Equipment and machinery cleaning are essential maintenance activities across all industries. These practices extend the lifespan and maximize the uptime of expensive industrial equipment. Companies specializing in industrial cleaning continuously face challenges in selecting the most effective methods and cleaning agents while complying with OSHA standards. Their goal is to remove stubborn contamination while protecting sensitive components, maintaining environmental responsibility, and ensuring safe working conditions for their personnel.
Industrial Cleaning Methods
Environmental factors and substances that moving and fixed parts encounter during operation cause contamination on the machinery. When multiple machines interconnect to work together in the production process, they form an integrated production system. This system includes not only the primary machinery but also the necessary material handling equipment and processing units. Both equipment and machinery cleaning employ a combination of manual and mechanical cleaning methods.
Manual Cleaning
Manual cleaning tasks involve using basic hand-held tools such as cleaning cloths, brooms, shovels, and scrapers. These tools effectively remove accumulations of solid or paste-like substances from containers, clean enclosures, and frames, and remove contaminants from walls and windows. Appropriate industrial cleaners enhance these efforts by softening and dissolving the dirt before personnel remove it through wiping or washing. Manual cleaning is particularly important for machine tools. While conveyor chains remove larger chips during operation, smaller debris gradually accumulates in the machines. Over the course of a year, sludge can build up in coolant collection tanks, occupying up to a third of the volume, thereby reducing coolant capacity and compromising heat dissipation.
Mechanical Cleaning of Machines and Equipment
Various forms of mechanical cleaning use technical tools for contamination removal, with primary methods which include blasting, vacuuming, and pressure flushing. In blasting operations, operators apply cleaning media such as steam, water, sand, steel shot or dry ice, at high pressure to contaminated surfaces. To enhance cleaning effectiveness, operators often add industrial cleaners to the water in high-pressure water blasting. Although frequently promoted as environmentally friendly because it leaves no residual waste aside from the removed contaminants, it is important to note that dry ice is essentially frozen carbon dioxide, which ultimately disperses into the atmosphere as a greenhouse gas after use. Pressure-generating equipment such as pumps, compressors, steam boilers, high-pressure hoses, and manual or mechanically operated spraying devices (lances, guns, spray heads) facilitate this technology.
Vacuuming employs air conveyance systems and vacuum trucks to empty collection tanks and vessels. Operators use vacuum force to extract waste materials or spent cleaning solutions from containers. Air conveyance systems effectively remove dust and liquids that can be transported via the airstream and collected outside the facility, while vacuum trucks generate sufficient suction to transport materials ranging from liquid to sludge directly into their integrated containers. Pressure flushing plays an essential role in equipment cleaning by clearing deposits from hard-to-access areas in piping, ducts, and devices, thereby preventing potential blockages. Hot water is effective for removing water-soluble contaminants, acidic solutions for lime deposits, and alkaline industrial cleaners for oily and greasy residues. It is crucial to verify material compatibility when selecting cleaning agents.
Selection of Suitable Cleaning Agents and Methods
Key factors to consider when selecting agents and methods include the required cleanliness standards, contamination type, accessibility of affected areas, and material sensitivity to specific components. When equipment must remain powered during maintenance, workers should avoid using water-based solutions. This restriction also applies when they cannot adequately protect sensitive instrumentation and control systems from agents. Food industry and medical technology applications require additional disinfection steps during machine and equipment maintenance to meet stringent hygiene standards. These facilities typically undergo multiple cycles with solutions, followed by disinfectants, and conclude with pure water rinses.
Cleaning metal surfaces requires paying particular attention to cleaning agent compatibility. Acidic cleaners, while effective against lime-scale, can promote rust formation on ferrous metals. Alkaline cleaners effectively remove oil and grease but may damage light and non-ferrous metals. Complex situations arise when dealing with mixed contamination of both lime-scale and grease. Even after identifying agents that effectively clean without damaging the primary materials, plastic and rubber components like seals and controls may present additional challenges. Some cases necessitate developing specialized cleaning techniques and agents.
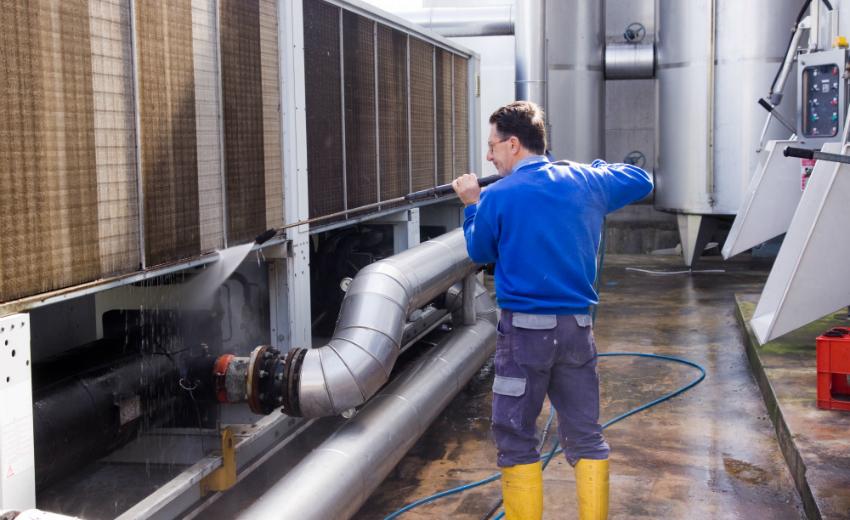
Preventing Hazards During Machine and Equipment Cleaning
Specialized contractors often perform industrial cleaning operations, and they have expertise in safe equipment maintenance procedures. Since these contractors may be unfamiliar with facility-specific conditions, it is essential to establish clear organizational protocols to protect personnel from potential hazards. This particularly involves isolating areas from ongoing operations. Before initiating machine maintenance, proper lockout-tagout procedures must be performed to ensure the equipment remains de-energized. Personnel must receive comprehensive briefings about existing hazards and emergency response procedures before performing these tasks.
Accidents can result from improper handling of hazardous materials, careless work in explosive environments, or mishandling of pressurized systems. A formal permit system and detailed operational procedures must be put in place to help minimize these risks. Maintenance in confined spaces presents unique challenges. Before sending personnel into containers or tanks for interior maintenance, consider alternative closed-system methods. These methods typically involve agitating contamination using heated air or cleaning solutions, with the medium being recirculated and contaminants then being separated outside the confined space. When confined space entry cannot be avoided, all applicable safety regulations and procedures must be strictly followed.