Tube drawing is a critical manufacturing process that creates precise, high-quality metal tubes used in everything from automotive parts to construction materials. The process transforms stock materials into finished tubes with precise dimensions. The starting materials are typically steel hollow cylinders (known as tube blanks or billets) from rolling mills, welded tube stock, or semi-finished non-ferrous metal products. This guide explains how high tensile forces (pulling forces), combined with specialized tools, convert these materials into finished tubes, and how lubricants help facilitate this process.
Classification of Tube Drawing in Manufacturing Processes
Drawing is a metal forming process that intentionally alters the geometry of stock material. Under intense forces, the metal flows into a new shape. The tools control this flow by forcing the material to occupy the space between their surfaces. When this occurs under both tensile and compressive forces, it is known as tension-compression forming. This category includes drawing, deep drawing, collar drawing, and drop forging. In this process, the pulling force directly acts on the material, pulling it through the tools where it conforms to their contours. Different tool designs can create long workpieces with various profiles. When the final product is a tube, this is referred to as tube drawing.
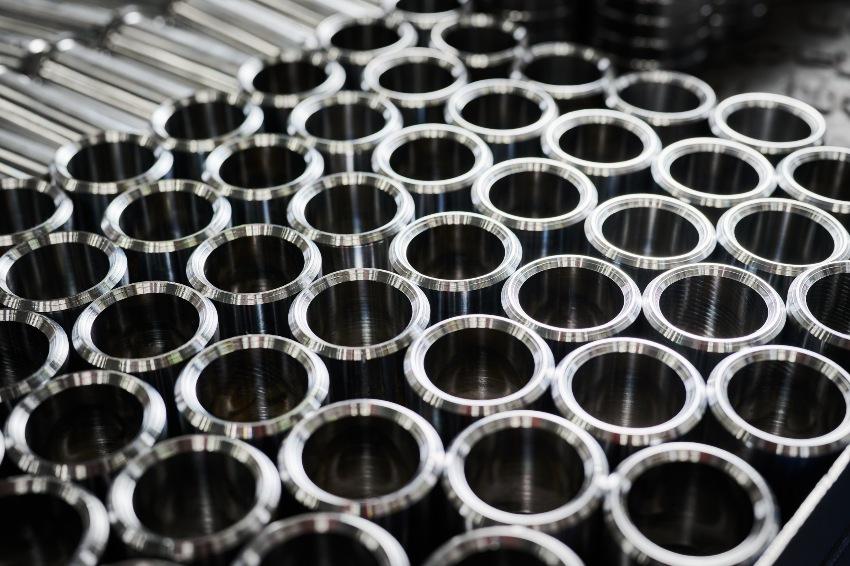
Cold Forming
The forming process starts with material at room temperature, making it a cold forming operation. At this temperature, the metal is less pliable, requiring significant tensile forces to make it flow. Major shape changes often require multiple forming stages. However, cold forming offers excellent dimensional accuracy and strengthens the material through work hardening, making it beneficial for many applications. When multiple forming steps are needed, manufacturers must use heat treatment between stages to reverse the hardening effect of cold working.
Tube Drawing: Overview of Manufacturing Methods
This manufacturing method depends on the required tube diameter and dimensional tolerances. Steel tubes start as either hot-rolled hollow cylinders or welded tubes. For aluminum or copper tubes, manufacturers often begin with larger diameter tube stock that has wider tolerances, produced through extrusion or centrifugal casting. The main production methods include hollow drawing, plug drawing (using fixed or floating plugs), and rod drawing. Specialized internal and external tools can create complex profile shapes.
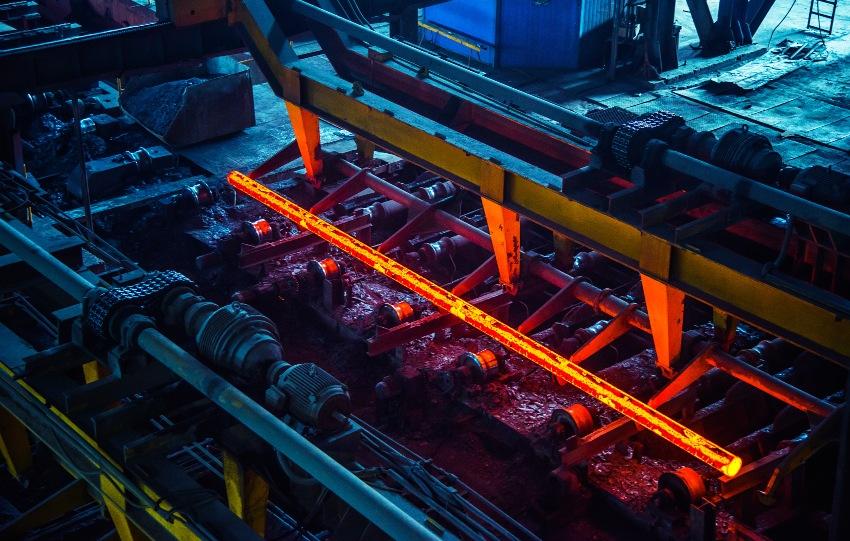
Preparation of the Raw Material
Before drawing begins, the stock material must undergo a thorough cleaning to remove scale, rust, and contaminants. This typically involves shot blasting or acid pickling. To improve the entire process, surface treatments like zinc phosphating can be applied to steel materials. The phosphate coating helps the material slide along the tools, and its texture holds lubricants effectively.
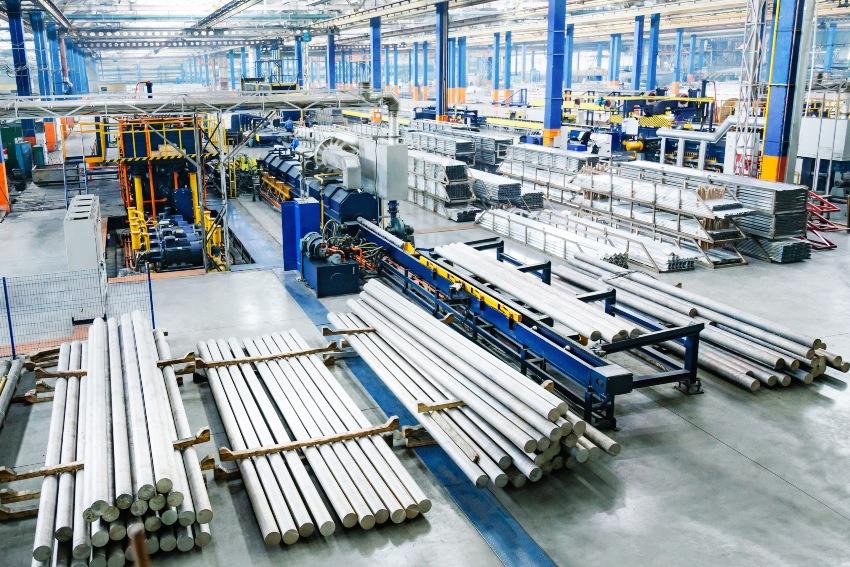
Lubrication
Lubricants reduce friction and provide cooling. Without proper lubrication and cooling, the friction between the material and tools, as well as the internal friction from material flow, would generate excessive heat, that the forming process would stop. Lubricants create a protective film between the tool and material surfaces. These lubricants must withstand high temperatures and pressures while maintaining proper viscosity throughout the process.
Hollow Drawing
Hollow drawing represents the simplest tube drawing method. It uses a fixed drawing die whose inner diameter determines the tube’s outer diameter. During forming, the wall thickness decreases while the inner diameter stays relatively constant. This method works well for tubes where precise inner dimensions are not critical, such as those used in structural engineering, scaffolding, and frameworks. The same process applies to wire and rod production. Modified drawing dies can produce various profiles, including guide rails.
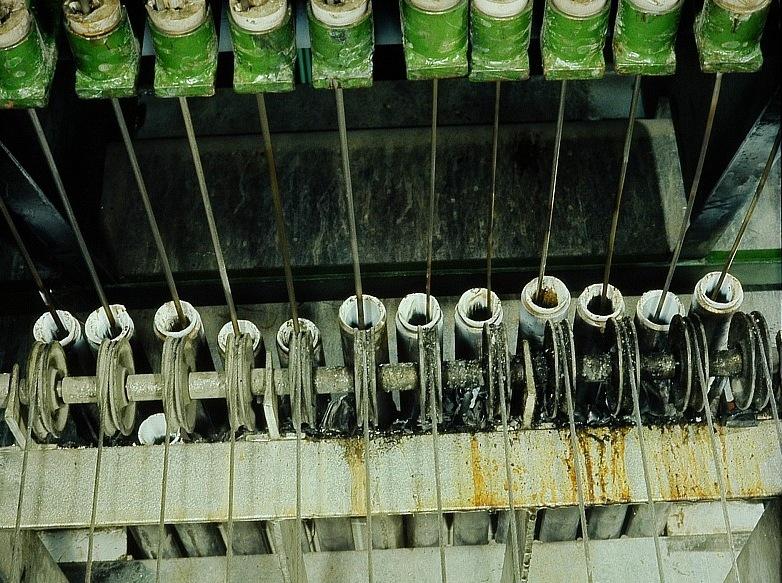
Plug Drawing with Fixed or Floating Plug
When applications demand high precision in wall thickness, inner diameter, and outer diameter, of a rod, manufacturers use an internal tool called a plug. The plug’s cylindrical section determines the inner diameter, while a drawing die controls the outer diameter. Typically, manufacturers attach the plug to a rod, insert it into the stock material, and fix it in front of the drawing die. For very small diameter tubes, especially when the stock comes in coils, a floating plug works better. This self-centering tool has a cylindrical front end followed by a tapered section. By varying the plug and die geometry, manufacturers can create different profiles.
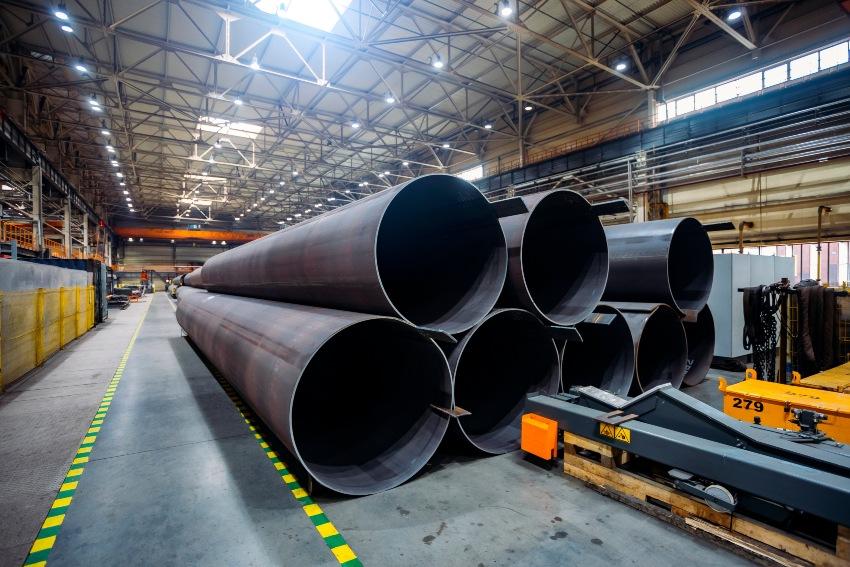
Rod Drawing
Rod drawing involves a rod-shaped internal tool sized to the desired inner tube diameter. During the process, this rod accompanies the stock material through the drawing die. This method reduces the stock’s inner diameter to align with the rod’s outer diameter, while the drawing die sets the final outer diameter. The rod’s length dictates the maximum tube length. After forming, a slight expansion through rolling frees the rod, which can affect dimensional precision. Rod drawing permits larger dimensional changes in one step compared to plug drawing. Manufacturers often use this technique for initial shaping, followed by plug drawing for final sizing.
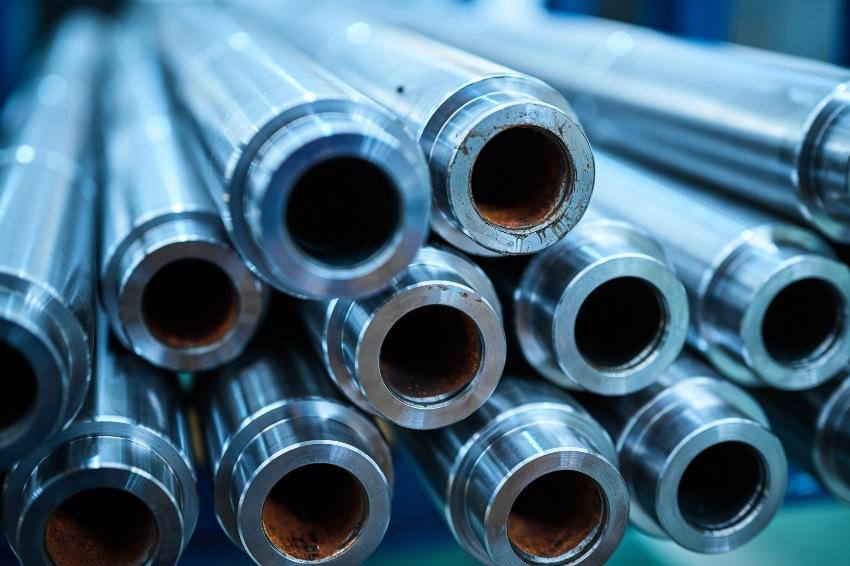