« Passive and Active Corrosion Protection – We explain the differences »
Passiver und aktiver Korrosionsschutz umfasst alle technischen Maßnahmen, die dazu dienen, Werkstoffe vor der Zerstörung durch Umgebungseinflüsse zu schützen. Der Sauerstoff und die Feuchtigkeit in der Atmosphäre setzen vor allem Eisenwerkstoffen zu, die in allen Bereichen der Industrie und der Infrastruktur zu finden sind. Um die Bauteile und Konstruktionselemente langfristig zu erhalten, sind große Anstrengungen und ein hoher finanzieller Aufwand erforderlich.
Causes of Corrosion
In nature, only noble metals occur in their pure form as chemical elements. Most metals used as materials for components are painstakingly extracted from ores, where they are hidden in chemical compounds. Metallic materials naturally seek to form chemical bonds with substances in their environment as soon as the opportunity arises. This process is known as corrosion. Naturally occurring processes such as corrosion are always driven by a difference in physical quantities, which is balanced out by implementing these processes. This includes differences in pressure, temperature, concentration, and electrical or mechanical tension. To prevent corrosion, these differences must be stopped or diverted which can be done passively by building a barrier or actively by inducing a counteraction or change in direction. Passive corrosion protection is achieved by a surface coating that separates the metal from its reactants, while active corrosion protection interferes with the chemical reactions.
Materials science distinguishes between chemical and electrochemical corrosion processes. Chemical corrosion is caused by hot, dry gases or molten metals in chemical industry or metallurgy plants. It can be prevented by using materials that resist such attacks. Far more common are corrosion phenomena that result from electrochemical reactions:
Electrochemical Corrosion Processes
Electrochemical reactions occur when a metal is wetted by an electrically conductive liquid (electrolyte) and diverse types of metals make contact with each other. They also occur when there are concentration or temperature differences in the attacking liquid, or different mechanical tensions exist within areas of the metal.
Under these circumstances, corrosion elements form. The term is borrowed from the galvanic elements used in batteries and accumulators. Certain areas of the material or entire components become the positively charged anode, where the metal dissolves. Other areas become the negatively charged cathode, where the liquid absorbs electrons. If the dimensions of the corrosion elements are microscopically small, they are referred to as local elements. The material decomposes within the microstructure between the crystals of the different alloy elements. Active protection against electrochemical corrosion requires a precise understanding of the reaction mechanisms.
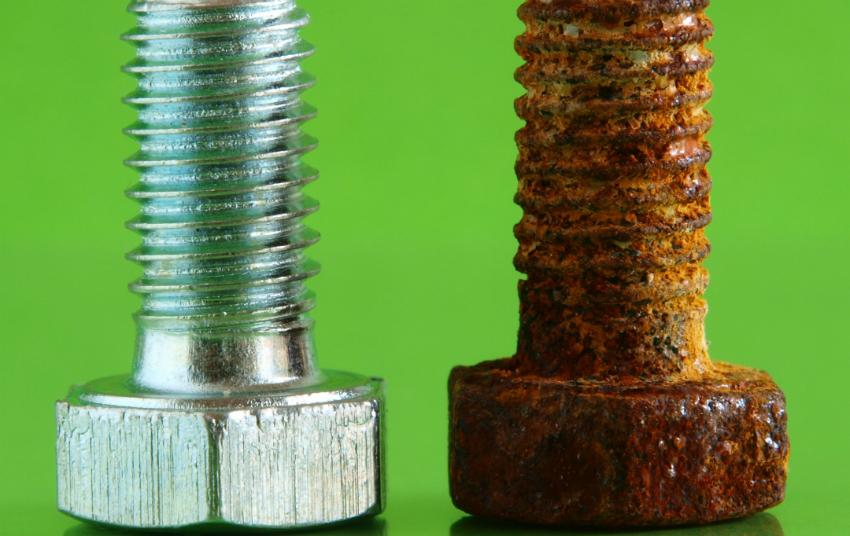
In addition to moisture, the presence of oxygen is important. Most corrosion products are metal oxides. Oxygen is always present in the atmosphere, and it dissolves in water that is in contact with air up to a certain limit. It also forms during the decomposition of water in electrochemical reactions.
Some metals form corrosion products that create dense, cohesive layers on the surface, protecting the material from further degradation. The most well-known example is the green patina widely seen on copper roofs. Similar protective layers form on aluminum and magnesium. On chromium and stainless steel, very thin, invisible surface layers form that almost completely block attacking media. Rust on iron-containing materials, in most cases, is loose and porous, which will accelerate corrosion.
Types of Corrosion
Based on the appearance of the corrosion products, corrosion can be categorized as:
- Uniform corrosion
- Intergranular corrosion (grain boundary corrosion)
- Transgranular corrosion
- Pitting corrosion
- Stress corrosion cracking
We will now take a closer look at passive and active corrosion protection, their respective methods, and applications.
Passive Corrosion Protection
Passive corrosion protection is achieved by applying corrosion protection agents that coat the metal surface. Long-lasting protection can be achieved with professional coatings on a conversion layer. Conversion layers are created by phosphating, chromating, or burnishing. In these processes, the material reacts with the treatment agent in the surface layer. A final paint layer completes the protection against corrosive media. This method is used predominantly in metalworking for machine cladding and vehicle parts.
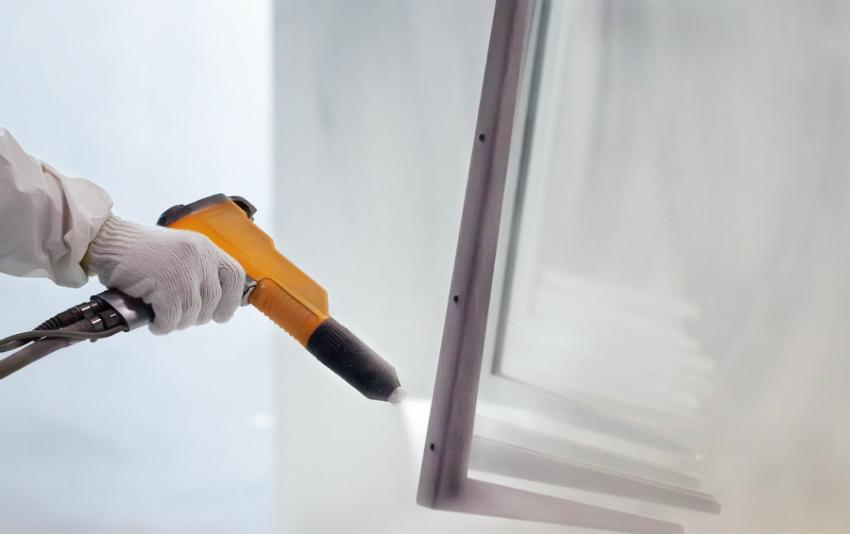
On steel structures like bridges or power line masts, the paint layer gradually wears away due to weather exposure. To maintain the stability of these structures, regular inspections are necessary. If the coating is cracked or the paint flakes off, it must be completely removed, and the surface must be primed and repainted. Special rust-proof paints can extend the intervals between corrosion protection treatments.
As an alternative to paints and coatings, metallic coatings such as zinc or chrome are used for corrosion protection, especially for iron materials. In metalworking, semi-finished products and processed parts are treated with temporary corrosion protection agents. Thin layers of oil, paint, or zinc, which can be easily removed, prevent rust formation before or during processing. This is particularly important in winter when metal parts are stored or transported in the cold and then placed in a heated workshop. Humidity then condenses on the surfaces and can cause unprotected parts to start rusting within minutes.
Active Corrosion Protection
Active corrosion protection is primarily used for materials that are difficult to access during use and cannot undergo regular surface treatment. This applies, for example, to underground cables and pipelines, waterworks, power plant boilers, storage tanks in the chemical industry, and the outer hulls of ships. Active protection against corrosion is based on either cathodic or anodic corrosion protection and the modification of the material or the corrosive medium.
Cathodic Method
In the cathodic method, the electrical current is compensated by an equal current flowing in the opposite direction. This is done by using an external direct current source or sacrificial anodes made of less noble metals. The sacrificial anode or protection anode is short-circuited with the material and dissolves in place of the material.
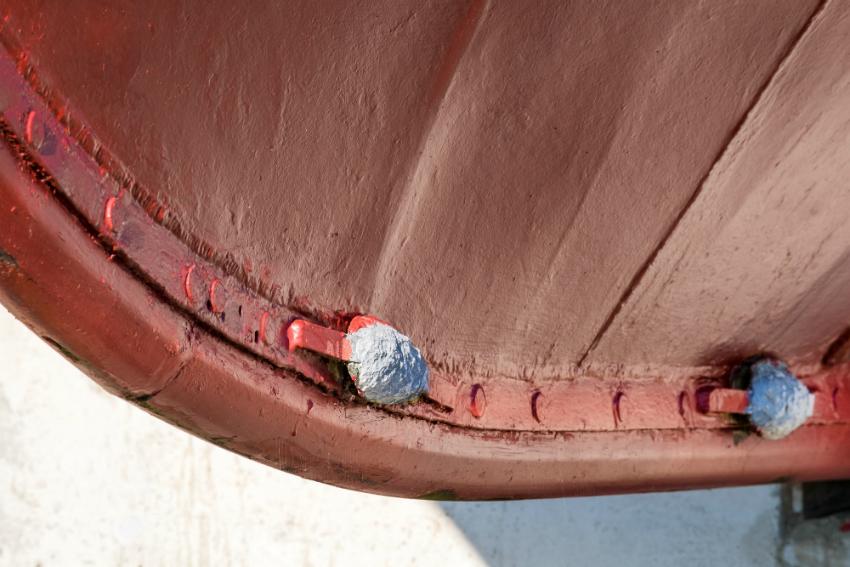
Anodic Method
Anodic corrosion protection methods utilize the formation of a thin protective layer of corrosion products on the material’s surface, preventing further attack. The metallic object is passivated through polarization. This method requires that the metals produce suitable oxidation products.
Active protection against corrosion also involves relieving stress differences in the material caused by metalworking through heat treatment. Measures such as stress-relief annealing and normalization not only balance these stresses but also positively affect the microstructure of the material.
Use of Inhibitors
In cooling water circuits and boiler feedwater systems, inhibitors are used to disrupt the chemical reactions between water and the container or pipe walls. For example, a diluted hydrazine solution can be used. This compound of hydrogen and nitrogen removes oxygen from the water and raises the pH level. Hydrazine reacts with oxygen to form water and nitrogen, thus creating a more alkaline environment Alkaline solutions are preferred because they are less aggressive towards iron-based materials.