Cold forming is a metalworking process where materials are shaped under significant compressive or tensile forces with or without minimal preheating. This distinguishes cold forming from hot forming, with the dividing line being the recrystallization temperature.
Formation of Material Microstructure During Cooling
The formability of metals is linked to their internal structure. At the start of metal processing, materials exist as molten liquid. As they cool, atoms begin to align and form crystals. A crystal is defined by its regular geometric atomic arrangement. As more atoms attach, the crystals grow until they meet each other, thus forming a solid structure.
This microstructure can be observed under a microscope by preparing samples that are ground, polished, and etched. The crystals, randomly oriented, appear as grains, surrounded by grain boundaries.
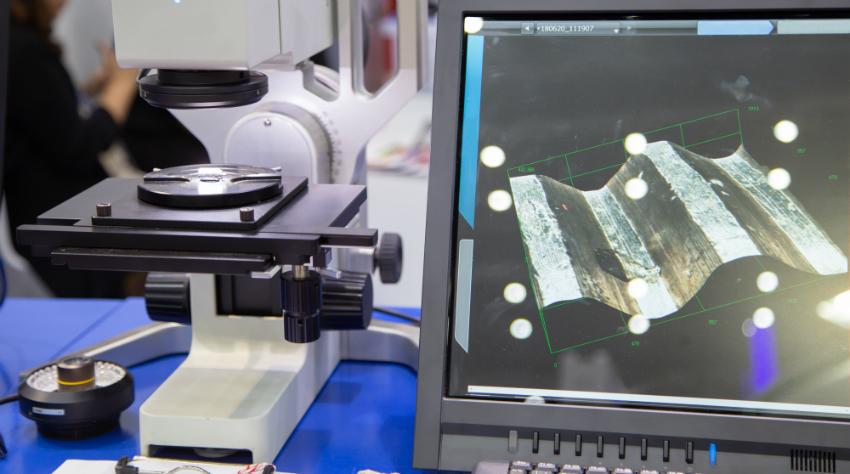
Changes in Material Structure During Cold Forming
In cold forming, crystals are compressed or elongated. To retain the new shape, the applied forces must overcome the atomic bonds within the crystal lattice, causing dislocations in the structure. These dislocations create internal stresses, leading to strain hardening of the material.
Increased temperatures intensify particle motion. Once a certain threshold is reached, thermal motion counteracts the internal stresses. The atoms reorganize into new crystals with a normal structure. The original configuration is restored around any dislocations. This process begins at the material’s recrystallization temperature.
Stress-strain diagrams for individual materials provide guidance on required forces. In tensile tests, standardized samples are subjected to increasing force. Initially, the material stretches proportionally to the applied stress. Once the material dependent yield strength is exceeded, the sample begins to neck. Further stress leads to fracture. The range between yield strength and fracture strain is used for cold forming.

Materials Suitable for Cold Forming
Materials for cold forming should have an extensive range between yield strength and fracture strain while requiring minimal force. This includes many aluminum alloys, copper, and specific steel grades.
Steel, an alloy of iron and carbon with a maximum carbon content of 2%, is often tailored with additional metals to influence properties. Steel, suitable for cold forming, typically has a carbon content below 0.5% and alloying elements under 5%. ¹
Cold Forming Processes
Cold forming is categorized into bulk and sheet forming. Sheet forming includes deep drawing and bending, maintaining a largely constant material thickness. Bulk forming involves significant cross-sectional changes, such as rolling and extrusion.
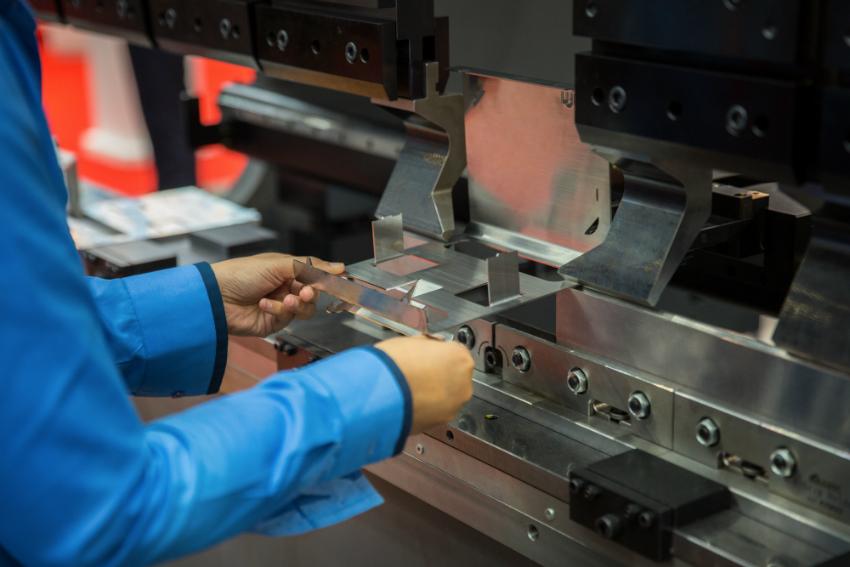
In rolling, metal passes through the gap between rotating tools, whose shape determines the workpiece’s geometry, producing profiles, rings, or threads. Strain hardening near the surface often strengthens the material—a desirable effect. For significant cross-sectional changes, multiple forming steps may be required, with increasing strength necessitating intermediate recrystallization annealing.
Cold extrusion involves pressing metal into a die with a punch, thus adopting the die’s shape. This process is ideal for high-volume production of rotationally symmetrical parts. For large components, soft annealing before forming can reduce the required forces.
Lubricants for Cold Forming
Friction during cold forming generates heat, which can cause oxidation of the workpiece and cold welding between tool and workpiece. Friction is reduced by coatings applied to the surface before forming, such as zinc phosphate, forming oils, waxes, graphite, or specialized soaps.
Forming lubricants must be compatible with the materials and processes used. Kluthe offers a wide range of lubricants tailored for applications like cold heading of fasteners, wire drawing, or sheet bending. The portfolio also includes lubricants specifically designed for bulk cold forming.
Multiple forming processes often alternate with recrystallization annealing to reduce strength. Coatings are typically removed before heat treatment and reapplied afterward. In many cases, high-performance lubricants can replace zinc phosphate coatings.
The development and selection of forming lubricants increasingly prioritize ease of post-process cleaning and environmental compatibility. Many products are free of chlorinated, sulfurous, boron-containing, and heavy metal compounds. Additionally, lubricants without secondary amines or formaldehyde releasers are available.
Advantages of Cold Forming
Compared to machining, cold forming offers better material utilization and maintains continuous grain flow. For large production runs, shorter processing times lower costs.
Cold forming enables the production of parts with extraordinarily complex geometries and high strength. It is widely used in industries such as automotive manufacturing, energy plant construction, and valve production. Another key application is in equipment and container construction.
Why Choose Cold Forming?
Compared to hot forming, cold forming achieves better surface quality and higher dimensional accuracy without the energy-intensive heating process. However, it requires greater mechanical force.
Strain hardening often eliminates the need to harden finished parts. Cold-formed shafts and threaded spindles are stronger than machined parts of the same cross-section.
______________________________________________________________________________________________
¹ https://www.massivumformung.de/fileadmin/user_upload/8_Karriere/IMU_Fachbuch_2013.pdf