« A Brief Overview of the process »
Anodizing is a process that provides aluminum semi-finished products (partially processed materials) or workpieces with a corrosion-resistant and wear-resistant surface. This protective layer is formed with the aid of an electric current and includes components from the base material. During this process, the surface metal reacts with oxygen to form a durable layer of aluminum oxide in the near-surface area. This gives rise to the term “anodizing,” which is derived from the word anode, referencing the positive electrode used in the electrochemical process.
Why Anodize Aluminum?
Aluminum and its alloys are some of the most important construction materials. Its high strength and particularly its light weight make it crucial for use in manufacturing vehicles, airplanes, household items, and in construction. American aerospace companies like Boeing rely on anodized aluminum for aircraft components, while Apple uses it for their MacBooks and iPhones manufactured in the U.S. The architectural landmarks across American cities often feature anodized aluminum for both functionality and aesthetics. Aluminum surfaces quickly develop a very thin oxide layer when exposed to air, which protects the material from corrosion.
However, this layer is susceptible to mechanical wear and various chemicals. The anodizing process, sometimes referred to as the anodizing method, creates an artificial oxide layer that offers enhanced wear and corrosion protection.
How Does the Anodizing Process Work?
Like many surface technology processes, anodizing involves several steps, depending on the desired optical, chemical, and physical properties of the layer. If the material surfaces need to be particularly smooth, preparatory steps such as grinding or polishing are performed first.
Surface Pretreatment
For proper layer formation, it is essential that the surfaces are clean and free from fats and oils. The natural oxide layer also needs to be removed before the actual process can begin. Surface pretreatment includes degreasing, pickling (chemical removal of surface oxides), and de-smutting (removal of residues). Degreasing is done with hot steam, hot water, and if needed, alkaline cleaning agents.
During pickling, alkaline solutions dissolve the natural oxide layer. Since the alkaline residues from the pickle would interfere with layer formation, they must be neutralized and rinsed off. This step is known as de-smutting. Thorough rinsing with deionized water after each step ensures a quality-controlled process.
Anodizing through Anodic Oxidation
To anodize aluminum, it is securely attached to the positive pole of a DC power source and submerged in an acid bath. The container wall or an acid-resistant component in the bath is connected to the negative pole of the power source. When the power is turned on, the aluminum part or semi-finished product becomes the anode. At the surface of the anode, the material combines with oxygen to form aluminum oxide, creating a protective layer. Meanwhile, the container wall or the component connected to the negative pole (the cathode) facilitates a chemical reaction that produces gaseous hydrogen.
Process Parameters in the Anodizing Method
The anodizing process is conducted at temperatures between 59 and 68 °F. The applied voltage ranges from 14 to 20 volts. In the bath, a current density of 1.5 A/dm² (approximately 14 A/ft²) is established, at which the layer thickness increases by up to 3 µm/min. Depending on the exposure time, protective layers 10 to 25 µm (0.0004 to 0.001 inches) thick are created. A special case is hard anodizing, which produces a highly wear-resistant corrosion protection with layers measuring 25 to 250 µm (0.001 to 0.01 inches) thick. This technique is especially important for American military applications and in the U.S. automotive industry, where companies like Ford and GM use hard-anodized components in engines for superior wear resistance. These layer thicknesses can be achieved at temperatures below 50 °F with an electrical voltage over 40 V and current densities of 2 to 3 A/dm² (approximately 19 to 28 A/ft²).
Post-Treatment by Coloring and Sealing the Layer
The protective layer has a porous structure. Moisture and aggressive substances could penetrate these pores to the base material and cause corrosion damage. Therefore, the protective layer must be sealed in a final step. The pores can also absorb dye. If the surface is to be colored for decorative purposes, the porous layer lends itself well to dyeing. This is typically done immediately following anodizing by dipping in a dye bath or electrolytically.
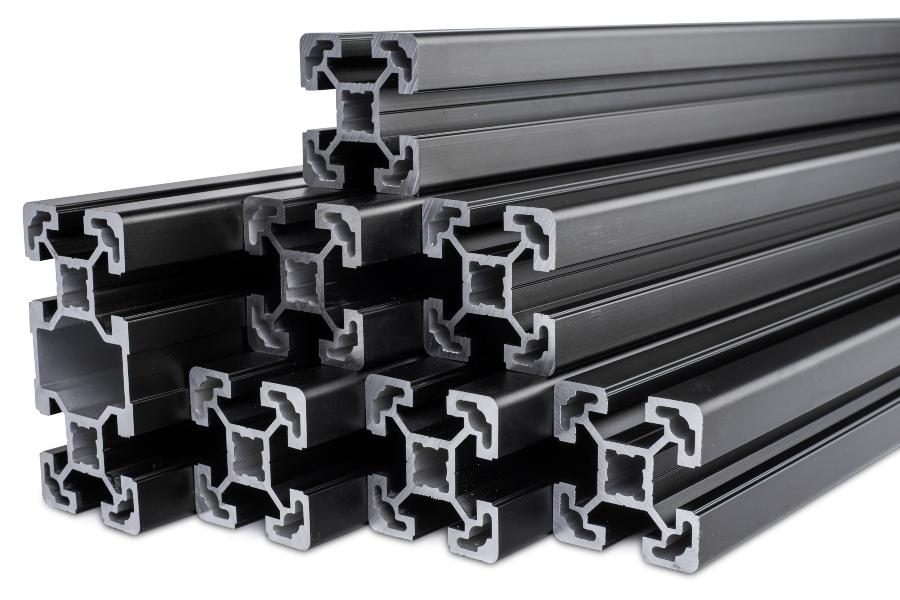
The anodizing method concludes with the sealing process. The anodized metal is boiled in deionized water or treated with hot steam. At temperatures between 194 and 212 °F, the aluminum oxide in the pores reacts with water to form aluminum oxide-hydroxide. This substance constricts and closes the pores. and itis a naturally occurring mineral known as boehmite (a form of aluminum oxide hydroxide).
What Happens During Anodic Oxidation on the Material Surface?
Oxidation is a chemical process in which electrons are released from the atomic shell. The opposite process is reduction, where electrons are absorbed into the atomic shell. The anodizing process relies on the fact that water, under the influence of direct current, breaks down into negatively charged hydroxide ions (oxygen and hydrogen, OH-) and positively charged hydronium ions (water and hydrogen, H3O+).
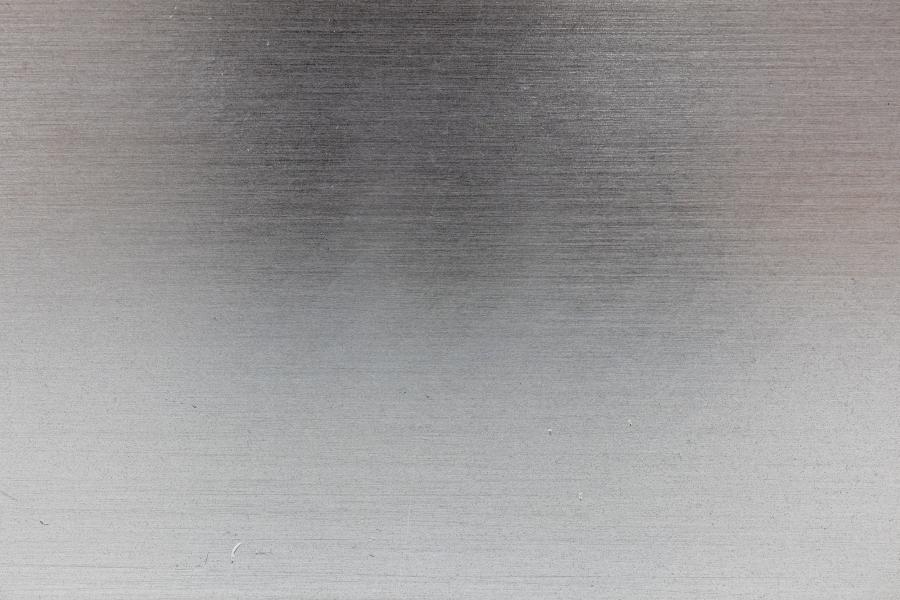
While ions at the cathode absorb electrons and form gaseous hydrogen, the metal of the anode reacts with the oxygen from the hydronium ions to form metal oxide and water. The released electrons flow to the positive pole of the power source. The acid in the electrolyte bath (conductive solution) is not involved in the reaction. It only serves to enhance conductivity and enable sufficient current density in the bath.
Layer Formation in the Anodizing Process
The anodic oxidation of aluminum, anodizing, initially produces a very thin layer of aluminum oxide on the surface of the workpiece. This layer acts as an insulator. If it were not for occasional voltage breakdowns, the current flow would be interrupted.
Where the current flows, small “channels” remain in the layer. These are the pores that must ultimately be sealed.
Characteristics of the Anodized Layer
Layers created by the anodizing process have good adhesion, high electrical resistance, high hardness, and good corrosion resistance in neutral liquids (pH 5 to 8). The layers are also non-toxic, allowing anodized aluminum devices to be used in the food industry. This is why American cookware manufacturers like All-Clad and Calphalon use anodized aluminum for their premium products. In the sporting goods industry, companies like Louisville Slugger incorporate anodized aluminum in their baseball bats for durability and performance. The high hardness contributes to good wear resistance.
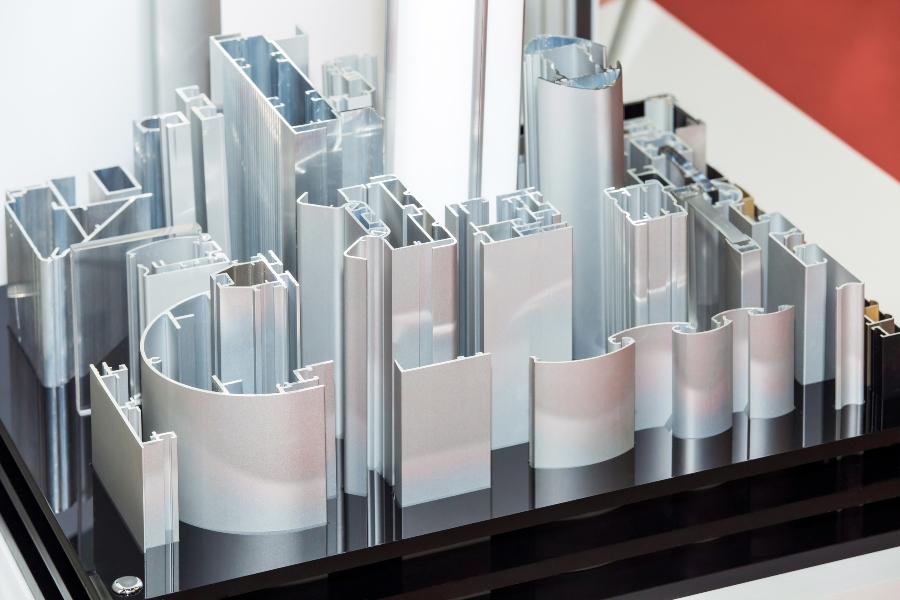