Decarburization refers to the reduction of carbon content in molten or solidified alloys. This process commonly occurs during the production and processing of steel but can also affect cast iron when exposed to elevated temperatures. This article explains the role carbon plays in metal alloys, when it is intentionally removed, and under what conditions it escapes unintentionally.
Decarburization in Steel Production
In nature, iron is always found in combination with oxygen as iron oxide. To extract the iron, this bond must be broken. The required chemical reaction is called reduction. The most common reducing agent is elemental C. At elevated temperatures, this element bonds with the oxygen in the iron oxide to form CO2. From the reducing agent’s perspective, this is an oxidation reaction. The overall process is known as a redox reaction. To fully reduce the oxide, an excess of the reducing agent is required. This results in an alloy containing this element, which increases the strength of naturally soft iron.
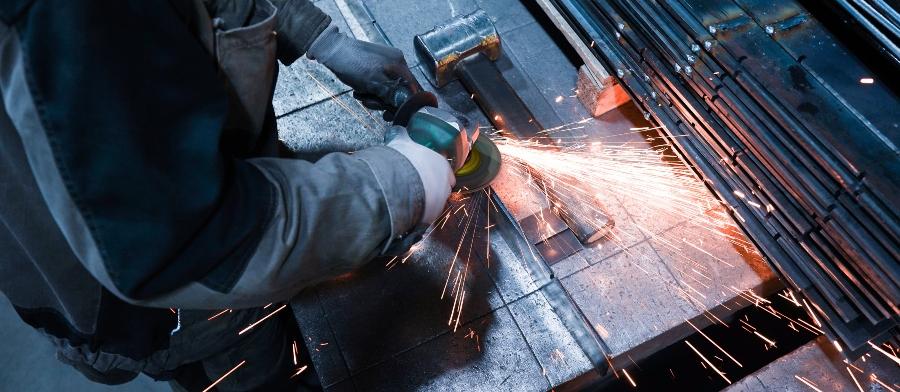
However, as the content of this element increases, the material becomes more brittle. Decarburization allows adjustment of this content. This adjustment creates steel with the right balance of strength and toughness for its intended use. This is achieved by blowing air through the molten metal, causing the excess to burn off, this process is known as refining. Steel with a content of this element up to 2.06% can be forged and rolled, which is the defining characteristic of steel. Alloys with higher content are classified as cast iron.
Decarburization in Semi-Finished and Finished Components
The mechanical properties of steel depend not only on the amount of this element but also on how it is distributed within the microstructure. This structure forms as the molten metal cools. Once the melting point is reached, individual crystals begin to solidify, and more atoms attach to them. These crystals grow until they meet each other, forming a grain structure. The cooling rate determines whether carbon atoms are incorporated into the crystals or settle at the grain boundaries. When steel is further processed into semi-finished parts, forming processes apply mechanical force and heat. This process alters the microstructure.
To achieve the desired properties for a given application, semi-finished and finished parts are often heat-treated. During hot forming or heat treatment, unintentional decarburization of the surface layer can occur. This happens as carbon atoms migrate to the surface under elevated temperatures.
This migration is due to a concentration difference between the material and the surrounding air. The movement of atoms caused by such gradients is called diffusion.
At the surface, the element reacts with oxygen from the air to form carbon dioxide. This can result in complete removal of the element from surface areas. This condition is known as complete decarburization. If only a reduction in carbon content occurs, the process is referred to as partial decarburization.
Effects of Unintended Decarburization
Decarburization reduces the strength of the material near the surface. In finished parts subjected to bending or stress, this can quickly lead to cracking or structural failure. The resulting damage may necessitate costly repairs and create significant safety hazards. A further effect occurs with wear and corrosion protection.
Many parts are provided with coatings in subsequent surface technology processes that protect against corrosion and wear. These coatings may lose their adhesion due to reduced carbon levels, weakened surface strength, or the formation of cracks. This can cause them to peel or flake off. To avoid expensive consequences, it is important to check whether heat-treated or hot-formed parts have experienced decarburization before applying any surface coatings.
Measuring the Depth of Decarburization
The depth of the affected surface layer is referred to as the decarburization depth. Determining this value is often necessary for quality assurance or failure analysis. The measurement is done using metallographic methods.
For this, sample sections are cut and polished. Etching reveals the microstructure when examined under a microscope. Decarburized areas appear much lighter than the carbon-rich base material and can be clearly measured.
Preventive Measures
During hot forming, suitable forming lubricants can reduce exposure to air and help prevent decarburization. In surface technology, there are lubricants designed to create dense, tough, and tightly adhering films. Alternatively, designers can plan for machining allowances. These allowances help remove the decarburized surface layer during finishing processes like grinding or milling.
Decarburization During Operation of Machine Components
Decarburization can also take place during service, especially in machine components made of steel that are exposed to high temperatures. In such cases, surface coatings can help prevent carbon loss, by shielding the material from direct contact with air.