How Does Manganese Phosphating Work?
Manganese phosphating is a conversion coating process used primarily on low-alloy ferrous parts. It provides excellent corrosion resistance and reduces friction and wear in sliding or rotating applications. This guide explains how manganese phosphate conversion coatings are formed and how they affect the properties of treated parts. These coatings provide excellent corrosion protection and are especially valued for their wear resistance in sliding applications.
Manganese Phosphating Process: How the Layers Form
The main steps in manganese phosphating are:
- Cleaning and degreasing
- Pickling to remove rust and scale
- Activating the surfaces
- Forming the manganese phosphate layer
- Post-treatment through oiling or coating
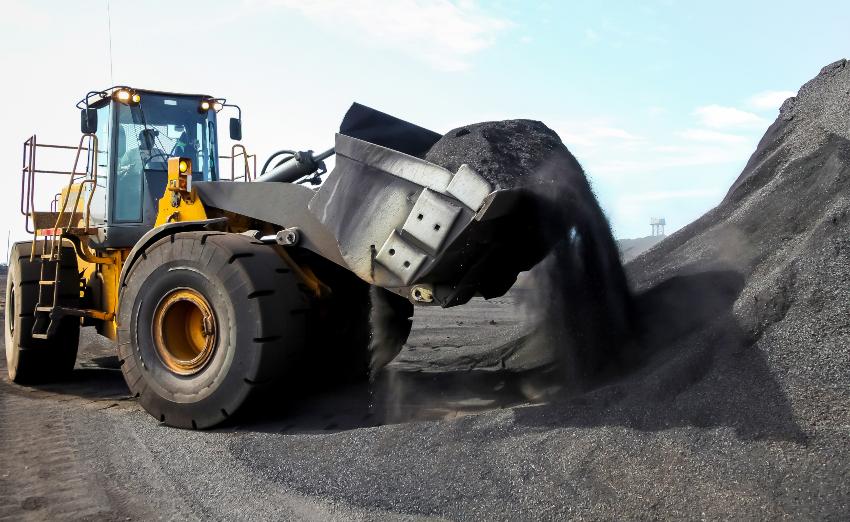
Cleaning and Degreasing
Cleaning and degreasing are the first step in any surface treatment process. Workpieces often have accumulated cooling lubricant or corrosion prevention residues that can interfere with the chemicals used to build the manganese phosphate layer. The type of cleaner depends on the contamination: alkaline cleaners work well for heavy, greasy deposits, while milder neutral cleaners can handle light residues. After cleaning, a thorough cascade rinse removes any leftover cleaning solution. In this step, the parts pass through a series of rinse tanks while deionized water flows in the opposite direction, allowing the rinse water to be reused for mixing fresh cleaning solutions.
Pickling to Remove Rust and Scale
Heat treatments and welding often leave rust or scale on metal surfaces. Storing parts for extended periods can also lead to rust spots. Since conversion coatings rely on chemical reactions, these contaminants must be removed. Pickling is only necessary if such impurities are present and it is typically done with an inorganic acid that dissolves rust and scale. After pickling, parts go through a multi-stage cascade rinse.
Activating the Surfaces
Before manganese phosphating, the surfaces must be activated. As salts of phosphoric acid, phosphate coatings naturally form a crystalline structure. The activation solution creates nucleation sites where the manganese phosphate crystals can start to grow. These crystals expand until they meet and cover the entire surface. The number and distribution of nucleation sites determine how large the crystals become in the next step. Choosing the right activation agent helps tailor the coating structure for the intended application.
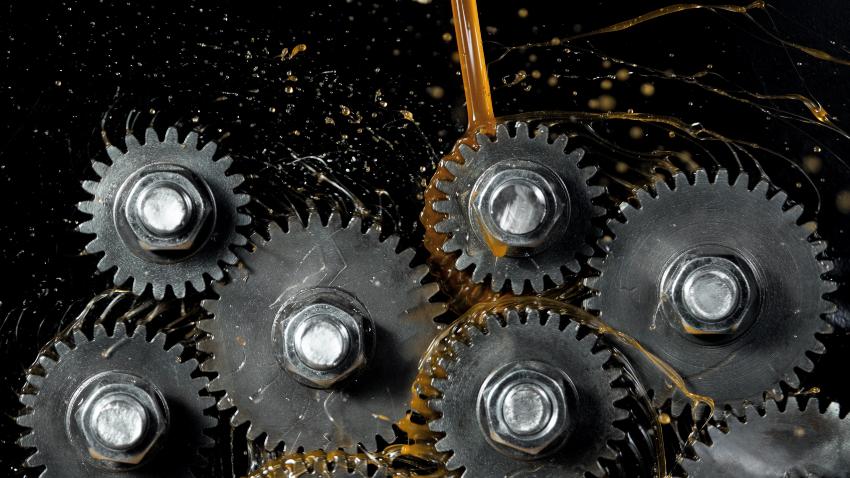
Forming the Manganese Phosphate Layer
This conversion coating takes place in immersion tanks using a solution of diluted phosphoric acid, Mn²⁺ ions (manganese), and other additives. Bath temperatures for this process are typically around 185 °F (85 °C), with immersion times ranging from 5 to 20 minutes. A multi-stage cascade rinse and drying process completes the phosphating. To keep the concentration of process chemicals within the required limits, the bath must be monitored. Dosing pumps replenish chemicals as needed, and any water lost due to evaporation is replaced with rinse water from the final cascade rinse. Sludge generated during phosphating should be continuously removed using a sloped tank bottom to avoid the need for frequent draining and cleaning.
In the periodic table, Mn (atomic number 25) and iron (26) are next to each other. They share similar chemical properties, and their ions are almost identical in size. As a result, the metal surface easily forms mixed crystals that contain both Mn²⁺ and Fe²⁺ ions along with phosphate ions. These ions can combine in nearly any ratio. The crystal size depends on prior surface activation, while the final coating thickness is mainly determined by immersion time and bath conditions. Coating thickness can be controlled very precisely, typically ranging from 0.00008 to 0.0002 inches (2–5 µm), with thicker layers up to about 0.0012 inches (30 µm) possible.
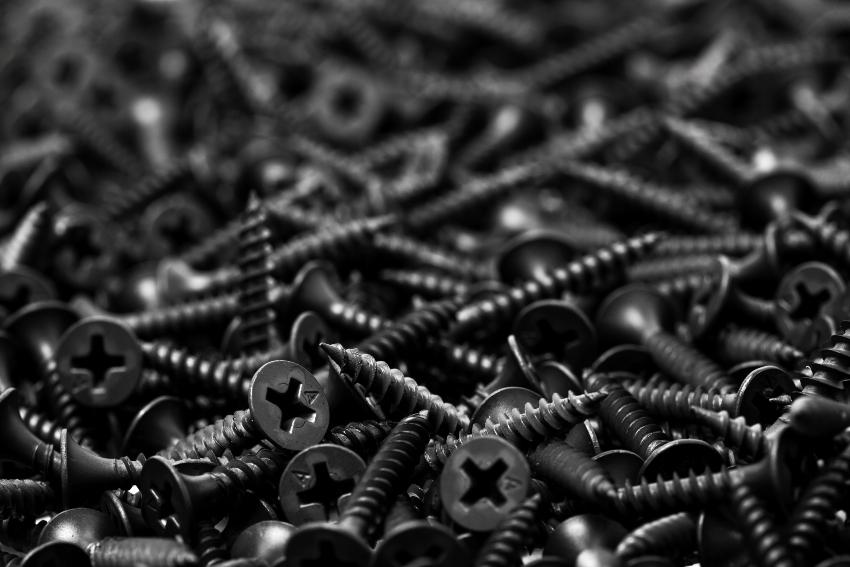
Post-Treatment: Oiling or Coating
Thanks to their fine, porous structure, phosphate coatings based on manganese make an excellent base for subsequent painting or coating. This is why this method is often used as a pretreatment step before applying an organic coating to high-quality components. The coating’s structure also makes it highly receptive to oils and greases, which are used for additional corrosion protection. The parts are dipped in appropriate oil baths, and the protective agents penetrate and remain in the pores.
Typical Applications for Manganese Phosphating
These manganese based phosphate layers stand out for their wear resistance and ability to reduce friction in sliding contacts. For this reason, they are widely used on parts such as gears and plain bearings. For example, automotive camshafts and transmission gears often receive this type of coating to improve break-in wear resistance and ensure reliable operation under high loads. These benefits also apply to forming processes: when parts are to be further processed by deep drawing, wire drawing, or tube drawing, a phosphate layer containing manganese can reduce the required forming force, decrease tool wear, and minimize the risk of cold welding.
Additional features of these coatings include:
- Electrical insulation
- Temperature resistance of up to about 570 °F (300 °C)
- Attractive matte black-gray appearance
- Excellent dimensional stability
- Good flexibility
- Insoluble in water
- Resistant to solvents, fuels, and lubricants
- Strong adhesion
- Environmentally friendly
Typical uses for manganese phosphating range from fasteners and gears, to components for roller and plain bearings, all the way to parts used in valve manufacturing. Industries that rely on manganese phosphate coatings include automotive, general machinery, aerospace, and plant engineering.
In mechanical engineering and firearms manufacturing, black oxide finishing (also known as bluing) is still common. This conversion coating provides temporary corrosion protection and an attractive black finish. Bluing is done with highly concentrated salt solutions heated up to about 300 °F (150 °C), producing smooth layers up to 0.00004 inches (1 µm) thick. However, the strongly alkaline salts used for bluing are classified as hazardous materials. In many cases, the energy-intensive, environmentally taxing bluing process can be replaced with manganese phosphating, which generates less hazardous waste and is easier to manage under OSHA and EPA regulations.