« Effectively Preventing and Removing Surface Discoloration »
Colored metallic surfaces are often desirable. For instance, steel does not have to just be shiny silver; it can be colored through sophisticated processes to almost any hue, including green, blue, red, gold, and even blackened steel. Additionally, layering multiple tones to create an iridescent effect that changes color depending on the viewing angle is technically feasible. However, some discolorations are unwanted, like brown discolorations on chrome steel or greenish tints on tinned copper surfaces. These do not necessarily damage the metal but can be unsightly. Similar discolorations can also occur on plastic surfaces, negatively affecting their overall appearance.
How do discolorations of metal and plastic surfaces occur?
The processes responsible for discolorations of metal and plastic are quite varied. It is essential to consider the chemical properties and the chemical reactions involved to properly identify the cause, prevent future discoloration, and potentially restore affected surfaces.
Metal discolorations due to oxidation
The color of metals can be altered by oxidation processes at the surface. These so-called temper colors form as oxygen atoms penetrate the metal surface to varying depths, determined by the temperature during the oxidation process. For example, steel exposed to temperatures around 932°F (500°C) turns gray, while paler yellow hues suggest lower temperatures around 392°F (200°C). Other metals, like titanium, can also display a range of colors through temperature-dependent treatments. However, oxidation processes that occur at room temperature, often involving atmospheric oxygen or other compounds, are usually undesirable. Rust that has formed on iron, for example, not only gives it a reddish tint but also negatively affects its material properties, potentially leading to the complete degradation of the iron. Another example is the tarnishing of silver, which is caused by sulfur compounds leading to a black silver sulfide coating.
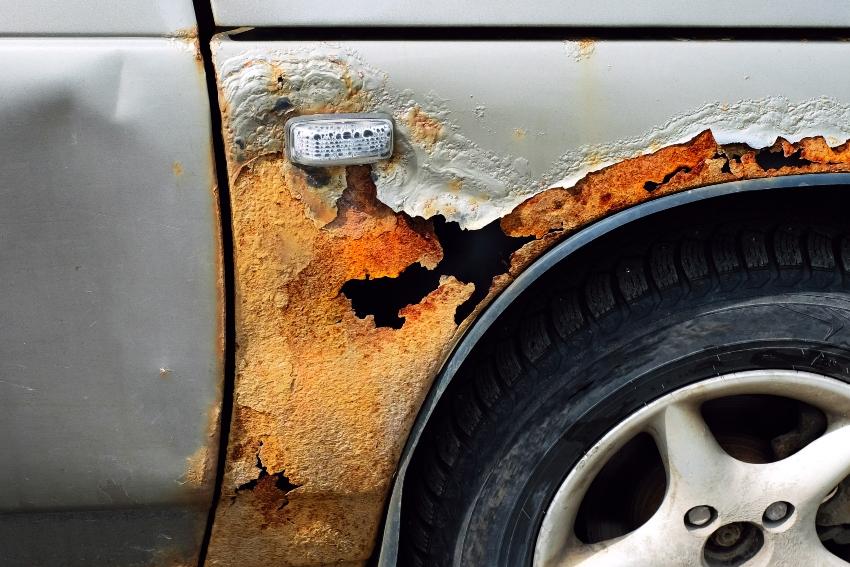
How can metal surface discoloration be effectively prevented?
Since surface discoloration arises from oxidation and it needs to be prevented. This is typically achieved through the application of coatings, including:
- Polymer-based coatings such as polyurethanes (used as primers due to their excellent adhesion properties)
- PVC coatings
- Oils, varnishes, and hard paraffins
Using multiple types of coatings can enhance protection. Sometimes, oxidation processes on metal surfaces are desired and used as protection against corrosion and accompanying discoloration. This includes processes like galvanizing or chroming of metal parts, where the formation of an oxide layer is promoted to protect the underlying metal from further unwanted corrosion and discoloration.
Methods to remove metal discolorations
Despite all protective and coating measures, unwanted metal discolorations can still occur, particularly on parts exposed to the elements, like on building exteriors. Examples include rusted rain gutters or reddish brown discolorations on stainless steel railings. Removal can be done mechanically or chemically. Grinding can remove unwanted discoloration, but it is important to avoid creating localized heat, which could further damage the metal surface.
An alternative method is blasting the surface, which effectively removes discolorations while generally leaving an exceptionally smooth and clean metal surface. Careful brushing with a stainless steel or brass wire brush can also completely remove surface discolorations. Tinned copper used in outdoor areas of buildings can turn green under the influence of road salt in the winter. Brushing off the discoloration is simple and should be followed by applying a protective layer, such as bitumen or clear coat, to prevent recurrence.
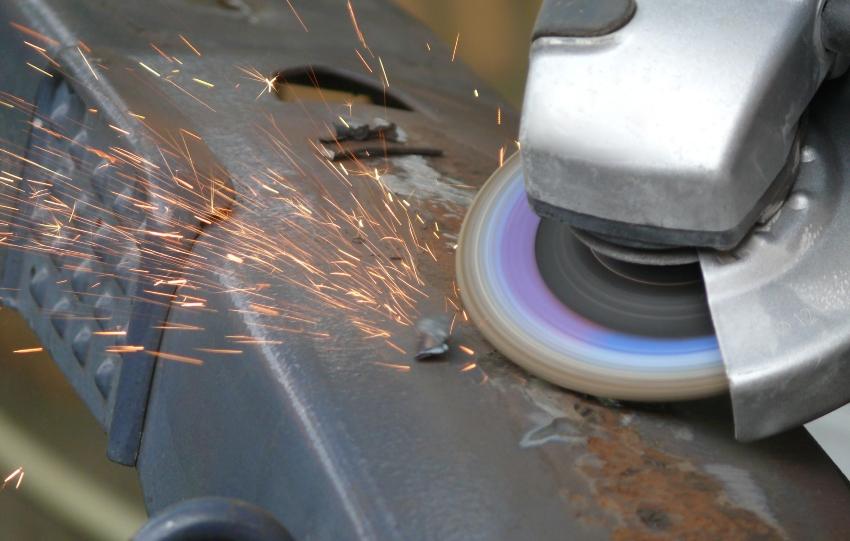
Metal discolorations can also be removed chemically. The “pickling of metals” is nothing more than etching the surface with acids or alkalis. Different pickling agents are used depending on the metal. This should be considered when selecting the appropriate pickling agent. However, sometimes less aggressive chemicals are sufficient, meaning mildly acidic or mildly alkaline cleaning agents. These are sprayed onto the surface and either rinsed off with water or wiped off with a cloth. This is commonly known in private households from cleaning tarnished silverware. In the industrial sector, specially tailored industrial cleaners are used.
Plastic discolorations and their causes
Fading of plastic products is a common issue. Direct UV radiation can partially destroy the polymer chains in plastic, leading to brittleness. UV light also affects the pigments and dyes in plastic, partially degrading them. Indirect UV exposure can have similar effects. However, other factors can contribute to discolorations in plastics, sometimes even baffling the experts. For instance, in the automotive industry, it was discovered that light-colored components could discolor under the influence of daylight, only to revert to their original color after a few days. This is suspected to be due to interactions among various additives, colorants, and light stabilizers in the plastic, as plastic is rarely a pure polymer.
Plastics contain additives, plasticizers, or redox-active metal particles, which may also be impurities from production. Under environmental influences, these particles also react with each other or are destroyed, as mentioned above. Finally, other external factors can also lead to discoloration. When metal dust, for example iron dust, settles on PVC windows, it can react with the PVC with the help of sunlight, resulting in unsightly yellow spots. The use of aggressive cleaning agents can also cause damage. Industrial cleaners in particular are often offered as concentrates. If you do not follow the prescribed dilution and instead use a concentration that is too high, this can have serious consequences. For example, the plastic PVC can be attacked by ammonia or benzyl alcohol present in a cleaner if these ingredients are dosed too highly.
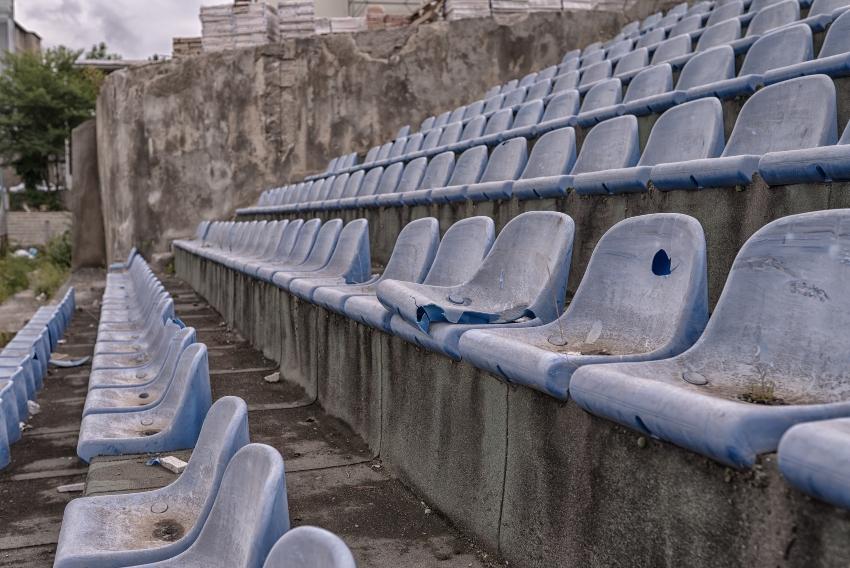
Protection and care from the start
For plastic surfaces, as with metal, a protective layer is crucial. There are special care products that penetrate and effectively “encapsulate” plastic. Additives, like light stabilizers in the plastic product itself or in the protective layer, shield against UV radiation. The best approach is, of course, to avoid direct UV exposure altogether.
Regular cleaning of surfaces is crucial, as shown by the effects of iron dust on PVC surfaces. The selection and correct application of cleaners are essential to avoid unpleasant surprises, especially with industrial cleaners, which often have different compositions than typical household cleaners.
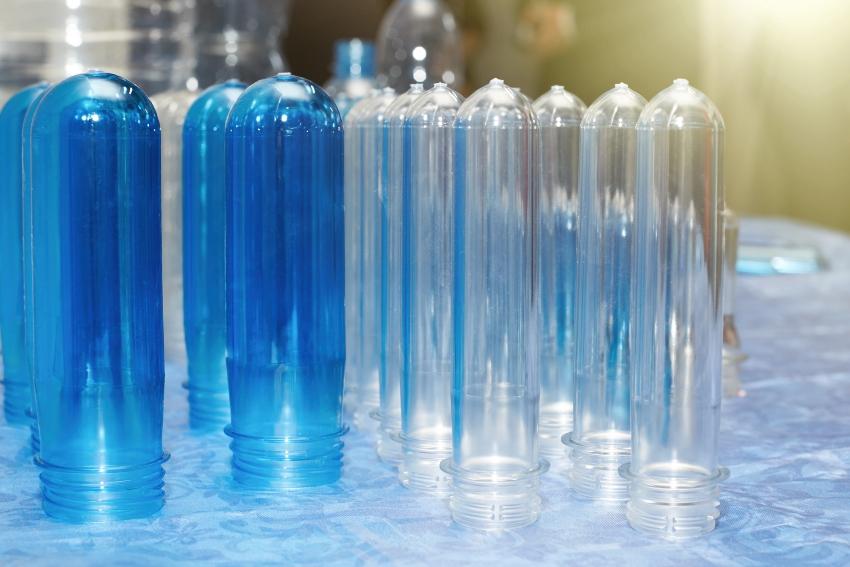
Removing and preventing future discolorations on plastic surfaces
As with metals, plastics can be treated chemically or mechanically. Mechanical cleaning of plastic can be done with careful sanding. After treatment, the material should be sealed with a protective layer. Chemical treatments must be very carefully applied and specifically tailored to plastics, utilizing special industrial cleaners available for this purpose.