Professional surface treatment significantly increases the lifespan of components. The chosen method depends on the base material and the desired effect. Among the most essential techniques in this field are electroplating and anodizing. While both use electricity and can serve both protective and decorative purposes, their similarities end there.
Surface Coating with Electroplating
Electroplating uses electrical currents to deposit metal uniformly on workpiece surfaces. The resulting metal layer typically serves to protect against mechanical wear, as corrosion preventative, and/or improve electrical conductivity. Additionally, electroplating can simplify further processing or achieve aesthetic changes.
This technique is frequently applied to steel or stainless-steel components, employing metals with properties suited to the application, such as:
- Copper
- Zinc
- Tin
- Brass
- Nickel
- Silver
- Gold.
Electroplating is not limited to metallic objects; it can also be applied to materials like plastics, ceramics, and glass. . These materials are pre-treated with conductive coatings, chemically applied metal layers, or metal seeds to enable electroplating. Common coating materials used in this process include chrome, copper, zinc, and nickel.
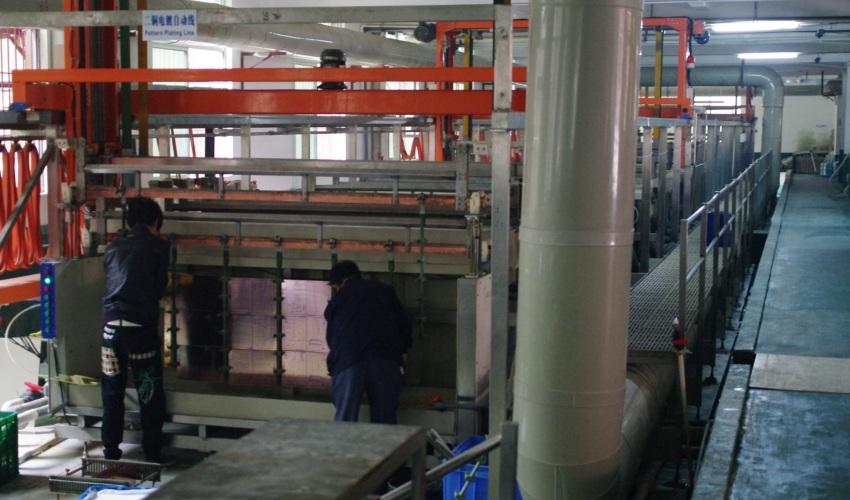
Surface Modification with Anodizing
Eloxal is the abbreviation for ‘electrolytic oxidation of aluminum’. The term itself indicates that only aluminum can be anodized. This lightweight metal naturally forms a thin but dense oxide layer under oxygen exposure, providing some resistance to corrosion. However, natural protection is limited, especially in the presence of substances like salt or sulfur dioxide and does not prevent wear.
Anodizing enhances the aluminum’s surface by creating a nearly pore-free dielectric barrier layer, topped with a finely porous, honeycomb-like outer layer. While natural oxide layers are only a few nanometers thick, anodized layers can reach up to 25 micrometers, making aluminum components suitable for harsh industrial conditions and marine environments. The porous structure also allows aluminum to be dyed, particularly when using pure aluminum alloys with a magnesium content below 4%.
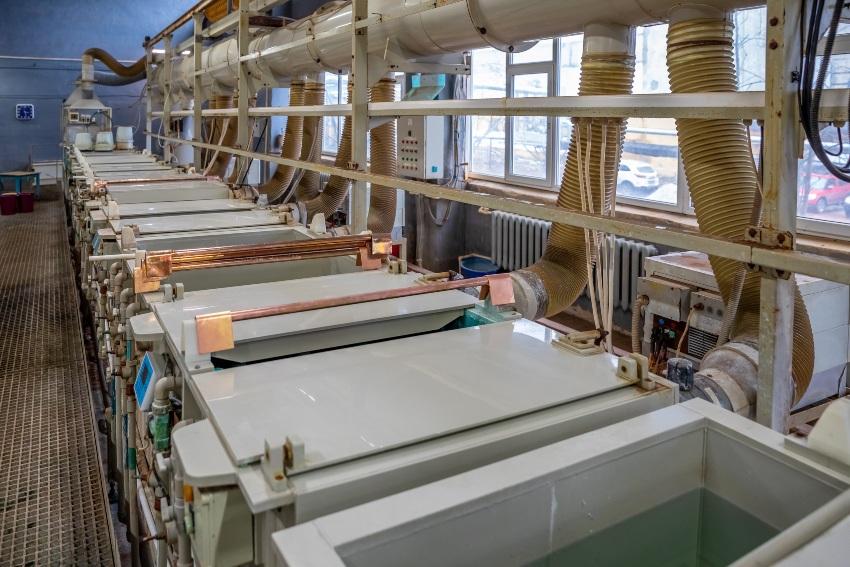
Electroplating Process Steps
Depending on the size of the workpiece and specific requirements, different electroplating techniques can be employed. For oversized components that cannot be treated in an electroplating bath, alternatives like dip plating or brush plating are used. In brush plating, the electrolyte is applied under voltage with a sponge.
Other techniques include:
- Barrel plating
- Chemical plating
- Strip plating
The electroplating process generally follows three main steps:
1. Pretreatment
Mechanical and chemical processes remove oils, greases, rust, scale, chips, and grinding dust from the workpiece surface. Multiple rinsing steps follow to ensure a completely clean surface. The pretreatment is completed with several rinsing processes that ensure an absolutely clean surface.
2. Coating
The workpiece is immersed in an electrolyte solution containing the desired metal. Connected to a DC power source, the workpiece acts as the cathode, while the metal anode serves as the source of positive ions. When the current flows, metal ions from the anode deposit onto the workpiece. The duration in the bath and the current strength determines the thickness of the coating.
3. Post-Treatment
After electroplating, the workpiece is rinsed and dried. Additional steps, such as passivation or chromating (e.g., for zinc-plated steel), may be added.
Anodizing Process Steps
Unlike electroplating, anodizing does not add a coating but transforms the surface layer of aluminum. The anodizing process involves four steps, followed by coloring as an optional fifth step.
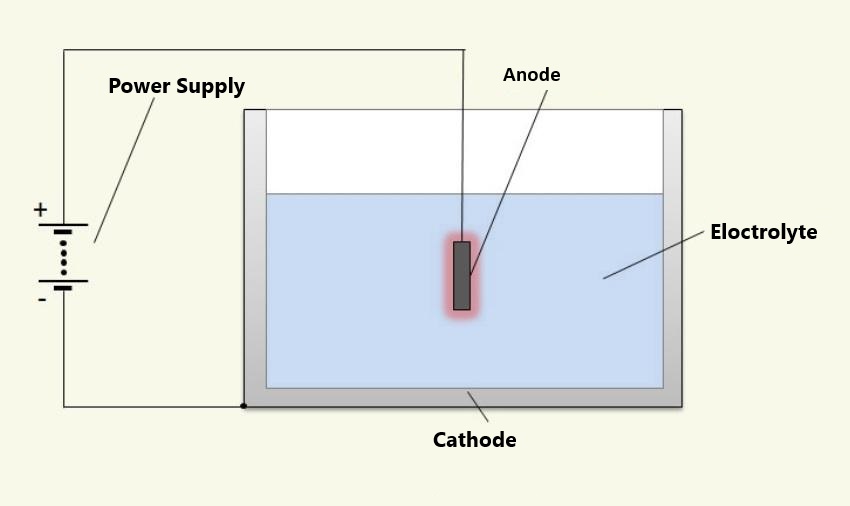
1. Pretreatment
As with electroplating, this step ensures a grease- and dust-free surface. For components with high aesthetic demands, chemical pretreatment can smooth surface irregularities through pickling.
2. Anodic Oxidation
Aluminum parts are submerged in an electrolyte solution (sulfuric or oxalic acid) with the workpiece connected as the anode to a DC power source. Lead or titanium plates, unaffected by the electrolyte, are used as cathodes. When the current flows, water at the cathode decomposes, releasing hydrogen, while oxygen reacts with the aluminum to form the oxide layer. The longer the process, the thicker the protective layer, forming capillary-like pores.
3. Coloring (Optional)
The pores created during anodic oxidation can absorb dyes. Since the color embeds within the pores rather than sitting on the surface, it is highly durable and abrasion resistant.
4. Sealing
After anodizing, the open pores are sealed by boiling the aluminum in demineralized water. This causes the aluminum oxide to react with water, forming aluminum oxide hydroxide. The pores swell from the edges toward the center, closing completely.
Pros and Cons of Electroplating
Electroplating is a cost-effective method offering extensive coating options. It provides excellent corrosion protection and enhances the visual appeal of workpieces. However, the process generates precipitation sludge containing concentrated chemicals, which must be disposed of properly to prevent environmental harm.
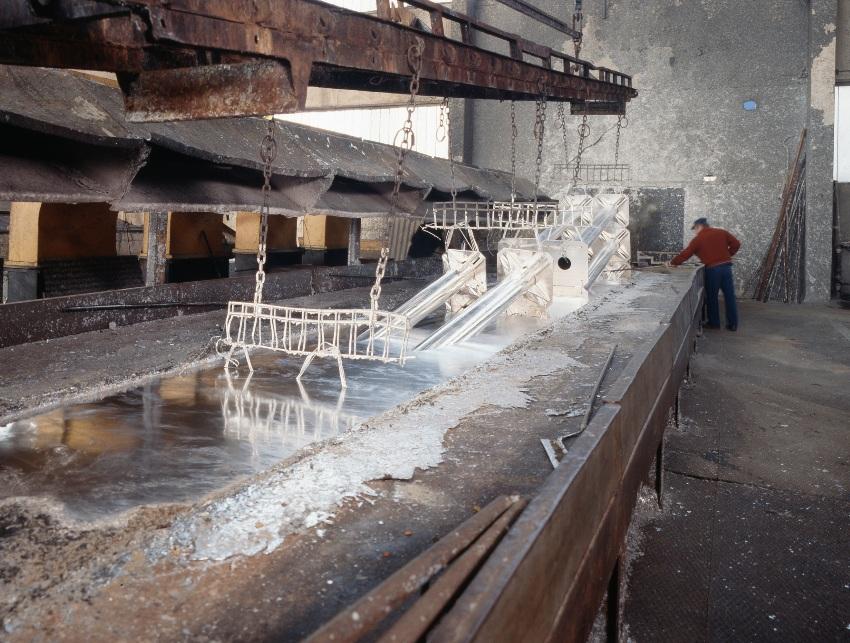
Pros and Cons of Anodizing
Like electroplating, anodizing creates a durable, corrosion-resistant surface. Anodized aluminum can achieve hardness levels between 200 and 400 HV, and even up to 600 HV with hard anodizing. The process also allows for vibrant, long-lasting coloring. However, anodizing is limited to aluminum components.
Anodized aluminum’s non-conductive protective layer cannot be easily re-anodized without first removing the oxide layer through pickling. This can alter the dimensions of precision components, potentially rendering them non-compliant with specifications.