« What does it mean? »
Pickling and passivation are chemical or electrochemical surface treatment processes that deliberately modify the properties of the material’s surface layers. These methods are commonly used in the pretreatment of metal workpieces to create corrosion prevention and prepare surfaces for subsequent coating processes.
Purpose of Pretreatment with Pickling and Passivation
Metals react with oxygen in the air at their surfaces, leading to visible signs of corrosion. Examples include rust on iron-based materials and patina on copper. These oxide layers, particularly in the presence of moisture, can impede functionality. High temperatures involved in processes such as heat treatment, rolling, welding, and laser cutting exacerbate corrosion, often leading to oxidation or discoloration in heat-affected zones.
Left untreated, such components degrade over time. Surface treatment prevents or delays this by applying coatings that separate the material from its environment. Effective coatings rely on the removal of natural oxide layers through pickling and the creation of defined material structures on the surface via passivation.
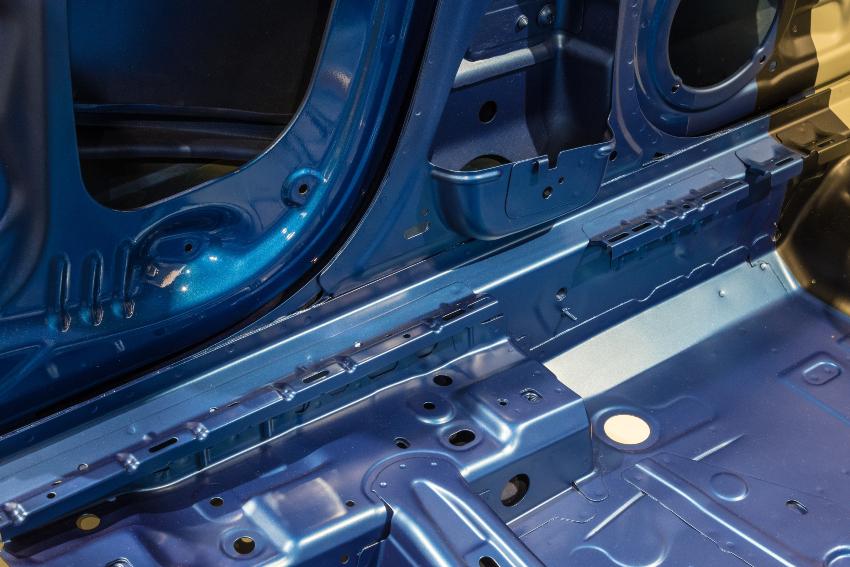
The Pickling Process
Loose layers of corrosion can be removed mechanically, but the remaining oxides require chemical removal through a pickling process. This process typically utilizes acids or acid mixtures. Since acids cannot dissolve oils or greases, thorough degreasing is necessary before processing. Neutral or alkaline pickling agents are also employed, with alkaline solutions capable of combining degreasing and pickling in a single step. Neutral pickling agents consist of salts that chemically react with the metal to form water-soluble compounds.
Chemical Pickling
Pickling agents penetrate the oxide layer and dissolve the underlying base material, detaching the oxide layer from the metal. The exposure time for the pickling agent must be precisely calibrated for the material and the product. Temperature also influences the reaction. The goal is to minimize material loss while effectively removing the oxide layer. Once the process is complete, the surface is thoroughly rinsed with water, leaving behind a clean, metallic surface.
Electrolytic Pickling
Electrolytic pickling enhances the process by using direct current to dissolve surface material. Voltage adjustments allow for precise control, enabling extremely accurate results.
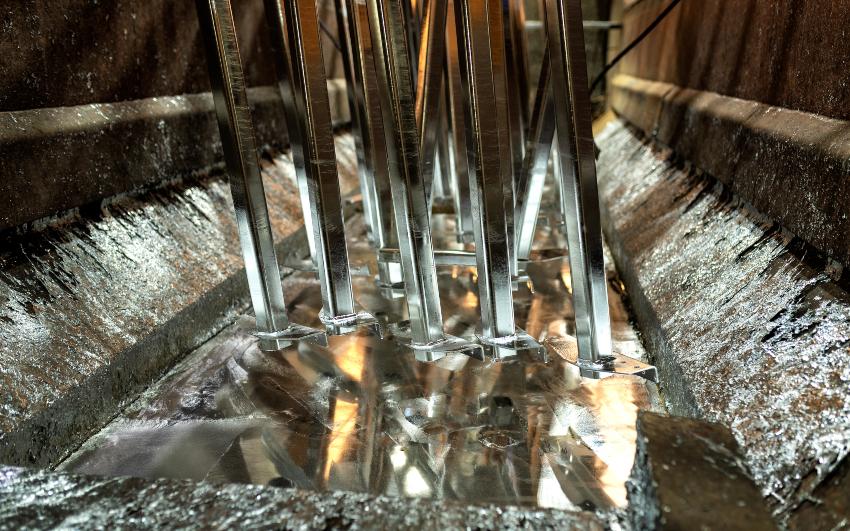
Practical Execution of Pickling
The method of applying the pickling agent to the metal surface determines the pickling process, which may include:
- Immersion
- Spraying
- Application of pickling pastes
- Circulation pickling
Immersion is the most efficient method to employ, as process parameters can be precisely controlled, and spent agents can be environmentally disposed of. Regular bath maintenance ensures waste products are removed, and chemicals are then replenished for cost efficiency.
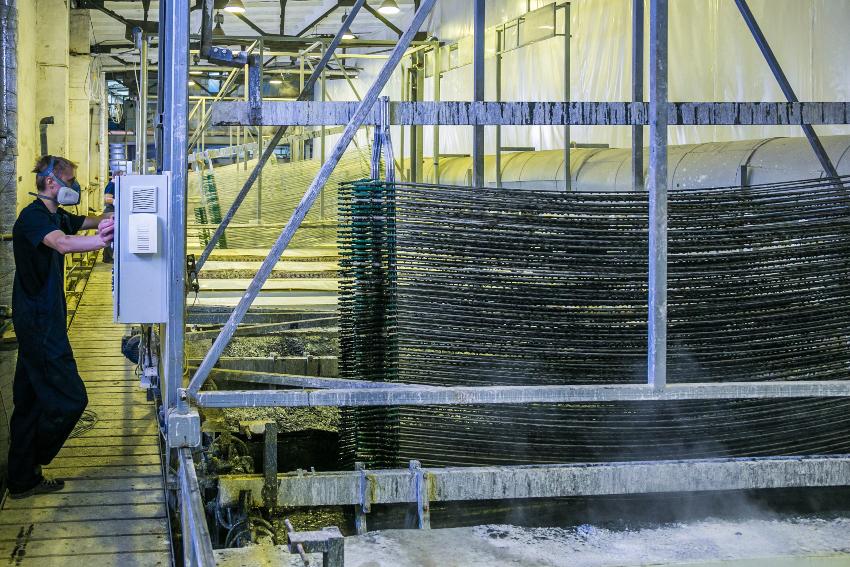
Spraying is often used for metal structures on construction sites, requiring strict health and environmental safety measures for use due to the corrosive nature of most pickling agents. Heat-affected zones near welds can be treated with pickling pastes applied directly to the affected areas. Circulation pickling is used in pipelines and industrial processing equipment, where the pickling agent flows through the system in a closed loop.
Passivation
Formation of Conversion Layers
Many metals naturally form thin protective layers in the presence of air and moisture, preventing corrosion. Passivation artificially induces this process. Acids create metal oxides or hydroxides on the surface that firmly adhere to the material and withstand elevated temperatures. These protective layers, known as conversion layers, result from the transformation of the metal’s surface. In surface engineering, passivation often precedes coating or painting to ensure strong adhesion.
Passivating Copper Alloys, Steel, and Galvanized Steel
To passivate copper alloys, steel, or galvanized steel, surfaces must first be cleaned of oils, greases, and contaminants. Pre-existing oxides, whether naturally formed or resulting from prior surface treatments, are removed through pickling. After cleaning, the components are immersed in passivation baths. Critical process parameters, including bath composition, immersion time, and reaction temperature, are continuously monitored, and maintained. Rinsing follows the passivation process.
Anodizing
For aluminum, passivation is achieved through an electrolytic process known as anodizing. In a sulfuric acid bath, direct current splits water into ions. The aluminum acts as the positive electrode, where oxygen combines with the base material to form aluminum oxide, creating a robust protective layer.
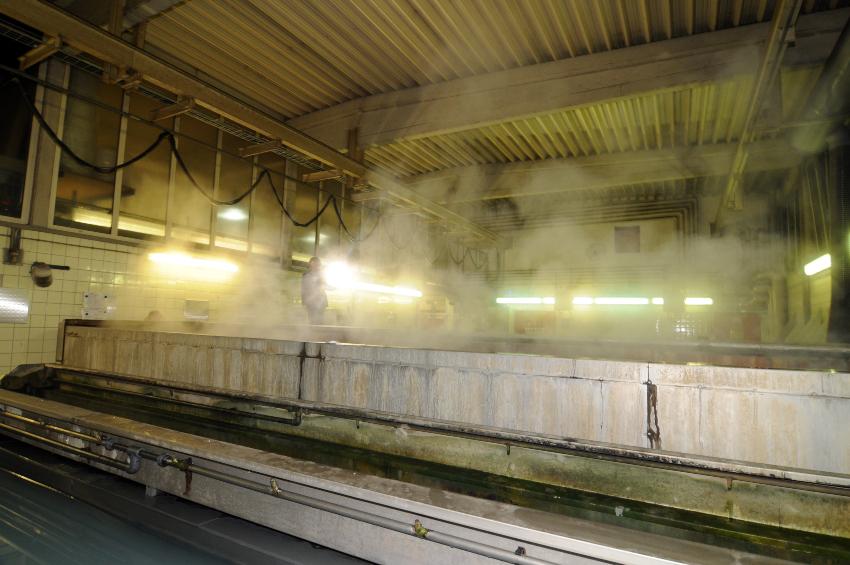