Coagulants cause coating particles in wastewater to join together into micro-flocs and allow them to be separated during further treatment. Read here about where wastewater is generated during painting processes, how detackification works, what requirements detackification agents must meet, and how water can be recycled in a resource-conserving manner.
The Fundamentals of Paint Detackification
Characteristics of Paint Particles in Wastewater
When using the spray method in metal and plastic coating, paints are atomized and carried by an airstream to the surfaces of parts or components. Consequently, the coating particles in the wastewater are very small. The particles become electrostatically negatively charged in the airstream. As a result, all particles have the same electrical charge and repel each other. These two properties cause the particles to remain finely distributed in the water and make them difficult to remove in this state. For separation, they must coagulate and form flocs. This is accomplished through chemical reactions and aided by detackification agents.
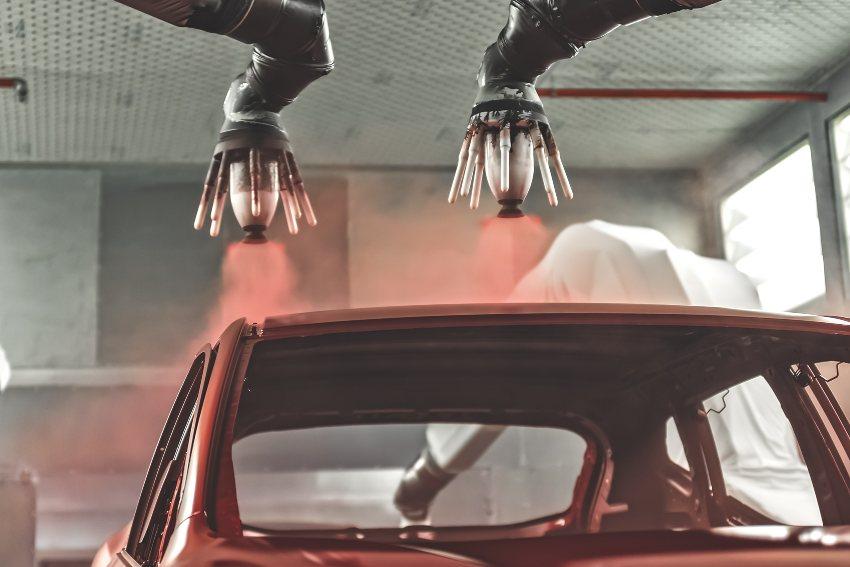
Functions of Detackification Agents
One task of detackification agents is to eliminate the repulsive forces between the particles. For paint detackification, chemistry uses positively charged components that attract the negative particles. This creates an electrically neutral connection between a paint particle and the corresponding component of the detackification agent. Small micro-flocs form from this. Paint de-bonding (the prevention of paint adhesion to surfaces) occurs alongside paint detackification. This keeps system components, pipes, and fittings free from encrustations and blockages. The vigorous mixing of wastewater and detackification agent required for the process can lead to foam formation. To suppress this, defoamers are included in the detackification agents.
Flocculation After Detackification
At this point, the micro-flocs are still too finely distributed in the wastewater to be separated. Therefore, chemistry has developed flocculation aids. These chemicals cause the micro-flocs to clump together into larger paint flocs. Depending on the process requirements, the flocculation aid can either be a component of the detackification agent or mixed into the wastewater following detackification. The composition of the flocs determines whether they settle to the bottom or float to the surface.
Requirements for Detackification Agents
Detackification agents must be adapted to the specific conditions of the coating process. The composition varies depending on whether the wastewater contains solvent-based or water-based material, or both. The behavior of the resulting flocs (floating or sinking) is also influenced by their composition. Further requirements arise from how the resulting sludge should be processed or disposed of. Therefore, chemistry offers an extensive range of wastewater detackification agents that account for wastewater composition, the types of systems and discharge systems used, and the utilization of the residual sludge.
Additional prerequisites for high-performance products:
- Good paint de-bonding
- High separation rate
- Quick and complete water clarification
- Good sludge dewatering
- Long service life for circulating water
- Extended cleaning intervals
- Recyclability of paint sludge
- Environmentally friendly ingredients
- Low consumption values
Additionally, Kluthe prioritizes sustainability and EPA compliance in the production of detackification agents. Minimizing the consumption of chemicals and water, as well as reducing waste quantities, contributes significantly to resource conservation.
Wastewater Generation in Painting
Wastewater is generated at various points during the painting process, where the application of detackification agents for wastewater treatment becomes necessary. The main sources of wastewater are water curtains and wet scrubbing.
Wastewater from Water Curtains
American manufacturers typically use spray application methods for both water-based and solvent-based paints in their finishing operations. Whether painting manually with spray guns or in spray booths, a portion of the paint flows past the surfaces of the parts or components. This portion is called overspray. If this paint were to continuously accumulate in the workplace or spray booth, the process would eventually come to a halt. To remove it from the workplace or the spray booth, the overspray is captured by irrigated water curtains and transported away with the wastewater.
Wastewater from Wet Scrubbing
Many painting systems and all spray booths are equipped with an extraction system that keeps the air clean in workplaces. The exhaust air is either directed outdoors or circulated and reused as compressed air for spray guns or booths. In both cases, exhaust air treatment is required. On the one hand, emission limits must be maintained, and on the other hand, constant operating conditions must be ensured. For exhaust air treatment, wet scrubbing processes are often used, in which coating particles are washed out of the air with water and transported away.
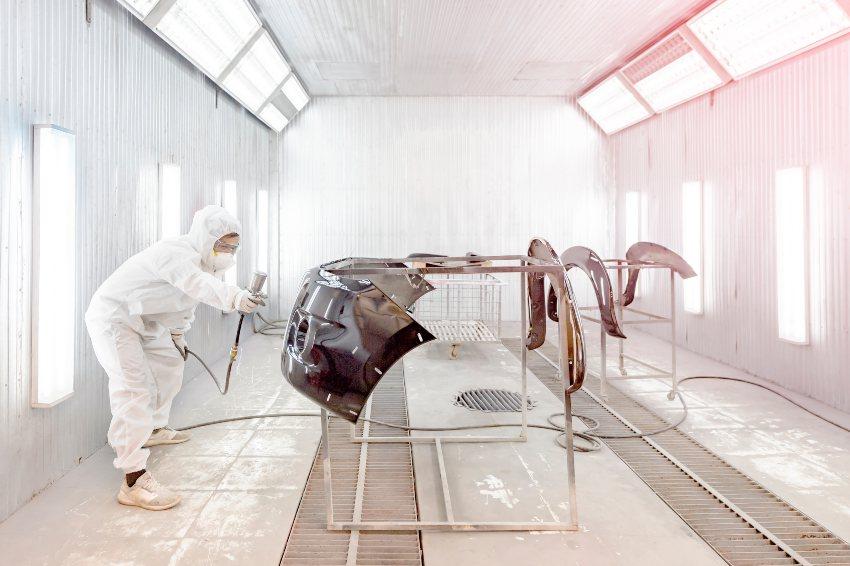
What is Water-Based Paint?
Industrial spray paints are formulations consisting of pigments, fillers, binders, and various additives. Solvents ensure that the mixtures remain in a liquid state until processing and evaporate during drying. If water is used as a solvent, these are water-based coatings. If organic solvents (VOCs) perform this task, they are solvent-based coatings. With water-based paint, it is practical to recover the paint from the sludge and reuse it. In-house recovery is advantageous when large quantities of a water-based paint of one color variant are processed. Otherwise, separate wastewater streams are required, which involve corresponding technical effort.
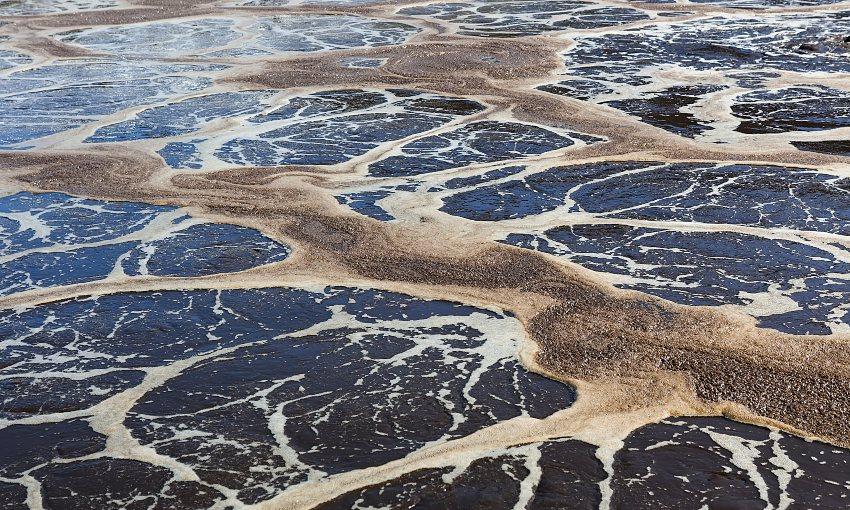
Water Recirculation
After coagulating the surface treatment particles with detackification agents and floc formation, the process liquid rests in a container where it clarifies through floating (flotation) or sinking (sedimentation) of the paint flocs. Subsequently, the solids that form the paint sludge are discharged. Pumps then return the clarified solution to the painting process. The resulting sludge is either further processed in a treatment plant or dewatered, dried, and burned for energy recovery.