« How Car Parts from Fenders to Center Consoles Get Their Paint »
Painting plastic parts is challenging because plastics repel most liquids and are difficult to wet. In the automotive industry, more frequently, parts are being made from plastic materials. Exterior parts are exposed to weather conditions, while interior parts must withstand frequent handling. How does the automotive industry meet these demands?
Advantages of Plastics in Automotive Manufacturing
Plastics are lighter than metals, reducing the mass of a car which leads to lower fuel consumption, making this the key reason for manufacturing as many car parts as possible from plastics. Another advantage is the variety of shapes that can be created with these materials. Finally, their elasticity reduces costs from minor damage.
Parts such as bumpers, hubcaps, trim strips, and mirror housings have long been made from plastics. Modern composite materials, also known as glass fiber-reinforced plastics (GFRP), are currently used in hoods, fenders, and doors.
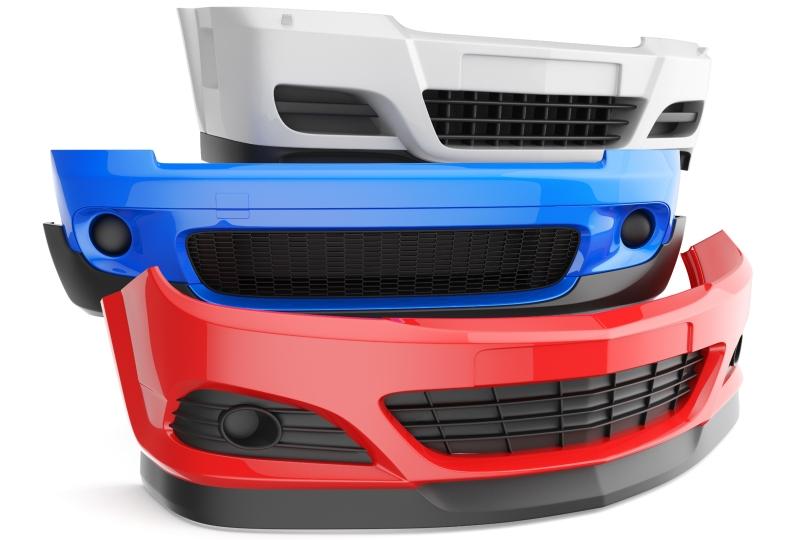
Paint as corrosion protection and aesthetic enhancement of plastic parts
While it is well known that metal requires corrosion protection, plastics also experience aging and degradation over time. Sunlight’s UV rays, moisture absorption, temperature fluctuations, as well as dust, insects, and rain all take a toll on plastic materials.
Painting plastic parts not only protects them from environmental influences but also offers an opportunity to customize the vehicle’s appearance. Depending on personal taste, parts can be highlighted with special colors, or the car can be given a uniform appearance.
Special Requirements for Paint Systems on Plastic
Liquids tend to form the smallest surface area possible due to the attraction forces between liquid molecules, a phenomenon known as surface tension. The relationship between the surface tension of the liquid and the solid surface determines whether drops form or whether the liquid spreads evenly. To create a smooth film, the surface tension of the solid must be greater than that of the liquid.
Therefore, painting plastic parts requires paints with the lowest possible surface tension.
Since plastics are elastic and car parts can be easily deformed, the paint must also have sufficient elasticity to prevent cracking. It must expand and contract with the substrate.
To achieve successful painting of plastic parts, additives are required to increase the paint’s elasticity.
The automotive industry uses a wide variety of plastics for different applications, each with distinct properties. Therefore, specialized paints and paint systems are needed, tailored to the specific requirements of each material.
The paint must be compatible with the plastic material.
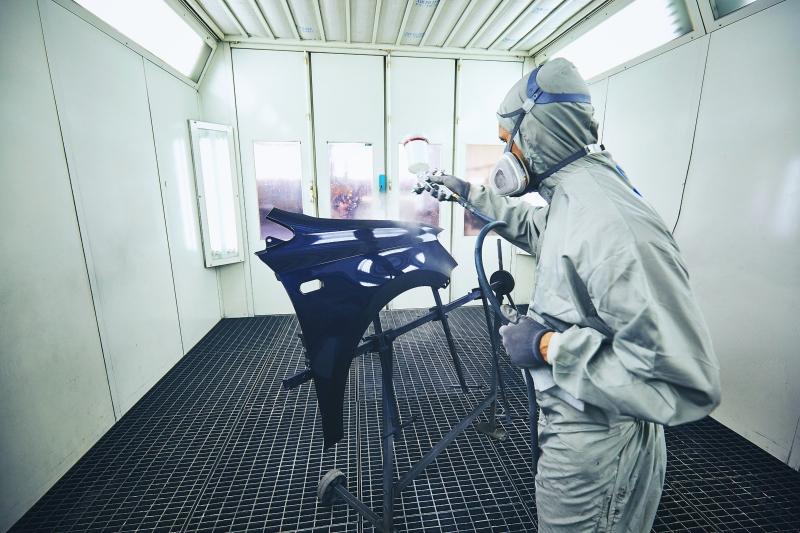
Painting of new parts
In large-scale production, automotive manufacturers and suppliers have equipment that allows parts to move through various necessary stages, including cleaning, priming, and painting plastic parts. Thorough drying is required between each stage.
Cleaning
For optimal paint adhesion, parts must be clean. New parts often have residues of release agents which are used for removing parts from molds during the production process. These residues may repel paint and must be completely removed. This also applies to greasy contaminants, such as fingerprints.
Cleaning methods include the powerwash process and CO² snow blasting. The powerwash process uses heated alkaline cleaning solutions, which are sprayed onto the plastic parts under high pressure. After washing, the parts are rinsed and dried. In CO² snow blasting, the surface is blasted with solid carbon dioxide.
Residual release agents and moisture are eliminated by the process of tempering. During this process, parts are heated until the water and solvents absorbed by the plastic evaporate.
Priming
Priming promotes adhesion. The plastic, primer, and paint must be coordinated as a system. Before proceeding, the primer must be completely dry.
Painting
When painting plastic parts, several thin layers of paint are applied. Each layer must dry before the next one is applied. Drying can be accelerated by applying heat. The data sheets and instructions from the paint manufacturers provide information on optimal temperatures and required drying times.
Painting Older Parts
Damage or personal design preferences are common reasons for painting older plastic parts. This restores or enhances the car’s value in the eyes of the owner. The paint system components must be tailored to the existing material.
Many process chemical manufacturers, such as Kluthe, offer comprehensive consulting services and employee training to assess the material, choose the appropriate paint, and guide the customer through the optimal approach. For new paint jobs, thorough surface preparation is essential. Scratches, cracks, or other damage are repaired with fillers or putty. The surface is sanded with fine sandpaper and then lightly roughened again to improve primer adhesion.
An intact existing paint job can be painted over without re-priming. However, all dirt, cleaning, and care products must be thoroughly removed first. Adjacent areas that should remain unpainted need to be carefully masked with tape. After this, the same steps are followed as those used when painting new parts.