Aluminum is a popular and essential material in industrial sectors such as machinery and equipment manufacturing, food processing, and architecture. As a true lightweight metal with low density, high electrical and thermal conductivity, and excellent workability, it is highly versatile. When exposed to air, aluminum naturally forms a protective oxide layer that shields it from further corrosion and environmental damage. However, it can also be coated with paint for added protection, provided the proper steps are taken during and prior to the painting process.
Where Painted Aluminum Is Used in Modern Industry
Aluminum components are used across a wide range of industrial fields. Due to its lightweight properties, the metal is commonly used in automotive, shipbuilding, and aircraft construction. In architecture, it serves both structural and aesthetic purposes — one high-profile example being the Empire State Building in New York, where aluminum was used extensively for the tower structure, spire, entrances, elevator doors, ornamental trim, and over 6,000 window spandrels.
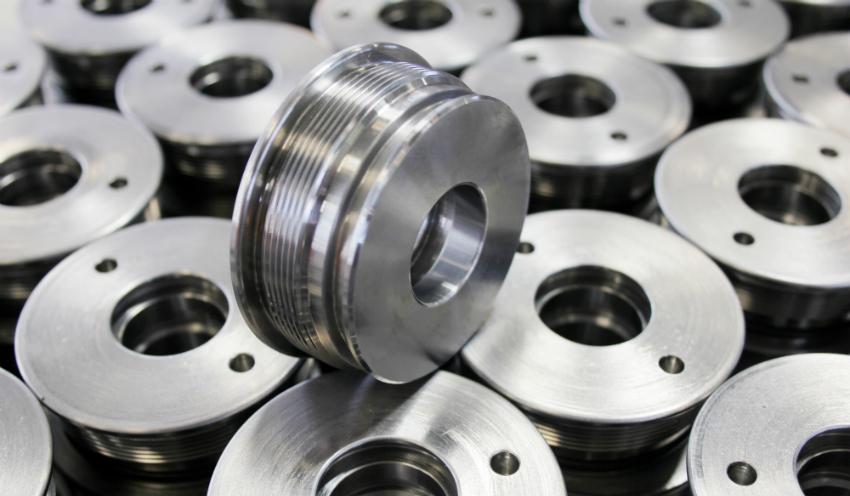
Aluminum oxidizes naturally in the air, forming a stable layer of aluminum oxide. In many applications, especially those with lower technical requirements, this layer offers sufficient protection. However, the oxide layer is not uniform or precisely defined in thickness, which can be problematic for industrial applications with stringent quality standards. In some industries, specific colors or finishes are desired. Aluminum is particularly sought after in the automotive sector, where weight savings allow for smaller engines and improved fuel efficiency.
From Raw Material to Finished Coated Product: A Multi-Step Process
Painting aluminum involves a sequence of coordinated steps. The surface must first be properly pretreated to ensure it is smooth and ready for coating. A suitable aluminum primer is essential and any contaminants from prior processing—such as oil films or lubricant residue—must be thoroughly removed. The painting procedure builds upon this foundation, which ensures that the entire part is evenly coated. Strong adhesion between the aluminum and the paint is crucial, and issues like residual moisture must be avoided. The painting process itself consists of several stages.
Surface Pretreatment Is Key
To paint aluminum successfully, the metal’s surface must be pretreated. Two conditions must be met for proper paint adhesion: First, the natural oxide layer must be modified or properly prepared. Second, the surface must be meticulously cleaned. Residues such as dust, metal shavings, grease, or oil from earlier stages can interfere with adhesion, resulting in uneven paint coverage and poor bonding between the metal and the coating. These contaminants can lead to defects and even corrosion, especially for parts exposed to the elements. For US industrial applications, adherence to ASTM B117 salt spray testing and AAMA 2605 performance standards is often required to ensure coating durability and quality. In such cases, surface flaws can significantly shorten the component’s lifespan.
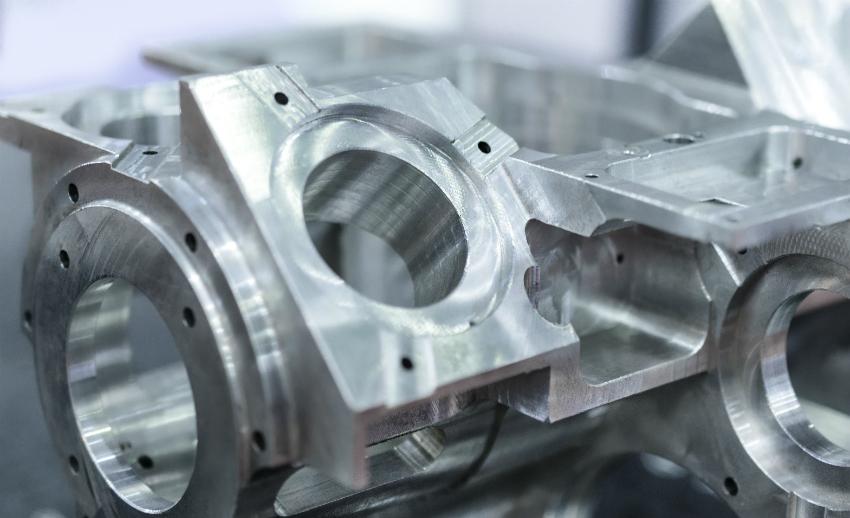
Depending on the size and application of the part, aluminum pretreatment can be conducted in different ways.
Mechanical Surface Treatment
Mechanical processing removes unwanted surface deposits such as scale, stubborn dirt, soot, and the naturally occurring aluminum oxide layer. Common methods include sanding, brushing, or abrasive blasting (e.g., sandblasting). Tools can range from manual sandpaper to orbital sanders and fixed grinding machines. Sandblasting is often used in industrial settings to clean off oxide residues. These mechanical treatments roughen the surface slightly, improving paint adhesion. Typically, mechanical cleaning is followed by a wash. Water-based cleaners remove loosely bound substances, while organic solvents eliminate oils and greases. The goal is a surface free of grease, which isa critical condition for proper paint adhesion. Ultrasonic cleaning is another option for removing more stubborn contaminants.
Chemical Surface Treatment
After degreasing, chemical processing typically follows. Acidic or alkaline pickling agents are used to dissolve the oxide layer while also roughening the surface—similar to the mechanical approach—to improve paint adhesion. Depending on whether the component is a flat aluminum sheet or a more complex part, the treatment can be applied using either a spray system or an immersion bath. Immersion is preferred for parts with holes or cavities, ensuring thorough coverage in hard-to-reach areas. Between each step, parts should be rinsed thoroughly with purified water, ideally in several successive baths, to remove all chemical residues and contaminants. Afterward, the surface must be dried completely before moving on to the painting stage.
Two Common Methods for Painting Aluminum in Industrial Settings
Depending on the part and performance requirements, different painting methods can be used.
Powder Coating: An Overview
Powder coating involves spraying a fine powder onto the aluminum part, where electrostatic forces come into play: the powder particles carry a negative charge, while the aluminum is positively charged, causing the powder to adhere to the surface. TElectrostatic forces temporarily bind the powder particles to the surface. The coated part is then placed in an oven and heated to around 390°F to 400°F (approx. 200°C). The powder coating contains pigments, a resin binder (such as acrylic or epoxy), and a hardener. As the temperature rises, the hardener and binder react to cure the coating, forming a solid, durable bond with the metal. Powder coatings are typically 2.4 to 4.7 mils (60–120 µm) thick, but thickness can vary.
Powder coating is often the method of choice when aluminum parts will be exposed to environmental stresses. In the US, these coating processes must comply with EPA National Emission Standards for Hazardous Air Pollutants (NESHAP) for surface coating of metal parts, which regulate volatile organic compounds (VOCs) and hazardous air pollutants. It is highly resistant to moisture, salt, and chemicals. Compared to wet painting, it is also more eco-friendly, since it eliminates solvent-based chemicals that evaporate during drying, using only the powder itself.
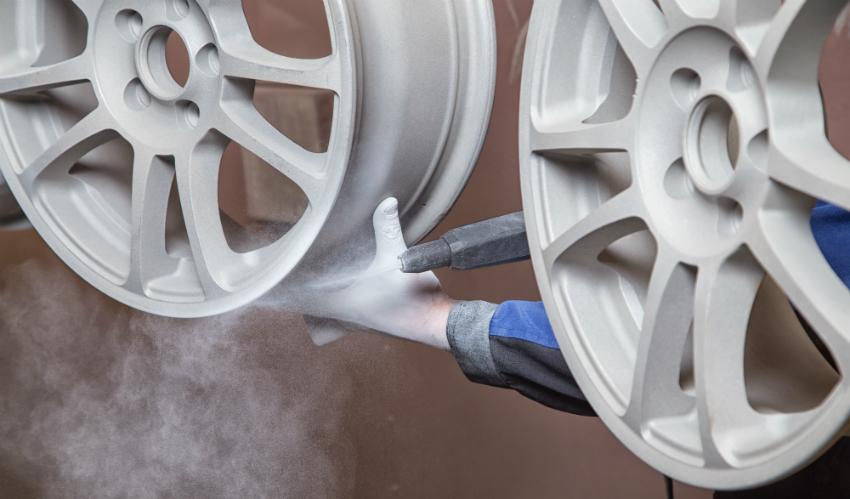
Wet Painting for Specialized Applications
For ultra-smooth finishes, powder coating is not ideal to utilize, as it results in a slightly textured surface. Alternatively, wet painting provides a smooth, uniform finish. The paint is applied as a liquid solution and then cures as the solvent evaporates.
Dip Coating, Curtain Coating, and Roller Coating
The are several other methods of paint application that are available. The paint can be applied using an immersion bath. In dip coating, the entire workpiece is submerged, fully wetted, and then removed. When using this method, it is important to ensure that no air bubbles form during immersion and that a uniform coating is achieved when the part is withdrawn. In curtain coating, the parts to be painted are transported on conveyor belts during the coating process. The transport speed can be adjusted while the paint is dispensed via a curtain coater—a vessel spanning the full width of the conveyor. This creates a “curtain” of paint that flows vertically down onto the workpiece. This method is ideal for flat objects—such as aluminum sheets.
Finally, the paint can also be applied to an aluminum part using rollers. A distinction is made between the application roller and the metering roller, which controls the amount of paint applied. This method can also be used to coat flat items, aluminum sheets, or even tin cans. Unlike powder coating, wet painting is not restricted by part size and is well-suited for large components such as aluminum sheets or coils.
Today, aluminum is often coated in color finishes that conceal its natural metallic appearance. This lightweight metal is widely used in industry, and when color is required, specific steps in the painting process must be followed to ensure a flawless and durable result.