The term “emulsion splitting” encompasses various methods applied in wastewater treatment. Emulsions are mixtures of liquids that do not dissolve into each other. Emulsifiers are necessary to create a stable emulsion. When it becomes necessary to separate the liquids, for example to recover valuable resources, reduce environmental impact or meet regulatory standards for wastewater discharge, emulsion splitting is used.
Emulsions in Everyday Life and Industry
The most well-known emulsion is milk, which consists almost entirely of water and fat. The emulsifier in milk is called casein, which keeps the fat droplets dispersed. Most people are familiar with the oldest method of emulsion separation which is butter churning. Here, mechanical forces break down the casein shells that enclose the small fat droplets, preventing them from clumping together. Larger fat clumps then form, leaving buttermilk behind. The most common method for creating emulsions is washing.
Greasy residues are difficult to remove with water alone, but with soap as an emulsifier, it becomes easy, though it leaves wastewater behind in the form of an emulsion. In wastewater treatment plants, emulsion splitting is used for water treatment. In metalworking, emulsions are used as cooling lubricants, combining the cooling effect of water and the lubricating effect of oil. This process generates large quantities of emulsion-laden wastewater, which will require emulsion splitting to recover the water.
Overview of Emulsion Splitting Methods
Emulsion splitting can be achieved through various methods: mechanical, thermal, chemical, electrochemical, and biological. The optimal method depends on the specific emulsifiers used and the other components in the emulsion.
Mechanical Methods
Mechanical methods for emulsion splitting include centrifugation and ultrafiltration. These methods use mechanical forces to neutralize the effect of emulsifiers in the emulsions.
In centrifugation, centrifugal force acts on the density differences between the components of the emulsion. On an industrial scale, this process is conducted in separators, which allow continuous operation, unlike centrifuges that require alternating loading and unloading.
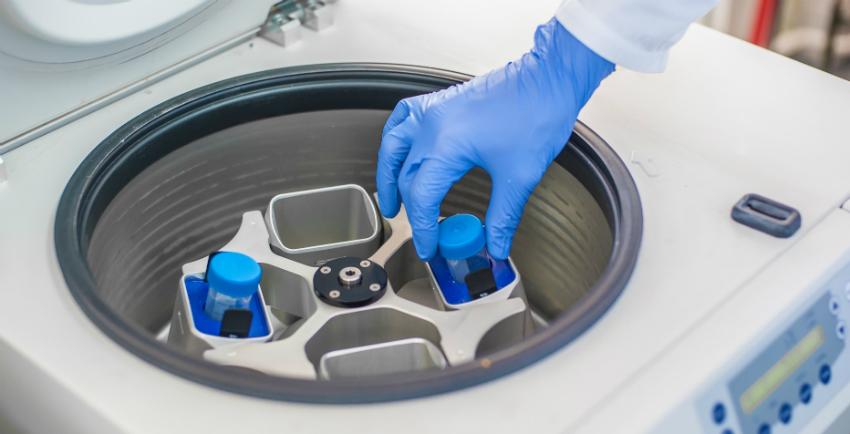
Ultrafiltration relies on high pressure to push water through a membrane, which retains the organic substances with large molecules. This method is only applicable to emulsions that are compatible with the membranes.
Thermal Methods
Thermal methods for emulsion splitting include distillation and adsorption.
In the distillation process, water is evaporated and then recovered as condensate. Despite different boiling points, some of the emulsified liquid also evaporates with the water. Any oil that enters the condensate with the vapor is then removed using mechanical separators. Evaporating water requires significant heat, but this heat is released again during condensation. In vacuum evaporation, this condensation heat is recovered for evaporation by maintaining different pressures in each sub-process, resulting in varying boiling temperatures.
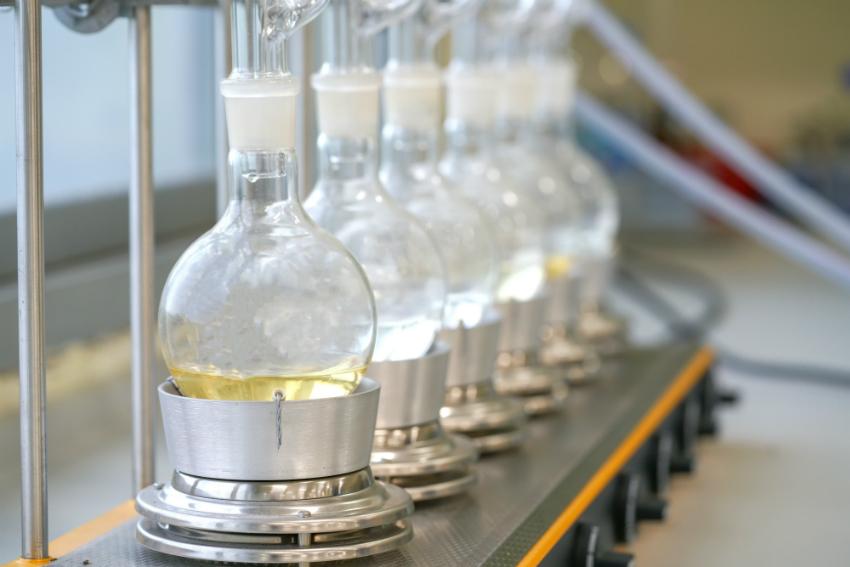
In adsorption, organic compounds form an emulsion and attach to solid materials such as activated carbon. This process requires low temperatures, categorizing it as a thermal method. There are two adsorption methods. One involves adding crushed activated carbon or specific oil-binding agents to the emulsion, which are then removed along with the organic matter. The other method is to let the emulsion pass through a device filled with an adsorbent that traps the oil.
Chemical Methods
Chemical emulsion splitting uses separation agents that either bind with or dissolve the emulsifiers and emulsified components. Strong acids or specialized organic separation agents are employed. Acids destroy emulsifiers, causing the oil droplets to clump together, a process known as coagulation or coalescence. Oil and water form two distinct layers that are then separated from each other in separators.
The drawback of this method is that the water must be neutralized afterward, resulting in significant sludge.
Special organic separation agents, known as demulsifiers, inhibit emulsifiers by chemically bonding with them or dissolving the emulsified substances. The resulting compounds or solutions float to the surface, forming a cohesive layer. Flotation agents are often added to facilitate and accelerate floating.
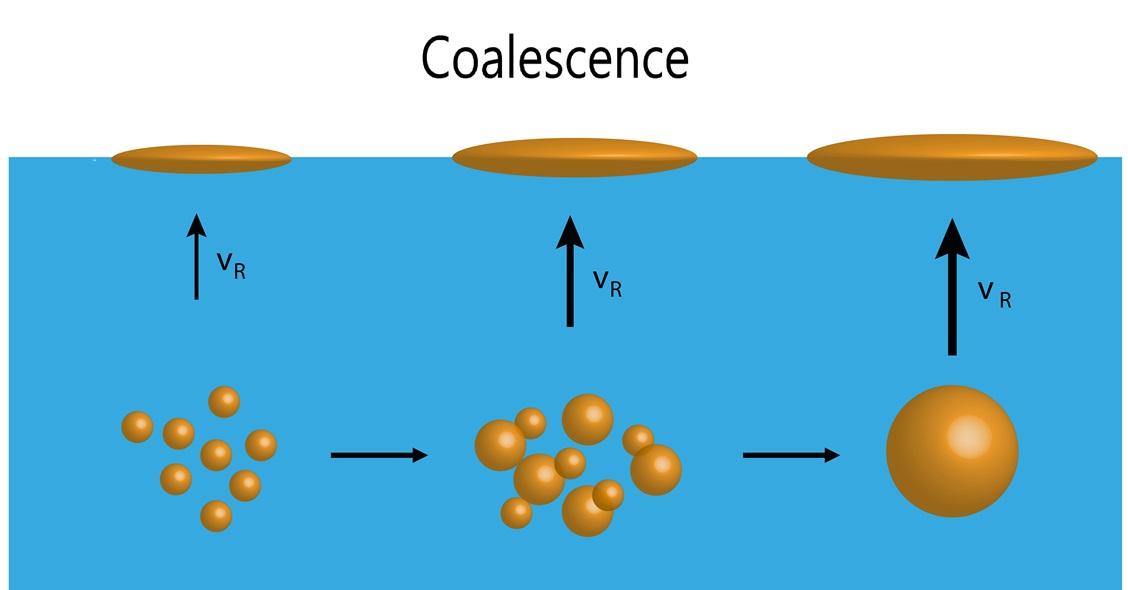
Electrochemical Methods
Many emulsifiers work based on electrical charges. In such cases, an electric field can be used to split the emulsion. Electrodes, charged with a direct current, are immersed in the liquid to create the electric field. Substances with opposite charges accumulate on the electrodes, forming separate layers through coagulation or coalescence that can then be isolated.
Biological Methods
Biological emulsion splitting relies on specially cultured microorganisms that feed on emulsified substances. The microorganisms are introduced to the emulsion, where, under optimal conditions, they grow and multiply. In settling tanks, they gather at the bottom as biomass, forming what is known as activated sludge. For this method to be effective, the emulsion must not contain biocides harmful to microorganisms. Biological emulsion splitting is often used in wastewater treatment plants.
Water Treatment in Emulsion Splitting Plants
Emulsion separation systems are frequently part of wastewater treatment technology, where a distinction is made between decentralized and centralized treatment. Decentralized emulsion splitting systems are operated by companies aiming to reduce waste and to reclaim process water. In centralized plants, large volumes of wastewater, collected by disposal companies or generated in treatment plants, are processed.
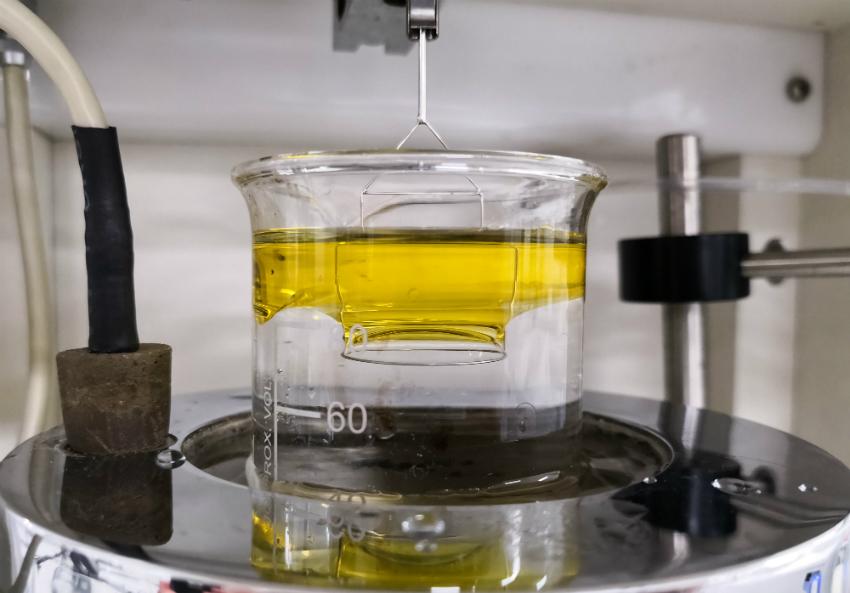
Decentralized Emulsion Splitting Systems
A decentralized emulsion splitting system is a compact unit with sections for emulsion splitting and separation of the lighter layer. Thermal and chemical emulsion separation methods are commonly applied here. Vacuum evaporators, available with capacities ranging from a few liters to several cubic meters per hour, are used for thermal splitting. Chemical systems using demulsifiers offer similar capacities. Separators, following emulsion splitting, divide the liquids into two phases: one containing organic compounds, the other water.
Centralized Emulsion Splitting Systems
In centralized water treatment facilities, the emulsion splitting unit is incorporated into a network of liquid storage tanks, energy supply systems, settling tanks, and control and regulation components. Managing large liquid volumes is more energy-efficient than decentralized treatment.