« Abrasive Wear Causes and Countermeasures »
Wear occurs whenever materials degrade through use. Abrasion is a specific form of wear that results from what is known as micro-cutting. High abrasiveness significantly reduces the service life of machine parts, places undue stress on materials, and leads to shorter maintenance intervals. To prevent this, here’s what matters most.
What Does “Abrasive” Mean?
The term abrasion comes from Latin and literally means “scraping off.” It describes the removal of material through grinding or rubbing. Materials experts refer to a substance as abrasive when it causes a grinding or rubbing effect that results in smoothing, cleaning, or wearing away of metals or other materials. In practical terms, this often applies to abrasives used to grind or polish surfaces. However, lubricants such as oils or greases can also develop unwanted abrasive effects, which must be avoided during machine operation. This kind of wear increases strain on individual machine parts and often results in expensive maintenance. By simply switching to a different lubricant, such wear can often be reduced. The choice of the right cooling lubricant or forming lubricant has a significant impact on the service life of moving parts. Abrasive, as well as adhesive wear, is one of the leading causes of failure in machines with moving components.
What Happens When a Lubricant Becomes Abrasive?
Lubricants can contain hard particles that impair their lubricating properties. Low-quality oils or greases, especially those used over prolonged periods, tend to form clumps that interfere with lubrication. When such particles—or microscopic surface roughness—penetrate the outer layer of a material, abrasion occurs. Under the microscope, characteristic signs of micro-cutting can be seen, such as tiny scratches or grooves. This is also referred to as furrow wear. It occurs gradually and often goes unnoticed at first.
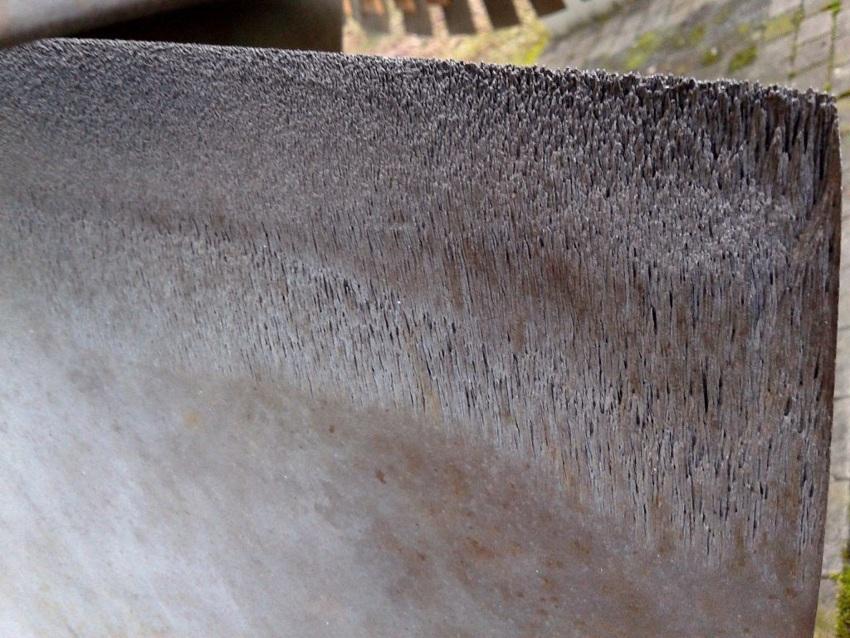
Much like a cave carved by water and wind over millennia, abrasive wear can take time to become noticeable. Highly stressed machine components like gears, roller bearings, or needle bearings are significantly affected. Choosing an appropriate lubricant is essential for maximizing the lifespan of interacting parts. Even hardened machine components such as gears or bushings are subject to abrasion. However, using high-grade lubricants can significantly extend service life and reduce maintenance and repair costs.
When Does Abrasive Wear Occur?
There are several common causes of abrasion-related wear. It typically occurs during machine startup or under sudden load changes. At low speeds, lubricants often fail to form a protective layer between components. This is especially true in sump-lubricated systems, which only function effectively once the gearbox is running. Not all gears are fully submerged in oil; only once the parts are in motion does the lubricant spread across all gears, shafts, and related components. Until the machine reaches an effective operating speed, the oil’s viscosity is not enough to prevent abrasion.
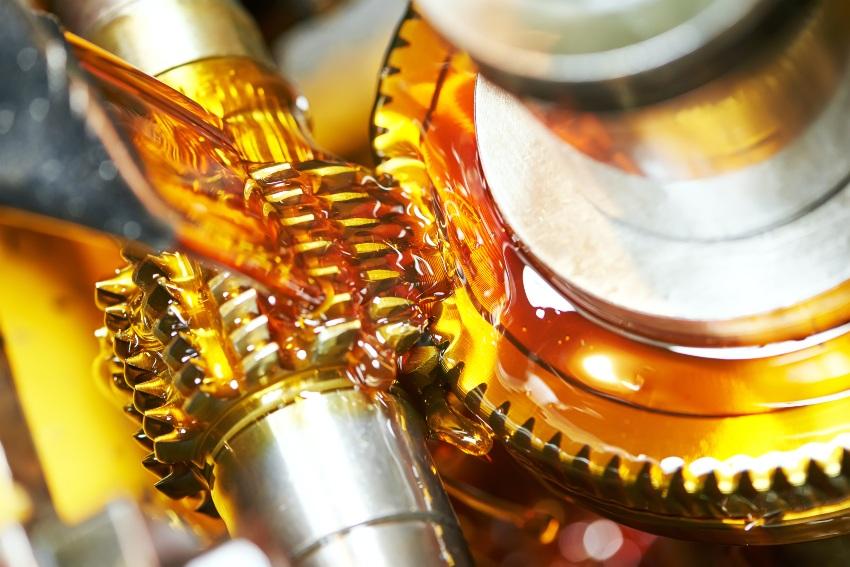
When Is a Lubricant Abrasive? Viscosity Matters
The viscosity of a fluid determines how thick or thin it is. Simply put, viscosity indicates how readily a fluid flows. This allows for a direct comparison of different liquids and their lubrication properties. Using a lubricant with too low a viscosity can lead to excessive wear. If the oil is too thin, it cannot form a sufficient separation layer between moving components. Even when gears appear to mesh perfectly, a proper lubricant ensures that the metal surfaces do not rub directly against each other. A thin oil or grease layer protects the material and prevents premature degradation.
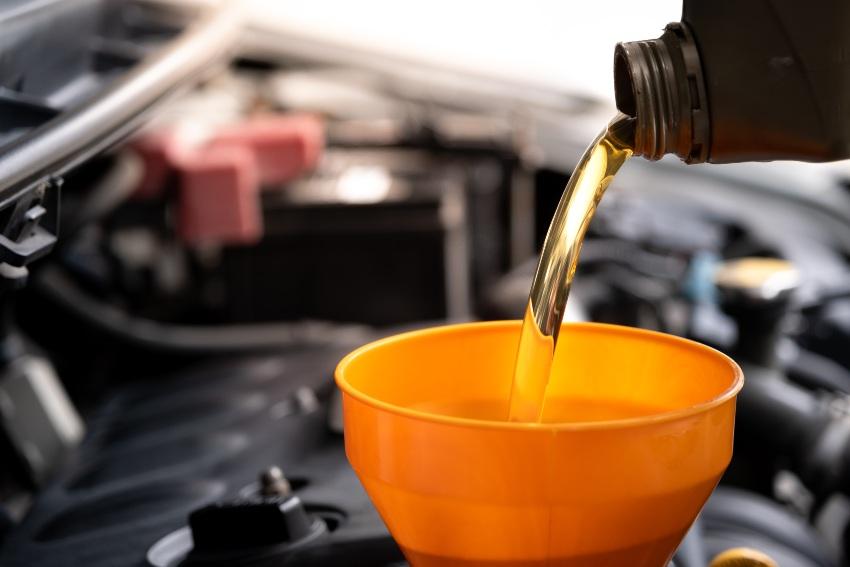
Abrasive wear can be significantly reduced by using additives in oils. These additives help protect surfaces in boundary lubrication situations—especially when the oil film begins to break down. High operating temperatures can also reduce an oil’s viscosity. When separation between moving parts is inadequate and the lubricant behaves abrasively, anti-wear additives offer critical short-term protection.
Abrasive Wear Caused by Particles in Lubricants
Another common occurrence—even in already lubricated machine parts—is the presence of hard particles in oil or grease. These microscopic particles are roughly the same size as the lubrication film intended to protect the metal surface. Because of their size, they can enter the narrow gap between moving parts and can compromise the lubricant’s effectiveness.
Detecting Abrasive Wear
To determine whether a machine is suffering from abrasive wear, a visual inspection is the first step—but microscopic damage is usually invisible to the naked eye. In such cases, an oil analysis provides clarity. This test can detect foreign particles in the lubricant and indicate whether it is time to change the oil.
Preventing Abrasive Wear
Even during the design phase of a machine, abrasive wear can be minimized by selecting appropriate material pairings. Combining metals with plastics, ceramics, or other materials can reduce surface abrasiveness significantly.
Oils should also be filtered before being filled into the system. Continuous filtration during machine operation is also highly recommended. Oil change intervals must be strictly followed, and only certified, high-quality lubricants suitable for the machine’s operational loads should be used. New equipment should undergo system flushing before commissioning to remove foreign materials and even the smallest particles. Seals and access points should remain closed to prevent contaminants from entering the system.