We are surrounded by products made from diverse materials and shapes. Manufacturing processes transform raw materials like metal or plastic into semi-finished products such as bars, tubes, and sheets. These intermediate forms are then processed further to create finished products, from simple tin cans, to precisely engineered automobile components.
Manufacturing technology employs a wide array of processes
Manufacturing technology encompasses a diverse range of processes. In manufacturing facilities, metalworking methods are typically categorized into several main groups: primary forming (creating initial shapes through processes like casting molten steel), material removal (machining operations that cut away material), joining (connecting parts through welding or bonding), surface treatment (applying protective coatings like paint or zinc plating), and deformation (reshaping materials through processes like bending or pressing). Each category represents distinct ways in which raw materials are transformed into finished products, from basic components to complex machinery parts.
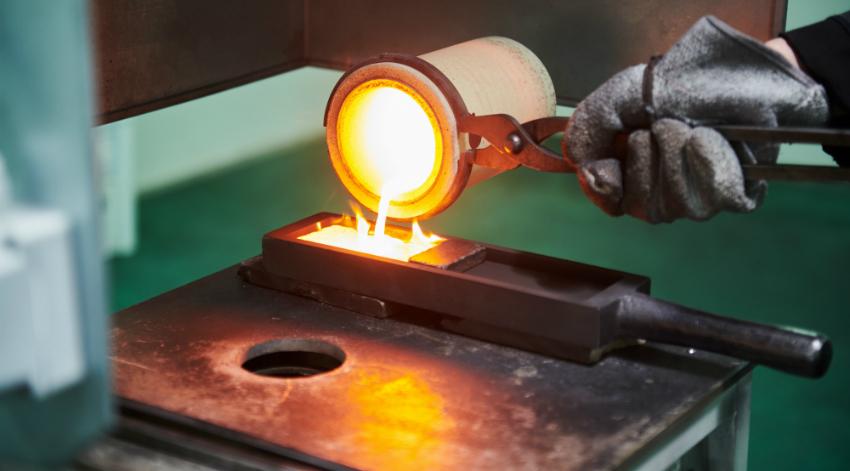
Machining and forming processes are two critical manufacturing methods
Machining processes involve deliberately removing material from a workpiece’s surface, which creates small pieces of waste material called ‘chips’. This removal happens during operations like drilling, milling, or sawing in both wood and metalworking. Forming, by contrast, shapes materials without material loss through processes such as rolling, deep drawing, or bending. The process occurs at different temperature ranges: hot forming (above recrystallization temperature, where the metal becomes soft enough to be easily reshaped), semi-hot forming, and cold forming (below recrystallization temperature, where the metal remains relatively rigid). The choice between these methods depends on the desired properties of the final product.
Both machining and forming processes involve various forces—some are intentional, like workpiece deformation in forming, others are unwanted, like mixed friction in machining. Although friction inevitably generates heat, excessive friction and heat can damage machines and compromise the workpiece’s surface quality. Proper chip removal is also crucial to protect both the workpiece surface and the tool.
Coolants and lubricants have various roles
Coolants and lubricants serve multiple essential functions: they reduce friction between the workpiece and the tool, dissipate heat, and wash away chips to protect both tool and workpiece surfaces. Additionally, they provide crucial corrosion protection across all processing methods, helping to minimize tool wear.
Water-miscible or non-water-miscible?
Cooling lubricants are categorized as either water-miscible or non-water-miscible, with each category offering products tailored with specific additives for different manufacturing processes.
Non-water-miscible cooling lubricants
These kinds of cooling lubricants use mineral oils as their base, ranging from low to high viscosity. Performance is enhanced with additives, such as synthetic or natural fatty substances such as palm oil) that improve surface adhesion by creating a lubricating film (metal soap) at the friction interface. Additional compounds provide corrosion protection, extend coolant life, and prevent foam formation.
The choice between low-viscosity and thicker coolants depends on both the process and the metal being machined. Low-viscosity oils, often referred to as unalloyed cutting oils, suffice for easier-to-machine metals and grinding operations, typically requiring no additives. More demanding processes like drilling, milling, or turning require medium to high-viscosity cooling lubricants containing EP (extreme pressure) additives. These additives, which include compounds of sulfur, phosphorus, zinc, or nitrogen that enhance pressure stability. While their exact mechanism remains unclear, adsorption layer theory suggests these additives form a protective layer that absorbs pressure and reduces friction, preventing surface welding under high pressure. Such coolants excel in both demanding machining operations and forming processes where high pressure is essential.
Water-miscible lubricants
These lubricants are available in two forms: emulsifiable and water-soluble. These lubricants combine mineral or synthetic oils with 80-98% water, and include emulsifiers for stability. Some lubricants use polyglycol-based synthetic oils, while others incorporate mineral oil bases. Their formulations also contain additives that enhance lubrication, prevent corrosion, and control foam. Such water-miscible cooling lubricants are ideal for machining operations that require optimal cooling efficiency.
Overall, non-water-miscible coolants are used when reducing friction is the focus and the lubrication effect is paramount. Conversely, when cooling is a priority, especially in extremely fast processing operations like machining, water-miscible coolants are preferred.