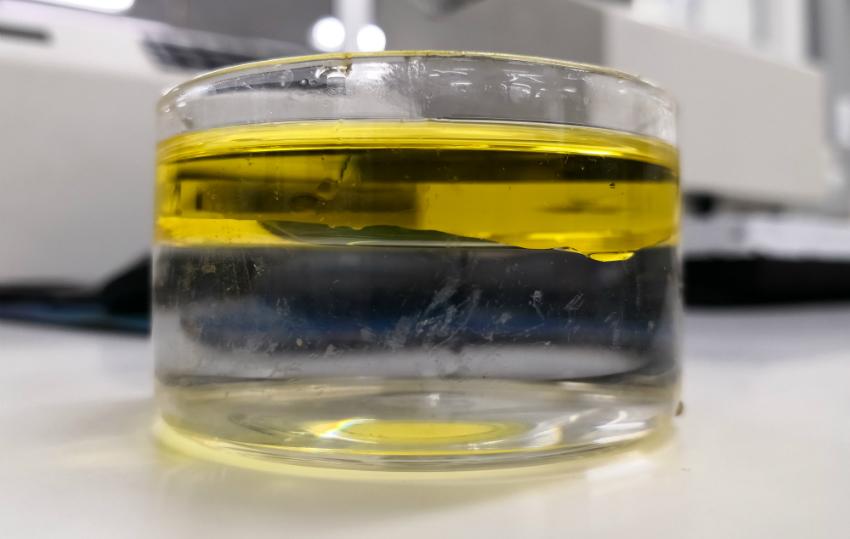
In metalworking, oil separation from water-miscible cooling lubricants reduces downtime caused by frequent emulsion changes. Discharging untreated wastewater into the sewer is prohibited. Therefore, facilities like gas stations and repair shops that handle environmentally hazardous mineral oils must have separation systems installed.