« Which Painting Option is Recommended? »
Both powder coating and liquid paint are widely used in surface coating. The decision between the two depends mainly on factors such as the material, contour, and size of the parts to be painted, as well as the specific characteristics required for the layers produced. Additionally, the cost-effectiveness of the coating technique and the ongoing operational costs significantly influence this decision.
Applying the Paint to Surfaces
Powder coating consists of finely ground solid particles. Liquid paint is a liquid mixture of the paint combined with a solvent, or two components that chemically react to bond together. This distinction defines this painting technology. While a liquid wets surfaces, powder normally trickles down.
In powder coating, the trickling is prevented by electrostatically charging the grains, thereby attracting them to the surfaces. This principle only works with metallic materials that are grounded. Therefore, materials such as plastics, mineral building materials, or wood can only be coated with liquid paint.
Drying Conditions
The final solid layer in powder coating is formed by heating the prepared parts in a drying oven. There, the powder melts, spreads evenly on the surface, and hardens as it cools. Liquid coatings solidify when the solvent evaporates or when the components chemically react with each other (two-component formulations) or with the oxygen in the air (synthetic resin coatings).
These processes generally take longer than heating in a drying oven. Coatings that dry based on evaporating solvents or by reacting with the air’s oxygen solidify from the outside in. To ensure that the areas closest to the material, which are away from the air, dry properly, liquid paint often needs to be applied in several thin layers until the required total thickness is achieved. Only after an intermediate layer has dried can the next one be applied. Powder coating, however, requires only one pass to achieve the necessary layer thickness. This process takes less time and is also somewhat cheaper.
Properties of the Paint Layers
The quality of the protective layers relies heavily on proper surface pre-treatment, which includes cleaning and degreasing, creating conversion coatings, and drying the surfaces. These preparatory processes are necessary regardless of the coating system used.
These processes ensure good adhesion and even application. Steel parts that are later subjected to strong mechanical stresses and weathering are often additionally galvanized as part of surface pre-treatment, especially before powder coating.
Modern paint systems are optimized so that similar layer properties can be achieved with both powder and liquid applications. If the focus is on corrosion protection, there is a tendency to prefer powder coating. This type of coating is scratch and abrasion-resistant, weather-resistant, and flexible, reducing the risk of cracks in the protective layer on parts subjected to bending stress.
In machinery and equipment manufacturing, as well as in the construction of agricultural machinery and commercial vehicles, powder coating is the most commonly used process. Liquid painting is preferred when, in addition to corrosion protection, specific visual effects are desired, and when non-metallic materials need to be coated.
A multi-colored or high-gloss surface coating is much easier to achieve with this process. Large fields of application for liquid paint include the cathodic dip coating of car bodies for passenger vehicles and the painting of plastic casings.
The Structure of Coating Technology
Im industriellen Maßstab erfolgt die Lackierung in Anlagen, die aus mehreren Stationen bestehen. An die Oberflächenvorbehandlung, die aus aufeinanderfolgenden Prozessen aufgebaut ist, schließen sich die Farbgebung und die Trocknung an. Bestandteil größerer Anlagen ist Technik zur Rückgewinnung von Rohstoffen und Betriebswasser, zur Abluftreinigung und zur Aufbereitung des Abwassers.
Processing of Powder Coating
Powder coating requires powder spray booths, which are either enclosed or fitted with openings. Enclosed booths are operated in batches. For continuous operation or the use of hand spray devices, booths with appropriately designed openings are used. The parts to be coated are located on racks, which also provide grounding. The paint is driven by an air current through a spray gun. The electrostatic charge is generated by an electric field at the outlet of the gun (corona) or by friction within the gun. The charged powder cloud is attracted to the surfaces, resulting in significantly less overspray (paint that misses the surface) than with liquid painting.
Following the path of the electric field, the paint particles also reach undercut and rear surfaces. The curing of powder coating takes place in a drying oven with precise temperature control. The temperature profile consists of heating, holding, and cooling phases. The cabin size and the size of the drying oven limit the dimensions of the parts. The overspray is periodically removed from the cabin. Small quantities are usually disposed of, but it is economically viable to process and recycle large quantities.
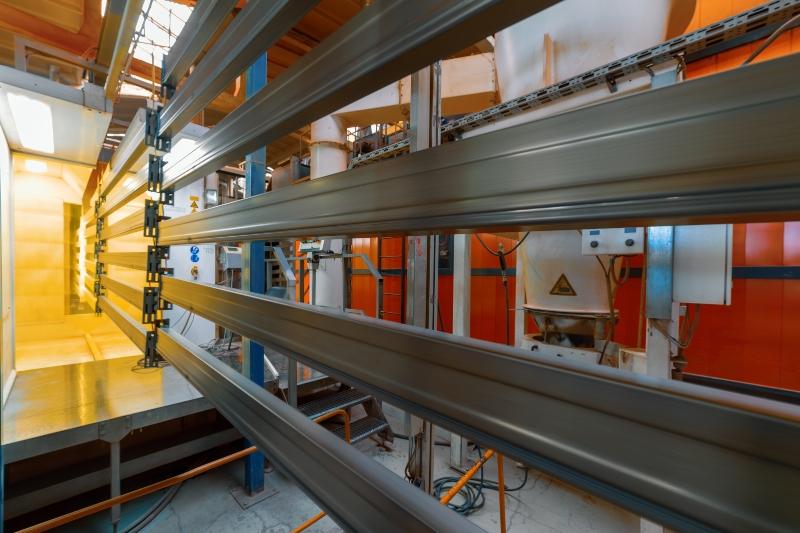
Processing of Liquid Paint
Liquid painting can be done by brushing, spraying, or dipping. Depending on the volume of workpieces, the work is conducted at manual workstations, in dipping tanks, or in spray booths. Spraying results in greater paint losses caused by overspray, which flows past the surface and is caught by a water wall in larger facilities. With this method, the paint only reaches the surfaces facing the exit opening. In dipping tanks, losses due to overspray are eliminated. The liquid paint reaches all areas of the surface. For an even surface coating of parts with complex contours, dipping is supported by an electric field. The field is generated by a DC voltage that is applied between the part and additional electrodes (cathodic dip painting).
The drying of painted parts can occur without the use of thermal energy in the air, though the process can be accelerated with the application of moderate heat
Safety and Environmental Aspects
One advantage of processing powder coating is the absence of volatile organic solvents and lower water consumption. Increased attention is required for the electrically charged powder cloud. The powder paint consists primarily of organic materials that are flammable. Therefore, precautions against dust explosions must be taken, especially concerning the exhaust system. If the powder paint is sprayed manually in the cabin, personnel must be protected against electric shocks. The relevant employees must not themselves become electrically charged. This is achieved through conductive work clothing, conductive footwear, and conductive, grounded floors.
US facilities must follow OSHA standards for hazardous locations (29 CFR 1910.307) when designing powder coating areas to prevent potential fire and explosion hazards. A disadvantage of powder coating, compared to liquid painting, is the higher energy consumption by the drying oven for curing. Liquid painting often involves volatile organic solvents that can form flammable vapor-air mixtures and are considered air pollutants. In the United States, facilities must ensure compliance with EPA regulations regarding VOC emissions and hazardous air pollutants when using liquid paints. This disadvantage is being mitigated by the increasing use of water-based paint.