Conversion means transformation. A conversion coating, by definition, is simply a transformed layer. But what exactly is being transformed—and how? Let us take a closer look.
What Exactly Is a Conversion Coating?
In surface treatment, a conversion coating refers to an extremely thin layer that is formed on the surface of metals through a chemical or electrochemical reaction. During this conversion process, either metal ions from the surface react with the treatment solution, or inorganic compounds deposit onto the metal surface. These layers form a strong bond with the underlying metal. This process is a critical step in surface pretreatment because it enhances paint adhesion and provides effective corrosion protection.
Common methods to create conversion coatings include iron phosphate, zinc phosphate, and tri-cation phosphate treatments. More recent techniques use titanium or zirconium fluorides, often combined with specialty polymers, to achieve optimal paint adhesion. These methods have replaced hexavalent chromium (Cr(VI)) compounds, which were commonly used in the past but are now banned due to their toxicity and high health risk. In contrast, treatments using trivalent chromium (Cr(III)) compounds are still considered safe and approved for use.
How Are Conversion Coatings Created?
The type of conversion coating used depends largely on the metal being treated. Common substrates include steel, aluminum, and magnesium, which are often coated before painting or powder coating. Several surface treatment techniques are available, with the most prominent being phosphating—further classified into iron, zinc, and tri-cation phosphating. Other methods include passivation and anodic oxidation.
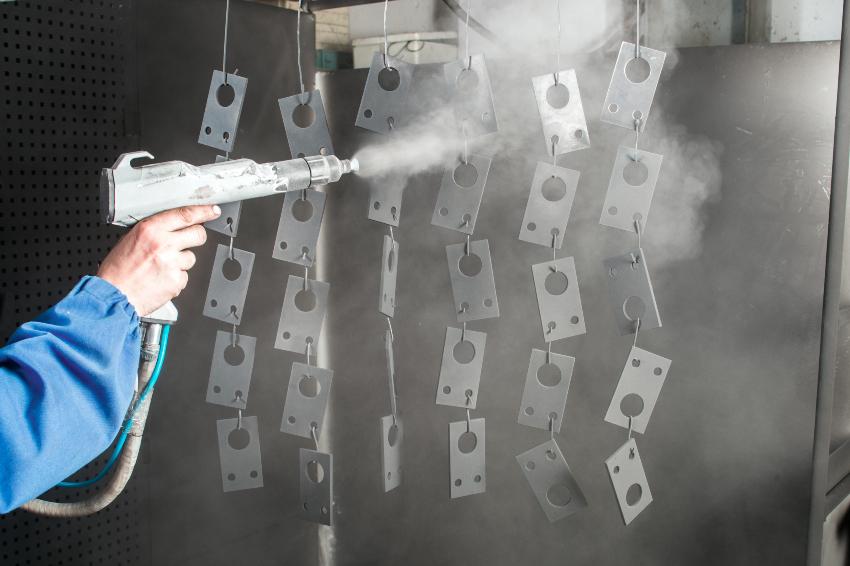
Iron Phosphate Coating (Alkaline or Phosphating)
Iron phosphation is primarily used on iron or steel surfaces but can also be applied to zinc or aluminum alloys. A series of chemical reactions form the conversion layer on the surface. The acidic phosphating bath dissolves ions from the metal surface, which then react with alkaline phosphates in the solution to create various insoluble phosphates. These deposits form a layer composed of oxides, hydroxides, and phosphates—resulting in an amorphous mixture.
The typical thickness of layers formed by this process ranges from 0.15 µm to 0.8 µm (roughly 0.000006 to 0.00003 inches). Because of their amorphous structure, the treated surfaces can show varying colors, including yellow, blue-iridescent, golden, or gray tones. Such phosphate layers are mostly used on painted metal parts intended for indoor use. They are not suitable for environments exposed to heavy weather or moisture. Since the treatment relies on ions derived from the base metal itself, it is known as a “self-generated” or “metal-inherent” conversion layer.
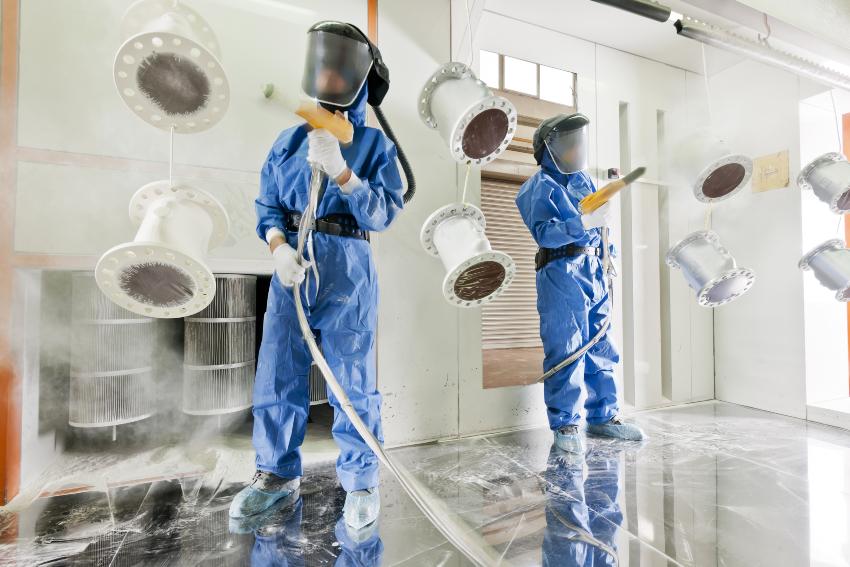
How Zinc Phosphate Coatings Work — and Why They Are More Protective
Unlike iron phosphating, zinc phosphate layers form through the reaction of zinc and other metal ions in the treatment solution with phosphate anions, resulting in what is called a ‘foreign’ or non-inherent layer. The treatment bath typically includes primary zinc phosphate, phosphoric acid, and chemical accelerators such as chlorates, nitrates, nitrites, hydroxylamine, or nitroguanidine. These compounds—also used in phosphating—help prevent the formation of hydrogen gas bubbles, which could block the surface during the reaction. Unlike the amorphous layers typical of ferrous phosphating, zinc phosphating produces crystalline structures, primarily composed of tertiary zinc phosphate or zinc–iron phosphate. The typical thickness ranges from 8 µm to 20 µm (approximately 0.0003 to 0.0008 inches)—significantly thicker than simple phosphate layers. This greater thickness contributes to improved corrosion resistance.
Tri-Cation Phosphating Uses Foreign Ions to Create Robust Layers
This advanced form of phosphating is primarily used on galvanized steel sheets, which do not release iron ions. Instead, the treatment solution contains other metal cations—such as manganese, calcium, copper, or magnesium—which react to form a protective surface layer. These coatings shield the substrate from corrosion and serve as a reliable base for further surface treatments.
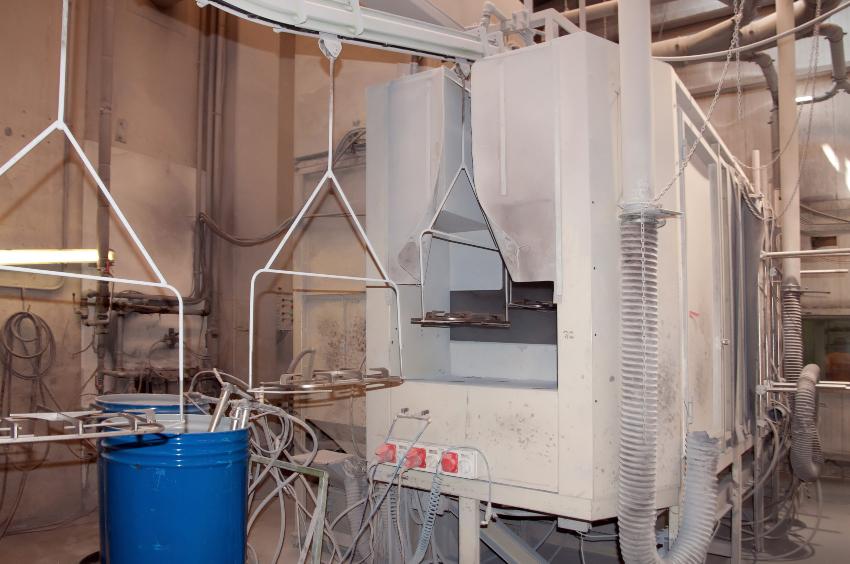
Passivation – Another Way to Form a Protective Conversion Layer
Aluminum, widely used in industries such as aerospace, benefits from passivation as a corrosion protection method. This process should not be confused with yellow or green chromating, both of which involve toxic Cr(VI) compounds and are no longer in use. In passivation, Cr(III) reacts with aluminum to form difficult-to-dissolve trivalent chromium oxides on the metal surface. This layer not only protects the underlying aluminum from corrosion but also improves paint adhesion. Passivation is suitable for other metals as well, including zinc and zinc alloys.
Anodic Oxidation – An Electrochemical Alternative
Protective aluminum oxide layers can also be formed through electrochemical methods. In this case, the aluminum is submerged in an electrolyte solution and serves as the anode. As electrolysis occurs, oxygen is released and reacts with the metal to form a layer of aluminum oxide that shields the surface. The coating thickness can be controlled by adjusting the current, time, temperature, and acid concentration in the electrolyte bath. In practice, layers with a thickness of 5 µm to 8 µm (roughly 0.0002 to 0.0003 inches) have proven effective.
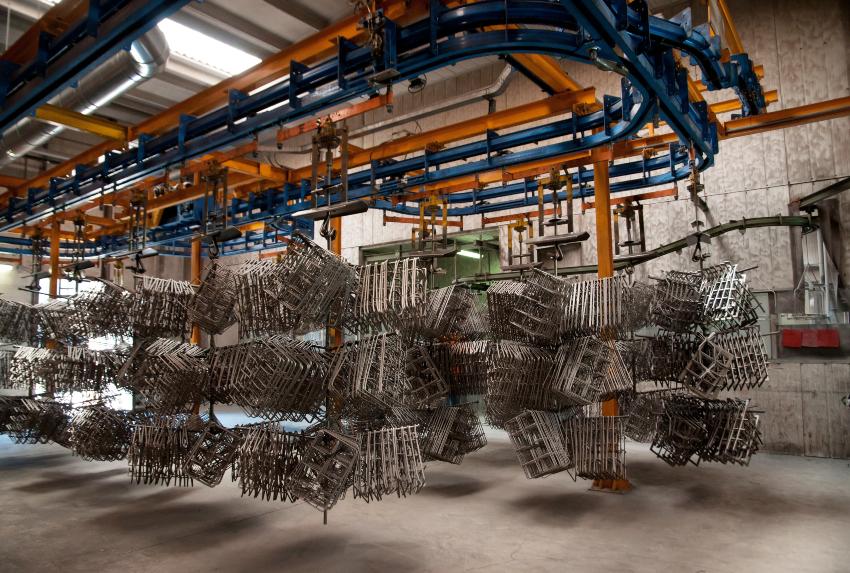
What Does the Future Hold?
New methods are constantly under development. Many combine inorganic compounds such as titanium or zirconium with organic polymers. Titanium or zirconium forms a chemical bond with the metal surface, creating a conversion layer that is much thinner than conventional coatings.
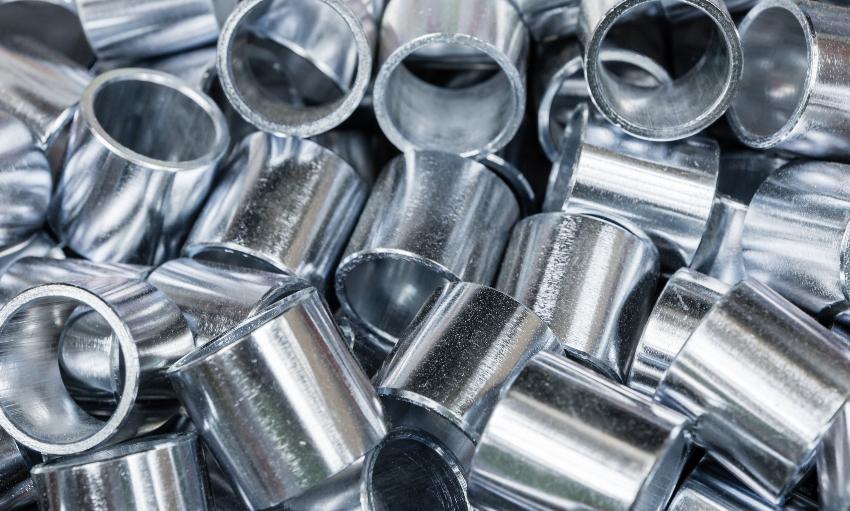
In the next step, organic polymers are added to form a hybrid layer composed of both organic and inorganic components. These systems have already been tested on aluminum and result in ultra-thin coatings in the nanometer range (less than 0.001 µm, or approximately 0.00000004 inches). Despite their minimal thickness, they offer excellent paint adhesion.
Before a metal component receives its final finish — usually a sleek coat of paint — it must first go through a series of preparation steps. One of the most important is surface treatment, and conversion coatings play a crucial role in this process. They ensure durable paint adhesion and long-term corrosion resistance. By carefully matching the metal substrate with the right surface technology, the best results can be achieved. With continued innovation in chemical nanotechnology, the future holds even more advanced possibilities.