Steel is found in nearly every aspect of daily life—houses, bridges, tools, and machines. While it is not a lightweight metal, steel is relatively easy to shape and provides tremendous structural strength. Pure steel, however, cannot be used directly as it corrodes when exposed to air—a process commonly referred to as rusting. To protect against rust, steel surfaces are often treated through methods like galvanization, which coats the steel in a layer of zinc. This layer forms a protective barrier, but under certain conditions, it can develop a specific type of corrosion known as white rust. White rust can compromise the appearance and, over time, the durability of galvanized steel. In this guide, you will learn how to effectively remove white rust and prevent it from reappearing.
Rust or Patina?
Galvanized surfaces protect the underlying steel from corrosion by forming a layer of basic zinc carbonate, known as zinc patina, when exposed to air. This dense, smooth layer provides excellent surface protection and creates a solid foundation for additional processing, such as metal or plastic coating. The downside of patina is that it forms slowly and takes a few days to fully develop. During this time, if the surface is not handled properly, white rust may form instead of the desired zinc patina. White rust is a mixture of zinc hydroxides, zinc oxides, and zinc carbonates, with its exact composition depending on environmental factors like humidity and temperature.
Is White Rust Harmful?
The answer is a bit of “yes and no.” A light formation of white rust is generally not a problem. Initially, it may affect the appearance, but over time, the zinc hydroxide in the white rust layer converts into zinc carbonate, assuming the conditions that originally caused the white rust are no longer present. The protective layer will gradually be restored, and the surfaces will blend in visually. However, heavy white rust formation can severely damage or even destroy the zinc layer.
Factors Responsible for White Rust Formation
To form a protective zinc patina on freshly galvanized surfaces, moisture, sufficient oxygen, and CO2 are needed. If these conditions are not met, or if freshly galvanized parts are stored in chloride- or sulfate-rich environments, a protective zinc patina may not develop. In adverse conditions, an unwanted layer of white rust can form within hours. Light white rust can be removed, but heavy rust is more challenging, so it is better to prevent its formation from the outset.
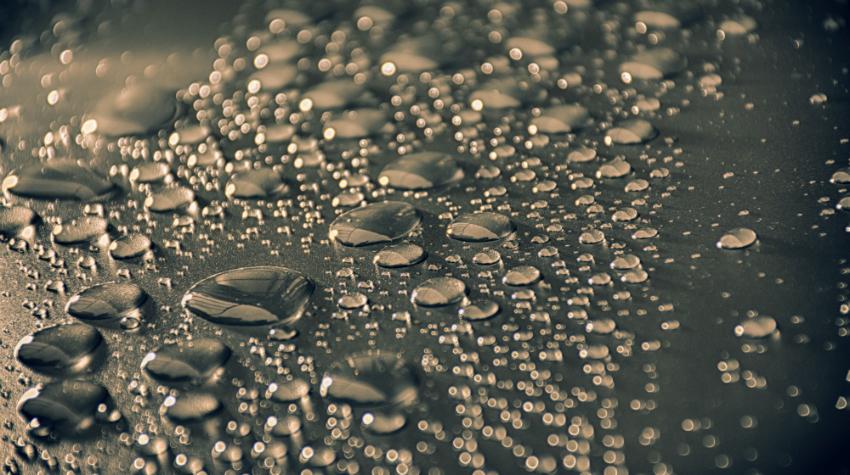
Proper Storage
After a steel part is galvanized, it is either temporarily stored or transported for further processing. In both cases, good ventilation is essential to prevent moisture and condensation. Ideally, storage should be in a dry, clean area with stable temperatures. Therefore, it is more sensible to store parts uncovered in a hall rather than outdoors. If outdoor storage is unavoidable, the parts should be protected. A loosely placed plastic cover is better than a tightly fastened tarp. Freshly galvanized steel should not be sealed with an airtight cover, as plastic coverings can trap moisture and promote white rust formation.
To promote air circulation, parts should not be stacked directly on top of one another but placed on wooden beams—a simple yet effective measure. Regular inspections for condensation and sufficient air circulation can prevent potential damage early on. Additionally, galvanized steel parts should be stored at an angle to allow water runoff. In autumn and winter, particular attention should be paid to environmental conditions during outdoor storage, as rain, fog, and temperature fluctuations will stress the surfaces. Parts stored outside at sub-zero temperatures, which are then moved to a warmer warehouse will cause water to condense on the surface, which must be wiped off.
A Look at Warehouses, Logistics, and Transport
Inside warehouses and production halls, environmental conditions can be better controlled than with outdoor storage. Humidity should be kept constant and not too high, as humidity levels above 50% are considered critical and can accelerate corrosion. Measuring humidity at various points helps with monitoring and allows for early intervention. Technical measures, such as a dehumidification system or air circulation system, are also helpful if humidity levels consistently reach critical levels. Ceiling fans are a simple but effective solution.
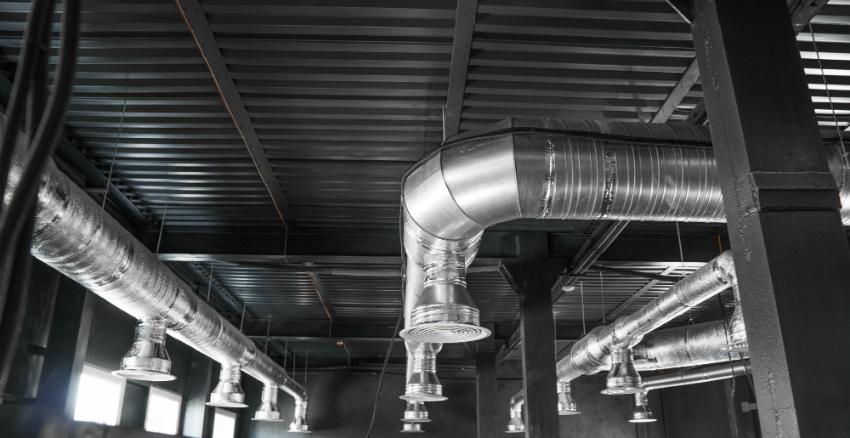
Similar precautions apply to transportation. Condensation, or “sweating,” should be avoided whenever possible. Parts may heat up in the summer and cool down in the winter. When ambient temperatures change, unwanted condensation can form. Open transport of galvanized parts is preferable in the summer, while they should be adequately protected from moisture in the winter. Precautions must be taken to prevent road salt from splashing onto the parts, which can also damage galvanized surfaces.
Direct Surface Protection
Galvanized surfaces can be safeguarded both indirectly and directly. The most practical approach is to oil parts and galvanized sheets. Chemically, corrosion protection can be achieved through chromating, specifically, by applying a passivation layer based on chromium (III) compounds. This process, known as thick-layer passivation, can be further enhanced with an additional sealing layer. However, pre-coating parts after galvanization does not provide adequate protection against white rust, thereby allowing unwanted corrosion to develop.
How to Remove White Rust
White rust can be removed using either chemical or mechanical methods. The first step is to evaluate how far the unwanted corrosion process has progressed. For light white rust, treatment may not be necessary, especially if the part is not undergoing further processing. If the part will be painted, however, the surface must be cleaned and all white rust thoroughly removed to avoid issues with paint adhesion. White rust can be removed manually with a soft nylon brush, warm water, and soap, or by using a low-pressure gun to remove the unwanted spots.
Heavy white rust forms when parts are stored for prolonged periods in damp, poorly ventilated conditions. Simple surface cleaning is insufficient for removing this, as the surface must be fully cleared of oxidation residues to prevent further moisture retention, which can worsen rust formation. Nylon brushes are effective for removing rust, followed by a thorough rinse with water. For more stubborn spots, chemical cleaners containing sodium hypochlorite may be applied, followed by a final rinse with warm water. While surface pretreatment can improve the appearance of heavy white rust, complete restoration may not always be possible, and the thickness of the zinc layer—and thus its corrosion protection—may be compromised. In such cases, it is important to measure the protective layer’s thickness with a coating gauge and apply a suitable coating to restore any damaged areas.
White rust on galvanized parts often results from improper storage and transport. In small amounts, it usually does not cause significant harm and will eventually transform into a protective zinc patina. However, heavier white rust should be removed to prevent damage and maintain corrosion resistance. By ensuring optimal storage and transport conditions during production, white rust formation—and the need for removal—can be largely avoided.