« Using Defoamers in Industrial Applications »
Foam formation is a common issue in many industrial systems. In such cases, defoamers are needed to either suppress or prevent foaming altogether. This article offers an overview of how foam forms and how foam control agents work.
Foam Formation in Liquids
Foam consists of gas bubbles surrounded by thin membranes, which may be either solid or liquid. Solid foams are used in construction and insulation materials or in sponges. Liquid foams appear in products like foods and personal care items—where they are often beneficial. In process and surface technology systems or in wastewater treatment, however, foam formation is generally undesirable. It can cause reaction mixtures to overflow, disrupt containment, or compromise product quality. Foam forms when a gas mixes with a liquid capable of creating stable membranes, also known as lamellae or films.
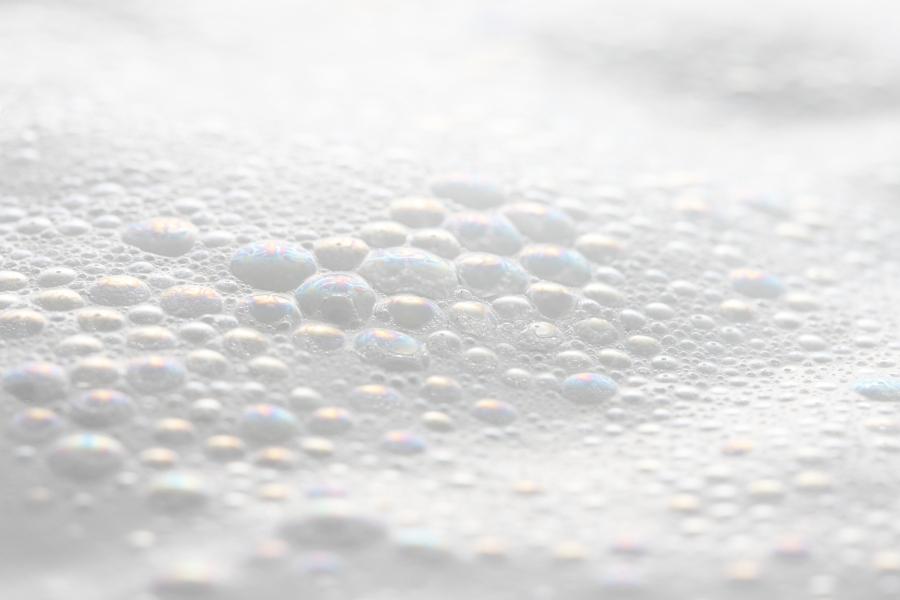
This phenomenon often occurs in solutions containing proteins or surfactants. The gas may be introduced externally, such as air entering agitated or flowing liquids, as in a washing machine, internally, through chemical or biochemical reactions (e.g. carbon dioxide during fermentation), or through the evaporation of volatile components (as with milk boiling over). To prevent foam from forming, defoamers can be added to the liquid. These agents destabilize the bubble membranes so that any gas bubbles reaching the surface burst immediately.
What Makes an Effective Defoamer?
To effectively suppress foam, a defoamer must meet three key criteria:
- It should be insoluble in the foaming liquid.
- It must be able to penetrate the bubble membrane.
- It should spread efficiently along the gas-liquid interface.
Defoamers are typically dispersed into the foaming liquid as small droplets—a property known as dispersibility. For these droplets to penetrate the foam film, their surface tension must be lower than that of the liquid. Once they reach the interface, they weaken the membrane until it ruptures.
This rupture is aided by a process called spreading, where the defoamer droplet spreads out along the bubble surface. For this to happen effectively, the interfacial tension between the defoamer and the liquid must be low. If it is too high, the droplet remains intact and cannot spread.
What Are Defoamers Made Of?
The composition of a defoamer depends on the system in which it is used. Mineral oils are commonly used to prevent foam, thanks to their low surface tension and good distribution in aqueous media which is often aided by small amounts of emulsifiers.
To improve performance, defoamers may include hydrophobic solid particles that help droplets penetrate bubble membranes more easily. Many formulations also contain biocides to prevent microbial growth. Silicone oils are highly effective due to their very low surface tension, although they are often incompatible with water-based systems. Modified silicone oils, however, offer high efficiency in foam control.
Where Are Defoamers Used?
Defoamers have a wide range of applications—across the food industry, pulp and paper manufacturing, textiles, wastewater treatment, surface technology, and metalworking. Foam often arises from ingredients in raw materials or auxiliary substances that were used earlier in the process.
Metalworking
In metalworking, cooling lubricants are used to dissipate the heat generated by friction. These fluids are mixed intensively with air during operation, which promotes foaming.
Excessive foam would interfere with heat dissipation and disrupt circulation of the coolant.
Surface Pretreatment
Surface pretreatment involves cleaning and degreasing metal parts. The cleaning agents often contain surfactants that tend to foam. Defoamers are added to this process to reduce foam levels and prevent overflow during the process.
Surface Coating
Surface coating processes rely on wetting agents to evenly distribute chemicals across the workpiece. These agents often consist of foam-producing surfactants. Foam bubbles on the surface would interfere with wetting and reduce the adhesion of the coating. Trapped foam in paints or coatings can cause defects such as craters or pinholes.
Wastewater Treatment
Foam control is also essential in wastewater treatment. In biological treatment, bacteria break down pollutants while consuming oxygen.
Chemical Processing
There are a number of operations in the chemical industry which involve close contact between gases and liquids—such as distillation or gas scrubbing. If the chemicals used have a tendency to foam, this can cause serious disruptions, reduce process efficiency, or even pose safety risks. In such cases, foam prevention is critical to maintaining stable and safe operation.