Metalworking facilities and auto repair shops often have a distinctive aroma of oil . When machines reach high temperatures, there is also a noticeable smoky odor. Any substance you can smell is present in the air and, therefore, can be inhaled into the lungs. Prolonged exposure to substantial amounts of oil vapors, oil mist, and oil smoke can pose significant health risks.
How Oil Vapors, Mist, and Smoke Form
Thermal Mist Formation
Liquids evaporate into vapors that disperse into the atmosphere. The rate of this process depends on the vapor pressure, which is temperature dependent. For instance, at 68°F (20°C), water has a vapor pressure of 23.4 mbar (0.34 PSI). At 140°F (60°C), this increases to 199.2 mbar (2.89 PSI). Most oils used in metalworking have a much lower vapor pressure, typically less than 0.1 mbar (0.0015 PSI) at room temperature.
Air pressure fluctuates around 1,000 mbar (14.5 PSI), and this pressure is shared with also influences and includes vapors rising from liquids. When the maximum vapor concentration is reached, the air becomes saturated. If the temperature drops, the vapor condenses into tiny droplets, forming oil mist.
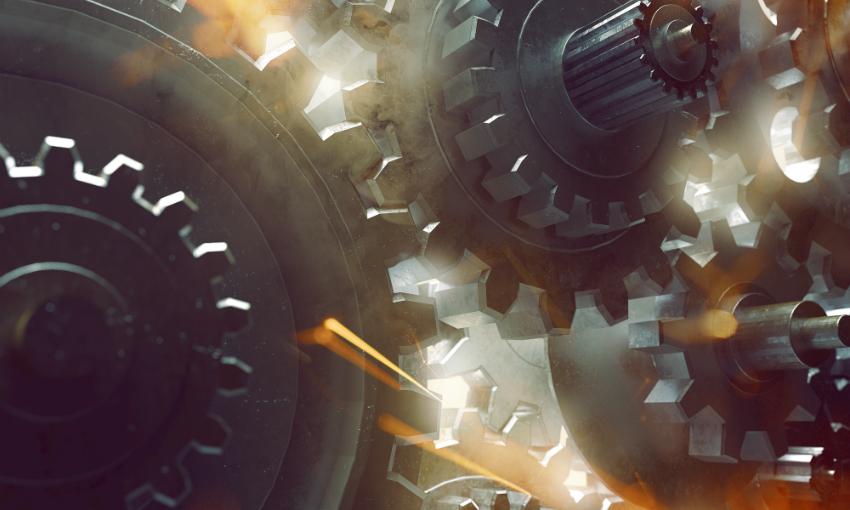
When a liquid reaches its boiling point, it vaporizes. Metalworking coolants (cutting fluids) boil at around 212°F (100°C), a temperature often attained during machining processes like turning, milling, and especially grinding when cooling is inadequate. The vapor quickly cools in the atmosphere, leading to the formation of oil mist in oversaturated air.
Mechanical Mist Formation
Oil mist can also form through mechanical means, such as spraying or atomization. In metalworking, rotating tools or workpieces can propel cooling lubricant drops throughout the workspace. Additionally, using compressed gas to clean parts immediately after machining releases fine oil mist. Other sources include bursting foam bubbles and oil-laden compressed gas emissions.
Formation of Oil Smoke
Oil smoke occurs when mineral oils heat up on hot surfaces to the point where they decompose. This process is called pyrolysis. Highly flammable gases and solid particles are produced. When they begin to burn, the smoke development intensifies. Light gray smoke turns black due to the soot that forms.
Health Risks of Oil Mist and Smoke
The primary health concerns associated with oil mist and smoke stem from additives found in metalworking fluids, such as emulsifiers, preservatives, and defoamers. Additionally, oil droplets can collect dust and metal particles, creating aerosols. These particles, sometimes only a few nanometers in size, can penetrate deep into the lungs when inhaled. To mitigate these risks, the Occupational Safety and Health Administration (OSHA) and industry best practices recommend protective measures, including emission reduction, air quality monitoring, and minimizing exposure to metalworking fluid emissions.
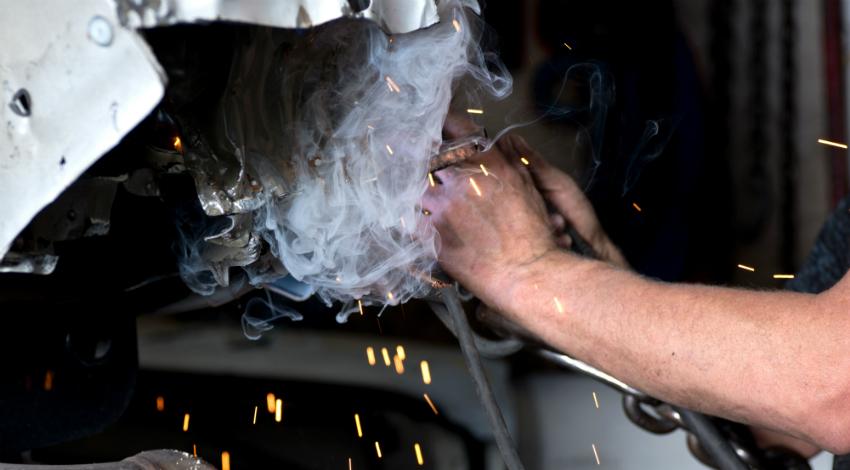
Air pollution limit values
Air Quality Limits set by OSHA and related industry regulatory guidelines suggest oil mist and vapor emissions to maintain workplace safety.
Recommended exposure limits include:
- Water-miscible metalworking fluids: 10 mg/m³
- Non-water-miscible forming lubricants: 40 mg/m³
Non-water-miscible metalworking fluids:
- Flashpoint above 212°F (100°C): 10 mg/m³
- Flashpoint below 212°F (100°C): 100 mg/m³
If workplace air quality stays within these limits, significant health risks are unlikely.
Reducing and Preventing Emissions
Regular Maintenance of Metalworking Fluids
Routine monitoring and maintenance of cutting fluids is essential to minimize air contamination. This practice includes checking fluid levels, ensuring effective filtration, and proper storage conditions.
Maintaining Low Temperatures
Keeping fluid temperatures as low as possible is essential. According to industry guidelines (such as VDI 3035 in Europe and similar ASHRAE standards in the US), most machining processes should not exceed 104°F (40°C). This requires using sufficiently large coolant reservoirs that are cleaned regularly. After cleaning, systems should be flushed to prevent residual detergent from causing foam formation, which can hinder heat dissipation.
Careful Handling of Workpieces
Workpieces coated with metalworking fluid should only be blown off with compressed air if safety enclosures are in place. This could be a fully enclosed machine, or a dedicated work area equipped with an exhaust system. Additionally, parts should not be allowed to air dry in the immediate workspace, as this can release additional mist. The same procedures apply to metal chips.
Eliminating Unnecessary Emission Sources
Using enclosed machining systems significantly reduces emissions. Coolant containers, chip bins, and used cleaning cloths should all be covered whenever they are not in use. Any spilled cutting fluid should be cleaned up immediately, and leaks in piping and storage tanks must be sealed.
Engineering Controls to Improve Air Quality
If basic measures are insufficient, technical solutions are required to maintain air quality. These include adequate workshop ventilation and local exhaust systems.
Facility Ventilation
A well-designed and professionally installed ventilation system is crucial for ensuring proper air exchange. Ventilation system designs should comply with ASHRAE (American Society of Heating, Refrigerating and Air-Conditioning Engineers) standards for industrial air quality. Professional engineering firms should be consulted to design and maintain these systems to meet airflow and filtration requirements.

Machine and Equipment Exhaust Systems
Local exhaust systems capture contaminants at the source before they disperse into the workplace. Due to environmental regulations, extracted gases should be filtered before being released outside. Various separation technologies are available for removing oil mist and particles, but oil vapors are harder to remove. This is why recirculating ventilation systems, which return filtered emissions to the facility, are not recommended as oil vapors can accumulate in the workspace.
For the separation of oil mists, filters, coalescing separators, or electrostatic precipitators are used. Inside the filters, filter fleece or filter mats retain the contaminants. Coalescing separators are equipped with a fine fiber structure where microscopically small droplets merge, drip off, and collect at the bottom of the device. In electrostatic precipitators, the contaminants are electrically charged. Subsequently, an electric field directs the particles to collection plates, where they accumulate and drain downward.